The Role of AI in Transforming Industrial Engineering Processes
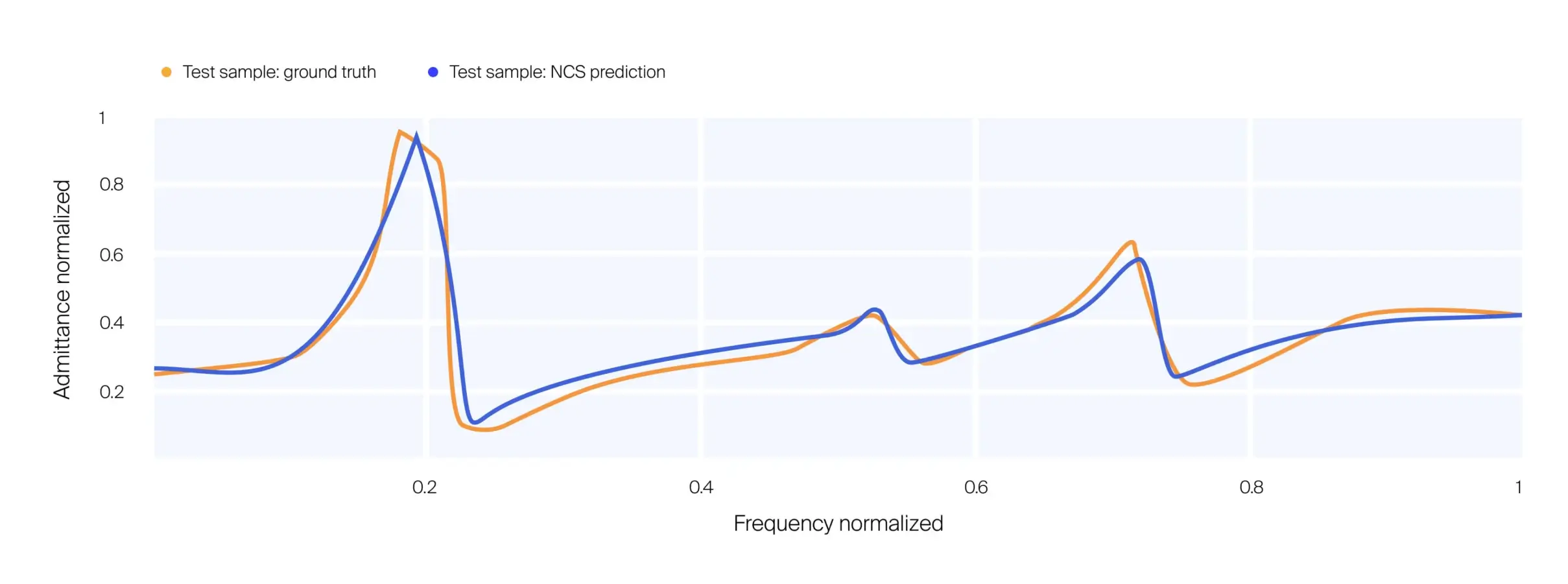
Industrial engineering is changing at an exciting pace, largely thanks to the integration of artificial intelligence (AI). Industries face increasingly complex systems, and the need for efficiency has never been greater to stay competitive. In this article, we’ll describe how AI is transforming industrial engineering. We’ll cover how AI enhances process optimization, predictive maintenance, supply chain management, and robotics. We will also address the challenges that come with implementing these technologies in the workplace. Join us as we explore how AI is paving the way for smarter decisions and a boost in productivity!
What is Artificial Intelligence and Core Technologies
Artificial Intelligence (AI) is a field of computer science focused on creating systems capable of performing tasks that typically require human intelligence. AI applications include recognizing patterns, learning from data ranging from customer satisfaction to operational data captured by smart devices, making decisions, and adapting to new incoming information.
AI encompasses a variety of approaches and techniques that enable machines to process information and generate the above "intelligent" outcomes for industries. Thus, data analysis becomes more efficient, predictive, and adaptive, enabling innovative solutions in various domains. We will first briefly review the history of AI applications, from its "uselessness" in the 90’so the current deployment of AI in engineering.
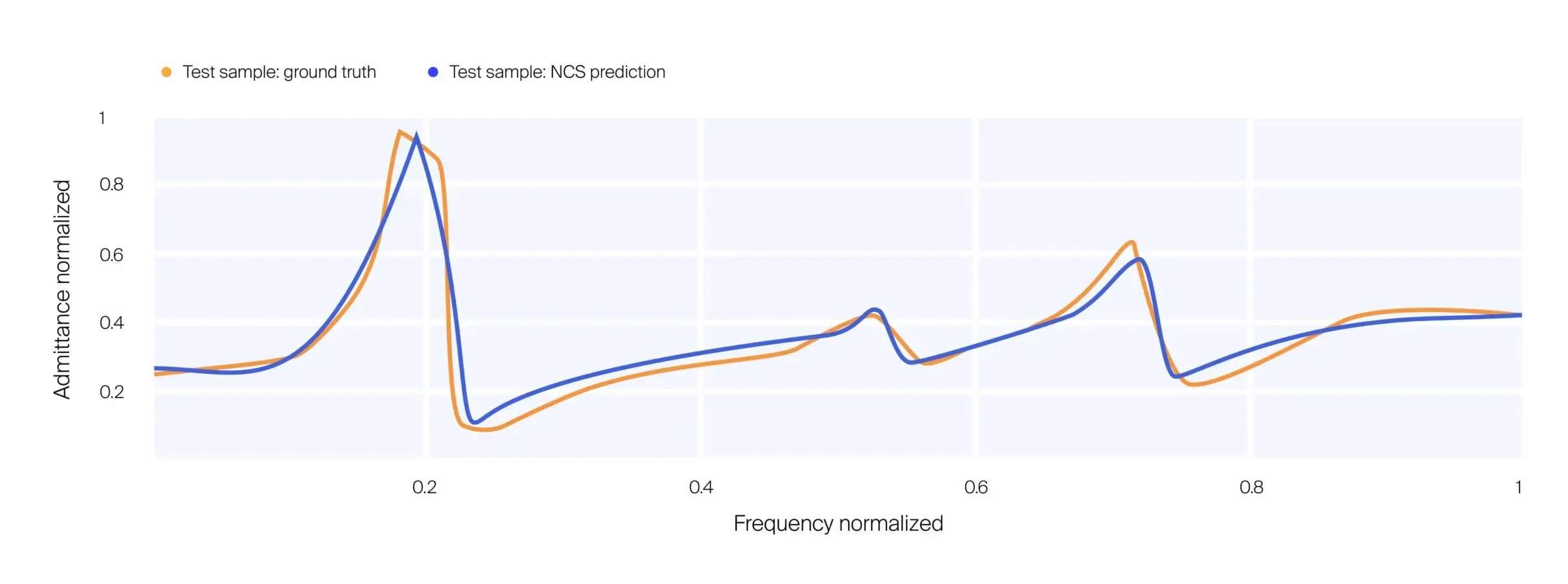
History of AI Applications - AI in Industrial Engineering
The development of Artificial Intelligence and AI applications has been marked by alternating periods of optimism and stagnation. Early AI research in the 1950s and 1960s saw the emergence of symbolic AI, focused on rule-based systems. However, computational limitations and overpromised expectations of the future led to a “Winter” in the 1970s and 1980s, marked by reduced funding and interest.
In the 1990s, AI began a resurgence with advancements in machine learning (ML), driven by increased computational power and larger datasets. The early 2000s introduced data-driven approaches like Support Vector Machines and early neural networks.
By the 2010s, Deep Learning revolutionized the range of AI applications. Techniques such as convolutional neural networks (CNNs) and recurrent neural networks (RNNs) enabled breakthroughs in image recognition, computer vision, NLP, and autonomous systems. In industrial engineering, AI applications were found to optimize supply chains, perform predictive maintenance, control quality, and automate factory automation, thus creating the revolution of AI in industrial design.
CNNs, for example, transformed quality control by enabling real-time visual inspection of products on production lines, identifying defects with previously unattainable precision. Predictive maintenance, leveraging RNNs and other temporal models, analyzed sensor data streams to predict machinery failures before they occurred, drastically reducing downtime and repair costs. AI-driven supply chain optimization utilized reinforcement learning and dynamic programming to improve logistics efficiency, better inventory management, and production schedules, adapting to fluctuating market demands.
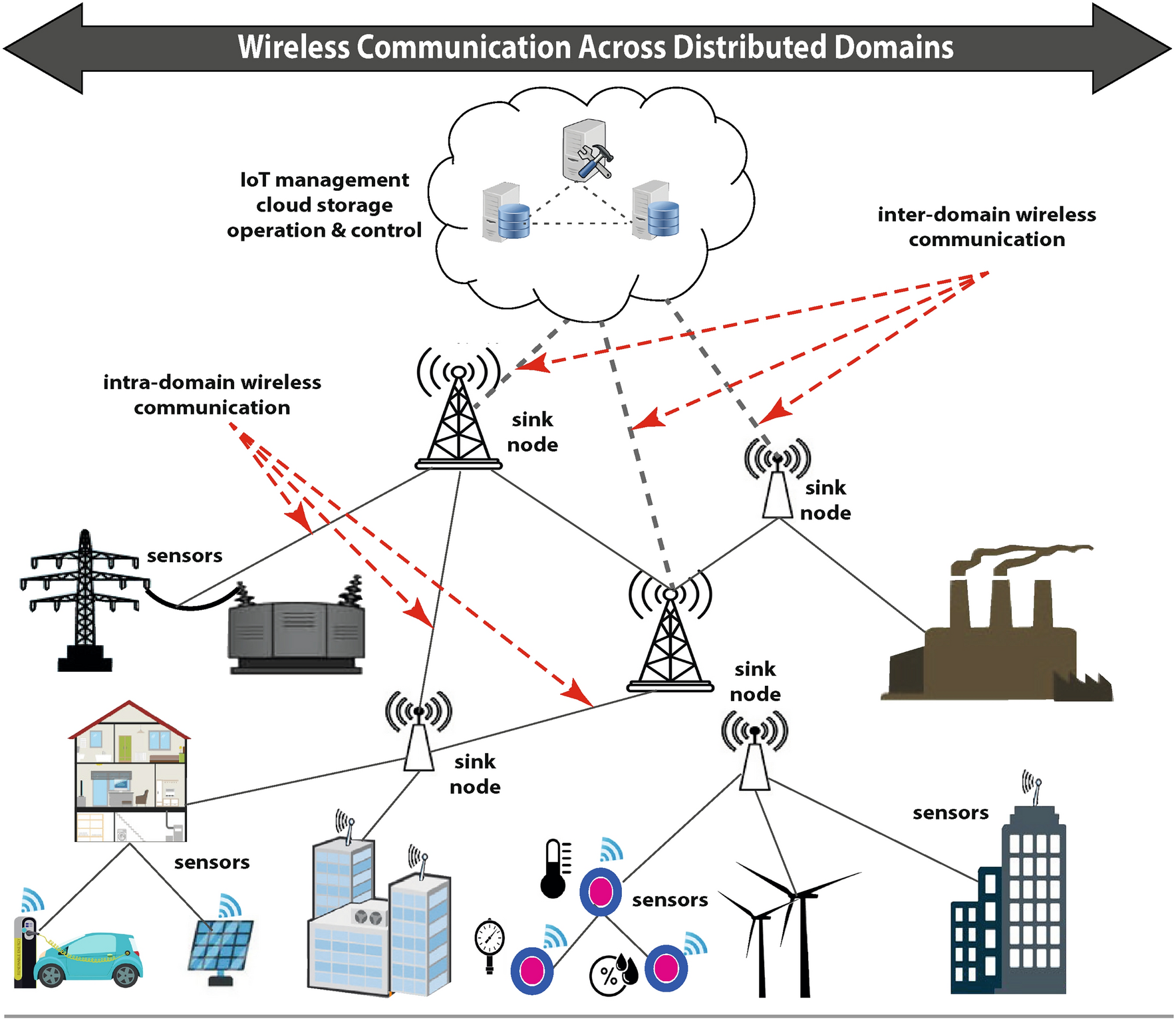
Autonomous robotics, powered by AI, further revolutionized factory automation, handling complex tasks such as material handling, sorting, and assembly. These systems are integrated with smart devices known as Internet of Things (IoT), to create ‘smart factories,’ where AI algorithms process vast amounts of sensor data to adjust operations for optimal dynamic performance.
This highlights the evolving interplay between Industrial Design vs. Industrial Engineering, as both fields adapt to leverage AI-driven technologies for efficiency and innovation
AI’s integration with simulation software in areas like finite element analysis (FEA) enhanced the design of durable, energy-efficient systems by allowing engineers to explore and validate a broader range of designs more efficiently.

Today, AI in industrial engineering leverages Deep Learning to enhance process efficiency, reduce downtime through predictive analytics, and facilitate real-time decisions. AI in additive manufacturing processes enhances real-time monitoring, defect detection, and process optimization through machine learning techniques. It also enables design automation and predictive maintenance, improving production efficiency, quality, and scalability.
Machine Learning and NLP in Industrial Engineering
Machine learning (ML) is a prominent branch of Artificial Intelligence in which algorithms improve their performance by analyzing data. For example, supervised Machine learning involves training models on labeled datasets to make predictions, while unsupervised Machine learning detects structures in unlabeled data. Reinforcement Machine learning involves systems learning optimal behaviors through trial and error in a dynamic environment. The relevance of Machine Learning (ML) for industrial engineering lies in its ability to handle complex, high-dimensional data and optimize processes that are challenging to address through traditional engineering methods. ML, particularly in supervised learning, excels at predicting equipment failures by analyzing historical data from sensors, such as vibration or temperature logs. Techniques like Random Forests or Gradient-Boosted Trees identify patterns that show potential breakdowns, minimizing downtime and maintenance costs. Reinforcement learning enables systems to explore decision paths and autonomously optimize industrial processes.
Another critical domain is natural language processing (NLP), which enables machines to interpret, understand, and generate human language. NLP makes applications like text summarization and translation possible. In multilingual organizations, NLP algorithms from platforms like Google Translate or DeepL provide accurate technical translations, breaking down language barriers in global operations. Computer vision, another vital area, focuses the latest research on enabling systems to analyze and interpret visual inputs. Examples are recognizing objects in images or detecting anomalies redudcing waste and promoting sustainable manufacturing processes.
For example, NVIDIA’s DeepStream SDK enables real-time visual analysis in assembly lines. AI models can recognize and classify visual patterns to detect product defects in semiconductors, automotive parts, and consumer electronics. These systems leverage convolutional neural networks trained on vast amounts of data (images) to identify even microscopic flaws, improving production accuracy and reducing waste.
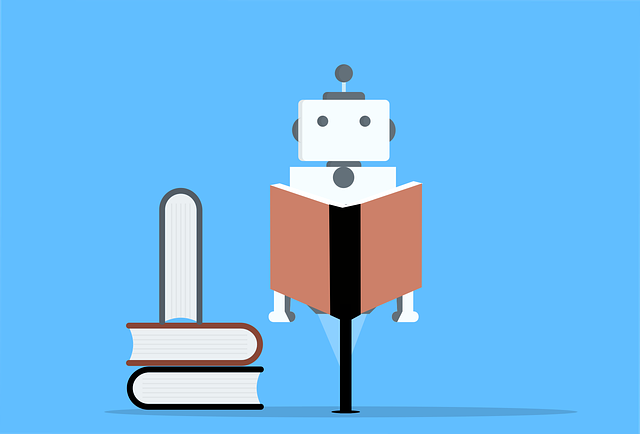
Role of Mathematics and Data Analysis - AI in Engineering
Artificial Intelligence relies on mathematical foundations, particularly linear algebra, for operations like matrix operations in neural networks and probability theory, which helps manage uncertainties in data. Optimization techniques are also fundamental in training Artificial Intelligence models, allowing them to efficiently minimize error and maximize accuracy. The availability of the so-called "big data" (vast amounts of data) and computational power drives the practical implementation of Artificial Intelligence.
An example of the creation of vast amounts of data is predictive analytics techniques such as CAE (3D engineering simulation, e.g., Finite Elements and CFD). AI algorithms, such as convolutional networks, process this data to develop models in real-world scenarios. Data science is pivotal in bridging the gap between raw information and actionable insights, enabling the application of AI in product development. Engineers can extract patterns from vast datasets generated by simulations like CAE by leveraging machine learning techniques, improving decision-making processes based on modifying industrial shapes by operators (designers) or algorithms.
Thus, AI-driven systems can support predictive analytics by emulating (surrogating) CAE tools thanks to 3D Deep Learning capability. Finally, optimization algorithms can be coupled with predictive analytics.
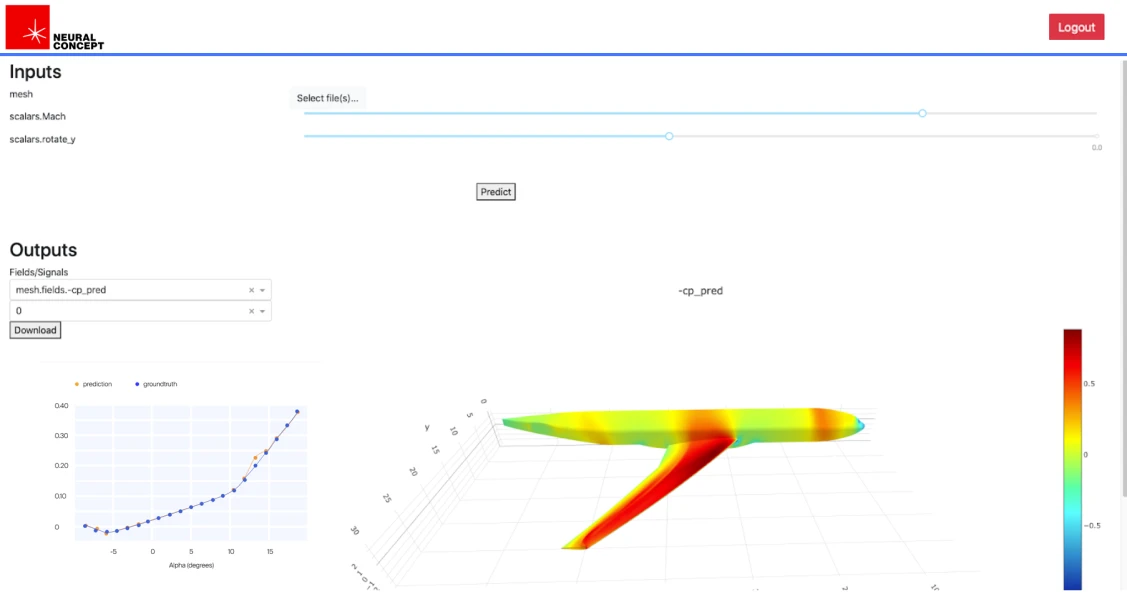
In industrial engineering, machine learning techniques such as supervised or deep learning enable predictive analytics for failure prediction, risk assessment, and process optimization. These methods analyze the results of simulations or operational data to create intelligent systems that enhance productivity and reduce costs. Data science and the growing computational capacity allow industrial engineering to embrace real-time analysis and adaptive systems. Machine learning techniques, particularly neural networks and ensemble models, ensure that engineers can optimize workflows, predict outcomes accurately, and innovate across manufacturing processes and supply chain optimization. AI is revolutionizing supply chain and logistics management by providing real-time insights.
AI and Process Optimization
In industrial engineering, refining workflows and maximizing resource efficiency are key objectives. AI is changing how these goals are achieved through data analysis. Industrial systems often face variability due to fluctuating demand, equipment performance, or unforeseen disruptions. AI technologies can process real-time data and adapt operations to these changes. For instance, in manufacturing, AI algorithms can reconfigure assembly lines or adjust material flows to avoid bottlenecks and keep production on track. But it’s more than future "self-configuring factories," as some experts have outlined. In the future, Industry 5.5.0 will increase efficiency while taking a more human-centric approach to AI.
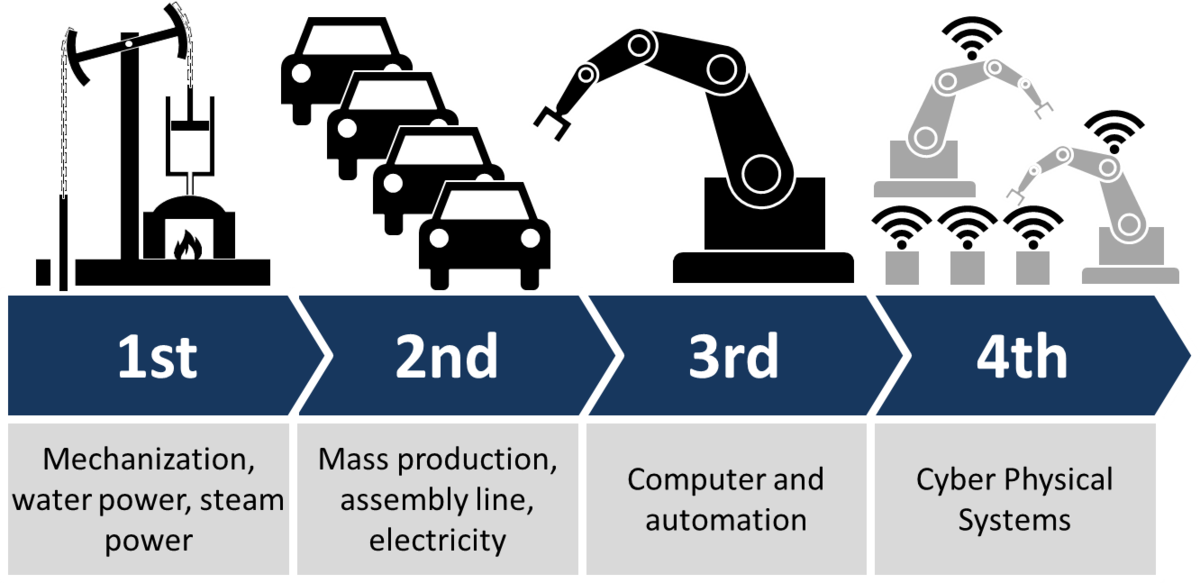
Machine learning technologies allow industrial engineers to evaluate potential changes before implementing them. Simulations can predict how adjustments in scheduling, equipment use, or logistics might affect overall performance. This capability reduces the risk of costly mistakes and ensures that changes lead to tangible improvements.
Maintenance Costs with AI in Industrial Engineering
AI-driven analytics identify points of inefficiency that might go unnoticed with traditional methods. Whether it is a delay in material handling, an imbalance in workforce allocation, or inefficiencies in energy use, Machine learning provides targeted recommendations to eliminate these issues and enhance throughput.
Maintenance strategies in industrial engineering can lead to increased productivity and reduced costs in various industries where machinery and equipment are the backbone of operations. Predictive maintenance leverages AI technologies to anticipate problems and minimize downtime. Sensors embedded in industrial equipment generate continuous data streams, tracking parameters like temperature, vibration, and power consumption. AI algorithms analyze this data to detect anomalies indicating wear or impending failure. For instance, an AI system monitoring a conveyor belt might detect slight variations in motor vibration that suggest a misalignment. Early warnings allow maintenance crews to address the issue before it causes a breakdown, with an evident reduction in maintenance costs.
Economic and Operational Benefits of AI
The implementation of AI in industrial engineering and maintenance delivers measurable benefits:
• Lower Costs: Repairs conducted proactively are less expensive than emergency fixes.
• Minimized Downtime: Early warnings prevent unexpected halts in the production schedules.
• Extended Equipment Life - Predict Potential Failures: AI helps to predict failures and keep machinery operating under optimal conditions, delaying the need for replacements.
AI greatly enhances supply chains, influencing profitability and customer satisfaction. It optimizes processes from sourcing materials to delivering goods. Accurate inventory levels are crucial to prevent shortages and surpluses. AI systems analyze historical data and market trends to maintain optimal stock levels, ensuring materials are available without excessive capital tied in inventory. They predict demand by examining sales patterns, seasonal trends, and factors like economic conditions; an AI system can forecast higher demand during heatwaves. AI also improves logistics routes by considering traffic, fuel costs, and delivery schedules, adjusting in real-time to minimize delays and cut transportation costs.
Robotics and Automation in Industrial Engineering
Robotics has long been a part of industrial engineering, but AI enhances its capabilities by enabling machines to adapt to changing environments and perform more complex tasks.
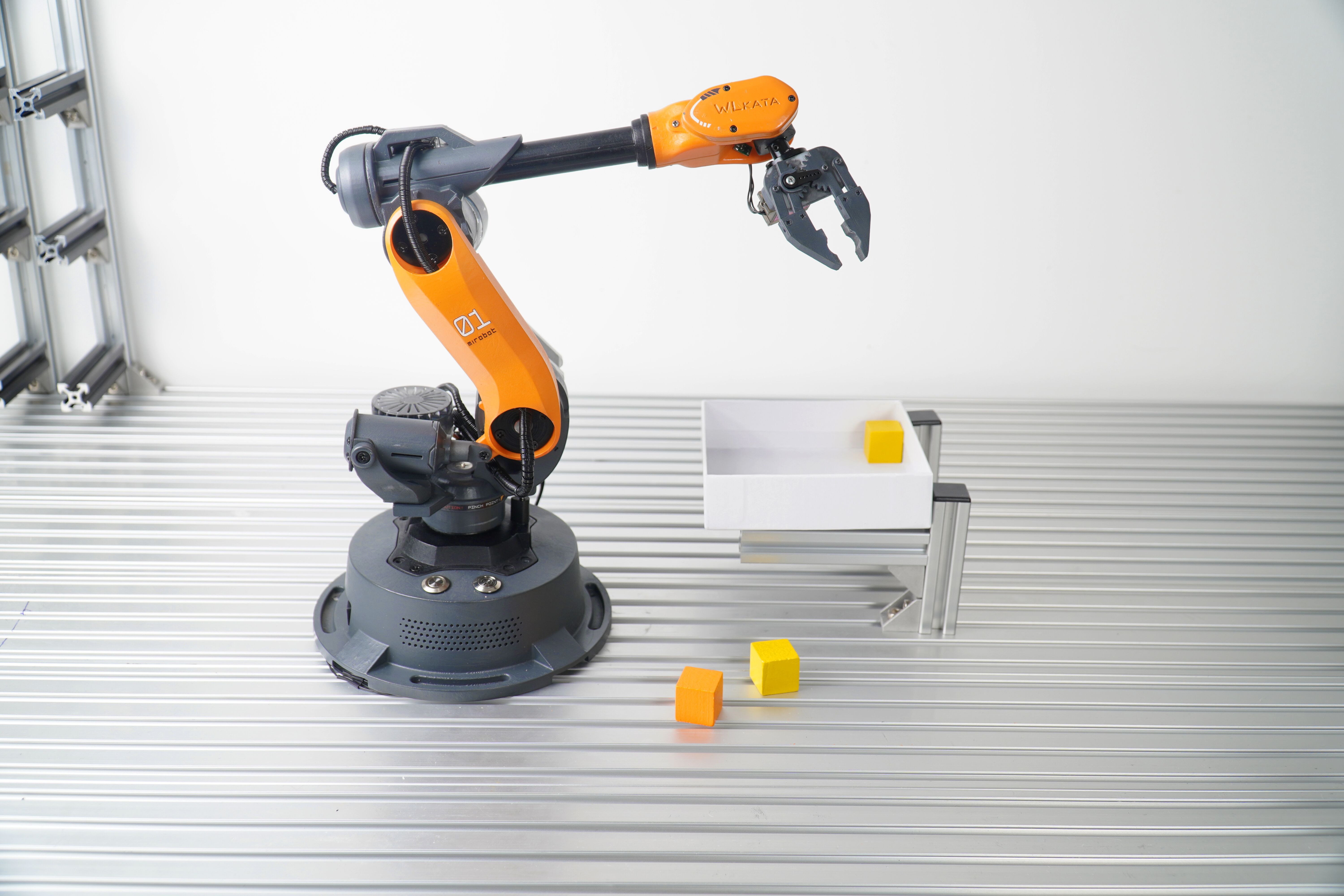
AI in Industrial Engineering: Intelligent Robotics
Robotics and automation exemplify AI applications in industrial engineering. AI algorithms enable robots to learn from experience, recognize patterns, and refine their actions. For instance, on an assembly line, AI-equipped robots detect component variations and adjust their movements to ensure proper assembly without stopping the line.
Safety and Precision
AI-enhanced robots improve workplace safety by taking over hazardous tasks for humans. They also deliver unparalleled precision in welding, material cutting, or delicate assembly, resulting in higher-quality products.
AI’s Role in Professional Development
AI reshapes industrial processes and opens new opportunities for engineers to grow their skills.
Access to Learning Resources
Industrial engineers can use AI-driven platforms to access courses, webinars, and industry insights that deepen their understanding of AI applications. These Artificial Intelligence resources help professionals stay current with technological advances and integrate them effectively into their work.
Emerging Career Opportunities in AI
Adopting AI creates demand for specialized roles, such as data scientists and Artificial Intelligence consultants. Engineers with AI and industrial systems expertise are uniquely positioned to lead projects and innovative solutions that bridge these disciplines.
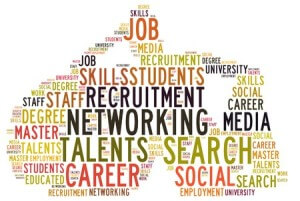
AI Implementation
While AI has transformative potential, Artificial Intelligence also presents challenges that industrial engineers must address!
AI Algorithms and Data Analysis
Artificial Intelligence systems rely on high-quality data to produce reliable insights. Inaccurate or incomplete data can lead to flawed predictions or suboptimal decisions. To overcome this hurdle, AI Engineers must establish robust data collection and validation processes during data analysis.
The integration of AI requires a whole engineering workforce proficient in its use. Engineers must acquire skills in data analysis to work effectively with AI tools and systems, which can be a barrier for those unfamiliar with the technology. AI systems can inadvertently perpetuate biases present in their training data. To avoid unintended consequences, industrial engineers must ensure that AI solutions are fair, transparent, and aligned with ethical standards. Introducing AI often meets antagonism from employees accustomed to traditional methods. Clear communication and inclusive planning can help address these concerns and build trust in AI systems.
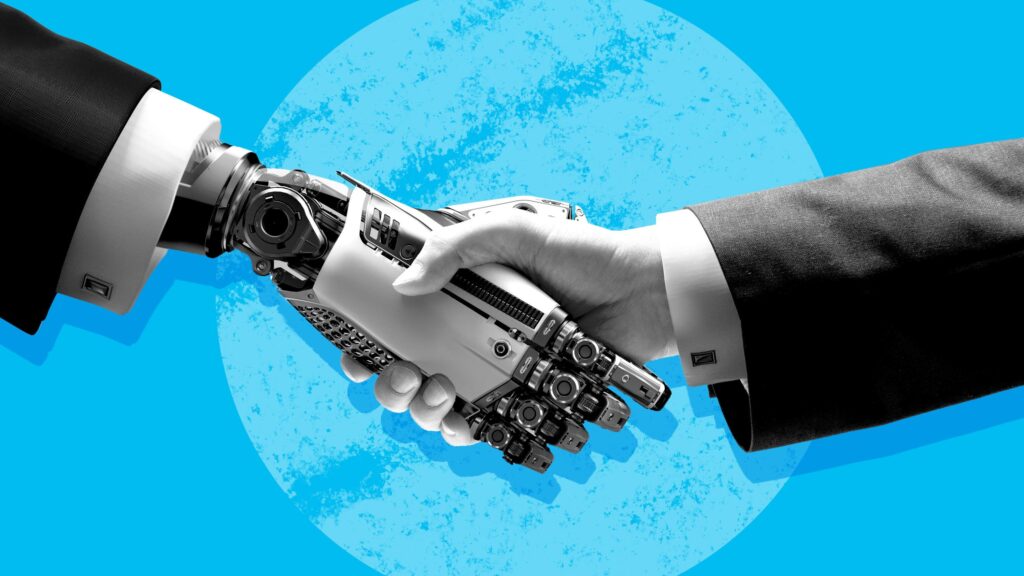
AI in Quality Control
AI has transformed quality control in industrial engineering, making it faster and more precise. Machine vision systems powered by AI can inspect products for defects with exceptional accuracy, even at high speeds. These systems detect flaws and identify defect patterns, helping engineers address underlying issues in production processes. AI helps to reduce waste and increase sustainability. AI systems can analyze usage patterns in industries with high energy consumption and recommend measures to reduce waste while improving efficiency. Additionally, AI supports circular economy principles by identifying opportunities for recycling and repurposing materials. For instance, platforms like Recykal use AI to enable better sorting and repurposing of materials. They integrate AI-powered transactional models to connect waste generators, recyclers, and manufacturers, streamlining the recycling process and ensuring that valuable materials like metals and plastics are extracted and recycled efficiently. Control systems integrated with AI-driven systems enhance operational efficiency by automating adjustments and fine-tuning in real-time. This ensures consistent quality control and drives process improvement by optimizing workflows and reducing waste across the production cycle.
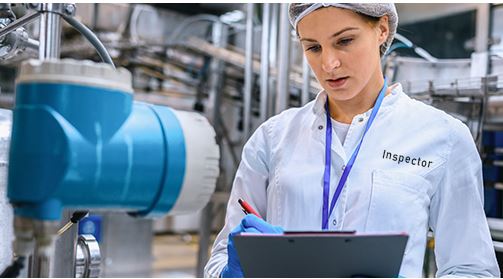
Conclusion
AI is the future of engineering for most industries. The transformation driven by Artificial Intelligence in industries is not merely an upgrade to existing processes. Instead, it is a reimagining of what industrial engineering can achieve in the modern era. AI revolutionizes industrial engineering by bringing efficiency, proactiveness, and innovation to previously rigid and reactive processes. The effect on various industries is extensive and deep, from optimizing workflows for increased productivity and enabling predictive maintenance to supply chain optimization and sustainability. This is likely to grow in the future. Challenges like data accuracy, ethical concerns, and resistance to change in some industries must be addressed. However, the potential benefits of AI technologies far outweigh these hurdles. Industries continue to adopt AI technologies, and the role of industrial engineers will evolve, demanding a balance of technical expertise, strategic thinking, customer satisfaction, and adaptability.
FAQ
Can AI replace an industrial engineer?
AI augments industrial engineers by automating routine tasks. However human expertise remains essential for complex problem-solving and strategic decisions.
Will industrial engineering become obsolete?
No. Industrial engineering evolves with AI, emphasizing roles in AI integration, optimization, and system design.
What industries benefit most from AI in industrial engineering?
The manufacturing, logistics, energy, healthcare, and automotive sectors benefit most from AI-driven increasing efficiency thanks to process optimization.
How can small and medium-sized enterprises (SMEs) adopt AI in industrial engineering?
SMEs can start by implementing AI tools for predictive maintenance, inventory management, or predictive analytics (simulation). They can leverage cloud-based solutions and pre-trained models to minimize initial investment.