The Multidimensional Benefits of Generative Design
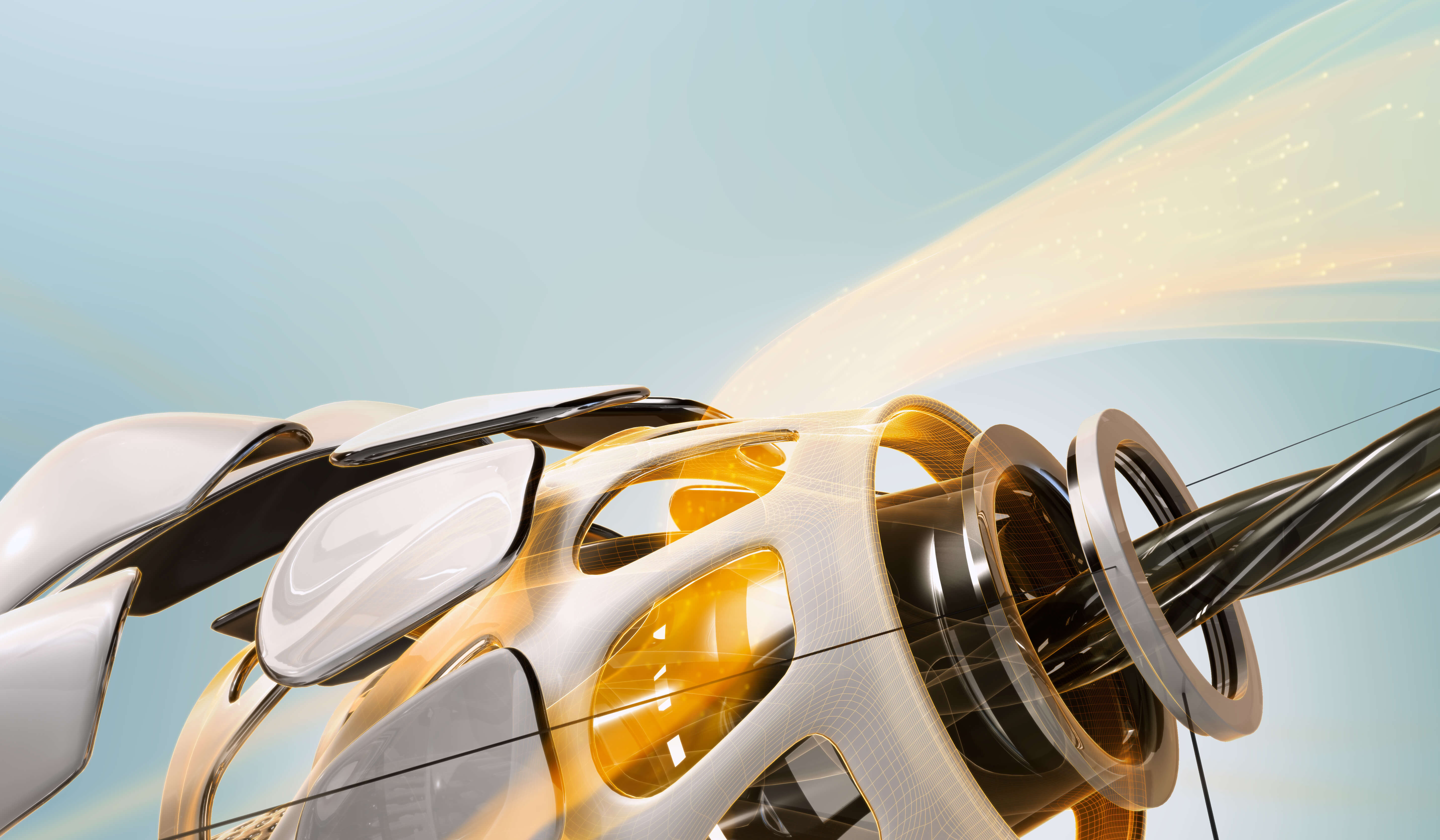
The engineering field is constantly pushing boundaries and making strides in various sectors, such as the automotive, aerospace, and construction industry.
Are you already familiar with generative design?
This innovative approach starts with counterintuitive design alternatives. It leads to state-of-the-art products that defy conventional design and manufacturing methods, thanks to facilitating technologies such as additive manufacturing or 3D printing.
This article will focus on the multidisciplinary integration of computer-aided design (CAD) and artificial intelligence (AI) within the generative design process. The next step in this integration is the deep learning approach to generative design. In deep learning, data are exploited to create real-time predictions. Here, human intervention is not replaced but is intellectually elevated at the level of a deeper understanding of processes. This contrasts with the traditional trial-and-error "slog" by the human designer sitting alone at her desk until late hours. Moreover, generative design is helping engineers in the design industry to integrate the design and manufacturing phases better and create more collaboration between company departments and, overall, a more inclusive working experience.
Benefits of Generative Design - Summary
This multidisciplinary integration offers impressive benefits to engineers and their organizations:
- Enhancing design opportunities with generative design working in a broader design space than with traditional methods, thus improving product performance;
- Reducing materials and costs while increasing performance thanks to manufacturable designs for lightweight structures;
- Optimizing designs continuously via innovative algorithm-driven design solutions is supported by data-driven predictions with AI.
All this ultimately achieves new product proposals that are cost-effective and time-saving.
What Is Generative Design?
Generative design is an innovative approach that utilizes algorithms (mainly artificial intelligence algorithms) to explore design possibilities and find optimal solutions based on specified design constraints and objectives. Next, you will see how to achieve benefits across various applications by leveraging the power of generative design and AI in engineering.
Initial Example of Generative Design Capabilities
Traditional solutions for design structures are created with manual design processes without generative design algorithms, i.e. relying on human expertise only.
Generatively designed products use computer algorithms to produce complex, intricate, optimized structures. The core of the process is leveraging algorithms to explore project design spaces larger than human intuition; simultaneously, algorithms do not only "explore and evaluate" but also optimize for various performance criteria, incorporating design goals and constraints, to create never seen before shapes.
Therefore, quite intriguingly, algorithmic shapes look "more creative" than human design. This apparent "mystery" is solved by clarifying the concept of broadened design space (see a later section in the article), which is more accessible when using fast algorithms stemming from AI.
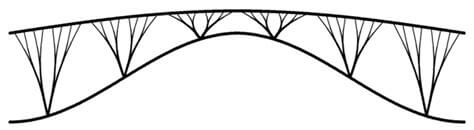
A practical example of an intricate structure created with generative design is the MX3D Bridge in Amsterdam. The MX3D Bridge is a pedestrian bridge designed with both generative design algorithms and 3D printing technology.
Generative design algorithms were employed to optimize the bridge's structure, considering material usage, weight distribution, and load-bearing capabilities. The algorithm generated a complex lattice structure with intricate patterns that are both visually appealing and highly functional.
In practice, the bridge was 3D printed using robotic arms that extruded molten metal, allowing for the precise fabrication of the intricate design.
The result is a unique, visually stunning bridge that showcases the potential of generative design in creating intricate and optimized structures with new manufacturing methods.
The Concept of Design Space
Before discussing the benefits of generative design, we will explore the concept of generative design capabilities in space, i.e. where design solutions are found by generative design algorithms based on constraints and objectives, thus considering product quality, performance and manufacturability.
Thus, the design industry lives (mathematically speaking!) in this space since it represents a multidimensional range of design variables and parameters within which engineers explore, evaluate, and optimize designs.
A design space refers to the range or set of allowable variations and parameters explored and optimized during a design process. It represents the design variables influencing a particular system or product's performance, characteristics, and constraints.
The design space encompasses all the possible combinations and values of parameters that can be adjusted or modified to achieve specific design goals and constraints (objectives) during the design process. These parameters include geometric dimensions, material properties, operating conditions, performance criteria, and constraints.
The concept of design space provides a framework for a systematic analysis, allowing engineers to decide about optimal shapes and achieve desired design goals while considering constraints and limitations.
The Cost of Exploring Design Spaces
We concluded the previous paragraph with an optimistic "to make decisions and achieve desired design goals while considering constraints and limitations". However, what is the practical cost of exploring weight constraints in a design space, and what are the available tools?
Design Space - Use Case
For example, in the design of an aircraft wing, the design space may include variables such as wing span, airfoil shape, sweep angle, and material composition. By varying these design parameters within certain limits, engineers can explore different wing configurations to maximize lift, minimize drag, improve fuel efficiency, and ensure structural integrity. The design space allows them to systematically analyze and compare the performance of various wing designs, ultimately leading to the selection of an optimal solution.
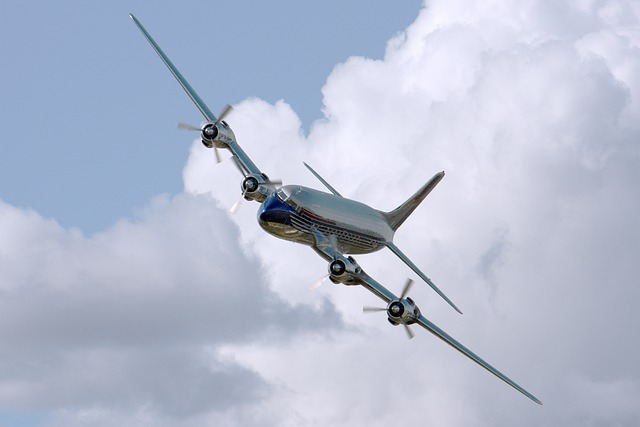
Design Space Exploration and Optimization
Exploring the design space involves systematically analyzing and evaluating different combinations of design variables to identify optimal solutions. This process often involves computer simulations, mathematical modeling, and statistical analysis. The concept of the design space is closely related to design optimization. By defining the boundaries of the design space, engineers identify the most promising regions that lead to desired outcomes.
Design Optimization Algorithms - Genetic Algorithms
Generative design tools employ optimization algorithms to iteratively explore the design space and identify the optimal design solutions among the various design options. These algorithms utilize mathematical methods to search for the design options that yield the best objective function values while satisfying the constraints.
An example is genetic algorithms inspired by natural selection and evolution.
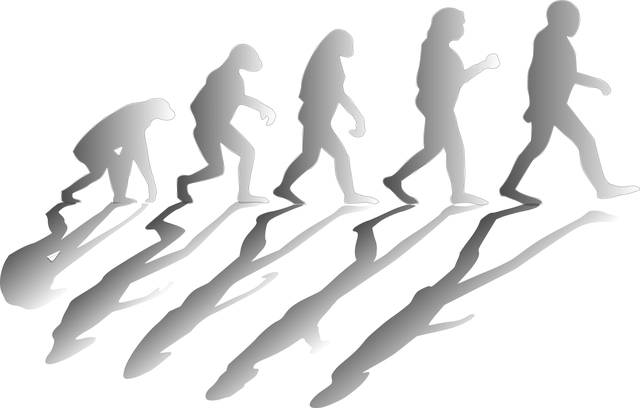
Genetic algorithms involve creating a population of design solutions, applying genetic operators such as mutation and crossover on design alternatives, and evaluating their fitness based on the objective function and constraints expressing the design goals.
Through successive generations and multiple iterations, the algorithm converges toward optimal solutions. These equations represent the underlying principles and steps involved in the optimization process of generative design.
CAD & CAE — Introduction to Computer Algorithms Supporting Design
We will now explore CAx tools, i.e. computer-aided design and computer-aided engineering, and their integration into generative design software.
Software Tool: The Role of CAD
CAD has completely revolutionized industrial design, providing designers with a powerful tool to experiment with multiple design options, conceive innovative designs, and refine them based on performance criteria and constraints. With the help of advanced computing power, CAD has transformed the design process, enabling designers to create intricate and optimized designs that adhere to manufacturing costs, weight limitations, and other specifications.
As additive manufacturing technology progresses, CAD will become increasingly vital in creating generative designs and facilitating virtual prototyping. The combination of human ingenuity and CAD software has ushered in a new design era, enabling designers to push the boundaries of innovation and produce exceptional products.
Traditionally, the design process relied on the expertise of human designers. While human designers play a crucial role in the creative aspect of design, CAD complements their skills by providing a platform that enhances their abilities and expands their design options. By utilizing CAD software, designers can explore various design alternatives, iterate quickly, and evaluate the impact of different design parameters on the final product.
One of the benefits of CAD is its ability to handle complex designs that would be challenging or time-consuming to create manually. CAD software simplifies the design process by automating repetitive tasks and providing intuitive tools for manipulating and visualizing 3D models. This automation streamlines the design method, allowing designers to focus on the creative aspects and refine their ideas.
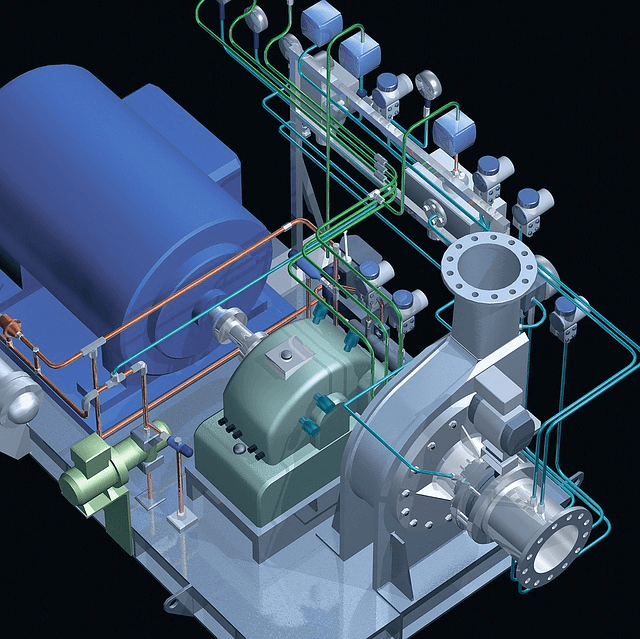
To create visually appealing but also cost-effective, functional, and efficient designs, virtually 100% of today's designers utilize CAD software.
The emergence of 3D printing is providing new opportunities for CAD designers. With additive manufacturing technologies like 3D printing, designers can transform their digital designs into physical prototypes or end-use products.
CAD also facilitates collaboration among different design professionals. With cloud-based CAD platforms, designers can work on the same project, share and review designs, and provide real-time feedback. This approach enhances communication and teamwork, leading to better design outcomes. Therefore, utilizing CAD software is crucial for achieving optimal results.
CAD Parametric Modeling
Parametric modeling in CAD uses parameters to create and adjust 3D models. However, learning and limiting creative freedom as predefined parameters and constraints control designs can be challenging. Also, it provides a severe limitation to the design alternatives, as we will see in the concluding chapter comparing the parametrically generated shape in Figure 6 to a generatively designed alternative.
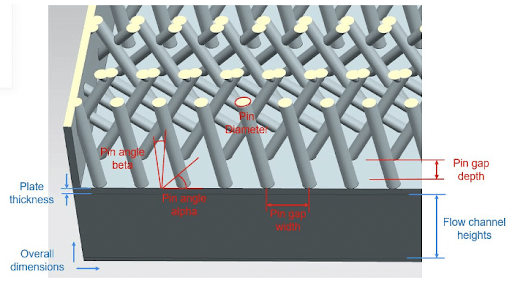
Software Tool: CAE Software and Cloud Computing
The engineering and design industries have undergone significant changes thanks to the introduction of Computer-Aided Engineering (CAE). With a wide range of simulation and analysis tools, engineers can assess and analyze designs virtually before creating physical prototypes. This process is essential in improving product performance, reducing costs, and speeding up product design and development time. CAE comes in different types, each catering to specific engineering domains. The three most notable types of CAE are Computational Fluid Dynamics (CFD), Finite Element Analysis (FEA), and Electromagnetic Analysis.
Introduction to CAE (Computer-Aided Engineering)
Computer-Aided Engineering (CAE) is a powerful technology that has revolutionized the engineering and design fields. It encompasses a range of simulation and analysis tools that allow engineers to test and evaluate designs before physical prototypes are built virtually. CAE is critical in optimizing products, reducing costs, and accelerating product development. Various types of CAE are available, each tailored to specific engineering domain: prominent types are Computational Fluid Dynamics (CFD), Finite Element Analysis (FEA), and Electromagnetic Analysis.
CFD focuses on analyzing fluid flow, heat transfer, and related phenomena. It employs numerical methods to solve complex equations that govern turbulent fluid behaviour in complex domains like the turbine blade shown in figure below.
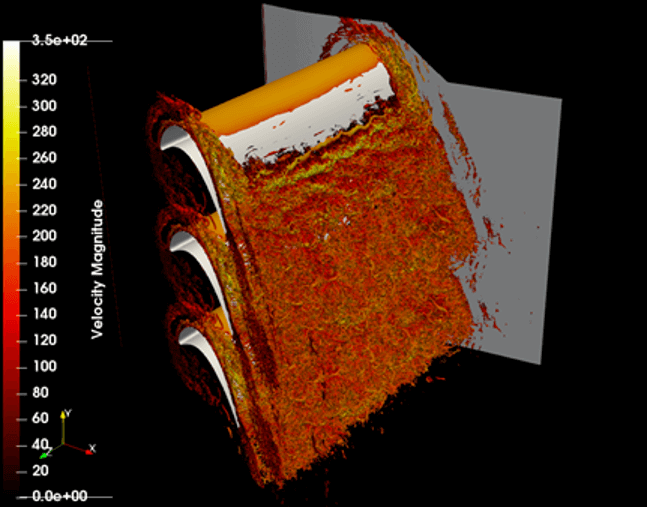
FEA specializes in analyzing structural behaviour and mechanical systems. It can simulate the response of materials and structures to applied loads, allowing engineers to evaluate stress, deformation, and vibration characteristics. FEA simulations enable engineers to assess design alternatives and improve product durability and performance.
Parametric design, combined with the capabilities of cloud computing, offers a range of benefits and opportunities for designers and engineers. By leveraging the power of the cloud, designers can enhance their design process, collaborate seamlessly, and access advanced computational resources. Cloud-based platforms enable collaboration among designers, engineers, and stakeholders, regardless of their geographical location. Parametric design files can be stored, shared, and accessed in real time.
Design Spaces and Benefits of Generative Design
Let us review the main benefits of generative design.
Design Opportunities
The generative design approach opens up new possibilities by exploring unconventional shapes, intricate geometries, and optimized structures.
Engineers can now push the boundaries of what was previously considered feasible, leading to breakthrough innovations in areas such as automotive design, aerospace components, and consumer products.
Flexibility
With generative design, engineers can define design goals, allowing them to incorporate specific requirements and optimize designs accordingly
In heat exchangers, generative design can optimize the configuration and geometry of fins, tubes, and fluid passages to enhance heat transfer efficiency. Engineers can develop heat exchanger designs that maximize thermal performance while minimizing energy consumption.
Improved Performance
Generative design offers a multitude of benefits, with performance improvement being a notable advantage, especially in the realm of manufacturing. By harnessing the potential of advanced algorithms and computational power, generative design revolutionizes the traditional design process by generating numerous design iterations and identifying optimal solutions that enhance performance.
Manufacturing constraints, such as material properties, weight limitations, and production capabilities, are considered during the generative design process.
Through iterative analysis and optimization, generative design algorithms can produce complex, innovative designs that outperform traditional ones.
These optimal designs leverage the capabilities of manufacturing processes to generate designs that maximize efficiency, durability, and functionality. By fine-tuning designs based on manufacturing requirements, generative design helps achieve superior performance.
Additionally, generative design allows for exploring unconventional and breakthrough design solutions that may not have been conceived by human designers alone. By pushing the boundaries of what is physically possible, generative design opens up new opportunities for lightweight, structurally efficient, and aesthetically pleasing products.
In summary, generative design's emphasis on optimizing performance through consideration of manufacturing constraints leads to groundbreaking designs that maximize the potential of manufacturing processes. By leveraging computational power and innovative algorithms, generative design has the potential to transform the manufacturing industry and drive innovation to new levels.
Reducing Materials
Generative design's ability to minimize material usage through intelligent algorithms and iterative optimization processes has tangible environmental benefits across various industries, promoting sustainability and resource efficiency.
- Aerospace Industry. One practical example is the aerospace industry, where generative design has been used to create lightweight and structurally efficient components. By iteratively analyzing load conditions and properties of materials, generative design algorithms can generate intricate and organic geometries that minimize weight without compromising strength. This reduction in material usage translates to significant fuel savings during flight and reduces environmental impact.
- Automotive Industry. In the automotive industry, generative design has been employed to create lighter vehicle components without sacrificing safety. By optimizing the design of parts such as brackets, supports, and chassis components, generative design can significantly reduce the overall weight of vehicles. This, in turn, improves fuel efficiency and reduces emissions, contributing to a more sustainable transportation sector.
Cost-Effective Design with Time Savings
The generative design software approach offers the benefit of cost-effective design with time savings. Generative design software can identify efficient solutions that reduce material waste, manufacturing costs, and production time. This streamlining of the design process leads to significant cost savings and accelerated product development timelines. The key is automating the design process and exploring virtually countless design iterations. The process becomes even more convenient by introducing Deep Learning as a surrogate of slower traditional CAE simulation.
What Is Topology Optimization?
Topology optimization and generative design are similar concepts within engineering and product design. Both terms refer to iterative processes that utilize computational algorithms to generate optimized designs based on specified constraints and objectives. Although the terms are sometimes used interchangeably, Topology Optimization is a specific technique employed within Generative Design methodologies.
Topology Optimization, as a subset of Generative Design, focuses on determining the optimal distribution of material within a given design space to achieve desired performance criteria. Topology Optimization aims to create designs that maximize structural efficiency while meeting weight, stress, or stiffness constraints by iteratively removing or redistributing unnecessary material.
In Topology Optimization, the design domain is divided into finite elements and mathematical algorithms are employed to determine the optimal arrangement of these elements. The algorithms analyze the structural behaviour and design performance, iteratively refining the shape by removing or adding material to achieve the desired outcome.
On the other hand, generative design encompasses a broader approach beyond structural optimization and can incorporate manufacturing constraints, aesthetic considerations, and user preferences.
Overview of Generative Design Software
The core idea behind generative design software is to provide a way for designers to input design goals and constraints and let algorithms generate and evaluate numerous design variations, often using advanced optimization algorithms. Generative design software can rapidly iterate through different designs by leveraging computational power and AI techniques, simultaneously considering multiple parameters and constraints.
Here are a few examples of popular generative design software. Their generative design capabilities include topology optimization algorithms to generate lightweight and structurally efficient designs automatically.
The software allows designers to define constraints and goals and automatically generate optimized design alternatives based on these inputs. Generative design software engines can optimize weight reduction, structural performance, and material usage, leading to innovative and efficient designs.
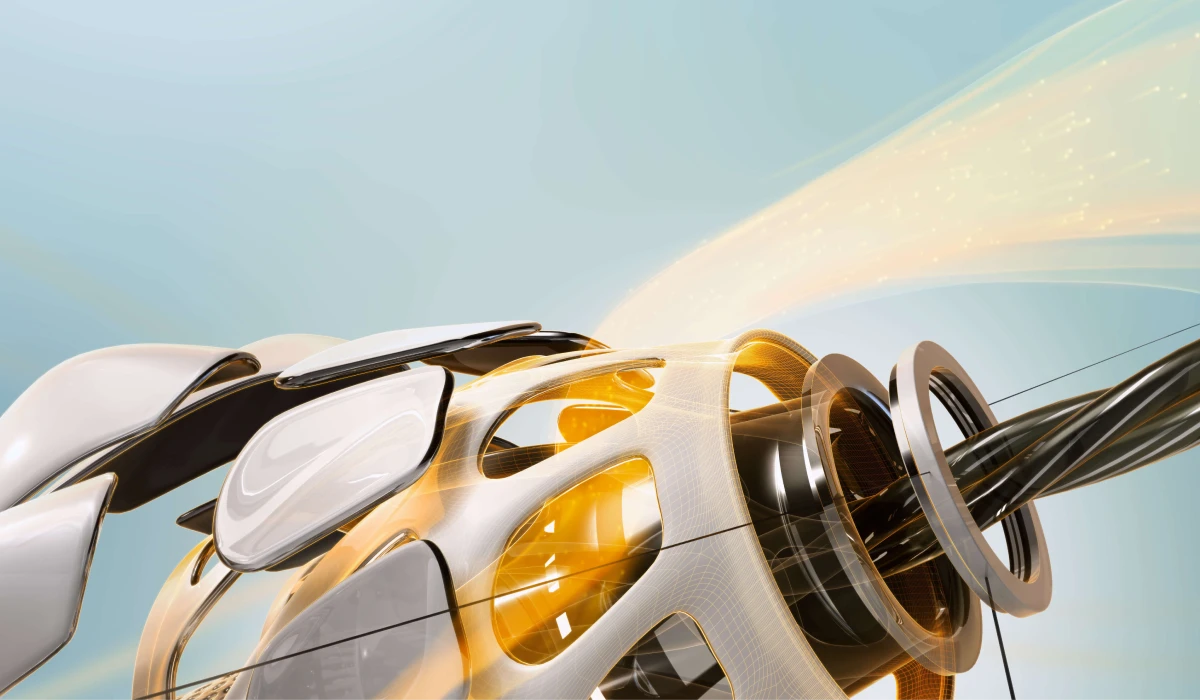
For instance, Dassault Systèmes offers generative design software capabilities to explore alternatives for complex and organic shapes suitable for additive manufacturing processes and 3D printing. CATIA helps product designers generate optimal designs that are lightweight, strong, and tailored for specific manufacturing techniques.
As another example, ANSYS Discovery Live is a CAE-flavored design software. This software tool enables engineers to interactively explore design alternatives and immediately visualize the impact of different design options on performance.
AI Algorithms and Machine Learning for Generative Design
Integrating AI algorithms and machine learning techniques into generative design software has significantly advanced the field. By leveraging these technologies, designers and engineers can explore new design options, optimize performance, and improve the overall efficiency of the product design process. The application of AI and machine learning in generative design software holds tremendous potential across various industries, allowing for the creation of innovative, sustainable, and optimized products.
AI Algorithms and Machine Learning: Introduction
Artificial Intelligence (AI) algorithms and machine learning (ML) techniques have revolutionized the field of generative design. By harnessing AI algorithms and machine learning, generative design tools can automate the design process, explore countless design iterations, and identify optimal design options.
Artificial Intelligence and Machine Learning as Generative Design Tools
In generative design, AI algorithms and ML play a crucial role in analyzing and understanding constraints, objectives, and historical data. These algorithms can learn from existing designs, materials, manufacturing processes, and performance criteria, generating novel and efficient design solutions. By continuously learning and adapting, these generative design tools improve over time, becoming more proficient at creating optimal designs.
ML and Generative Design Use Case
A notable use case for ML in generative design is in the automotive industry. ML algorithms can analyze large datasets of vehicle performance data, properties of materials, and manufacturing constraints to create, with generative design, components such as heat exchangers. Deep learning-driven generative design automates the process of finding an optimal shape. Human intervention operates at the level of a deeper understanding of the optimization processes rather than following traditional trial-and-error methods.

The closing Figure 11 in this article represents a complex heat exchanger shape that we invite you to compare with the "rigid" parametric initial geometrical shape of Figure 6. The initial parametric modelling would not be able to generate designs such as the one illustrated; in contrast, the "weird" shape of Figure 11 can be rapidly deployed in the manufacturing process as far as the practical manufacturing processes (such as 3D printing) is considered in combination to the design process. Thus, the shape is weird but not an unfeasible fancy shape.
At the end of this article, you can now appreciate how generative design represents a true trailblazer for innovative design alternatives in the automotive and many other industries.