What Is Simulation-Driven Design? Main Benefits Explained
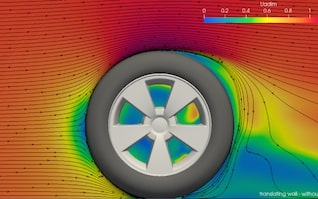
In engineering, innovation and efficiency are crucial to stay ahead in the competitive landscape. How do we design better and faster? Engineers need tools and methodologies that enhance their product development processes, besides their irreplaceable "grey matter" that AI can assist but not replace.
A product design methodology attracting a lot of attention and investments in recent years, especially in large automotive and aerospace corporations, is simulation-driven design.
This article explores what simulation-driven design is and the main benefits it offers to engineers who are at the forefront of designing and optimizing products and processes for their organizations.
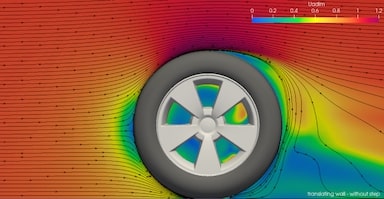
What Is Simulation-Driven Design?
Simulation-driven design is an engineering approach that leverages advanced (3D) virtual technology to drive the design and development process by getting, for a product or assembly, qualitative answers (such as a 3D color map showing pressure distribution) and quantitative details (such as the point-by-point values, extractions of averages or min/max values) before the physical product is built.
The approach integrates traditional CAE simulation tools, artificial intelligence predictions, system modeling, and process simulation into product development, helping engineers bring their concepts to life and respond to customers and constraints.
Design Space Exploration and Optimization — The Role of Simulation.
Simulation-driven design can offer numerous advantages. We will explore the process of first comparing two designs, then sweeping across several designs by changing a design variable, and finally moving into a multidimensional design space.
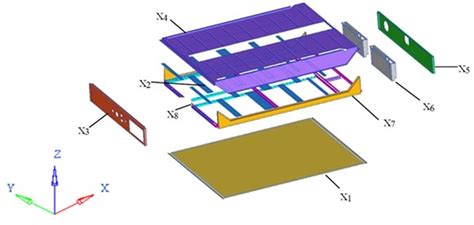
Comparing Solutions
One of the key advantages of simulation-driven design is its ability to compare different design solutions effectively. Imagine you have two potential solutions, "A" and "B" and you need to determine which one best aligns with your project's goals.
This process typically involves evaluating predefined KPIs, such as noise levels, peak forces, aerodynamic performance, and thermal efficiency. These metrics are often beyond the reach of mere intuition and demand concrete data acquired through experimental testing or Computer-Aided Engineering (CAE) analysis.
Changing a Design Variable
Another compelling aspect of simulation-driven design is the ability to go through various design iterations efficiently. By varying a specific parameter, like the thickness of a component, and integrating this approach with Computer-Aided Design (CAD), one can smoothly navigate a 1-dimensional design space. As the number of manipulated parameters grows, the design space transforms into a multidimensional realm.
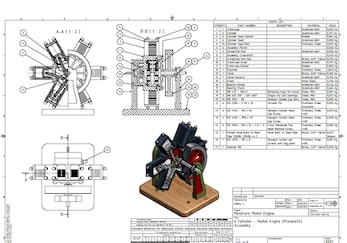
Changing Multiple Design Variables
However, it's vital to acknowledge that not all corners of this multi-dimensional design space are readily explorable. Constraints related to geometry, cost, or materials can impose limitations.
Additionally, the human element introduces the potential for bias, where one parameter might be favored over another.
Introducing Optimization Algorithms
Optimization algorithms are like "intelligent" problem solvers for designing things.
Imagine you have many factors to consider when creating a product like a vehicle. You want it to be fast, safe, and fuel-efficient. However, humans might have biases, like focusing too much on speed and not enough on safety.
This is where optimization algorithms step in. They act as impartial decision-makers, exploring countless combinations of these factors to find the best possible design. Think of them as helpful assistants trying different car designs in a simulation.
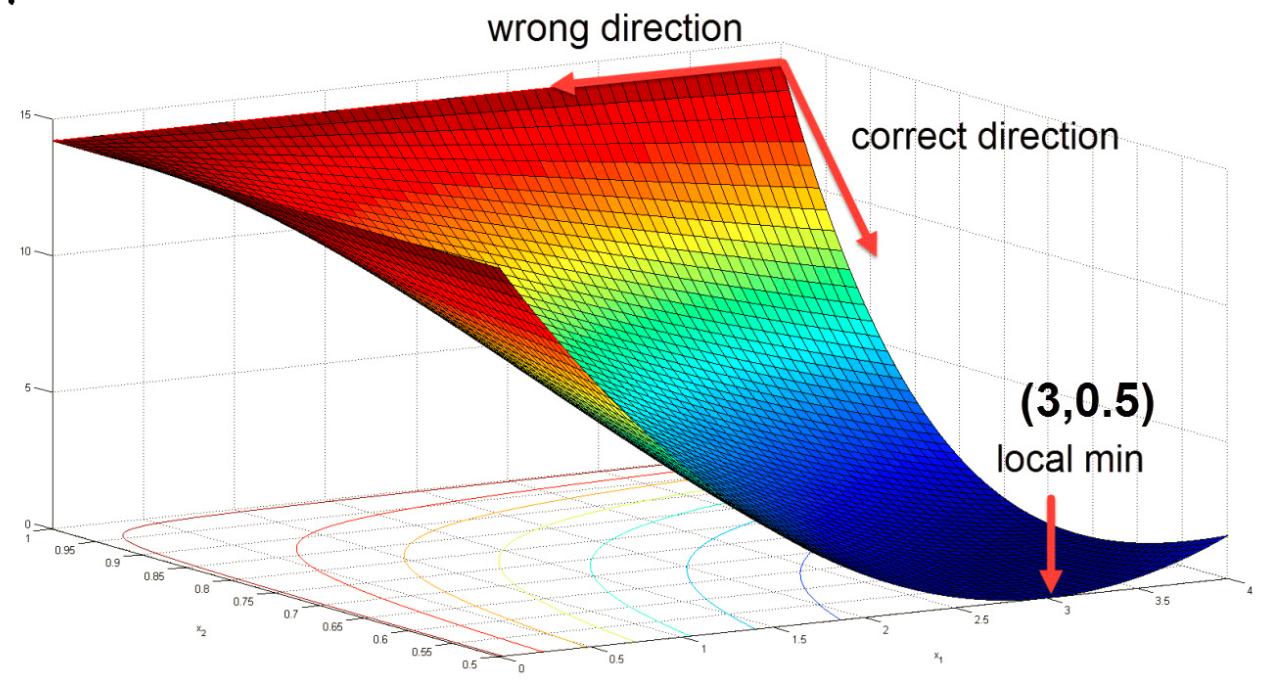
(math.stackexchange.com)
There are various optimization algorithms, such as genetic algorithms or simulated annealing. They work to search for the most balanced design that meets your goals (Key Performance Indicators or KPIs) without getting stuck in one idea.
In a way, they help ensure that your car isn't too fast but unsafe or too safe but slow – they strike the right balance.
In scenarios where physical prototyping and testing are theoretically feasible, the process can be prohibitively time-consuming and expensive compared to the rapid response capabilities of CAE combined with CAD. What if the process could become even faster than simulation? The answer is AI prediction.
Key Elements of Simulation-Driven Design
The use of simulation-driven design software is an integral part of this approach. This specialized software allows engineers to perform detailed simulations, providing insights into the performance, behavior, and optimization of various aspects of a product, from its structural integrity to manufacturing processes.
One of the main goals of simulation-driven design is to enhance the product development process. By integrating simulations into the early stages, engineers can validate designs early, identify design flaws, and make better-informed design decisions. This results in more efficient and cost-effective development cycles.
Computer-Aided Design (CAD) or "Digital Shaping"
Computer-aided design (CAD) is an indispensable tool that revolutionized how we conceive, visualize, and construct everything from consumer gadgets to skyscrapers. CAD is now essential for designers, architects, and engineers.
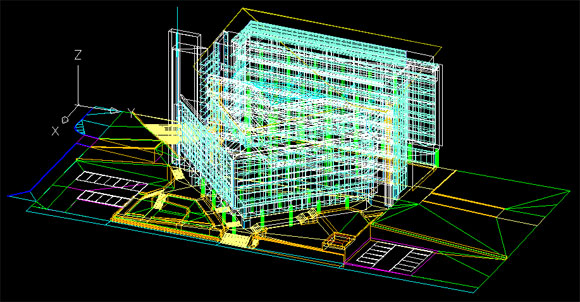
(gis.stackexchange.com)
CAD helps create detailed and precise 2D and 3D representations of objects, structures, and systems. This digital drafting board empowers designers to translate their imaginative concepts into tangible, visual models with accuracy.
Not only does CAD enable the creation of intricate designs, but it also ensures that they are rooted in practicality and feasibility. In other words, CAD facilitates a seamless connection between design and production by generating manufacturable designs.
Designers can incorporate their knowledge of manufacturing processes and constraints directly into the CAD software, ensuring that what they create is not just visually appealing but also feasible to produce.
Also, CAD formats are nowadays easily exportable into formats that CAE can read and process to verify the KPIs associated with a design. Based on what we described above, the simple process of "verification of a solution" by comparing it to a previous design is now overcome with more efficient design space exploration campaigns sweeping across one or more design variables or even exhaustive searches seeking optimum performance while considering constraints.
The question is, how do we modify a digital shape to satisfy targets? Several options are available.
Topology Optimization and Structural Optimization
Simulation-driven design can incorporate topology optimization. Topology optimization is a technique that, in its most common application, explores the most efficient material distribution in a given design space. This process helps engineers reduce material usage and costs while maintaining or improving product performance.

(ms.copernicus.org)
Additive Manufacturing and Structural Analysis
Additive manufacturing, commonly known as 3D printing, is gaining momentum in the manufacturing industry. Simulation-driven design allows engineers to optimize their designs for additive manufacturing, making it possible to create complex and lightweight structures that were previously unattainable through traditional methods.
Structural analysis ensures that 3D-printed products meet performance and safety standards. Simulation-driven design aids in this aspect by providing insights into structural integrity, allowing engineers to make informed decisions and eliminate potential issues early in the design process.
How Simulation-Driven Design Benefits Engineers
Early Validation of Design Concepts
Engineers can fully use simulation technology to validate their design concepts early in the product development process, well before the detailed design phase. This reduces, later on, the risk of costly design changes and tooling rework costs, making it a powerful tool for engineers looking to streamline product development workflows.
Informed Design Decisions
Simulation-driven design empowers engineers to make better-informed design decisions. After the concept design phase, engineers can optimize detailed designs to meet specific performance requirements and practical design, manufacturing and/or cost design constraints, by simulating various scenarios and evaluating their impact on the product.
Improved Efficiency and Cost Reduction
One of the most significant benefits of simulation-driven design is its ability to enhance efficiency and reduce costs. Using parametric modeling and simulation tools, engineers can explore a broad range of design concepts quickly and efficiently. This iterative process allows for identifying cost-effective design solutions without extensive physical prototyping.
Enhanced Collaboration among Design Teams
In the traditional design process model, ideas are often conceived at the drawing board and refined over time. With simulation-driven design, design teams can collaborate more effectively, thanks to a shared digital platform where "status quo" information and "what-if" scenarios are exchanged. This real-time collaboration model hugely reduces the risk of misunderstandings and accelerates the development process.
Streamlined Manufacturing Processes
Simulation-driven design is not limited to product development; it also extends to manufacturing processes. Engineers can simulate material flow, optimize production methods, and reduce manufacturing-related costs. This level of detail ensures that both the product and the manufacturing process are efficiently designed.
Innovations in Product Lifecycle Management
Incorporating simulation-driven design into the product development process can revolutionize the entire product lifecycle. It allows for exploring generative design, a concept that uses algorithms to generate design solutions.
This approach is particularly valuable for complex products and has the potential to uncover innovative design possibilities that may have been overlooked using traditional methods.
After the initial design phase, engineers can use simulation-driven design to fine-tune and validate their product. This includes post-processing simulations to ensure the product performs as expected in real-world conditions. These capabilities significantly reduce the risk of design flaws and costly product recalls.
In the competitive market, speed is often a differentiator. Simulation-driven design enables engineers to accelerate the design process, getting products to market faster. This speed gives companies a competitive advantage by reducing time-to-market and enabling them to respond quickly to changing market demands.
The Future of Simulation-Driven Design
The field of simulation-driven design is continuously evolving. As simulation technology advances, engineers will have access to even more powerful tools that enable them to explore and optimize designs with greater precision and efficiency for product reliability.
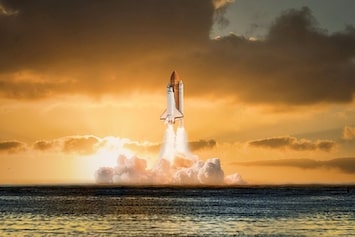
Simulation-driven design, with the AI data-driven "superpowers" and increased physics-driven models, will facilitate greater innovation in product design and engineering thanks to faster and more realistic surrogates of physical reality.
Engineers will be able to push the boundaries of what is possible, creating products that are more efficient, cost-effective, and high-performing. Imagination will be the only limit!