What Is Engineering Simulation and How Does it Work?
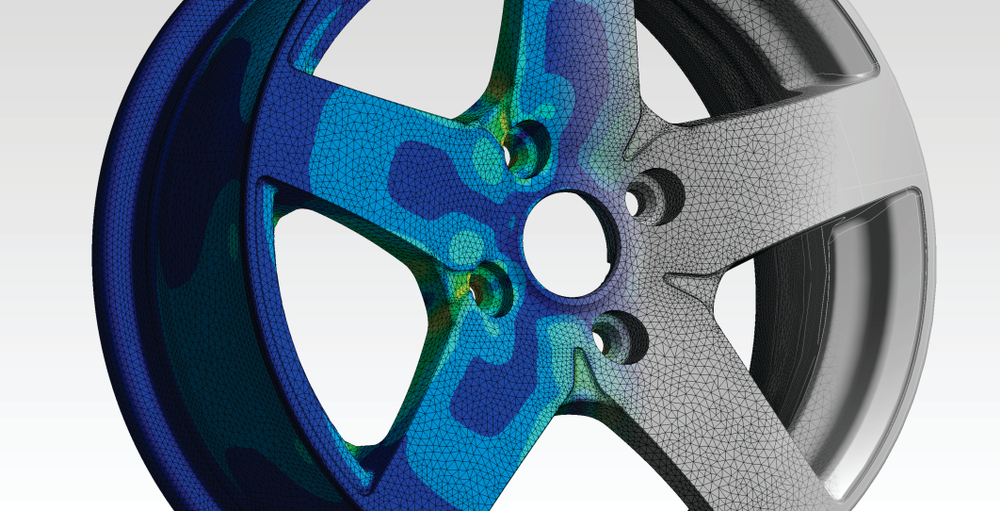
Let us introduce the world of engineering simulations with a familiar example. You are sitting on your terrace, eating ice cream, and texting a friend about a news story you saw on TV about a new vehicle model on the market. Many details of your experience — the building you live in, the refrigerator where you took the ice cream from, and other electronic equipment — were probably simulated with engineering tools!
You may wonder what app is behind it, but there is no holistic simulation software tool. There are engineering simulation tools underlying each type of "working physics," be it electromagnetic waves, heat transfer, solid stress, crashworthiness, or aerodynamics.
In this arena, predictive analytics with deep learning (a branch of Artificial Intelligence) can provide physics-agnostic, data-driven solutions based on the ingestion of vast amounts of high-fidelity data provided by experts.
Engineering simulation platforms are in the hands of specialists with practical skills and theoretical knowledge of structural mechanics or computational fluid dynamics. They know what type of physics to choose from the menu (such as FEA for structural mechanics and crash test simulation and CFD for fluid dynamics) and can translate 3D digital design (CAD) into outputs with physical meaning. They endeavor to reproduce real-world conditions to shorten the traditional time of physical testing and prototyping and, ultimately, time to market.
Please note that "overlapping" of physical approaches is possible such as in the case of thermal simulations that can be analyzed with FEA or CFD. Also, there is interest in to couple of different physical approaches such as in fluid-structure interaction.
Simulation engineering refers to simulating real-world phenomena using computational models within software tools that usually "run" on compute clusters based on CPUs or GPUs. Essential skills such as a good understanding of materials and fluid dynamics are crucial in this field. It is more than producing color maps: preliminary software validation with analytical or experimental data is important. This gives the better-tuned types of simulation the status of "high fidelity".
Thanks to the hundreds or thousands of high-fidelity simulations each CFD or FEA generates, high-fidelity datasets become available for data scientists to feed deep learning and produce surrogates of simulation tools such as Neural Concept Shape (NCS) with tailored predictive models for the "rest of us", i.e. non-specialist engineers who may need a simulation to be "run" quickly on a notebook.
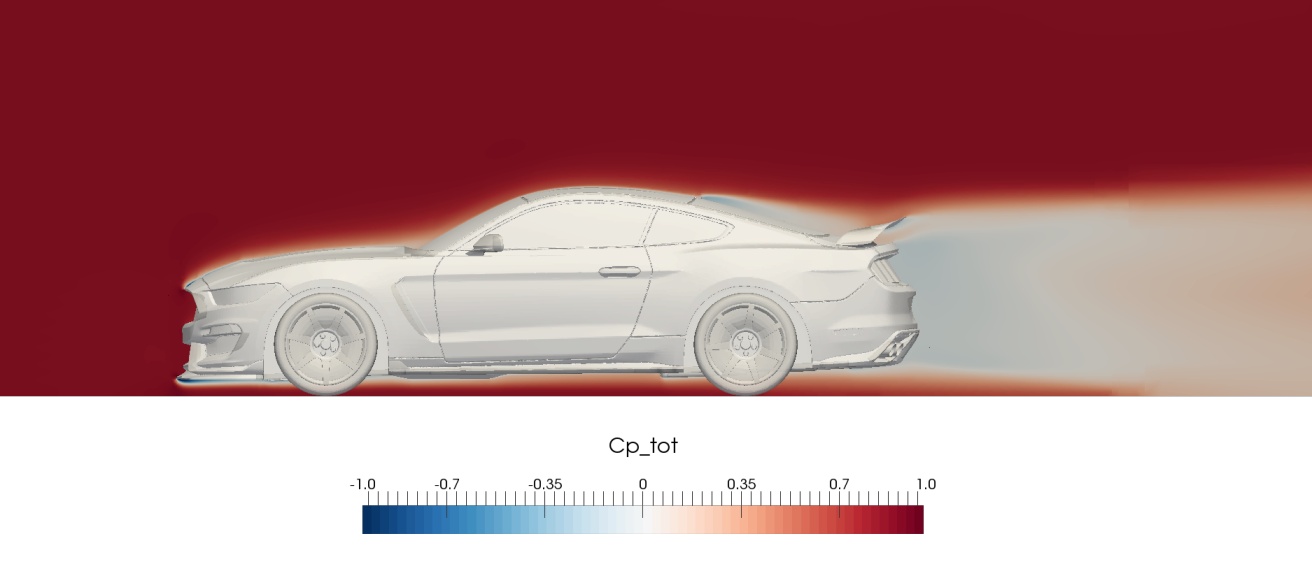
Article Overview
We will briefly review how simulation engineering works and the benefits of engineering simulations. We will also identify a few types of simulation software, ranging from computational fluid dynamics to structural mechanics, with finite element analysis.
Finally, thanks to recent developments and engineering applications such as NCS, we will see the benefits of artificial intelligence and deep learning simulations.
This AI development makes the described processes more available even to those who have no specific skills in simulations and have limited time and computing power. The success of the application is demonstrated by deep learning use cases described in detail elsewhere.
We will review the fundamental principles behind the engineering analysis of virtual environment architecture to understand how simulation can improve product performance in various industries.
The Engineering Simulation Process
Let us start with the traditional product testing process.
Imagine that to increase a car's fuel efficiency and reduce its carbon footprint, we want to test and streamline its aerodynamics thanks to better fluid dynamics: to get performance data, we will physically need a car prototype in a wind tunnel.
Similar processes can be applied to scale models of skyscrapers or airplanes. The equivalent of the physical prototype is roughly speaking the CAD shape and the equivalent of setting up the wind tunnel (speed, type of walls) are the "boundary conditions and preprocessing". Performing the test itself has its digital analog in the "solver".
Input Data
In simulation engineering, input data include material properties, environmental conditions, geometric dimensions, and boundary conditions.
These data are crucial as they define the virtual environments in which the simulation takes place and directly impact the reliability of the results.
Mathematical Modeling for Engineering Simulations
Mathematical models represent the physical behavior of the, usually 3D, object we want to simulate.
Physico-mathematical models are the key difference between experimental testing and modern ML approaches. It is key to have a solid understanding of the underlying physics, which is translated into mathematical equations.
However, once we have an equation, we must solve it for a specific set of inputs and geometry.
Role of Numerics
Solving equations is normally not possible with the pure power of the human brain because the cases where analytical solutions exist are very circumscribed. Therefore, numerical algorithms are employed by open-source or commercial software to solve these equations efficiently and accurately.
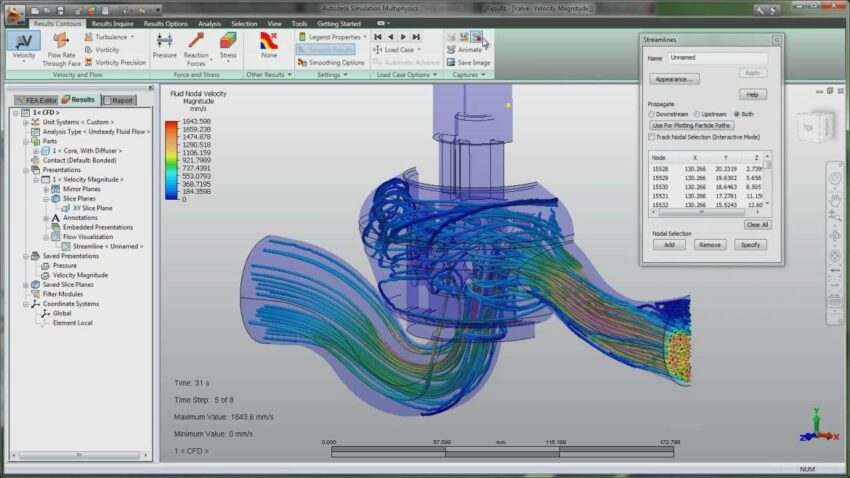
We will delve into a very important part of the simulation process, i.e., the translation of digital CAD shapes into a discrete representation of the continuum that the software will be analyzing. A good understanding of the mesh construction process and the development of tailored meshing strategies is a must for specialists.
Role of Hardware
Once numerical solution techniques are identified, they must be "run" on a combination of software tools and suitable hardware resources — CPU or, more recently, GPU, either owned by users or rented on the cloud.
Upside and Downside
Hardware greatly speeds up the simulation cycle for evaluating performance indicators, and any need for further design iterations can become very expensive.
AI deep learning techniques have helped reduce the wait time from hours to milliseconds, making it possible for anyone interested in evaluating product performance in real time to have quick simulation surrogates.
Engineering Simulation Software
Popular simulation software facilitates the simulation process with user-friendly interfaces and features aiding engineers in setting up simulations, such as automatic mesh generation and built-in solvers for various physics phenomena. These tools streamline the simulation workflow.
Role of Mathematical Models
We will briefly review the role of mathematical models in engineering simulation and how they describe complex systems' behavior.
Those models form the foundation of simulation engineering, providing a framework for representing physical phenomena and predicting system responses under different conditions.
Models are derived from fundamental principles of physics and engineering, and their accuracy and fidelity directly impact the reliability of results.
Equations and Algorithms
This segment involves formulating equations for an object's behavior and developing algorithms to solve these equations using techniques such as the finite element method or finite volumes for computational fluid dynamics. Usually, equation formulation is done upstream of hands-on software usage. At the extreme end of "ease of use", the user of simulation software may be "pushing buttons" without a clear understanding of the physical and mathematical intricacies of the software.
Boundary Conditions
These conditions may include constraints on displacements, velocities, temperatures, or other physical quantities. Thus, defining the boundary conditions constrains the system's behavior and specifies how it interacts with its environment.
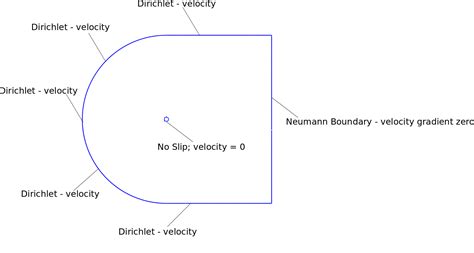
It is possible to observe an object's different responses to different boundary conditions, and sensitivity studies on different boundary conditions are extremely insightful.
Initial Conditions
This sometimes neglected aspect of the simulation process involves specifying the conditions at the beginning of the simulation. These conditions may include the initial velocities, temperatures, or other physical quantities, providing the simulation's starting point.
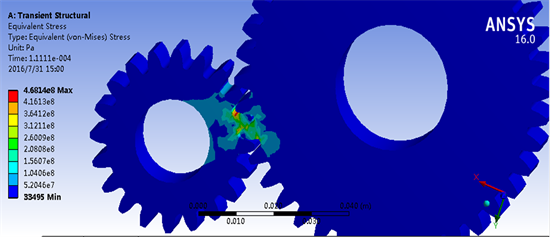
Based on the type of physics you simulate, initial conditions may range from being almost irrelevant to becoming critical for obtaining meaningful simulation results, as small errors or uncertainties could lead to significant discrepancies in the predicted behavior.
Types of Engineering Simulation Tools
There are many ways to simulate the same industrial product! For instance, a vehicle could be analyzed from the crashworthiness point of view with finite element analysis or from the aerodynamics point of view with computational fluid dynamics (CFD). Completely different sets of software tools and different skills are required.
Finite Element Analysis (FEA)
This simulation technique involves dividing the geometry of the system into small, discrete elements and solving for the behavior of each element with numerical algorithms. FEA is used for structural mechanics, heat transfer, and applications where the behavior of solid materials is of interest.
Computational Fluid Dynamics (CFD) Simulation Tools
This simulation technique involves solving the governing equations of fluid flow to predict the behavior of fluids and their interactions with solid structures. CFD is used for aerodynamics, internal fluid flows, and heat transfer.
Multibody Dynamics (MBD) Simulation Tools
This simulation technique does not fully represent 3D behavior. The approach is to represent objects as collections of interconnected rigid bodies. This technique is commonly used for dynamic simulations of mechanical systems such as autonomous vehicles, robots, and machinery.
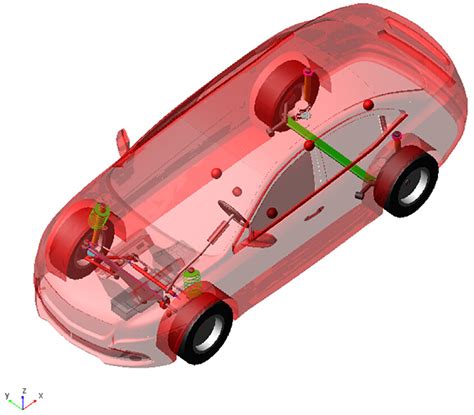
Applications of Engineering Simulation
We will briefly summarize the applications and examples of engineering simulation below.
Aerospace Industry
Let's briefly review specific simulation software for aerospace engineering applications (such as aerodynamics simulations, structural or thermal studies).
A standard tool in this business is NASTRAN (= NASA Structural Analysis), widely used in the industry for finite element analysis of structural components and assemblies.
Developed by NASA in the late 1960s, NASTRAN uses finite element methods to model and analyze the behavior of complex structures subjected to various loading conditions.
NASTRAN is renowned by engineers who use it to design and optimize aircraft and space structures.
Other tools, such as ANSYS or Siemens Simcenter, are also used in the aerospace sector, as is open-source software such as OpenFOAM.
Automotive Engineering
The automotive engineering sector is mature and advanced in developing and applying engineering simulation because of the demanding market and legislation requirements, and the tight interaction between OEM and Tier 1 suppliers.
Applications in automotive engineering include the role of simulation in automotive design, crash testing, and vehicle performance optimization. Powertrain applications, from internal combustion engines to battery simulation, are also crucial for improving vehicle efficiency and performance.
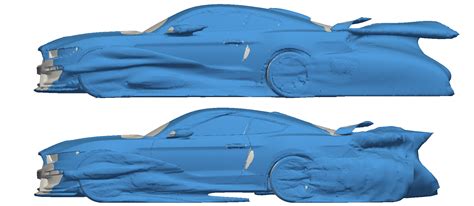
Conclusions
Engineering simulations are based on software tools that, thanks to numerical solutions, allow specialists to predict and validate the behavior of complex systems and optimize their performance without the need for costly and time-consuming physical testing.
By leveraging principles such as mathematical models, numerical algorithms, and advanced usage of simulation software on the cloud or in local compute farms, engineers can simulate a wide range of physical phenomena and gain valuable insights into the behavior of their designs.
The process of engineering simulations generates hundreds or thousands of cases per user stored and can be successfully recycled by Deep Learning. Here, the success story has just begun!
The continued generation of data enhances machine learning capabilities, and fosters progress in the democratization of simulations, making them available to many more engineers, such as project design staff, who strive for better products with iterative design processes.
The application of simulations is growing, opening up new possibilities for innovation and discovery in various projects for all industries.