Battery Pack Design: Maximizing Performance and Efficiency
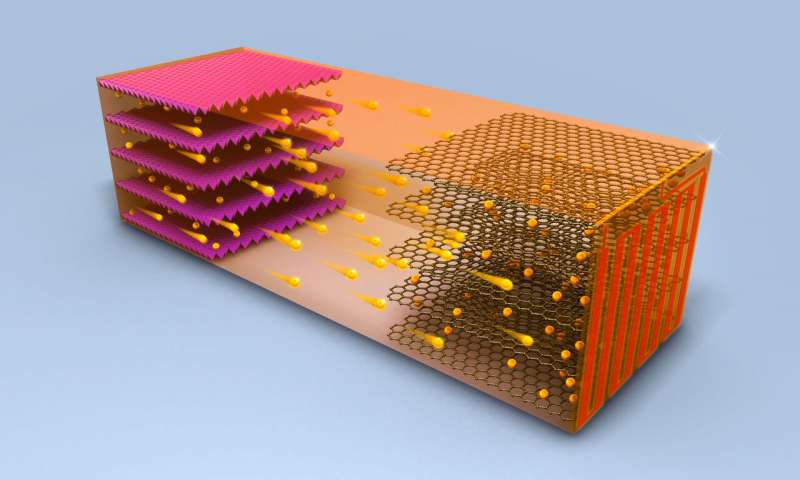
The concept of a battery pack is likely familiar and critical if you own an electric vehicle or an energy storage system. Such a pack stores energy to power these systems and comprises interconnected cells that produce energy.
This article will explore the EV generative design challenges of designing a battery pack. After providing an overview, we will explore a crucial pack design tool: engineering simulation (CAE).
Thanks to recent advancements in CAE technology that merge design and R&D data into Deep Learning (AI), engineers who design battery packs can now envisage using cost-effective AI-based tools to optimize thermal management systems and crashworthiness to protect and extend the battery pack's life.
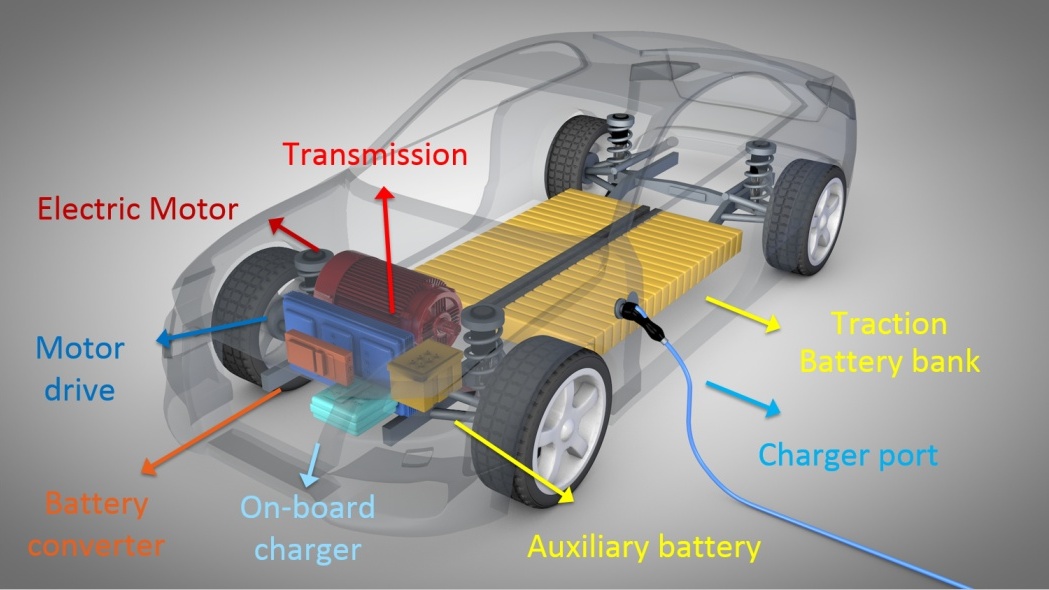
How to Increase Battery Power and Capacity
Two basic high-performance concepts are related to series and parallel arrangements.
What Is Battery Power?
This concept refers to the rate at which a battery supplies or consumes energy.
Power is typically measured in watts (W) or kilowatts (kW). High-power batteries can discharge quickly, making them suitable for applications that require bursts of energy, such as starting an electric vehicle or providing short-term high performance in electronic devices.
What Is Battery Capacity?
This concept represents the total amount of electrical energy a battery can store.
It is measured in ampere-hours (Ah) or milliampere-hours (mAh) and indicates how much energy a battery can provide over an extended period. Higher-capacity batteries can store more energy and provide power for a longer period before recharging. Battery cells can be arranged to increase voltage or capacity.
Series Connection
Series connections are commonly used in electric vehicles (EVs) and other applications requiring higher voltage levels. When battery cells are connected in series, the positive terminal of one cell is connected to the negative terminal of the next-generation cell, effectively adding up their voltages; the series-connected cells can be expressed as:
V = V₁ + V₂ + … + Vₙ (Voltage)
where V₁, V₂, …, Vₙ are the individual cell voltages.
Therefore, when cells are connected in series, the power remains relatively constant, and the voltage increases, enabling the battery to deliver a higher output.
Parallel Connection
Parallel connections are commonly used in applications where extended runtime is essential, such as energy storage and backup power supplies.
In this case, the positive and negative terminals are connected, respectively. In this configuration, the voltage now remains the same as that of a single cell, while the capacity is additive so that parallel connections increase the overall capacity of the battery pack:
C = C₁ + C₂ + … + Cₙ (Capacity)
while
V = V₁ = V₂ = … = Vₙ (Voltage)
When cells are connected in parallel, the output remains relatively constant because the voltage doesn't change. However, the capacity increases, allowing the battery to provide energy for a longer time.
Different Battery Chemistries
Lithium-ion and lead-acid batteries represent two distinct worlds of energy storage.
Lithium-ion (Li-Ion) batteries are lightweight and compact, have high energy density, and power our modern devices effortlessly.
Lead acid batteries have, in contrast, a heavy form and supply reliable energy to cars and backup systems.
As with EV batteries, acid lead batteries are much heavier and bulkier than lithium-ion batteries. Electric Vehicles require lightweight and compact energy storage solutions to maximize their range and overall efficiency; therefore, Li-Ion is the choice.
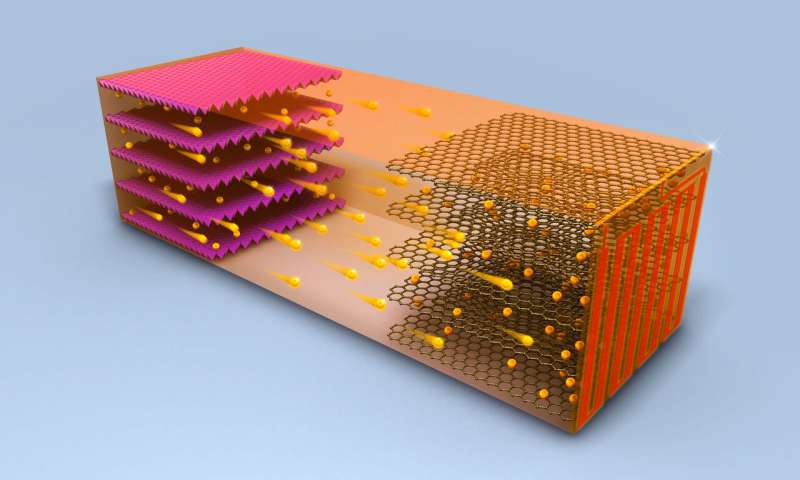
Hybrid Battery Packs
Hybrid battery packs combine different types of batteries used in certain hybrid vehicles, particularly hybrid electric vehicles and some plug-in hybrid electric vehicles. These hybrid battery systems are designed to maximize each battery's benefits while mitigating their limitations. The most common configuration in hybrid battery packs includes a combination of Li-Ion batteries and Nickel-Metal Hydride batteries.
Sub-Packs or Battery Modules
Battery packs comprise smaller sections called battery modules (or sub-packs). These modules have fewer cells, which makes them safe to handle. Replacing a few cells in the battery modules is easy without replacing the entire main battery.
Thus, battery modules facilitate enhanced safety, modularity, and serviceability of full-sized batteries and improved thermal management and overall battery performance. Manufacturers can deliver safer, more reliable, and easier-to-maintain energy storage solutions by dividing the battery pack into smaller, manageable sub-packs.
Battery Pack Components
The electric vehicle (EV) battery pack is a crucial component that stores and supplies energy to the vehicle's electric motor.
The combination and design of battery pack components may vary depending on the specific electric vehicle model and manufacturer. Battery technology is continuously evolving, and newer developments may lead to future changes in the composition and structure of electric vehicle battery packs.
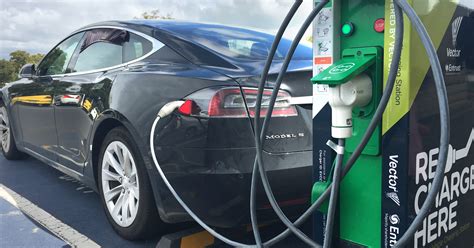
Battery packs can vary depending on the EV model and manufacturer, but they generally consist of the following eight key battery components:
Battery Cells
Individual battery cells are the basic building blocks of the battery pack. These cells are usually cylindrical (e.g., Li-Ion 18650 cells) or prismatic in shape and contain a positive electrode (cathode), a negative electrode (anode), and an electrolyte.
Battery Management System (BMS)
The BMS is essential to an EV battery pack as it monitors and manages individual cells. Its main functions include balancing cell voltages, monitoring temperature, controlling charge and discharge rates, and ensuring the longevity of the entire battery itself. The BMS' communications system communicates with the vehicle's onboard computer to provide real-time status updates.
Battery Cooling System
EV battery packs generate heat during the charging and discharging processes. A designed battery cooling system is integrated into the pack to maintain optimal operating temperatures and prevent overheating. The NC blog details how Deep Learning can produce heat exchange design software, guiding users to exploit available space for a demanding packaging case, such as the heat exchanger design software task (less room is always desirable). Typically, this involves liquid or air cooling methods to dissipate heat efficiently and maintain performance.
Enclosure
The pack is enclosed in a battery pack protective housing that shields the cells and the BMS from external influences such as water, dust, and physical damage. The enclosure is designed to ensure durability within the available space.
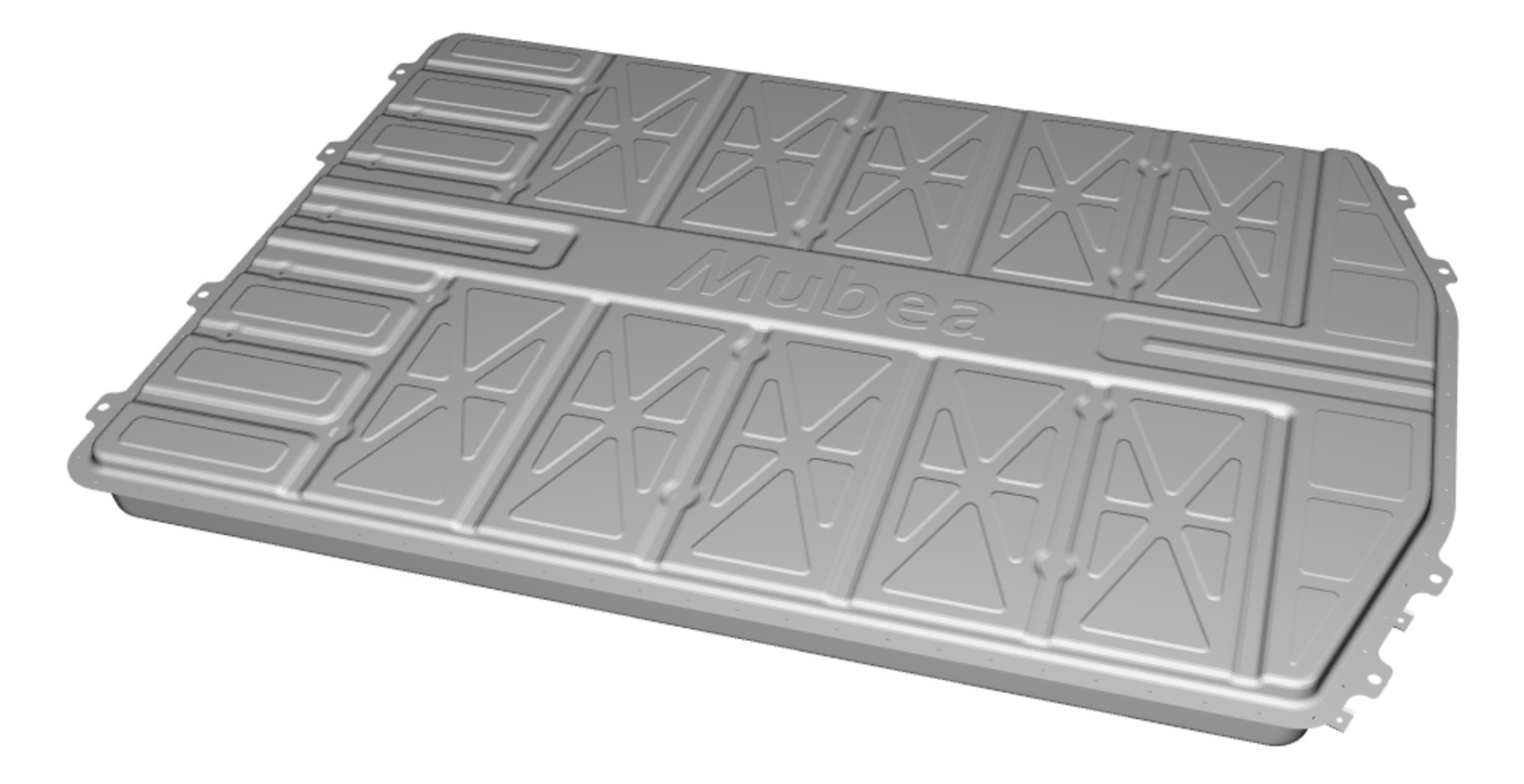
Connectors and Wiring
High-quality electrical connectors and wiring interconnect the battery cells and integrate them into the vehicle's powertrain system. These components must handle high currents and ensure minimal losses.
Thermal Management System
In addition to the cooling system mentioned earlier, a thermal management system may include additional elements of high-performance battery packs like thermal insulation, heat sinks, and temperature sensors.
It helps regulate the pack's temperature and ensures it operates within the optimal range.
Voltage Regulator
EV battery packs deliver high-voltage DC power, which needs to be regulated to match the voltage requirements of the vehicle's electric motor and auxiliary systems. A voltage regulator or DC-DC converter ensures the battery voltage power output is stable and compatible with the rest of the EV's electrical system.
High Voltage Connector
The battery pack needs to be connected to the electric motor and other high-voltage components of the EV. A high-voltage connector provides a secure and reliable connection between vital components, allowing power to flow to the vehicle powertrain.
The Battery Pack Design Process
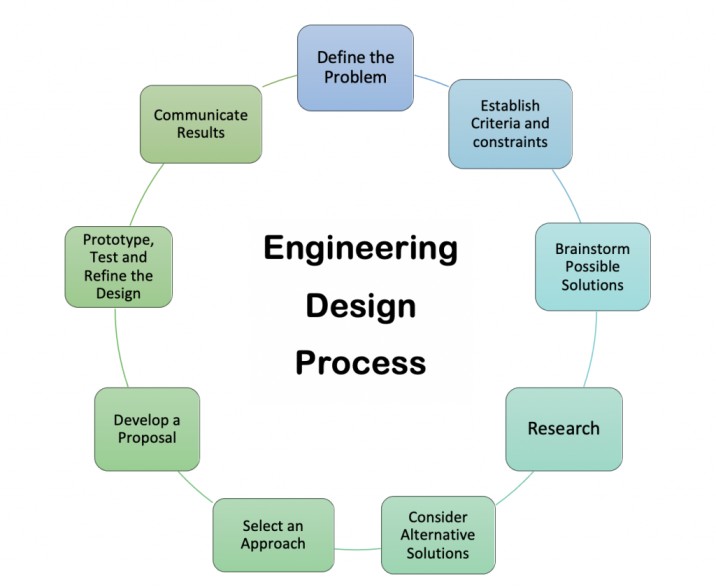
Designing a battery pack involves several key steps to ensure optimal performance. Here's a simple step-by-step guide for battery pack designers that could be useful for most battery packs without claims to be a technical manual:
Define the Battery Pack Requirements: The battery pack designer starts by understanding the intended use and related requirements, including voltage, capacity, size, and weight constraints.
Select the Battery Chemistry: The designer chooses the appropriate battery chemistry based on the application's needs, considering energy density, cycle life, and operating temperature range.
Determine the Number of Cells: The battery pack designer calculates the number of cells needed to achieve the desired voltage and capacity. This depends on the chosen chemistry and configuration.
Evaluate Combinations: Designers explore different battery pack combinations to find the most suitable arrangement that meets the performance requirements while optimizing space and weight.
Design Battery Pack: Engineers develop the physical layout and structure of the battery pack, considering factors such as cell arrangement, interconnects, and thermal management.
Integrate Protection Circuitry: Designers Include a protection circuit board (PCB) to monitor and manage the battery pack's performance, providing overcharge protection, over-discharge protection, and thermal protection.
Optimize Performance: Here, engineers fine-tune the design to maximize the battery pack's performance, balancing factors like energy efficiency, power output, and overall reliability.
Validate: Engineers from the experimental test laboratory conduct testing to ensure the reliability of the battery design under various operating conditions, including temperature extremes and mechanical stress.
Iterate and Refine: Designers iterate the design as needed based on testing results and feedback, making refinements to improve performance or efficiency.
Consider Cell Diameter: Designers evaluate the cell diameter and form factor to determine the best fit for the pack design, considering factors such as space constraints and energy density.
Explore Multi-Row Cells: The possibility of using multi-row cells to optimize space utilization and increase the energy capacity of the battery pack is investigated in this phase.
Document and Certify: The team thoroughly documents the battery pack designs and specifications, ensuring that the chosen battery pack combinations and the number of cells meet the requirements. Obtain necessary certifications to comply with industry standards and regulations.
Manufacture: The battery pack will be manufactured using approved materials and processes once the design is finalized and certified.
Quality Control: Engineers implement rigorous quality control measures during manufacturing to maintain consistency and reliability across all produced battery packs.
Cells Used in Battery Packs
Cylindrical cells are one of the most commonly used types of cells in battery packs. They have a tubular shape and are often referred to by their size designation. These cells are known for their robustness, high energy density, and good thermal performance. They are widely used in various industries, including electric vehicles or laptops.
Prismatic cells have a flat, rectangular shape, making them space-efficient and suitable for compact battery pack designs.
They come in different sizes and can be tailored to fit specific vehicle platforms, allowing for more flexibility in battery pack configurations. Prismatic cells are often chosen for their ease of integration, improved thermal conductivity, and potential cost savings in manufacturing.
Advanced Simulation Solutions for Battery Safety and Longevity
Battery design demands consideration for safety and durability. Advanced simulation solutions such as CAE enable engineers to optimize battery housing designs and reinforcements, identifying potential weaknesses and vulnerabilities and creating a battery pack capable of withstanding mechanical stress, vibrations, and impacts.
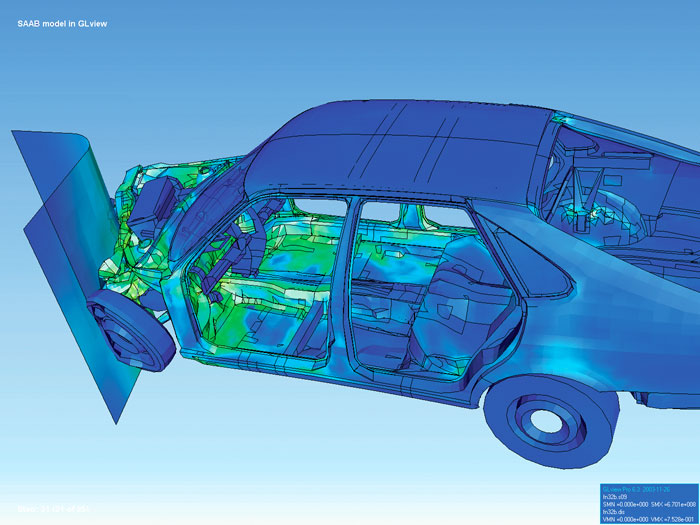
Simulations also evaluate thermal behavior. By simulating different thermal scenarios, efficient cooling systems based on software to calculate heat dissipation ensure that the system operates within a safe temperature range.
Durability is also crucial. Simulations allow engineers to predict cell degradation and identify possible failure points.
Deep Learning for Battery Pack Design
The exciting topic of Deep Learning prediction has already been extensively discussed elsewhere. The image compares CAE with Deep Learning's predictive function that can be extended to all EV components.
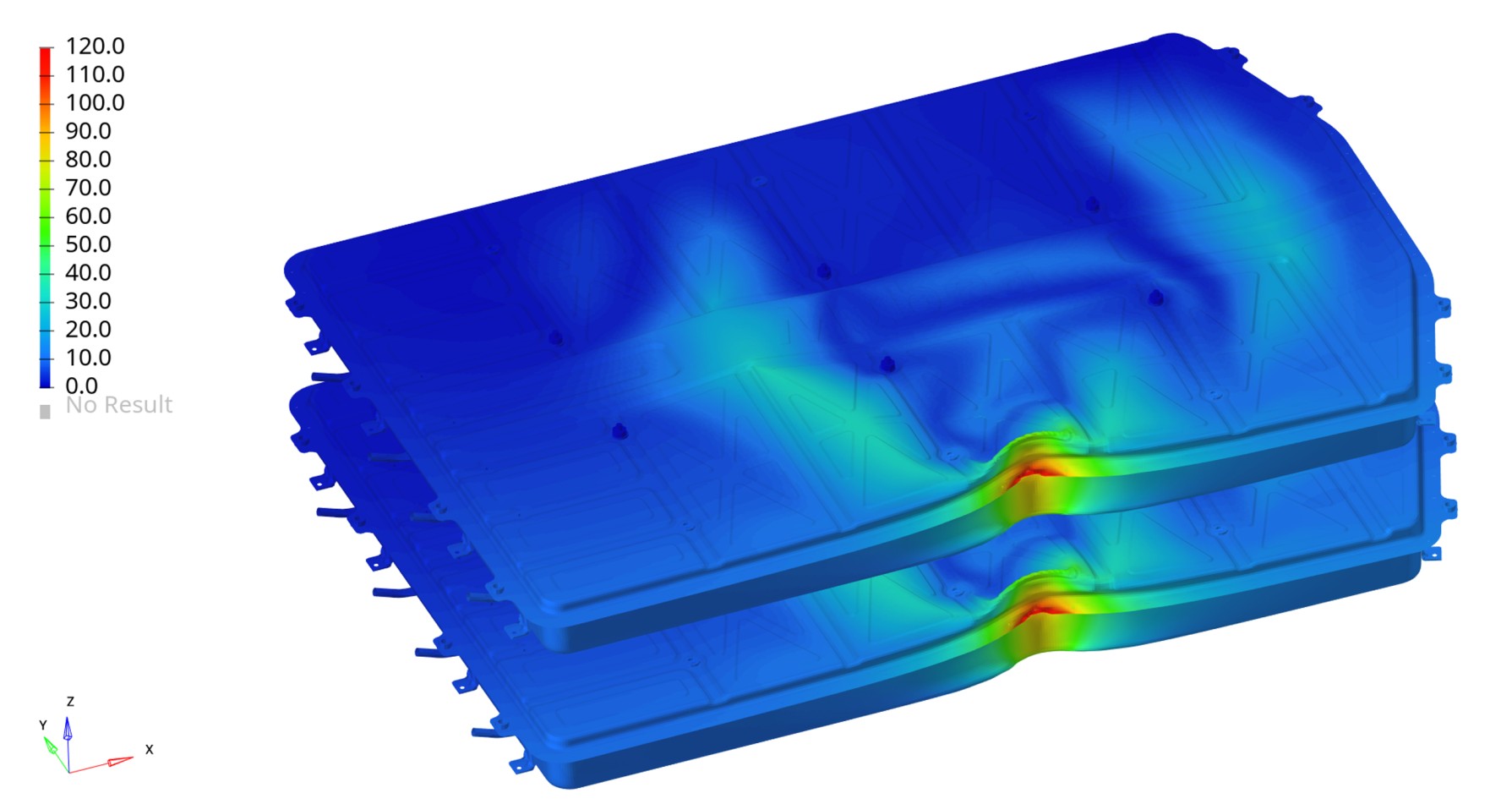
The process described, for example, where a designer without specific crash simulation skills can obtain displacement and maximum force, is a game-changer compared to the usual lengthy lead time of hours between design conception and CAE verification.
Even more groundbreaking innovations, such as algorithms driving design changes, will be deployed soon!