What is Manufacturing Automation: Applications and Advantages
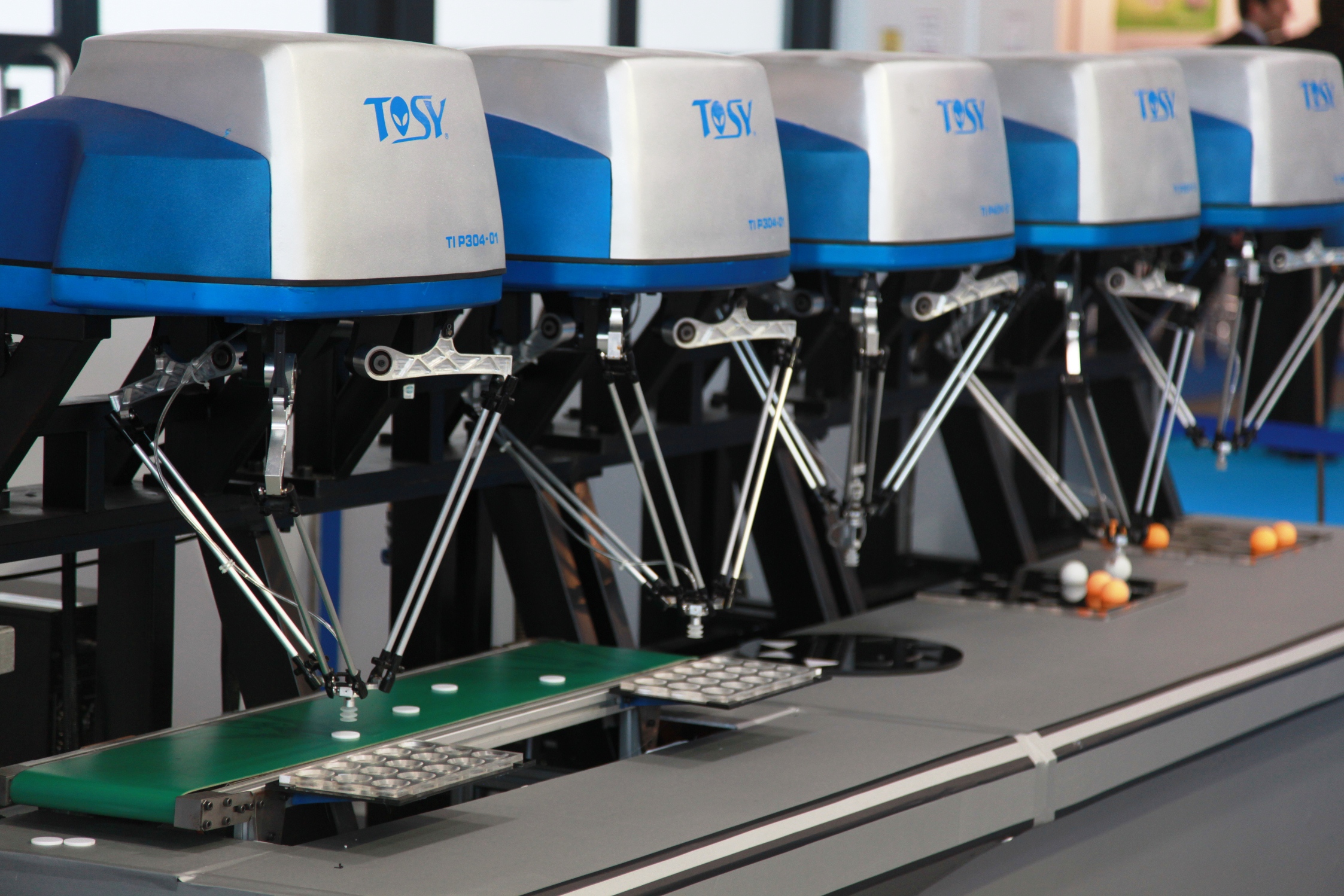
In the manufacturing sector, industrial automation helps systems to perform tasks traditionally done by humans. It involves the integration of robotics, artificial intelligence, and advanced software. Those tools enhance efficiency and improve quality of products. Since industries need to stay competitive, manufacturing automation has become a key driver of innovation, optimizing all processes in manufacturing - from production lines to supply chains.
What is Manufacturing Automation?
Manufacturing automation is about operating production processes with minimal human intervention.
From managers' perspectives, the key benefits of an automated manufacturing system are enhancing productivity and reducing costs. Integrating automated systems into production lines streamlines operations, improves product quality, and helps competitiveness in the fast-paced manufacturing industry. Automated processes impact product quality, optimize the supply chain, and enhance the manufacturing business's resilience.
For engineers, industrial automation's value is in implementing advanced manufacturing systems that can precisely and reliably automate production processes across various product lifecycle stages, from material handling to assembly. Such systems might include fixed process automation setups for mass production, repeatable tasks, or more flexible, programmable solutions for diverse manufacturing lines. On top of it, Artificial Intelligence solutions in factory floors can make industrial robots smarter and more adaptable, allowing them to handle complex, variable tasks.
Process automation is not limited to isolated machines. It involves a comprehensive design approach that integrates across the manufacturing industry ecosystem. With process automation technologies, engineers can transform traditional manufacturing processes into streamlined workflows that anticipate demand, reduce waste, and support efficient manufacturing process scalability.
This article sheds some light on Manufacturing Process Theory, a field that studies the principles, models, and systems that govern manufacturing processes. This includes analyzing manufacturing methods' dynamics, material behavior, system efficiency, automation principles, and quality across manufacturing environments.
The theory is critical for designing efficient production systems, improving manufacturing capabilities, and understanding the value of digitalization within manufacturing lines. Also, process automation in manufacturing can contribute to minimize environmental impact by enhancing sustainability practices in engineering.
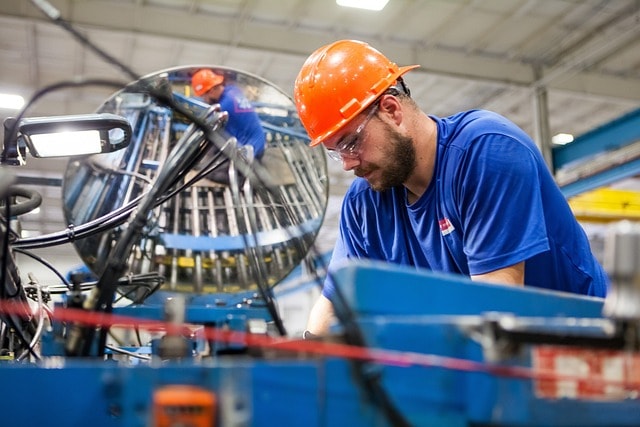
Types of Manufacturing Automation
In manufacturing process theory, there are three main types of manufacturing automation.
These are Fixed Automation, Programmable Automation, and Flexible Automation.
Fixed or hard automation is ideal for high-volume, repetitive tasks using dedicated equipment. Programmable automation is suited for batch production, allowing equipment to be reprogrammed for different product designs.
Flexible automation, also known as "soft" automation, provides maximum adaptability, supporting real-time changes in production without downtime, making it ideal for custom or variable production needs.
Fixed Automation (Hard Automation)
This type is designed for repetitive chores. It uses dedicated equipment and is most efficient in mass production environments, where large production volumes offset the setup cost.
Use cases for fixed automation are found in industries where mass-production, standardized products are essential for the manufacturing business:
- Automotive manufacturing is a classic example, where dedicated equipment assembles car parts in massive quantities with minimal variation.
- Electronics production relies on fixed automation to produce standardized components like circuit boards and chips efficiently.
- Additionally, the packaging industry use fixed automation to handle repetitive, high-speed processes, such as filling, labeling, and sealing. This is cost-effective when production runs are large and require minimal customization.
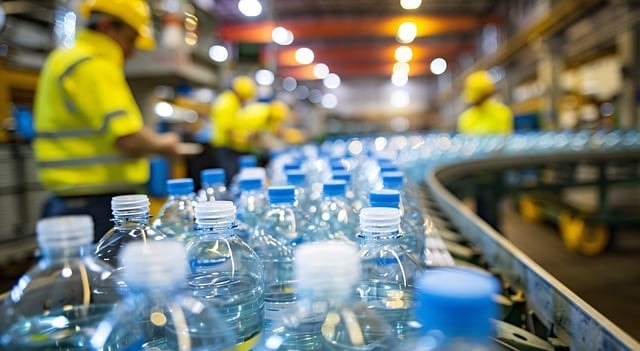
Programmable Automation
For batch production, programmable automation allows reprogramming equipment to handle varying product designs. This flexibility is valuable when product changes are required between production runs.
Use cases for Programmable Automation are common in industries with high product variation and shorter production runs.
- In automotive, programmable automation switches between different car models or parts, adapting production lines with minimal downtime.
- In electronics, programmable automation enables manufacturers to quickly adjust to new product models and features, especially during frequent updates in devices like smartphones or household electronics.
- Industrial machinery manufacturing also benefits, as programmable systems allow customization for different equipment specifications without overhauling the setup entirely.
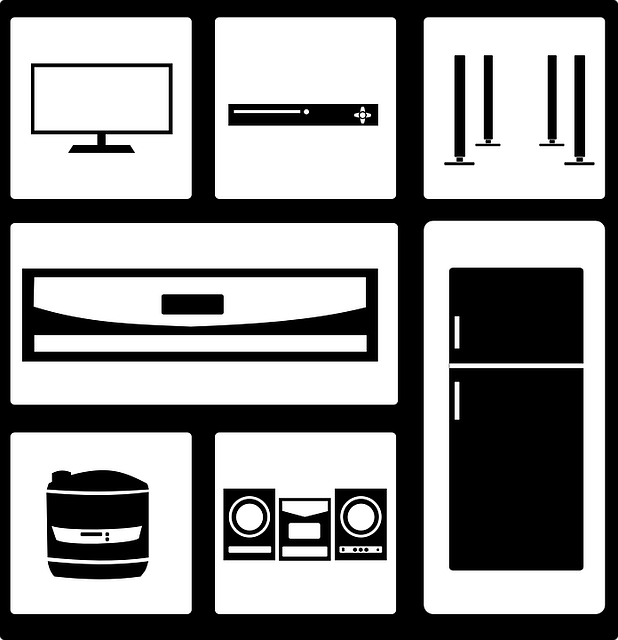
Flexible (Soft) Automation
This is the most adaptable type. It enables real-time changes to manufacturing without significant downtime. It’s ideal for low- to medium-volume manufacturing where frequent changes are needed, such as custom manufacturing.
"Flexibility" comes from advanced control systems, robotic configurations, and modular equipment that can respond to new instructions on demand. In practice, flexible automation can adapt immediately, without completely retooling if a manufacturing order changes.
This type of automation allows manufacturers to meet diverse product demands without extensive retooling between orders. High-mix, low-volume settings require the production line to handle frequent product changeovers, each with unique specifications or design features. Flexible automation meets these needs through advanced, programmable control systems and robotic configurations that can shift tasks on the fly.
For example, flexible automation ensures rapid changeovers with minimal idle time in industries like aerospace or medical device manufacturing, where each product or batch may need to meet specific customer requirements or regulatory standards.
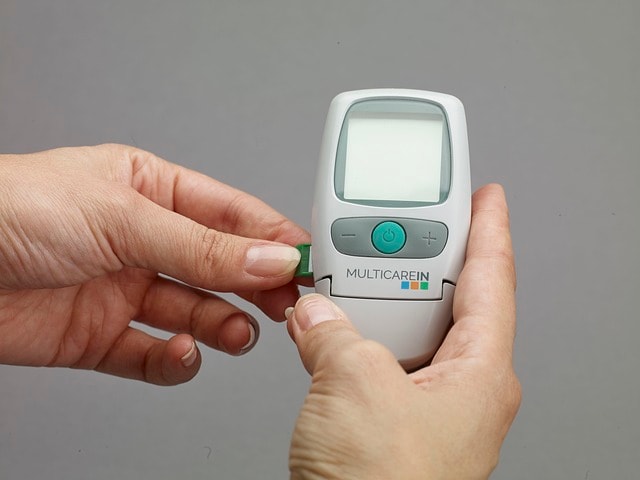
Core Applications of Automation in Manufacturing
We will see what core applications in manufacturing enhance efficiency, quality, and cost-effectiveness by streamlining tasks in the manufacturing process, minimizing human error, and optimizing supply chain operations.
Production and Assembly Automation Technology
Production and assembly are two of the most significant areas of manufacturing automation. Automated systems, including robotic arms and fixed automation, streamline processes by assembling components and completing repetitive assignments faster than manual labor. Automating manufacturing lines reduces labor costs, lowers human error, and increases quality. This type of industrial automation is essential in mass manufacturing environments where maintaining consistent quality and speed is crucial.
Material Handling and Packaging
Material Handling and Packaging involves automating the transfer, storage, and packaging of materials across a manufacturing facility. Automated manufacturing systems like conveyors, automated guided vehicles, and robotic packers make the manufacturing process more efficient by reducing manual handling. Automation in this area reduces bottlenecks and enhances flow within production cycles, directly improving the supply chain. Reducend handling means less time-consuming and risky activities for workers.
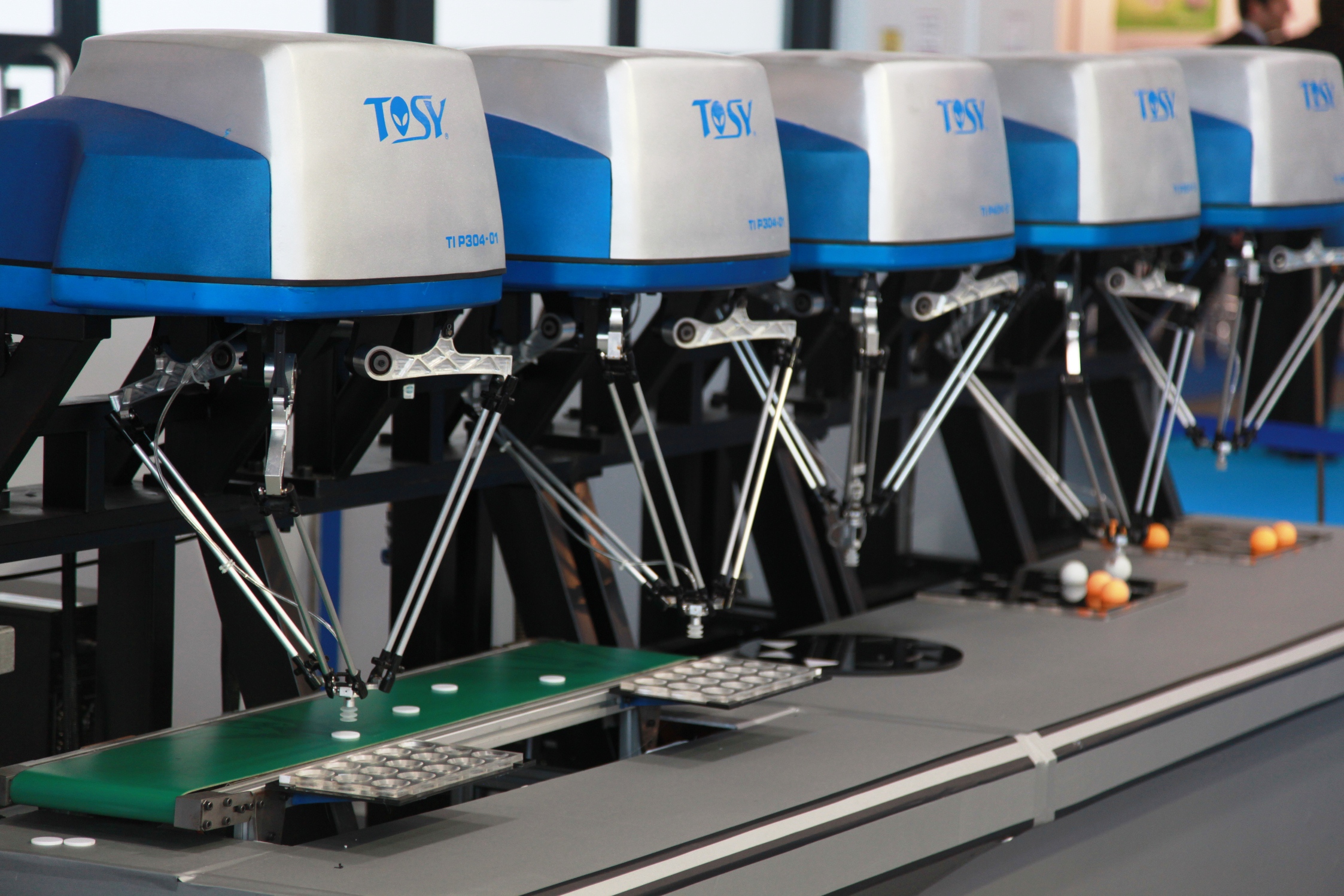
Quality and Maintenance - Production Monitoring
Quality Control and Maintenance uses process automation tools, sensors, and industrial internet technologies to monitor manufacturing quality and equipment health continuously. Real-time data analysis enables the early detection of faults or potential maintenance issues, helping production monitoring to avoid costly downtime and waste. Intelligent automation in quality checks allows manufacturers to maintain high standards while minimizing human errors.
Inventory and Logistics Management
Software systems and smart manufacturing solutions drive automated processes and enhance inventory management across all the supply chain. Automated systems track inventory levels in real-time and ensure materials are available when needed, aligning with JIT (just-in-time) principles.
By automating these time-consuming and often tedious tasks, manufacturers can increase efficiency, reduce storage costs, and improve response times, essential for maintaining competitive production rates.
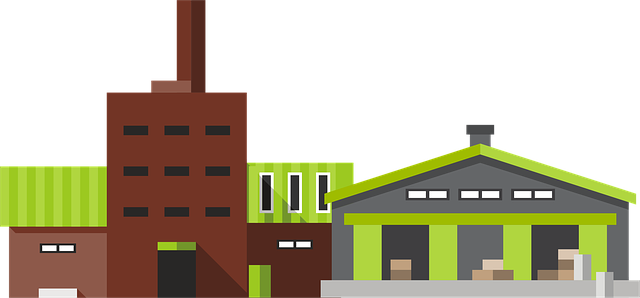
Advantages in Manufacturing
Automation boosts productivity, reduces costs, improves safety, enhances quality, and provides valuable data for continuous improvement.
• Increased Productivity and Efficiency: Automation speeds up production processes by doing assembly work, handling repetitive duties faster than human labor, increasing throughput, and allowing 24/7 operation. This leads to higher production rates and reduced cycle times.
• Cost Reduction and Labor Optimization: the objective is to reduce the need for manual labor and associated costs, allowing relocations to more strategic tasks.
• Improved Safety and Reduced Human Error: the objective is to minimize workers' exposure to dangerous tasks, such as heavy lifting or working with hazardous materials. With AI, we can also reduce the risk of human error, leading to fewer accidents and defects in the production process.
• Enhanced Quality and Consistency: Automated systems ensure uniformity and precision, leading to higher quality. They minimize variability, ensuring that they consistently meet strict quality standards.
• Data Collection and Insights: collecting data in real time offers insights into operational performance. This enables manufacturers to make data-driven decisions for continuous improvement.
The Role of AI and Machine Learning in Manufacturing Automation
AI and machine learning transform manufacturing automation by enabling smarter, more efficient processes, including the implementation of predictive maintenance.
Predictive Maintenance and Process Optimization
By analyzing historical data patterns and anomalies, machine learning models can forecast when maintenance is needed, allowing for proactive repairs. Additionally, AI continuously adjusts parameters in real-time, optimizing workflows, reducing waste, and ensuring resources are used efficiently. This predictive capability leads to smoother operations, longer equipment lifespans, and lower operational costs.
Quality Control and Supply Chain Management
Artificial Intelligence optimizes inventory forecasting in the supply chain by predicting demand patterns, reducing stockouts and overstocking.
Use Case
In the automotive industry, machine learning-based quality systems inspect parts for defects in real time, ensuring only flawless components move through the production line.
AI-driven software can help supply chain forecast demand, optimize inventory, and automate logistics, resulting in reduced costs, improved efficiency, and faster production cycles.
Future of Manufacturing Automation Tools and Their Challenges
• Initial Costs and ROI Concerns: Implementing advanced automation tools requires significant upfront equipment, software, and infrastructure investment. Companies may face challenges in justifying these costs if they don’t see immediate returns, although long-term savings and increased efficiency often outweigh initial expenses.
• Integration with Existing Systems: New technologies must integrate with existing systems, software, and processes. This can be complex, requiring customization or upgrading of infrastructure to ensure smooth operation.
• Skilled Workforce Needs: The shift to automated workflows demands new technologies like AI, creating a demand for continuous skill development in manufacturing.
• Data Security and Privacy: Automation tools become more connected, increasing the risk of data breaches! Protecting sensitive data requires robust cybersecurity measures to safeguard against threats from internal and external sources.
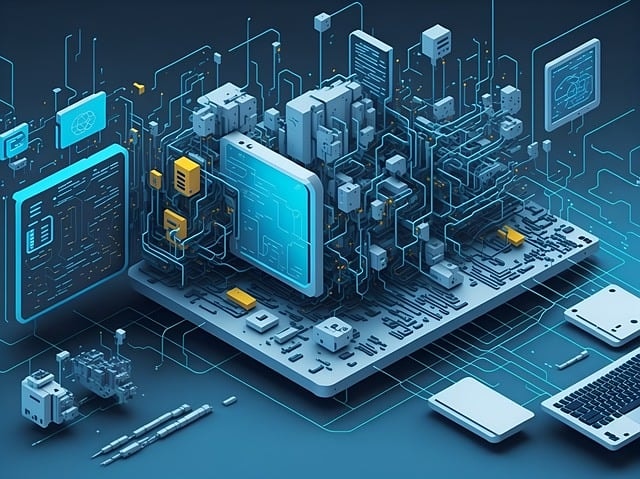
Future of Manufacturing Automation
The future of manufacturing is being shaped by integrating advanced Industry 4.0 technologies, such as Artificial Intelligence, the Internet of Things (IoT), and collaborative robotics. These technologies revolutionize manufacturing thanks to data collection. As a result, manufacturing becomes more adaptable, responsive, and optimized for specific needs.
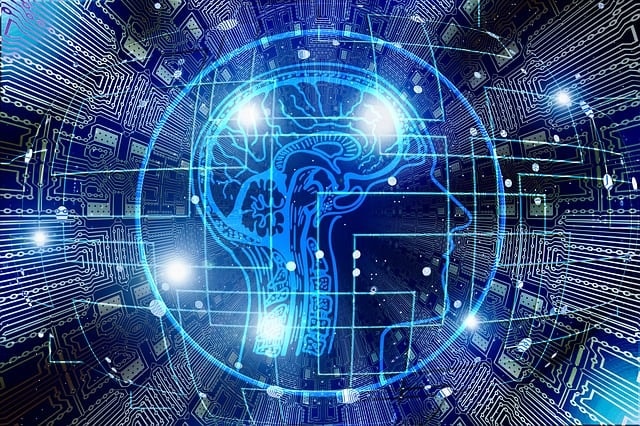
Mass Customization
A key aspect of this transformation is mass customization. Traditionally, mass manufacturing was about creating large volumes of standardized products. With Industry 4.0, manufacturers produce customized products at scale, adjusting designs and features without sacrificing efficiency while maintaining traditional mass manufacturing's high production rates.
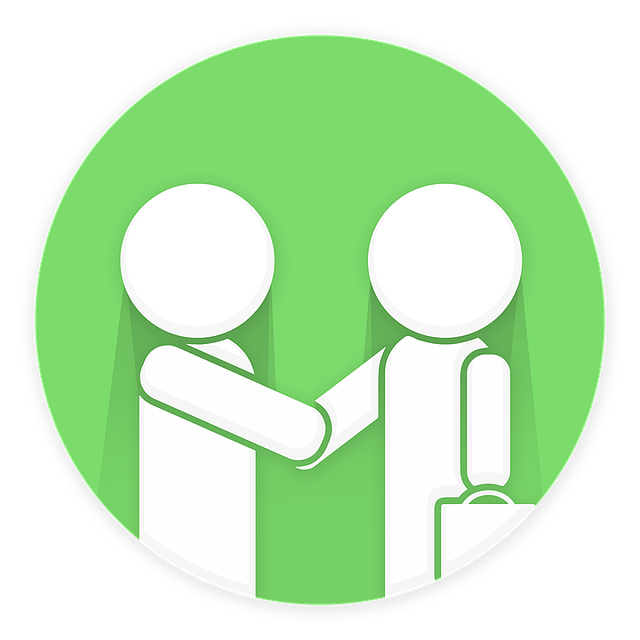
Increasing Role of AI and IoT in Industry 4.0 Smart Factories
In Industry 4.0, smart factories are fully interconnected through AI, IoT, and sensors embedded across all systems. This connectivity enables data collection and analysis in real-time, allowing machines to communicate seamlessly and adapt autonomously.
Collaborative Robotics (Cobots)
Cobots work alongside human operators, enhancing productivity without replacing jobs. They handle repetitive or physically demanding duties, while humans focus on more strategic, value-added activities or perform tasks, fostering a safer and more efficient workspace.
Sustainable Manufacturing
Automation is part of the best practices for sustainable manufacturing since it reduces waste by optimizing manufacturing processes and ensuring materials are used efficiently. Additionally, smart systems manage energy consumption, adjusting operations to minimize energy use and lower carbon footprints, making manufacturing more environmentally sustainable.
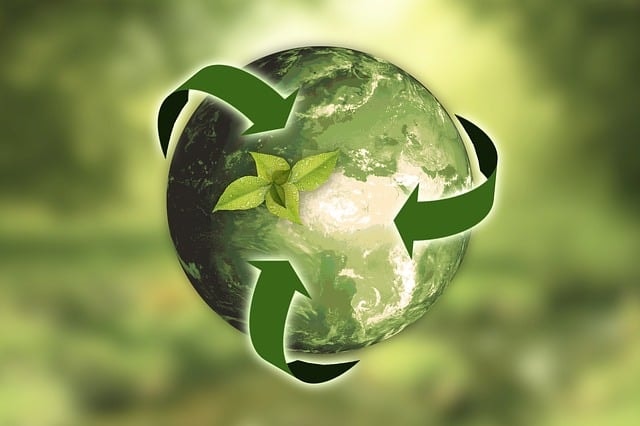
Conclusion
Let us recap on embracing manufacturing automation. Although initial investments can be high, the long-term benefits of increased productivity and reduced operational costs make automation a smart, future-proof strategy.
Implementing robotics, IoT, and AI reduces manual labor in several "boring" tasks, allowing the workforce to focus on higher-value activities in problem-solving related to product innovation .
With real-time data and analytics, automation enhances decision-making, optimizes resource allocation for sustainable policies, and improves quality control.