Types of Heat Exchangers: Advantages, Applications & Design
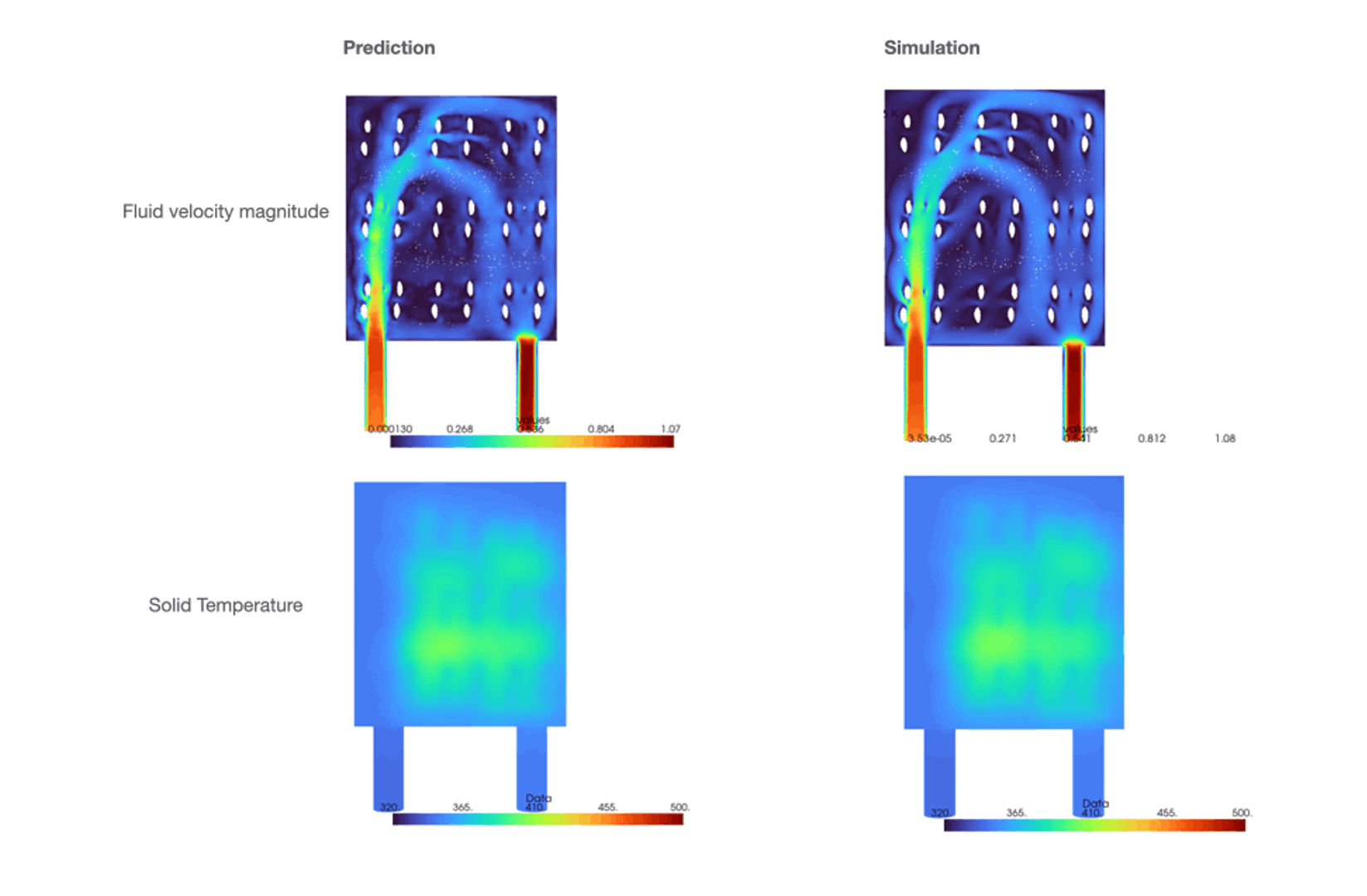
Heat exchangers are vital in daily life and engineering, enabling efficient heat transfer between fluids, which is crucial for many applications. They help maintain warmth in homes during winter and cool engines in vehicles and machinery. By recycling thermal energy, heat exchangers enhance energy efficiency and reduce waste. Continuous innovation includes exploring new materials and design options and using 3D simulation and artificial intelligence to improve performance. This guide provides an overview of heat exchangers, covering their designs, advantages, limitations, and industrial applications. It highlights recent advancements in design methods, aiding engineers and curious readers in understanding these essential devices.
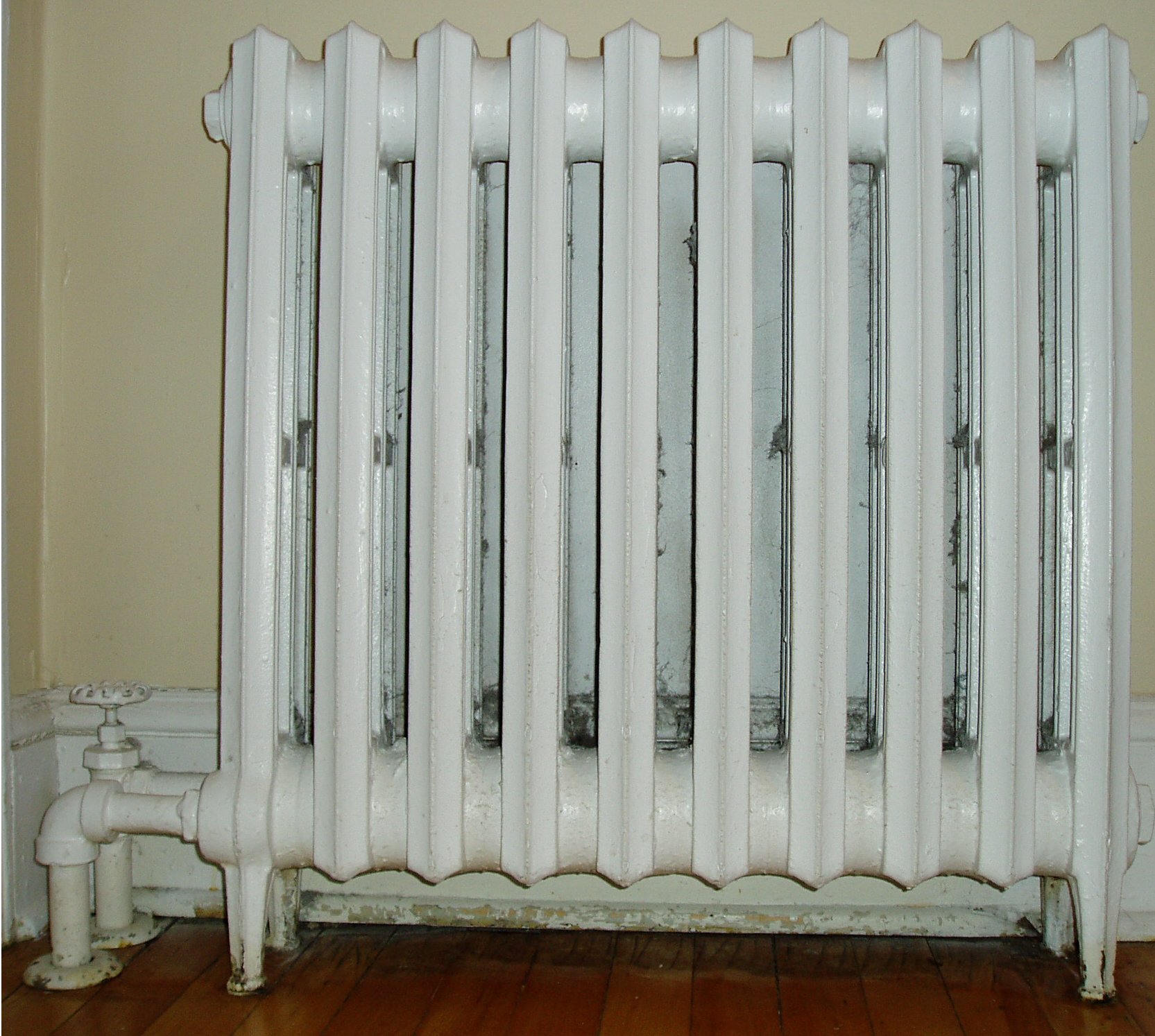
Let's start by defining heat exchangers. Then, we will move on to the critical topic of classifying the types of heat exchangers and land on applications of Artificial Intelligence Engineering.
What Are Heat Exchangers?
A heat exchanger is a device that helps "move heat" between two different substances, such as liquids or solids, without letting them mix. This process is essential for efficiently transferring energy. Heat transfer is essentially the movement of heat energy. The amount of energy transferred and the rate of transfer are closely related, with heat transfer describing how and how fast heat energy is redistributed.
This is a typical example of conjugated heat transfer, in which multiple modes of heat transfer—conduction, convection, and sometimes radiation—occur simultaneously within a system. Natural convection happens when heated fluid becomes less dense and rises relative to cooler fluid.
Heat exchangers are used in many industries. These include heating, ventilation, air conditioning (HVAC), automotive manufacturing, and chemical production. Using heat exchangers, these industries can use energy more efficiently, improve system performance, and reduce waste.
Various heat exchangers are tailored to specific needs and designed to enhance performance in different industrial applications.
The following section examines some of the most common types and their benefits.
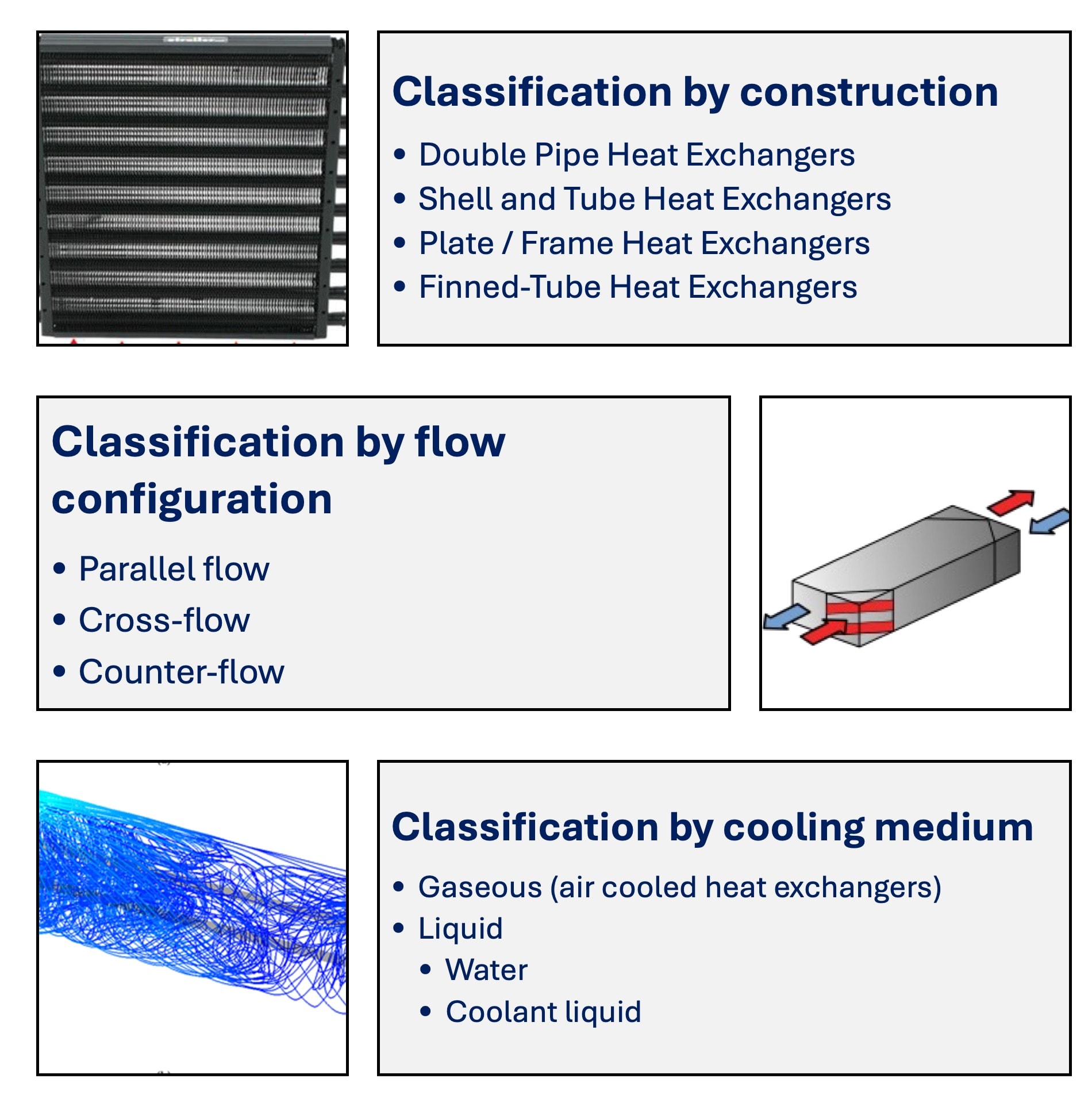
It is handy to classify heat exchangers according to their characteristics. The main criteria for classifying a heat exchanger are its type of construction, flow configuration, and cooling medium.
- Classification by construction: Double Pipe Heat Exchangers, Shell and Tube Heat Exchangers, Plate / Frame Heat Exchangers, Finned-Tube Heat Exchangers
- Classification by flow configuration: Parallel flow arrangement, Cross-flow, and counter-flow.
- Classification by cooling medium: gaseous (air-cooled heat exchangers) or Liquid (water or coolant liquid).
Most heat exchangers are indirect heat exchangers, as they involve heat flow between two fluids (hot fluid and cold fluid) that do not directly mix.
In these devices, a physical barrier, such as tubes or plates, separates the fluids while allowing heat transfer through the barrier. Examples include shell-and-tube exchangers, plate exchangers, and finned-tube heat exchangers.
Heat Exchanger Types - By Construction
Heat exchangers promote energy exchange between two or more fluids. They are classified by their flow configuration (parallel, counter, or cross-flow) and their construction. Efficient heat exchangers must undergo careful mechanical design to ensure optimal energy exchange, structural integrity, and compliance with operational requirements.
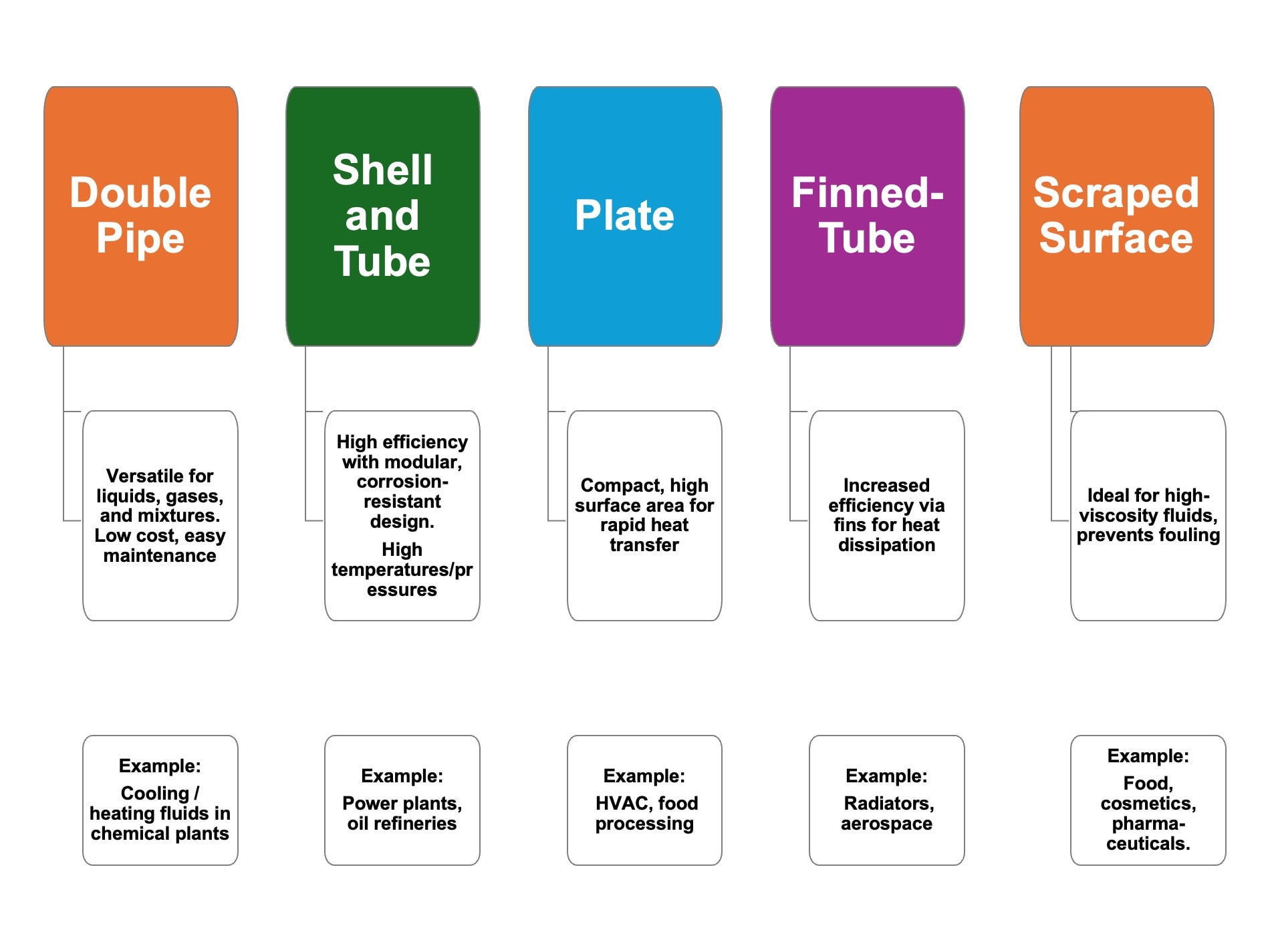
Double Pipe Heat Exchangers
Double-pipe heat exchangers handle various fluids, such as liquids, gases, and mixtures, making them versatile for diverse applications requiring cooling or heating. Their flow configurations can be parallel or counterflow, optimizing heat flow efficiency.
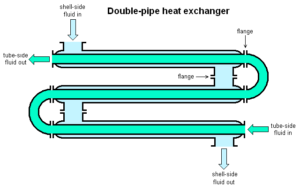
Maintaining these heat exchangers is straightforward since both pipes are accessible for cleaning and repairs. This minimizes downtime and enhances reliability. The simple design also lowers manufacturing costs, making double-pipe heat exchangers economical for small-scale uses. Countercurrent flow maximizes temperature differentials and heat transfer efficiency. Double-pipe heat exchangers can also be scaled for large chemical plants and small lab setups.
Example: Used in chemical processing plants for cooling or heating fluids.
Shell and Tube Heat Exchangers
Shell and tube heat exchangers feature tubes for hot and cold fluids within a cylindrical shell. They are widely used in power generation, oil refining, chemical processing, HVAC, and food and beverage. The small tubes carry one fluid while the shell encases the tube bundle for the second fluid. Key components of a shell and tube heat exchanger include tube sheets that seal the fluids and baffles that direct fluid over the tubes to enhance heat transfer.
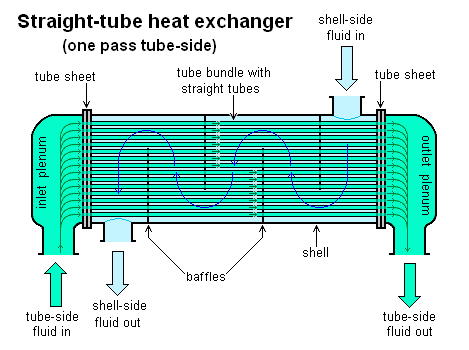
Shell and tube heat exchangers benefit from high efficiency due to numerous smaller tubes, which create temperature and pressure differences. Made from stainless steel or corrosion-resistant alloys, a shell and tube heat exchanger can endure harsh conditions and manage corrosive or fouling fluids. They also provide design flexibility with various tube arrangements and sizes and a modular structure for easy maintenance, reducing downtime in industrial settings.
Example: Shell and tube heat exchangers are widely used in oil refineries to manage temperature and pressure differentials.
Plate Heat Exchangers
Plate heat exchangers are used in HVAC systems, refrigeration, food and beverage industries, chemical processing, and power plants. They consist of stacked plates with alternating hot gas and cold fluid passages, efficiently facilitating heat exchange in a compact structure. This design provides a large surface area for heat flow, speeding up temperature changes. CFD simulations for a herringbone-corrugated plate at various angles illustrate this.
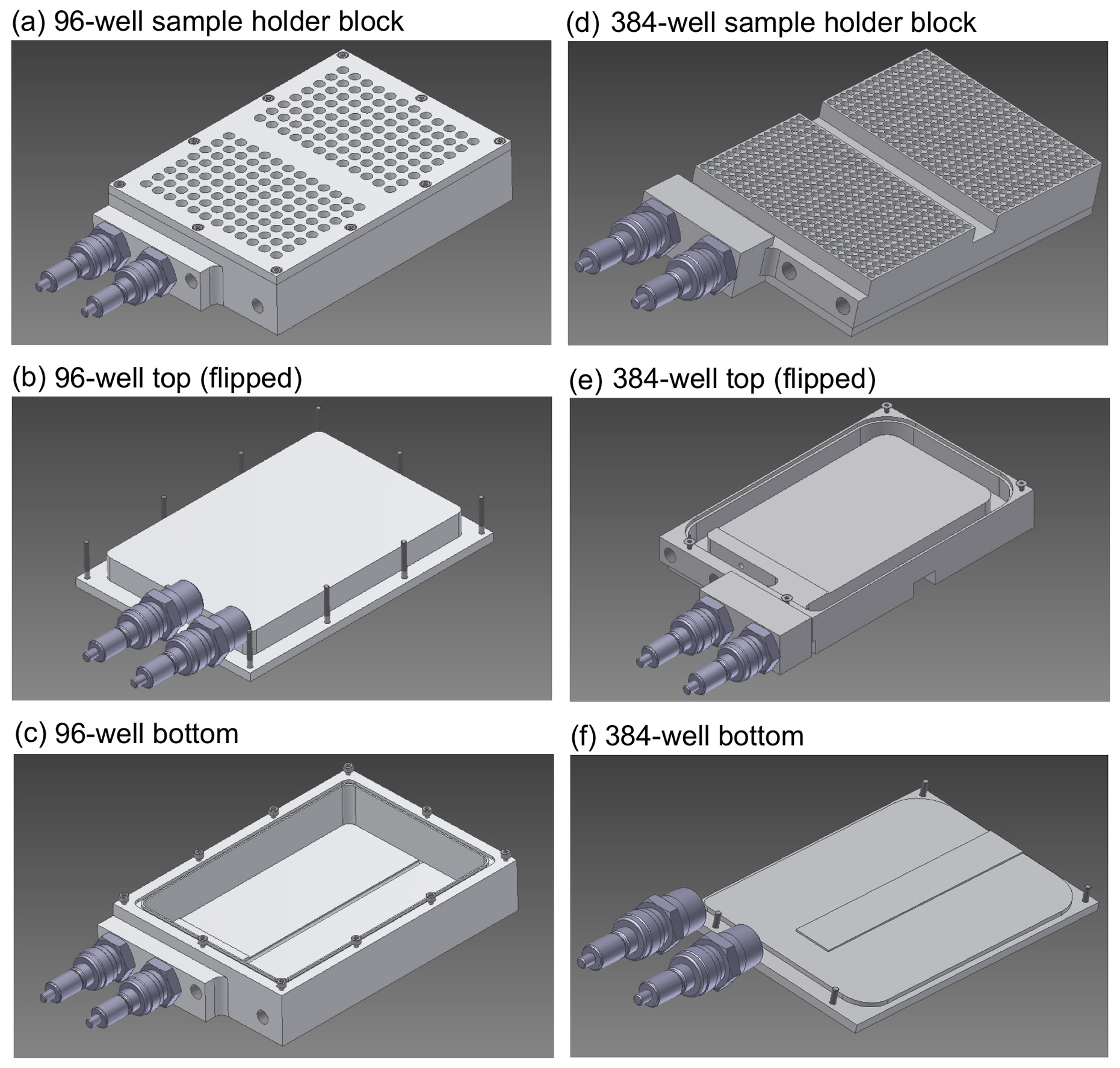
The wavy plates increase turbulence and promote effective heat movement, making these exchangers efficient for heating and cooling.
Example: Plate heat exchangers' compact design makes them ideal for use in space-restricted areas such as HVAC and refrigeration.
Plate Heat Exchangers: Frame Heat Exchangers
The term "plate heat exchanger" encompasses various designs where heat transfers between thin plates. The frame heat exchanger is one specific configuration within this category, specifically gasketed plate heat exchangers.
Plate heat exchangers generally consist of multiple thin plates with alternating channels for hot and cold fluids to flow through. The plates separate the fluid channels, facilitating efficient heat transfer between them.
The frame heat exchanger is distinguished by a frame or casing that supports and encloses the plates, providing structural integrity and facilitating fluid connections.
Example: Frame heat exchangers are widely used in HVAC systems to regulate building temperatures, in the food and beverage industry for pasteurization, and in chemical processing to heat or cool fluids.
Finned-Tube Heat Exchangers
A finned-tube heat exchanger is a standard device that enhances heat transfer efficiency. It includes tubes featuring fins on their outer surfaces. These fins markedly enlarge the surface area available for heat exchange, increasing heat transfer between the fluid inside the tubes and the surrounding air or another fluid. Consequently, finned-tube heat exchangers outperform designs lacking fins.
This design is similar to what you might see in everyday appliances. For example, the radiator in a car or the coils at the back of a refrigerator are finned-tube heat exchangers. In a car radiator, the fins help transfer heat from the hot coolant inside the tubes to the air outside, cooling the engine. In refrigerators, the fins help release heat from the refrigerant to the surrounding air to keep the inside cool.
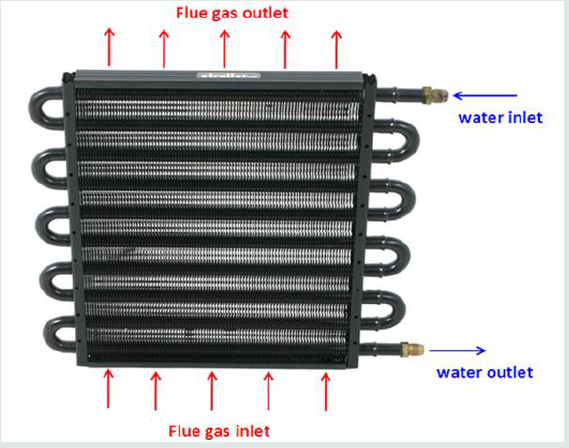
Example: Finned-tube heat exchangers enhance heat transfer and are used in various applications, from HVAC systems in buildings to industrial processes requiring efficient heating or cooling. They can maximize thermal efficiency while saving space, making them a practical solution in everyday life and engineering.
Scraped Surface Heat Exchangers
Scraped-surface heat exchangers are designed to handle high-viscosity fluids by continuously removing fouling layers from the heat transfer surface. Maintaining consistent temperatures offers enhanced heat transfer and prevents product degradation.
Example: These exchangers are widely used in the food processing, pharmaceutical, and cosmetics industries.
Classification of Heat Exchangers by Medium
There are two main types of heat exchangers by medium, i.e., gaseous or liquid. We will discuss air-cooled heat exchangers for practical purposes, and liquids will be divided into water-cooled and coolant heat exchanger types.
Air-cooled heat exchangers
Air-cooled heat exchangers use ambient air to cool hot fluids. Due to their simple design and lack of moving parts, this type of heat exchanger is energy-efficient, environmentally friendly, and requires minimal maintenance. They are commonly used in energy production, petrochemical facilities, and refrigeration systems.
Water-cooled heat exchangers
Water-cooled heat exchangers use water as the primary cooling medium, often in configurations like shell-and-tube or plate designs. They are highly effective for large-scale heat transfer, offering superior cooling capacity compared to air-cooled systems. These exchangers are widely applied in chemical processing, HVAC systems, and thermal energy plants.
Refrigerant-based heat exchangers
Refrigerant-based heat exchangers use refrigerants to transfer heat in vapor-compression or absorption systems. Their main advantage is achieving precise temperature control, making them ideal for refrigeration, air conditioning, and industrial cooling processes. These exchangers are commonly found in both residential appliances and commercial cooling systems.
Classification of Heat Exchangers by Flow Type
We will review the different types of flow configurations for heat exchangers. There are three main flow arrangement types: parallel flow arrangement, cross-flow arrangement, and counter-flow arrangement.
This means that how fluids move through heat exchangers determines heat transfer. Fluids can travel in the same direction, move perpendicular to each other, or flow in opposite directions.
Parallel Flow Configuration
In this type of heat exchanger, fluids flow in the same direction within the tubes, resulting in less efficient heat transfer than counterflow designs. However, parallel heat exchangers are generally more straightforward to design and require less space, making them ideal for scenarios with limited space.
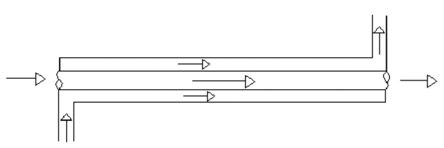
Cross Flow Heat Exchangers
In this setup, one fluid moves through the tubes while the other flows over their exterior, with their paths running perpendicular. This arrangement enhances heat transfer across the exchanger's surface. It is widely utilized in applications like air conditioning systems, where one fluid is gaseous and the other liquid. The crossflow heat exchanger balances thermal efficiency and a compact design.
Counter Flow Heat Exchangers
In these heat exchangers, the two fluids move in opposite directions. This configuration enhances the temperature difference between the fluids throughout their entire flow paths, further improving heat transfer compared to earlier designs.
Applications of Heat Exchangers by Industry
Heat exchangers are crucial in numerous industries. They enable effective heat transfer between fluids, enhancing performance and energy efficiency.
HVAC and Refrigeration
Heat exchangers are crucial in HVAC systems, transferring heat between fluids to control indoor temperature and humidity. They absorb heat from the refrigerated space and release it outside. For example, air conditioners use evaporators and condensers to manage cooling, and shell-and-tube heat exchangers are standard in large commercial buildings for central cooling.
Automotive and Transportation
Heat exchangers are integral to vehicle cooling systems in the automotive sector. They primarily cool engine coolant in radiators. They also ensure passenger comfort in car, bus, and train HVAC systems.
Beyond traditional vehicles, heat exchangers play a role in electric vehicles (EVs) for battery thermal management, which is crucial for performance and longevity. An example includes plate-fin heat exchangers used in electric motor cooling systems.
In electric vehicles, novel methods of using cooling water-glycol or other fluids are enhancing battery performance with immersion cooling.
Food and Beverage Industry
Temperature control is critical for food processing, including pasteurization, sterilization, and cooling. It also preserves food quality by rapidly heating or cooling liquids like milk or juice.
In brewing, heat exchangers are used to cool the extracted liquid efficiently.
Plate heat exchangers are standard because they can handle high-viscosity fluids and have a compact design, which is advantageous in space-limited processing plants.
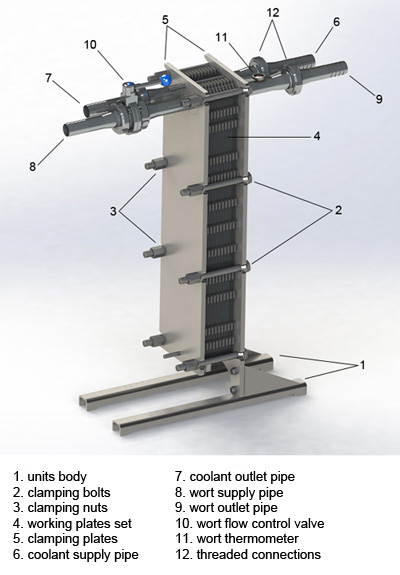
Chemical and Petrochemical Industries
Heat exchangers manage the extreme conditions of chemical reactions, often involving corrosive or high-temperature substances. They are used for cooling or heating processes, such as producing plastics or refining crude oil.
Shell-and-tube heat exchangers are widely used due to their robustness. They allow heat transfer between process fluids and cooling media like water or air. Shell-and-tube heat exchangers are also essential in gas processing, condensing, or vaporizing gases at different stages.
Power Generation
Whether fossil fuels, nuclear energy, or renewable sources like geothermal energy, power generation relies on heat exchangers to manage the energy conversion.
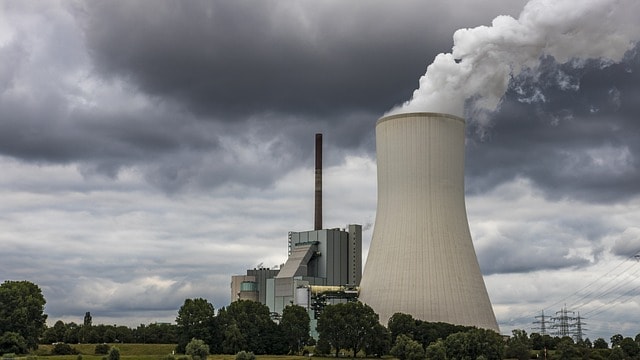
Heat exchangers facilitate the condensation of steam back into water within the Rankine cycle or cooling systems for gas turbines. Examples are once-through steam generators in nuclear reactors and air-cooled condensers used in solar thermal power plants, where they improve efficiency and control waste heat.
Heat Recovery and Heat Exchangers
Industrial processes and energy systems produce waste heat. Regenerative heat exchangers capture this heat and transfer it to water or air for reuse in various applications. They use indirect and direct heat transfer methods to achieve high thermal efficiency.
Heat Recovery and Heat Exchangers for Sustainability
Industrial processes and energy systems often generate waste heat. It's essential to capture this heat for reuse, employing both indirect and direct heat transfer methods for high thermal efficiency. We explore sustainable engineering through three key examples that illustrate efficiency and sustainability:
(1) Industrial Applications: Machinery in factories and plants generates considerable heat that, if not recovered, would be lost to the environment. Regenerative heat exchangers can capture this heat and transfer it to water for uses such as pre-heating boiler feed water, space heating, or hot water.
(2) Data Centers: With servers producing substantial heat, recovery systems can convert this waste heat into a resource, warming nearby buildings or supplying hot water to communities, promoting a more resilient and eco-friendly energy infrastructure.
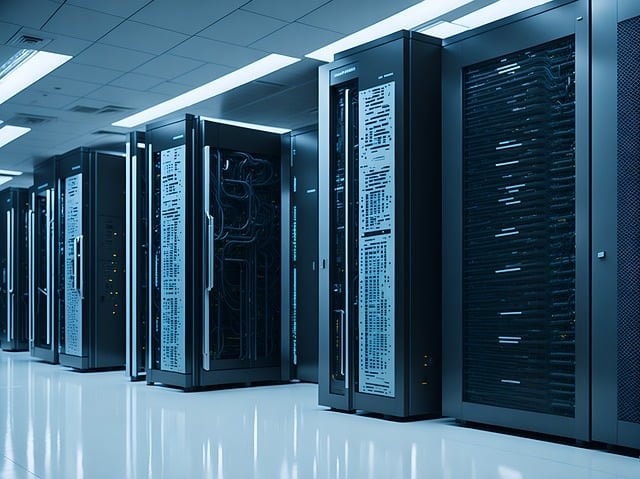
(3) Residential Settings: In this setting, energy recovery ventilators (ERVs) can extract heat from exhaust air and transfer it to incoming fresh air, reducing energy costs while maintaining indoor comfort.
Hybrid Characteristics
Regenerative heat exchangers have hybrid characteristics, combining indirect and direct heat transfer. Indirect transfer occurs via conduction through a solid matrix, while direct transfer occurs during transient phases when both hot and cold fluids interact with the matrix. This enhances the efficiency of heat exchange between fluids and the solid material.
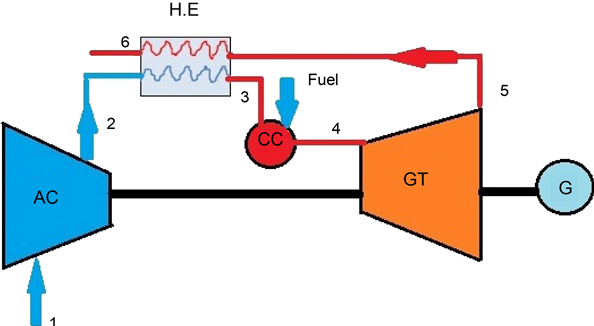
How Do Heat Exchangers Operate?
Heat exchangers are thermodynamic devices that enable efficient heat flow between fluids or between a fluid and a solid surface. Designing a heat exchanger is a thermodynamic exercise, which we will review below.
Thermodynamics Principles of Heat Exchangers
Let’s explore key concepts with basic math and physics. What is temperature? It measures the average kinetic energy of molecules in materials. The Zeroth Law of Thermodynamics defines temperature as a measurable property of thermodynamic systems. Higher-temperature objects show more molecular motion than lower ones. This description extracts a simple law for heat flow in convection, Newton's law of cooling. The equation for the heat energy flow Q is Newton's Law of Cooling, describing very simply the heat transfer process:
Q = h A (T₁ - T₂) = h A ΔT
h is the heat transfer coefficient, and A is the surface area. The coefficient h includes resistances from conduction, convection, and radiation, depending on materials' thermal conductivities, wall thickness, and fluid mass flow rate. The heat transfer coefficient for each stream is a function of Reynolds number and Prandtl number.
Regarding conduction, copper and stainless steel, which have high thermal conductivity, are commonly used in heat exchanger construction.
Heat exchangers follow the first law of thermodynamics, which states that the energy entering a system equals energy leaving it.
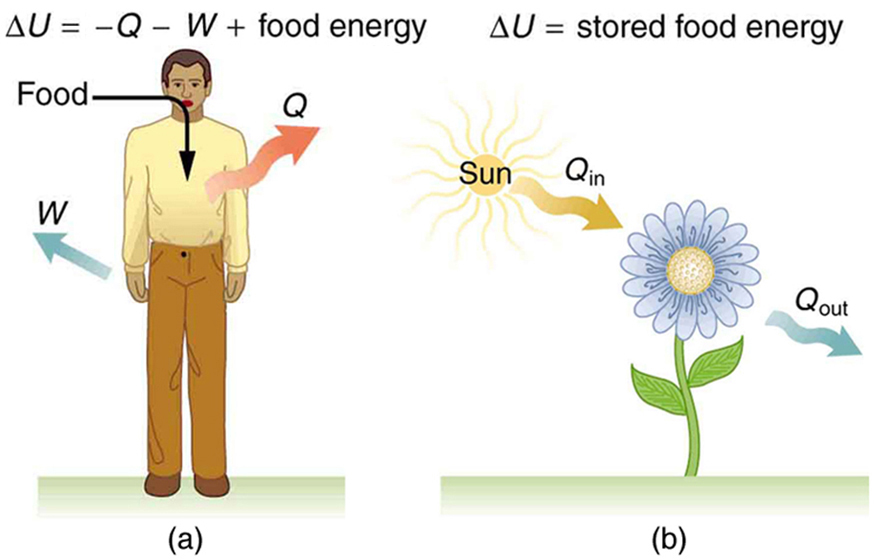
This can also be interpreted as the heat flow from the hot fluid equals the energy the cold fluid gains (in an idealized system with no heat loss to the surroundings).
Various heat exchangers use specific flow patterns to enhance heat transfer. Both fluids enter in a parallel flow heat exchanger at one end, gradually reducing ΔT along the exchanger's length. In a counterflow exchanger, the fluids enter from opposite ends, maximizing ΔT and improving transfer.
Thermal radiation is vital for heat exchangers. All objects above absolute zero emit thermal radiation in a broad spectral range. The net radiation heat loss Q from a surface with temperature T₁ and emissivity ε to the environment at temperature T₂ follows the Stefan-Boltzmann Law:
Q = σ A ε (T₁⁴ - T₂⁴)
Unlike Newton’s law of cooling, Q = h A (T₁ - T₂), which assumes a linear relationship between temperature difference and heat flow rate, the Stefan-Boltzmann Law’s dependence on the fourth powers of temperature (T₁⁴ - T₂⁴), demonstrates that radiation heat transfer increases exponentially with temperature. Newton’s Law is more suitable for modeling convection or conduction, particularly at lower temperatures, while the Stefan-Boltzmann Law dominates in high-temperature or radiative systems.
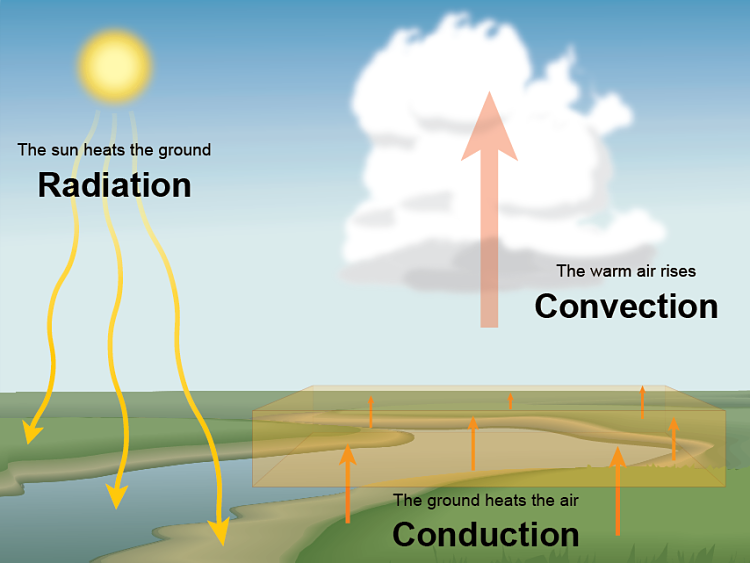
Two types of heat exchangers among many where radiation is relevant are:
(1) Finned-tube heat exchangers in furnaces - in industrial furnaces, radiative thermal transfer between high-temperature gases and finned surfaces enhances the overall efficiency and
(2) Shell and tube heat exchangers with radiation shields: at very high temperatures, the outer shells or inner tubes of the shell and tube heat exchangers may be designed to account for significant radiative heat exchange between surfaces.
Neglecting radiative heat would lead to inaccurate thermal modeling and suboptimal performance.
Effectiveness
Efficiency is crucial in heat exchanger operations. The effectiveness, ε, is the ratio of actual heat transfer to the maximum possible value, calculated as
ε = Qₐ / Qₘₐₓ
where Qₐ is the actual heat transfer, and Qₘₐₓ is the maximum value based on the difference of temperature between fluids.
Engineers optimize performance by considering fluid flow rates, properties, and design features. Increasing the surface area, using fins or turbulators, and selecting materials with high thermal conductivity enhance heat transfer.
Heat Exchanger Simulation
The conduction equation models heat exchange in solids, describing heat conduction based on temperature distribution. Solving it reveals the temperature profile and heat transfer rates in heat exchangers. In the context of battery thermal energy management, the conduction equation is crucial for understanding how heat is transferred within the battery materials. Batteries generate heat during the charging and discharging processes and efficiently managing this heat ensures optimal performance, prevents overheating, and prolongs battery life.
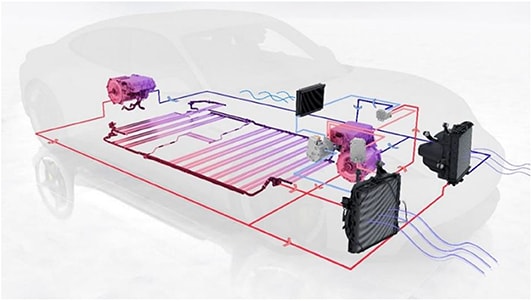
Analytical Solution for Heat Exchangers
Analytical solutions for heat exchangers involve solving equations from first principles, yielding exact results under ideal conditions.
We can think of it like a machine: "in" conditions are geometry and material properties, and "out" is the temperature distribution. These solutions work well for simple cases, like heat flowing through a straight rod or basic flow setups. They provide insights into thermal behavior and serve as benchmarks for complex scenarios.
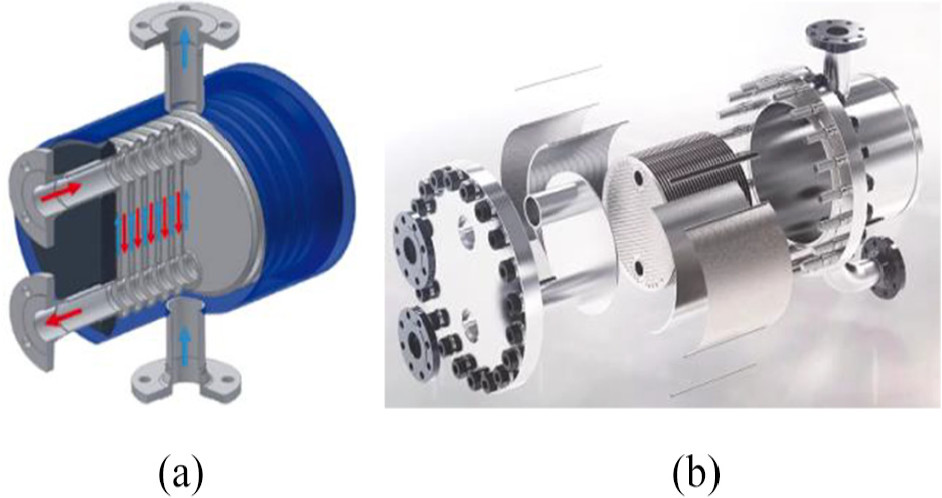
However, real-world heat exchangers often exhibit complex shapes, uneven materials, or turbulent flows, making analytical solutions impractical. Engineers then use numerical methods like FEA or CFD to tackle reality's complexities, though these methods have steep learning curves. This explains the introduction of Deep Learning to assist designers and democratize simulation for modeling heat exchange.
Thus, while analytical solutions are theoretically elegant, they're merely a perfect blueprint—not the complete construction plan, as discussed later in the article.
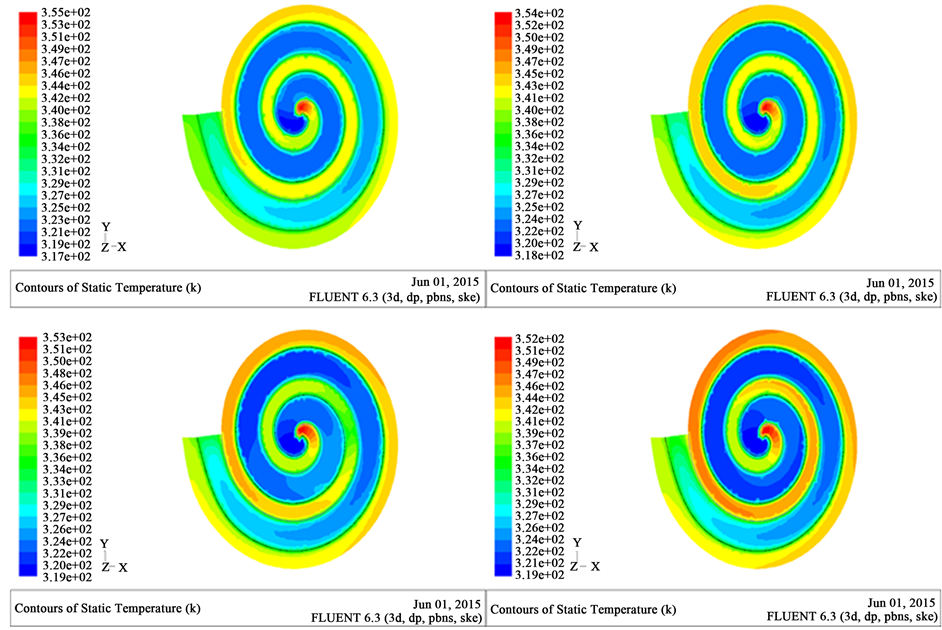
1D to 3D Simulation of Heat Exchangers
Numerical methods solve the conduction equation for intricate geometries. This equation applies to 1D, 2D, or 3D heat exchange processes and incorporates time dependence: these methods provide insights into heat transfer for complex geometries and conditions. They discretize objects by meshing and approximating temperatures at each point.
Standard methods for heat and fluid flows prediction include the Finite Difference Method (FDM), Finite Element Method (FEM), and Finite Volume Method (FVM), for instance CFD.
Deep Learning for Heat Exchangers
Recently, Jensen Huang from NVIDIA has delineated three stages of AI evolution:
- "Perception AI" deals with understanding and interpreting data like images and text;
- "Generative AI" focuses on creating new content or data;
- "Agentic AI" involves AI systems that can reason, plan, and execute tasks autonomously.
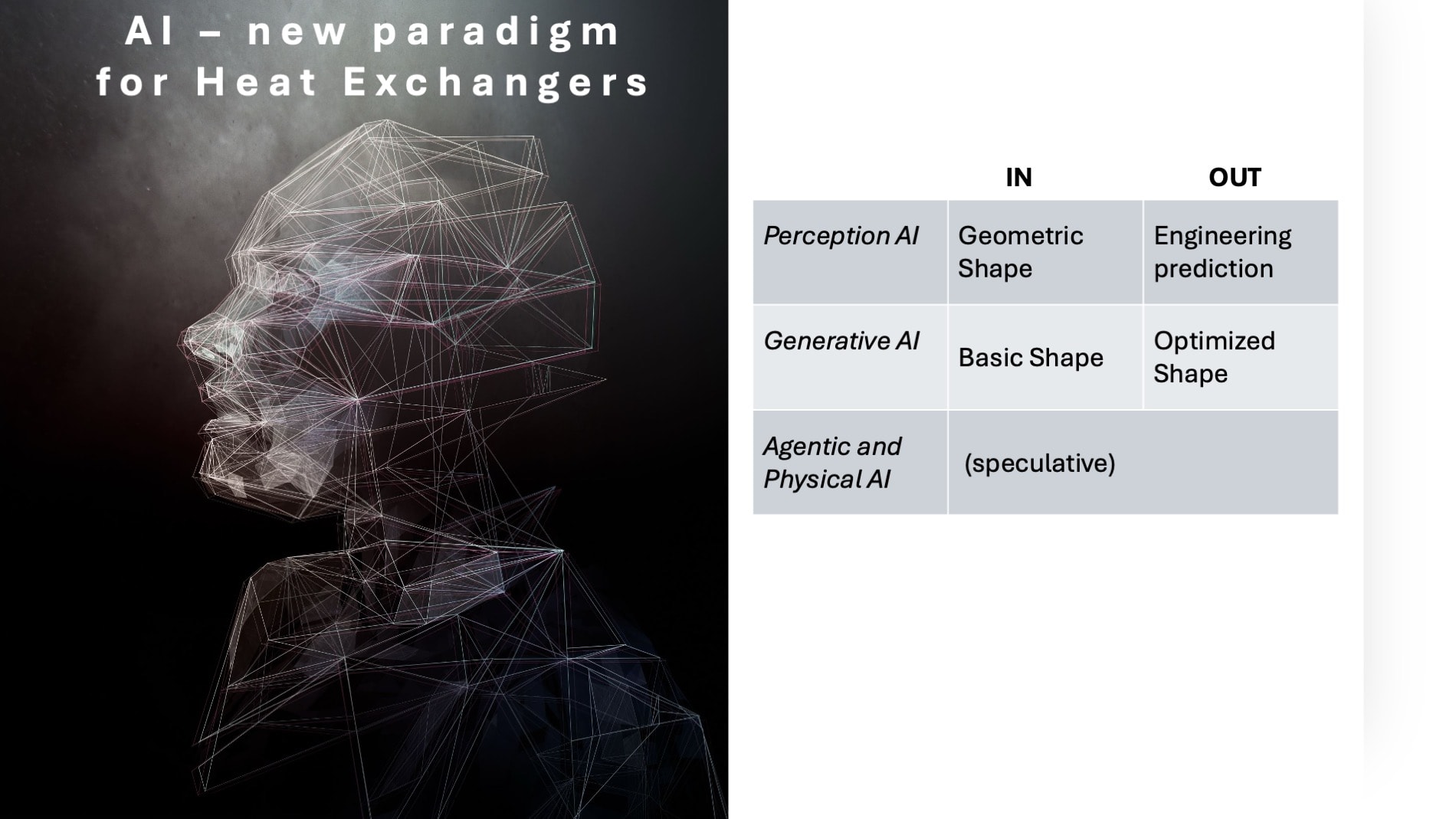
Perception Stage: Prediction
Various industries have stored simulation histories in the company's PLM (Product lifecycle management) system, which are also related to various heat exchangers. However, can these data be utilized more productively beyond storing and retrieving them?
3D Deep Learning helps with a data-driven approach that can simulate various heat exchanger types and potentially any object with any simulation.
The Neural Concept Shape approach leverages deep learning to understand the connection between shape (CAD) and functionality (CFD), creating custom surrogates for the fluid flow prediction via CFD or CAE in general for any physical situation involving flow, heat, stress, or electromagnetism. Several comparisons between AI and CAE results show excellent correlation for the tested samples.
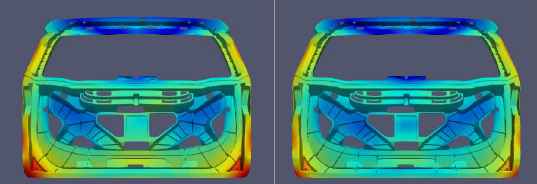
Generative Stage: Optimization
The Neural Concept solution is particularly suitable for design engineers and anyone wishing to operate on heat exchanger geometries to optimize their performance, with a background in technology, product management, and materials but without specific competence in 3D Simulation. Using an embedded Deep Learning predictor in a design workflow, the designer can interactively explore her design space or even start an "optimization campaign" to produce a generatively designed heat exchanger, as in the figure, thanks to machine learning optimization.
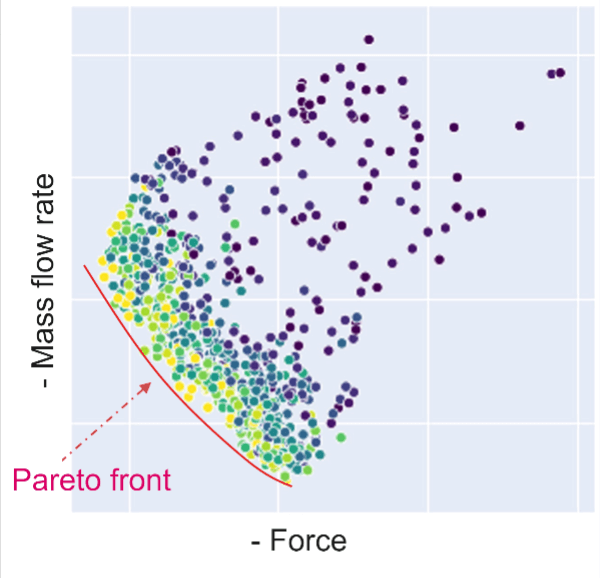
Agentic Stage: Operation (Speculative)
Agentic AI involves autonomous decision-making and action-taking based on perceived data and generated solutions. In the Deep Learning and Simulation context, this speculative scenario would involve an AI that designs, operates, or manages the heat exchanger in real time. It would adjust operations based on current conditions, optimize flow rates, switch operational modes, or suggest maintenance based on data analysis. This AI would be an intelligent agent, making decisions to meet goals without human intervention.
Conclusion
We reviewed various types of heat exchangers, exploring their broad spectrum of applications across different industries. We detailed techniques for extending these essential devices' durability and operational efficiency. Central to our article was an in-depth classification of heat exchanger types. We categorized them according to geometric shape and flow configurations since these factors play a critical role in their performance. Thus, the reader can now distinguish between a tube heat exchanger, a shell heat exchanger, and a tube heat exchanger.
Additionally, we examined a wealth of design resources available for these technologies, considering best practices and industry standards for various types of heat exchangers. We reviewed prediction methods. We started with simplifying assumptions on the heat transfer coefficient and landed on leading-edge topics of AI. We underline how cutting-edge AI technology is more than "being cool", demonstrating remarkable potential in analyzing and optimizing the efficiency of heat exchangers in industrial design environments.
This paves the way for future advancements in energy transfer systems.
Stay tuned for more articles on this subject in the future... it's still hot!
FAQ
What are the advantages of a heat exchanger?
A heat exchanger is designed to exchange heat between fluids without mixing them. This enhances energy efficiency, reduces operational costs, and minimizes environmental impact.
What is a sensible heat exchanger?
A sensible heat exchanger transfers heat between two fluids (or, solid+fluid) without phase changes. Heat transfer occurs when a temperature difference affects the fluids' thermal energy (sensible heat).
What is a compact heat exchanger?
It is designed with a high surface area to volume ratio for efficient heat transfer in limited space.
Is a condenser a heat exchanger?
Yes, a condenser is a heat exchanger that removes heat from a vapor to condense it into a liquid.
What is an industrial heat exchanger?
It is used in industrial processes to exchange heat between two or more fluids, often for cooling or heating purposes in manufacturing.