What is CAD Technology? Applications and Future Innovations
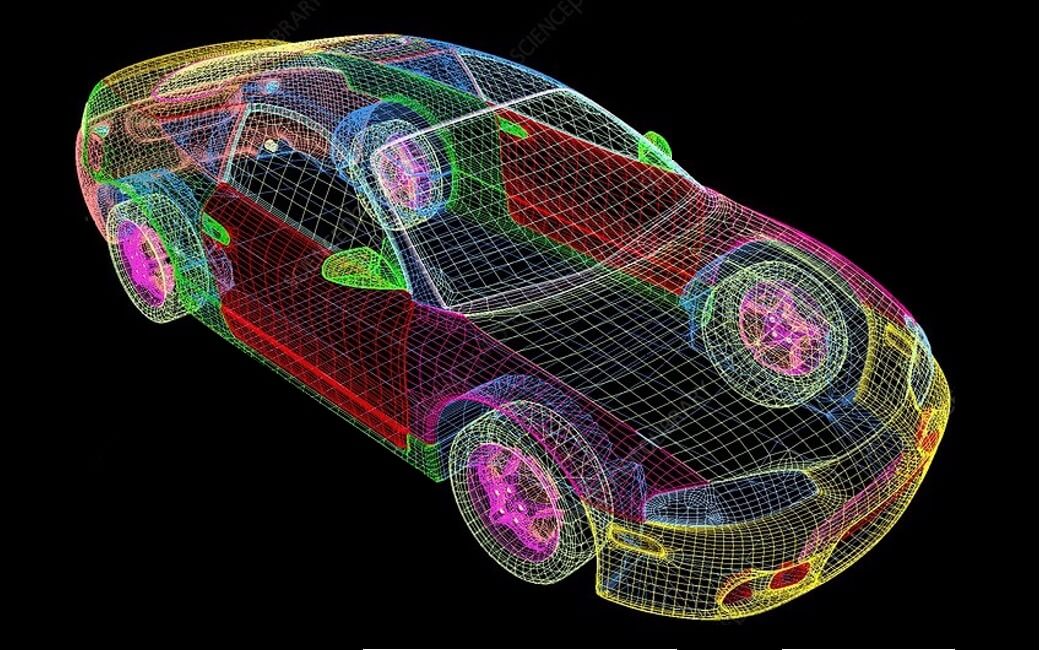
How would engineers and architects design in 2025 without CAD?
The answer is that they wouldn’t. How would engineers and architects design in 2025 without CAD? The answer is, they wouldn’t. CAD has become an indispensable tool for turning concepts into precise, workable models. With the power of GPUs, it transforms abstract ideas into detailed designs that are easy to understand and refine. CAD now integrates seamlessly with cutting-edge technologies like 3D simulation, 3D printing, and AI, enabling once impossible workflows. It’s no longer just a design tool; it’s the backbone of modern innovation.
CAD software has become indispensable for turning concepts into precise, workable models for the architectural and manufacturing industries. The power of GPUs transforms abstract ideas into detailed designs that are easy to understand and refine. A CAD program can now integrate with cutting-edge technologies like 3D simulation, 3D printing, and AI, enabling once-impossible workflows. It’s no longer just a design tool; it’s the backbone of modern innovation.
CAD tools are ideal for supporting iterative design processes and generative design, converting virtual concepts into practical decisions. These CAD software tools have revolutionized the design process and impacted manufacturing processes, demonstrating innovation potential from drafts to advanced 3D modeling and additive manufacturing.
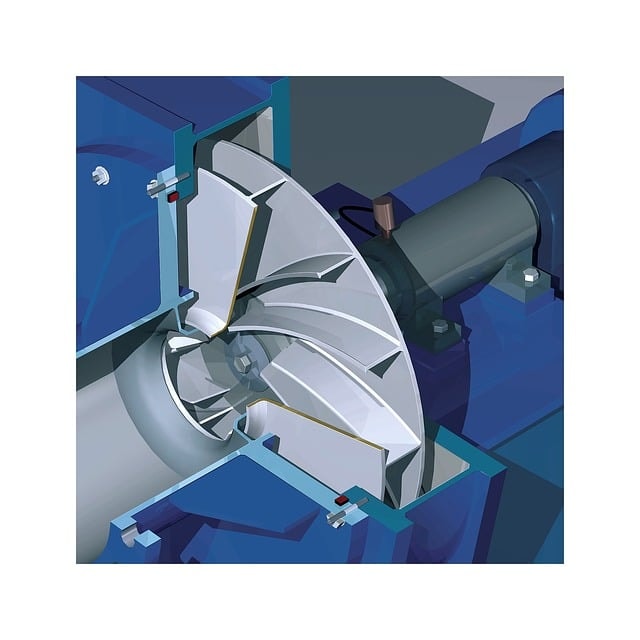
Most companies use computer-based software to create, modify, analyze, and optimize designs for various applications. Computer-aided design enables users to develop precise 2D drawings and 3D models, with advanced features like parametric modeling allowing changes to propagate across the design. In engineering, Computer-aided design enhances project management by ensuring comprehensive documentation and promoting clear communication across teams. Business-wise, Computer-aided design streamlines workflows, cuts costs and boosts product quality.
The article explores advancements such as Artificial Intelligence, generative design, and Virtual Reality, which will further speed up design and foster collaboration.
CAD Technology: Definitions, Examples
Computer-Aided Design (CAD) technology uses computers to create and optimize 2D and 3D models. It includes geometric modeling, computational algorithms, and parametric design tools for precise component rendering. CAD applications are unlimited in terms of industry sectors, ranging from industrial design to product design and manufacturing, and they are also an important input for R&D activities. Whenever a digital replica of real world objects is needed, Computer-Aided Design can help.
CAD software is fully integrated in the "digital thread" concept and is vital for product data management, since its outputs come in the form of electronic files, which are used accordingly for manufacturing processes.
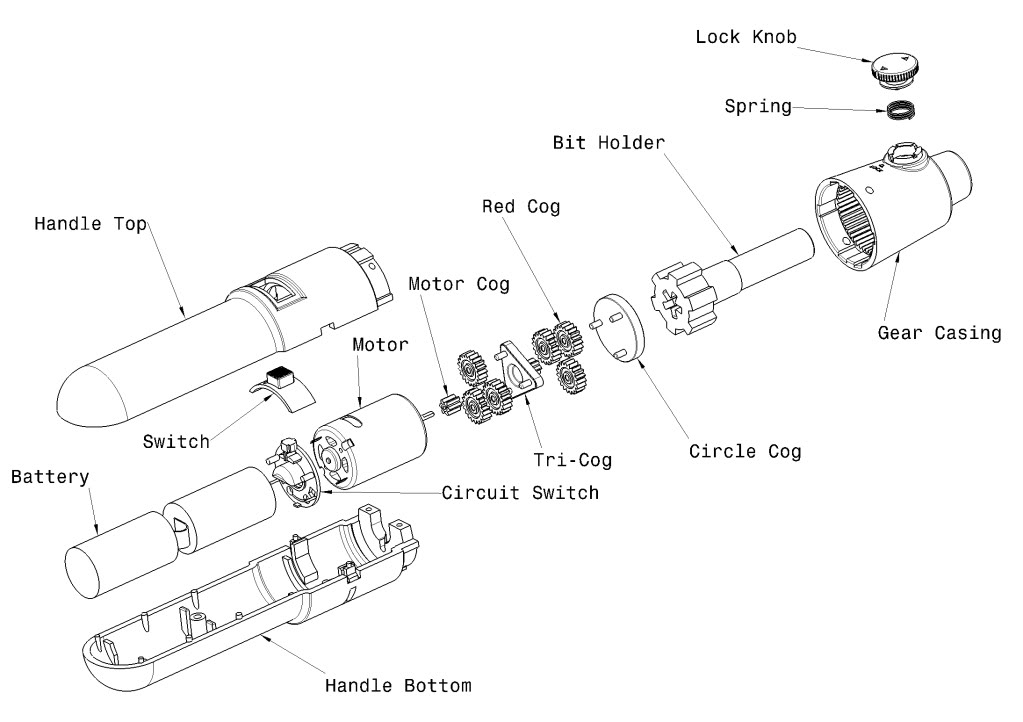
A component is a single part in a model.
An assembly is a collection of components forming a complete system. Virtual assembly simulations validate sequences before physical parts are available.
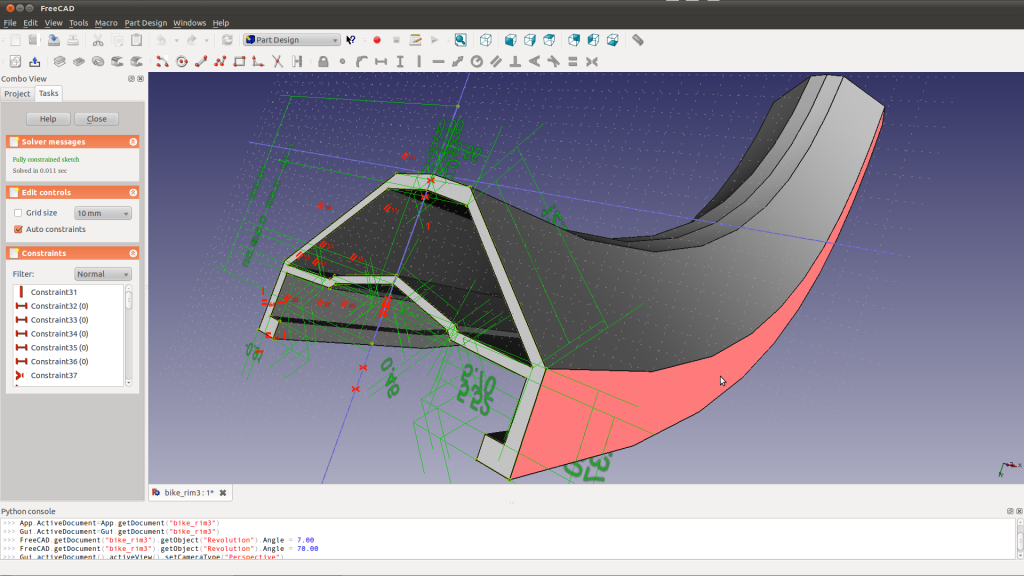
CAD tools use constraint-based modeling to automatically control and update designs through defined geometric and dimensional relationships like alignments, distances, and angles. Standards such as STEP and IGES ensure interoperability.
CAD software outputs come in electronic files used for manufacturing processes.
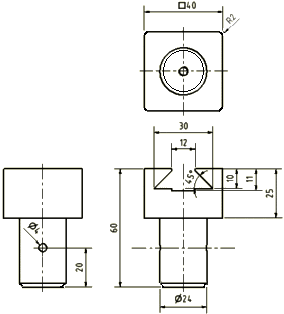
2D CAD software uses fundamental geometric shapes to create flat drawings. 2D is commonly used for designing and planning structures, sectioning, and detailing aspects of architectural projects.
2.5D Computer-Aided Design is an intermediary design tool that combines 2D and 3D CAD aspects.
CAD software, however, often provides a three-dimensional representation of a component or an entire system on a computer screen. As processing power and graphic capabilities improve, 3D CAD software is increasingly adopted. Design engineers can plan and create their work on a computer screen using CAD tools, print it, and save it for upcoming revisions.
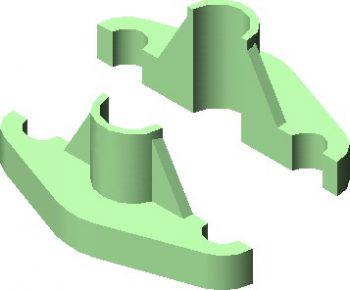
Solid modeling is one of the core features of CAD tools. It allows for the creation of realistic, functional 3D representations of objects. Most CAD software uses parametric modeling to establish functional relationships between design parts. These relationships ensure automatic updates across connected elements, maintaining consistency and reducing manual errors.
Examples of CAD Software
AutoCAD is a popular 2D and 3D CAD software in architecture, engineering, and construction. It is known for its ability to create detailed drawings and blueprints.
SolidWorks focuses on mechanical design and parametric modeling, enabling engineers to build parts and run simulations.
Fusion 360 from Autodesk combines 3D modeling, simulation, and manufacturing and supports CNC machining and 3D printing. These tools meet specific needs while offering strong modeling and simulation capabilities.
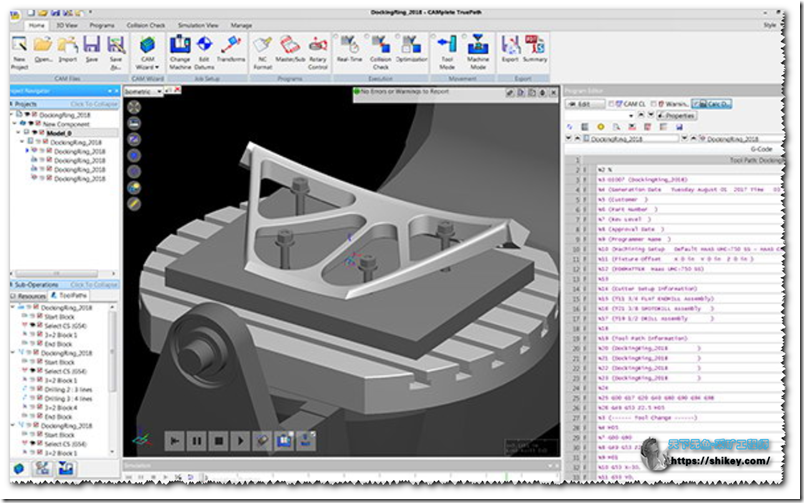
The Evolution of CAD Software
The historical development of CAD software can be traced back to the 1960s when computers were first harnessed for engineering computations and problem-solving. Let's trace the history in this section.
The Birth of CAD Tools
Computer-aided design (CAD) software originated in the 1960s and revolutionized the early manual drafting approach. Sketchpad allowed users to draw and manipulate shapes onscreen with a light pen. Manual drafting was forever changed when computer-based software enabled parametric modeling, which avoided repeating the same things on paper. Collaborations between universities and industry further advanced this technology.
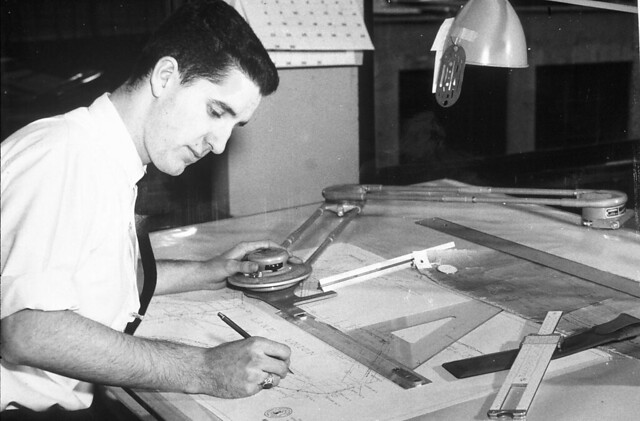
Engineering calculations were not yet closely linked to CAD tools, but the digital path was now open!
The Shift to 3D Modeling (1980s-1990s)
The 1980s saw a shift as CAD software tools adopted 3D modeling. This allowed CAD designers to create virtual representations of objects for better visualization and analysis during the engineering process. A significant development was SolidWorks in 1995, which introduced parametric 3D modeling, enabling changes to propagate across components in engineering projects.
Simulation Integration (2000s)
At the turn of the millennium, simulation was integrated into Computer-Aided Design systems, allowing engineers to simulate behaviors like structural integrity and fluid dynamics during the design process. CAE minimized the need to produce physical objects, saving time and resources and initiating the idea that creating products in a virtual space is possible. Graphics advancements allowed realistic visualization for improved concept presentation. Due to the unavailability of cloud computing, simulations needed local private computing farms.
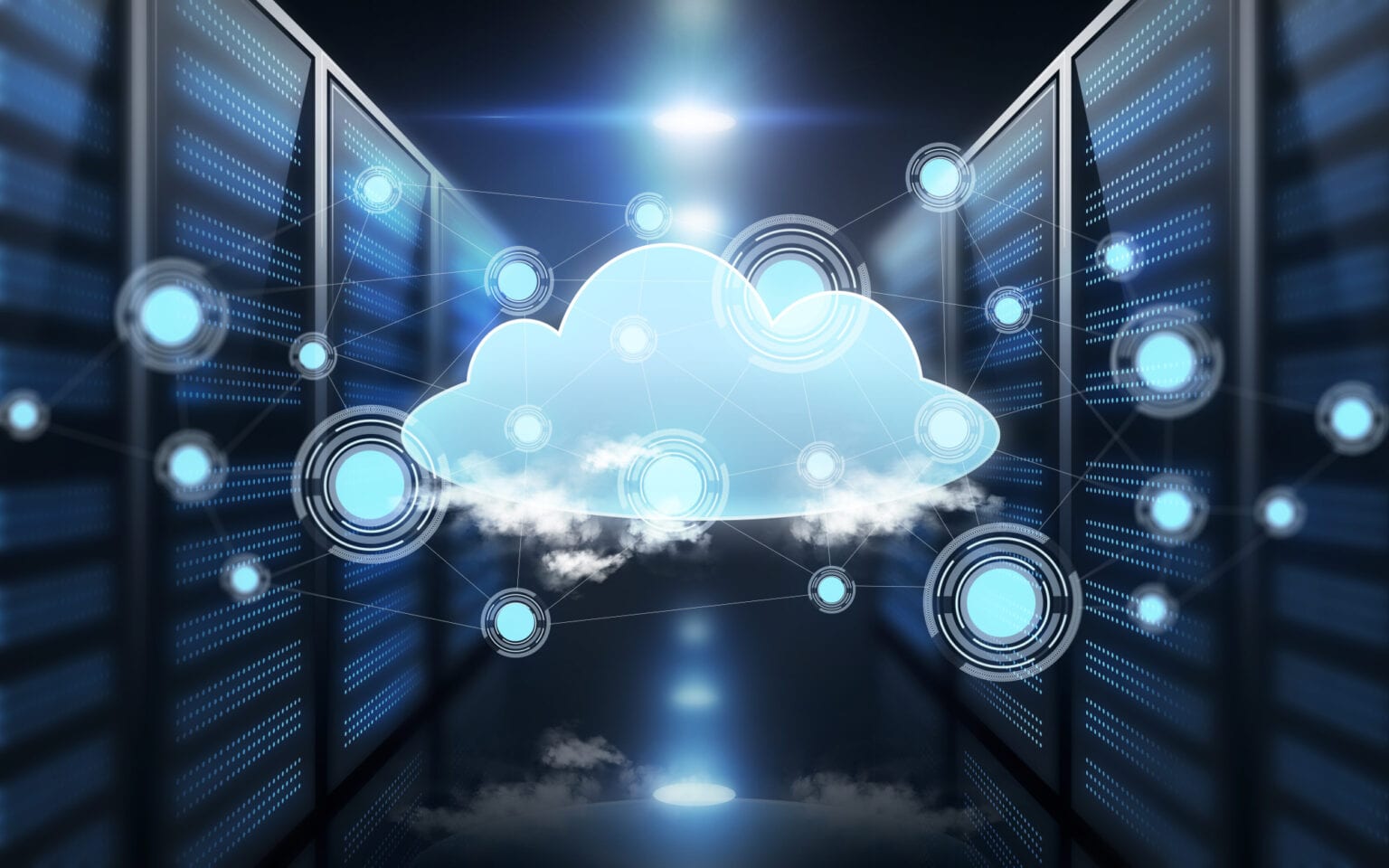
Cloud-Based CAD and Additive Manufacturing (2010s)
The 2010s brought innovations, primarily virtual and augmented reality, and 3D printing. Cloud platforms enabled global collaboration and data sharing, allowing designers to work remotely. This transformed industries by accessing talent and shortening product development. CAD software integrated direct 3D printer connection features, simplifying the transition from digital models to prototypes. Moreover, cloud computing for CAE gained popularity, enabling CFD on remote clusters and lowering IT costs.
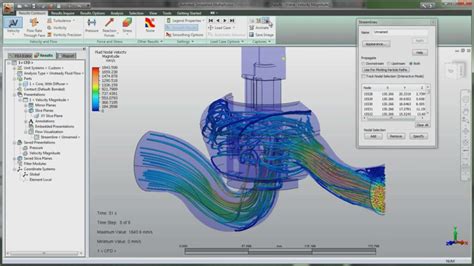
Key Features of Computer Aided Design
Parametric Design is an approach that creates designs based on specific parameters. This method automatically updates models when dimensions or relationships change, keeping the design aligned with defined rules.
2D and 3D Modeling uses software tools to create detailed two-dimensional layouts and intricate three-dimensional models. These tools are essential for design visualization, which helps understand how an object looks and functions and ensures precision in measurements and proportions.
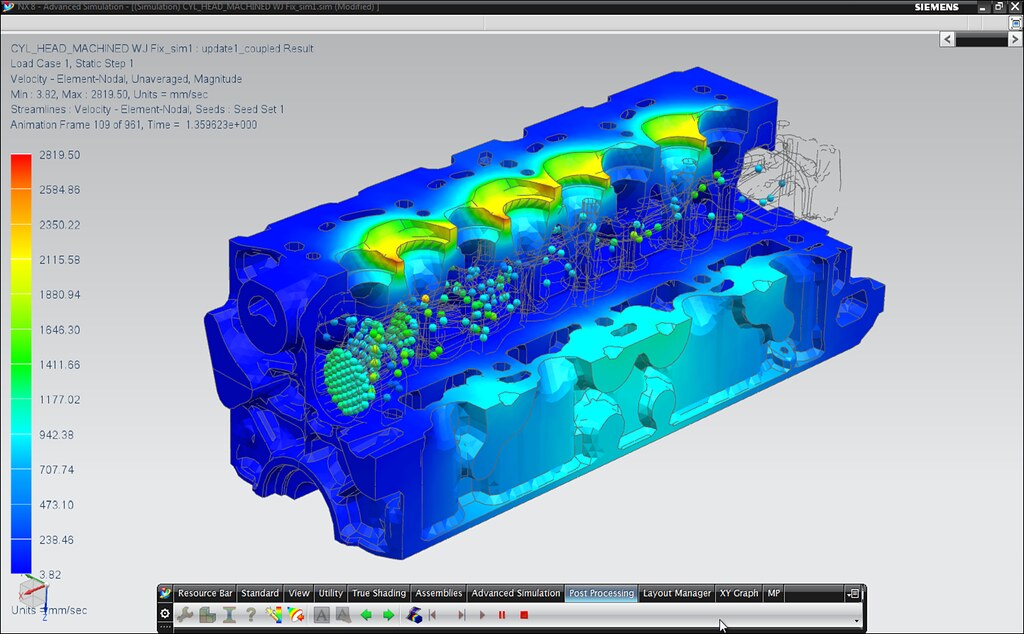
Simulation Capabilities allow designers to test and analyze their models under various conditions, such as stress, motion, heat, and other physical factors. This functionality significantly reduces the need for physical prototypes, saving time and resources by allowing virtual testing and validation of designs. Virtual assembly simulations in Computer-Aided Design can validate assembly sequences before physical parts are available.
CAM software converts models into "G-code" or other machine-specific instructions for CNC equipment. It defines tool paths, cutting speeds, and machining strategies to optimize material removal or additive processes. CAM integration with Computer-Aided Design minimizes manual translation errors and allows for rapid prototyping and precision machining directly from the model.
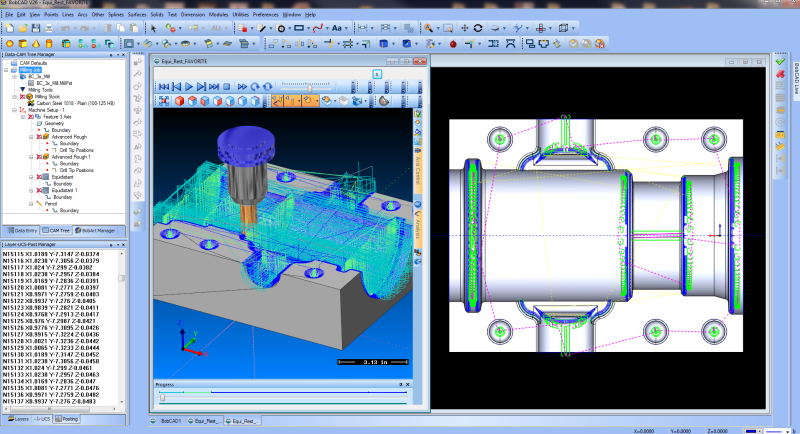
Collaboration tools enable real-time teamwork and streamline workflows for design integrity. PLM systems manage product data from design to disposal. CAD software integrates with PLM for version control and tracking changes, linking CAD models to bills of materials (BOMs) for accurate manufacturing data.
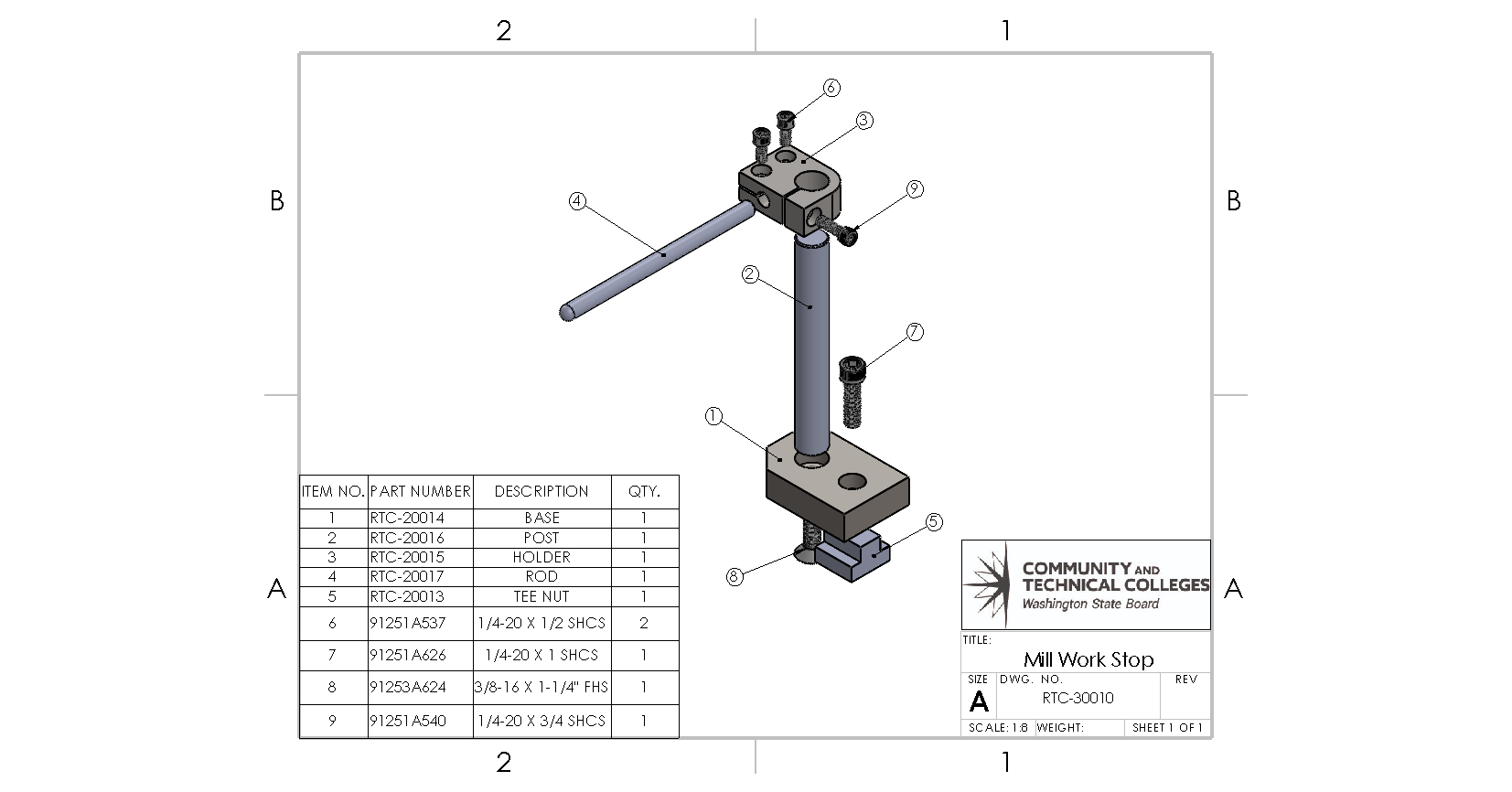
PLM automates workflows like design approval and compliance checks. Tools such as Siemens Teamcenter and Dassault Systèmes ENOVIA are essential in industries that require precise data synchronization, such as automotive and aerospace.
Cloud-based features refer to the ability to access CAD (Computer-Aided Design) tools and designs from any location via the Internet. This capability enhances remote work and collaboration, allowing team members to share and modify designs without being restricted by their physical location.
Computer-Aided Design in the Automotive Industry
The automotive industry has taken the lead in embracing and revolutionizing CAD technology! Computer-aided design has transformed how vehicles are made and how we think about them. Imagine ideas springing to life in digital form. CAD systems have reshaped every facet of vehicle development, from the very first sketch to the final assembly line.
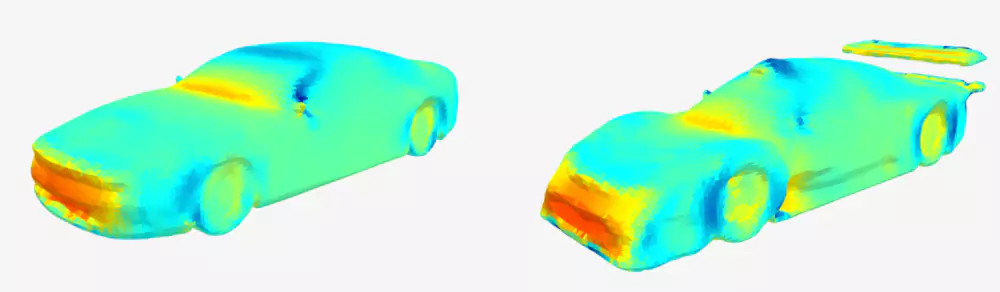
Concept Design and Styling
CAD and simulation tools are essential in automotive design, shaping a vehicle's aesthetic vision. Designers utilize CAD software to model and experiment with various shapes and proportions. 3D modeling allows for all-angle visualization, refining the brand's design language. Simulation tools verify functionality, enabling engineers to progress to the next design phase sooner and avoid late-stage revisions. The shift from Computer Aided Design to simulation has recently streamlined processes, removing tedious meshing operations for product designers and users.
Manufacturing Process and Assembly
In manufacturing, 3D models act as a virtual playground, allowing engineers to spot potential assembly issues before they become real-world problems, ultimately saving time and money.
Simulations enable teams to validate production sequences even before the parts arrive.
Additionally, CAD tools are not just about creating models; they streamline specific manufacturing processes, such as stamping, welding, and assembly.
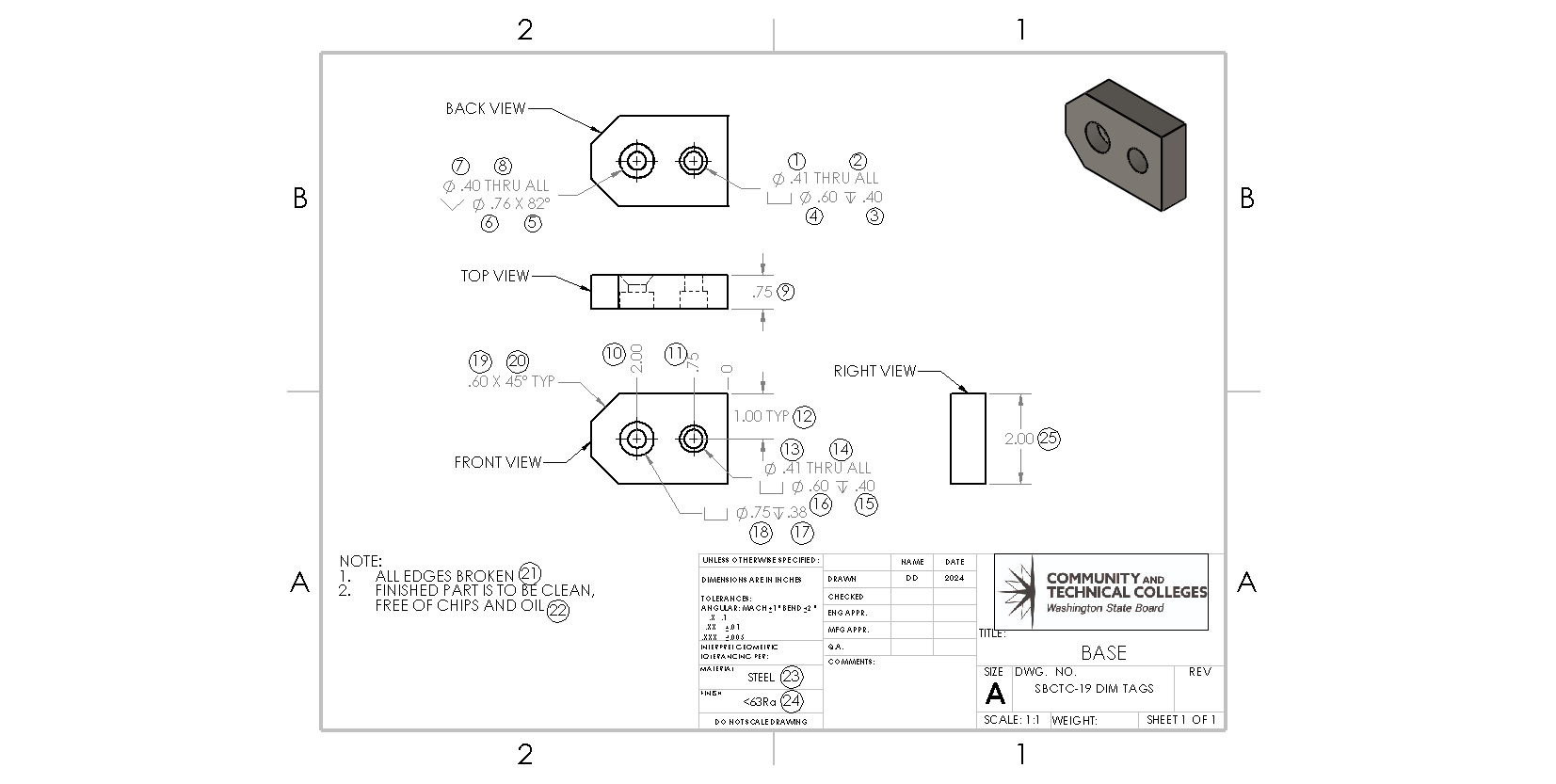
These tools help minimize material waste and enhance workflow efficiency by providing precise measurements and configurations.
Moreover, CAD software empowers engineers to design custom tooling and fixtures, boosting production accuracy and speed.
Applications of CAD Technology in Other Industries
How are CAD software tools used across the industry? We will explore the application of CAD tools in various industries and the potential benefits of the recent advances in 3D Deep Learning (AI).
Aerospace
Innovations in Aerospace product design rely on CAD technology deployed in engineering projects for accuracy and productivity.
Computer-Aided Design creates 3D models of components like wings, fuselages, and propulsion systems, addressing aerodynamics simulation, structural integrity, and weight distribution from concept to assembly. For spacecraft, CAD designs modules and docking mechanisms and facilitates simulations for trajectory planning and fuel optimization.
Material properties are modeled for safety, while Computer-Aided Design assists in the precise assembly and tooling design for lightweight composites in manufacturing. This integrated approach makes CAD tools essential in aerospace. Thus, Computer-Aided Design aids in the design of spacecraft components and modules, optimizing fuel consumption for missions.

Architecture and Construction
Computer-aided design enables architects and engineers to create detailed, accurate designs and simulations. Architects use CAD software to simulate structures, energy efficiency, and lighting conditions before construction begins.
Civil engineers use CAD tools to create representations of infrastructures on topographic and cadastral maps. Tools like BIM (Building Information Modeling) or platforms with GIS (Geographic Information Systems) integration often support this workflow, allowing, for instance, the fitting of a bridge geometric model to the terrain for accurate placement and design optimization.
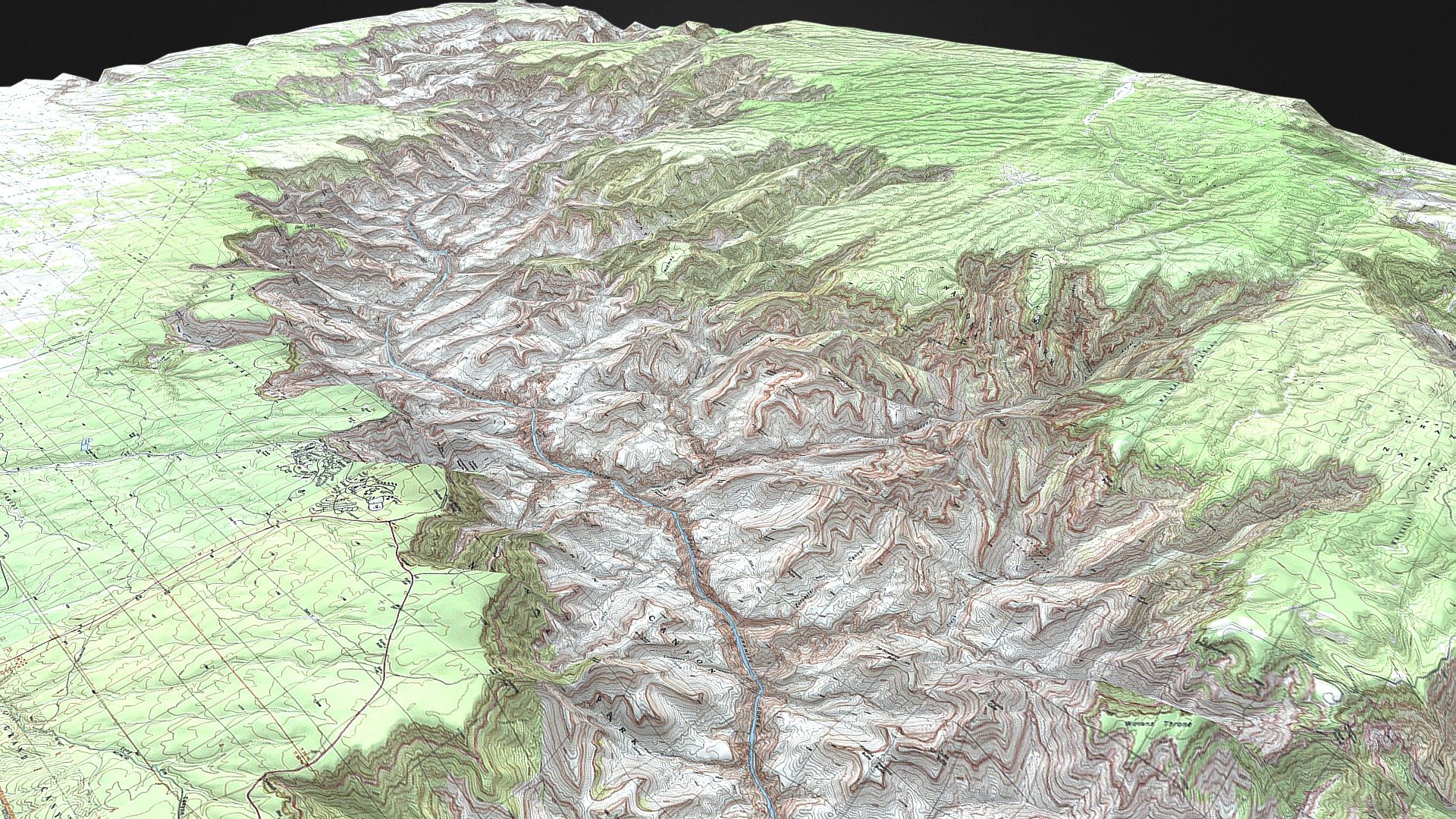
Benefits of CAD Technology
Computer-Aided Design helps the design process by offering designers precise tools for creating and optimizing models in various industries.
Below are its key benefits:
• Enhanced Productivity and Accuracy. CAD tools allow engineers and designers to create highly accurate models with minimal errors. Features like parametric design ensure consistency and reduce manual work, significantly improving productivity.
• Cost Savings in Prototyping and Manufacturing. Virtual prototypes created in CAD tools eliminate the need for multiple physical prototypes, saving material and labor costs. Simulation tools further reduce expenses by analyzing performance under real-world conditions before production begins.
• Collaboration and Innovation Opportunities. Cloud-based CAD software platforms and file-sharing capabilities enable seamless team collaboration, regardless of location. These tools allow multiple users to work simultaneously on a project, streamlining feedback and iterative improvements.
Common Challenges and Limitations
Imagine an SME (Small or Medium Enterprise) planning to set up a technical drawings office to support its technological innovations. What challenges could it face?
Learning Curve
CAD tools like SolidWorks or CATIA require significant training. Engineers and designers must invest time and effort in mastering features such as parametric modeling, assemblies, and simulations, which can slow initial productivity and increase training costs.
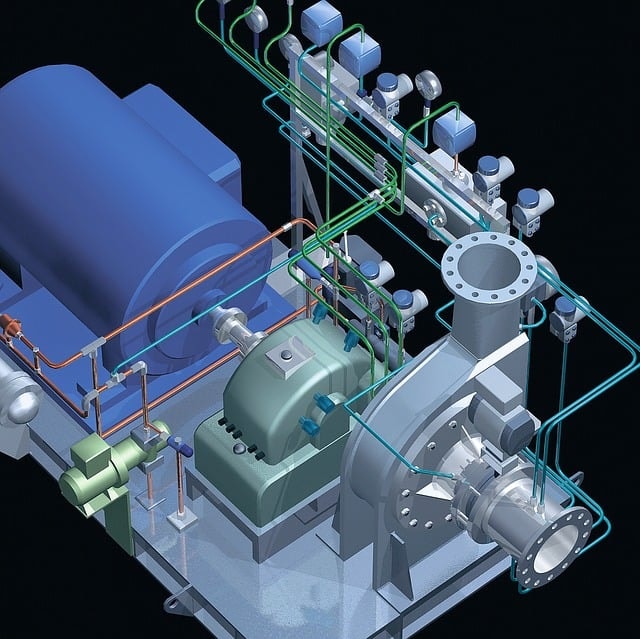
Initial Costs of CAD Tools
Professional-grade Computer-Aided Design software usually involves significant initial costs, such as licensing, hardware upgrades, and cloud subscriptions, making it challenging for SMEs to balance these with other expenses.
Interoperability Issues
Different CAD tools use proprietary file formats, which can lead to compatibility issues when exchanging designs across platforms. SMEs working with external partners may also need additional software or plugins to ensure seamless data sharing, which can increase costs and complexity.
What will the Future of CAD Technology be?
The integration of generative design, virtual reality, Computer-Aided Design technology, and data-driven prediction holds tremendous promise for the future of engineering.
Engineers will no longer have to abide by conventional constraints; they will use the following breakthroughs to push the boundaries of what is possible!
Integrated Simulation with Artificial Intelligence (AI)
Computer-Aided Design enables simulations like finite element analysis or fluid dynamics, helping designers identify issues early and reduce costly prototyping, for instance, in rotating machinery design.
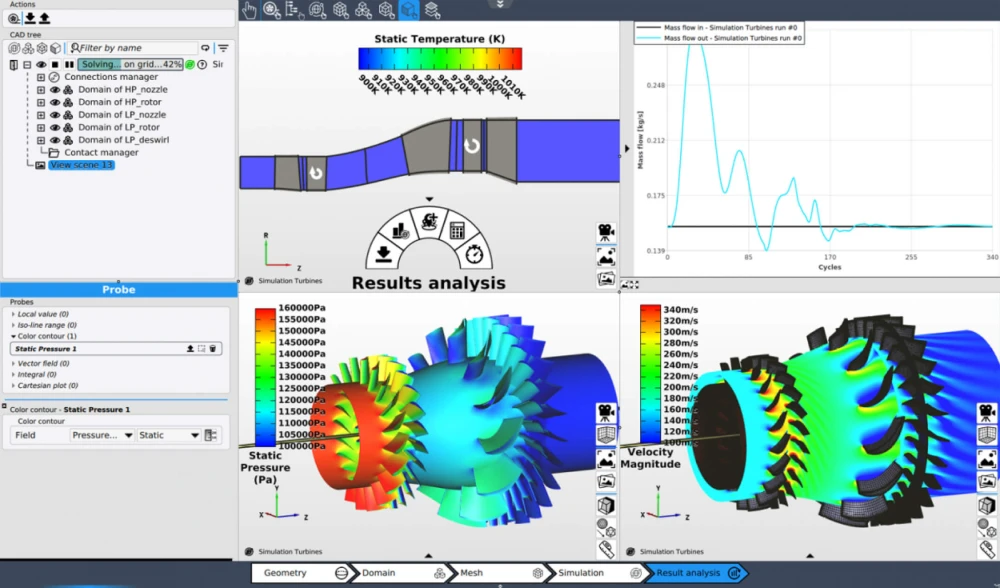
Could AI and machine learning enhance these capabilities by integrating high-fidelity computer-aided engineering into CAD software? Let us explore the scenarios of AI in mechanical engineering.
Imagine a CAD system that creates for product designers intricate 3D models using AI and ML to replace simulations with data-driven predictions from Convolutional Neural Networks, which simulate human vision. Techniques like deep learning can predict a CAD model's geometry and Computer-Aided Engineering attributes, such as fluidic or mechanical properties.
Artificial Intelligence-driven simulation revolutionizes design. Designers no longer have to wait for high-fidelity simulations. They can make rapid, data-driven predictions by themselves.
This allows CAD engineers to explore alternatives in the design space and create high-performance products. Thanks to innovative processes, they can reduce the time from concept to result.
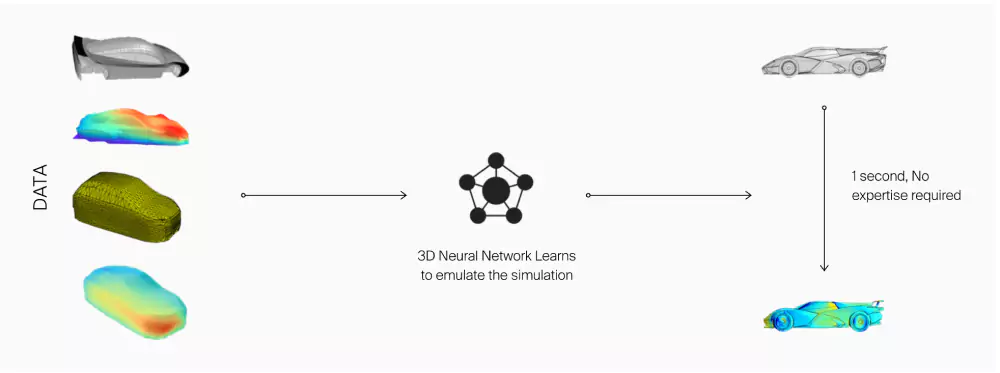
Machine learning techniques based on 3D CNN technology augment the impact of Computer-Aided Design technologies, predicting potential design flaws and optimizing designs based on geometric patterns.
The AI-driven predictive models enable designers to evaluate how design variations perform under specific conditions. AI-powered CAD simulation pushes innovation, allowing designers to test unconventional designs through predictive models. Complex tools often demand specialized knowledge. However, integrating AI models into CAD systems democratizes CAE, enhancing analysis accessibility for a broader range of designers. As shapes are modified, the AI system provides real-time feedback, aiding quick decision-making.
.png)
VR and AR Integration
Integrating VR and AR boosts design and stakeholder engagement. VR immerses designers in digital spaces to assess scale and spatial relationships. It's used in architecture, automotive design, and aerospace engineering. Architects visualize structures on-site, while technicians use AR for digital overlays in troubleshooting manuals.
Challenges in Computer-Aided Design Evolution
AI advancements will enhance Computer-Aided Design by delivering smarter design features and automating tasks, letting designers focus on innovation. Integrating VR and AR will facilitate real-time visualization and problem-solving pre-production. In conclusion, CAD's future is promising, with AI, VR, and AR transforming design across industries.
Signed Distance Fields: New Frontier
SDFs lead geometrical modeling and may shape future CAD tools as industries expand design limits. Signed Distance Fields (SDFs) define shapes using a mathematical function instead of traditional boundary representation (brep), which relies on surfaces, curves, and edges. The function indicates distances—positive outside, negative inside, and zero on the surface—enabling complex geometrical operations.
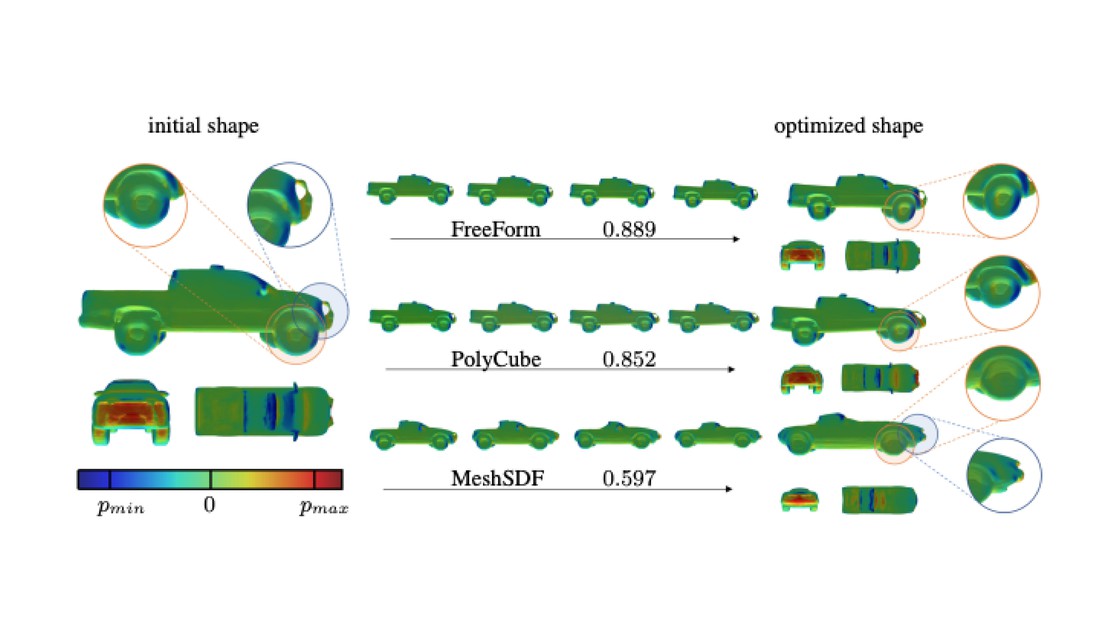
SDFs are gaining traction in niche tools like nTop for lattice structures and lightweight aerospace components despite challenges in mainstream software due to their lack of explicit topology, complicating integration. If adopted widely, SDFs could transform Computer-Aided Design by enabling seamless handling of large assemblies, real-time updates, and improved simulations.
Conclusions
Computer-Aided Design has evolved from simple drafting tools to a fundamental innovation element for product engineering. It empowers designers and engineers to create precise models, simulate real-world conditions, and optimize manufacturing processes.
The future of Computer-Aided Design integrates technologies such as artificial intelligence and virtual reality, facilitating predictive simulations, generative designs, and global collaboration across corporations. Machine learning assists engineers in predicting potential design flaws and optimizing designs based on historical data.
CAD's benefits in productivity, cost savings, and accuracy make it indispensable and will crucially influence the future of design and manufacturing.
FAQ
What are the 4 types of CAD?
There are many types! 2D creates two-dimensional layouts. 3D CAD builds three-dimensional models, divided into Solid Modeling for solid objects and Surface Modeling for complex shapes. EDA, or Electronic Design Automation, designs electronic systems like circuit boards and integrated circuits, using tools for circuit design, layout, and simulation.
What are CAD examples?
Examples of CAD software include AutoCAD (for 2D/3D drawing), SolidWorks (for 3D modeling), Revit (for building design), and CATIA (for complex engineering systems). Specific CAD software tools are designed for niche applications like PCB design and engineering tasks.
Where is CAD mostly used?
CAD software is frequently used in designing vehicles like cars, trucks, airplanes, or spacecraft.
How does CAD differ from traditional drafting?
Computer-Aided Design surpasses traditional methods by enabling easy revisions and faster production. It integrates with technologies like 3D printing and offers precise 2D/3D measurements and simulations. CAD software represents the objects of drafting using vector-based visuals or raster graphics.