What Is Battery Liquid Cooling and How Does It Work?
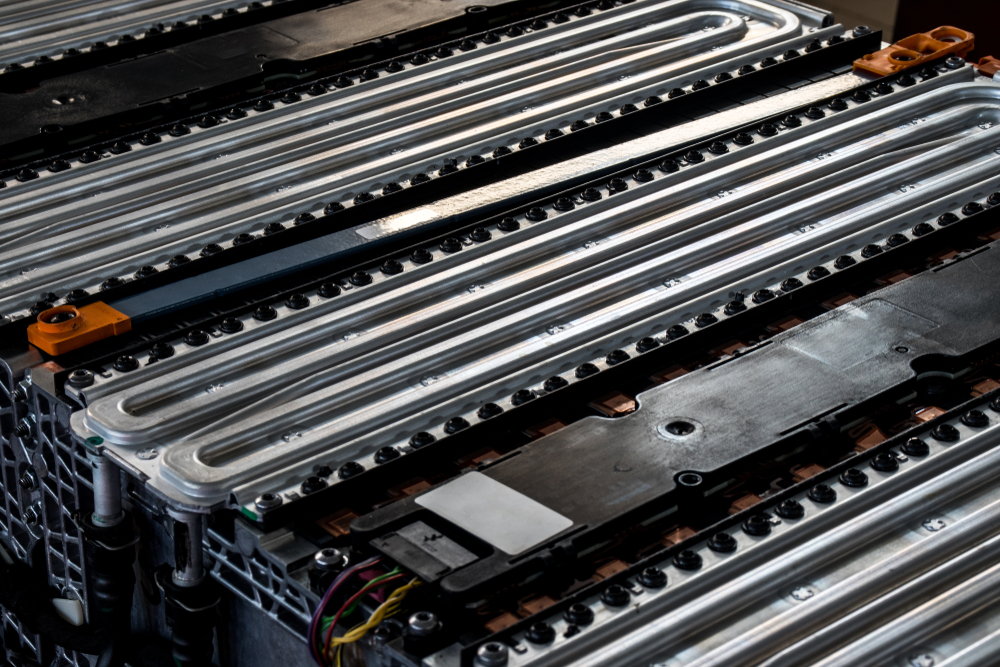
Battery thermal management systems impact vehicle safety and performance. Electric vehicle owners want to be reassured about their cars' reliability and autonomy. Concentrating engineering efforts on the EV battery cooling system and its optimization can guarantee electric vehicle durability and safety while allowing for fast charging.
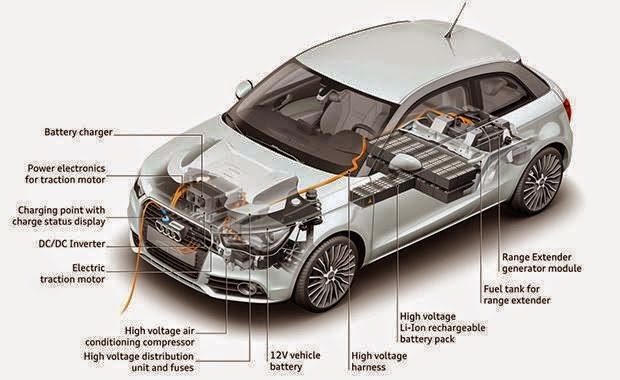
EVs are characterized by battery packs that store energy in chemical form. These battery packs comprise several cells connected in series and parallel to achieve the desired voltage and capacity.
Lithium-ion (Li-ion) batteries are the most common type used in EVs thanks to their high energy density, long cycle life, and relatively low self-discharge rate.
Li-ion batteries generate heat during charging and discharging and must be kept within an optimal temperature range. In the "thermal runaway" phenomenon, if a battery becomes too hot, it can lead to a dangerous condition where it rapidly releases energy, potentially causing fires or explosions.
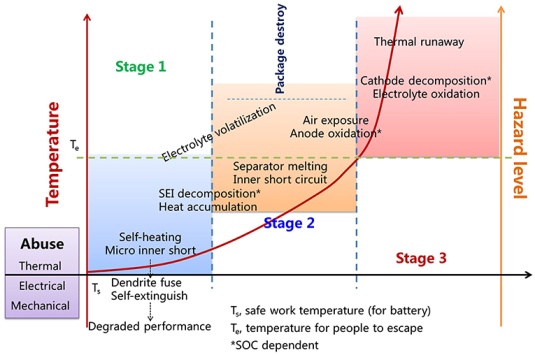
In the face of those dangers, let's keep cool: the situation is under control!
Cooling helps maintain battery modules at optimal operating temperatures, improving battery efficiency and extending lifespan. An efficient battery thermal management system also ensures consistent performance under varying conditions (e.g., extreme temperatures and the sought-after fast charging).
In the following, we will investigate the introductory physics of liquid cooling vs. air cooling and its beneficial effects on Electrical Vehicle (EV) drivers.
A topic impacting our daily lives in terms of personal comfort and with huge industrial implications is thermal management and how to master it. We will leave the reader to imagine the challenges related to air cooling systems in our buildings or the R&D for new fabric optimized for heat exchange for sports equipment.
In the following, we will focus on cooling systems for electric vehicle batteries and the battery thermal management system after a very soft start on heat exchange. This will help identify liquid cooling systems to extend the battery pack's safety and life.
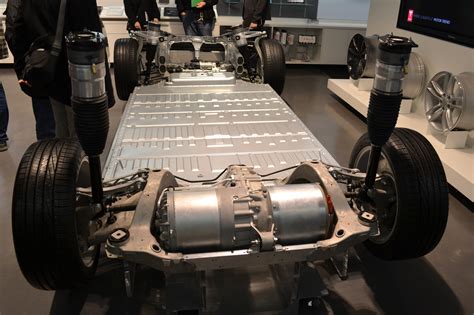
Elementary Overview: Liquid Cooling System Vs. Air Cooling System
Many engineers can use heat exchanger design software, but what are the principles behind it?
It is easier and more intuitive than most non-technical readers would think. This short introductory overview will focus on the 101-level "physics of cooling."
We will review the concept of cooling systems and why liquid cooling can be superior to air cooling in a thermal management system while considering the technological challenges of cooling systems based on air and liquids.
To keep the discussion general, before tackling the battery thermal management system, we will describe "any" cooling system in this paragraph. Thus, the physics can be related to a heat exchanger and not necessarily to a battery pack.
Since battery packs have their idiosyncracies, we discuss the specifics of the battery cooling system in a later chapter.
Air Cooling: Forced Vs. Natural Convection (Passive Cooling Vs. Active Cooling)
It is intuitive that given a long time, any object with T₁ exceeding a desired temperature T₀ can just be placed into a "thermal bath" or "thermal reservoir." The reservoir is in an arbitrarily large surrounding environment at temperature T₀; it is so large that it is not influenced by the object, so the object's temperature will reach T₁ → T₀ while the reservoir temperature will be maintained at the set value T₀.
However, this passive approach, waiting for thermal equilibrium, may take a long time, which is unacceptable for the daily use of engineering products.
An air cooling system is often chosen to prevent an object from exceeding a temperature range within a specific time. Again, let us carefully distinguish between "natural" and generally slow convection and "forced" and fast convection.
To give a practical elementary example, let us sit in front of a hot dish. The first option is to wait for it to cool down by natural convection (let us ignore conduction phenomena in this elementary model). However, what shall we do to reach the desired temperature if we have a time constraint?
The first active cooling mechanism that comes to mind is active air cooling, which we are all familiar with: we blow on a hot dish to "take the heat away." More technically, this mechanism uses forced convection, thus multiplying the heat transfer coefficient "h" from its natural convective value to a forced convective value typical of active cooling systems.
The next question is, what are the types of heat exchangers yielding the most efficient cooling, giving "superpowers" to the heat transfer coefficient?
Liquid cooling is the answer you were looking for. Follow us for the next exciting step into coolness!
Enter Liquid Cooling: Air Cooling Vs. Liquid Cooling Methods
We now dive into some simple mathematics behind the heat transfer coefficient and its relationship with flow rate in liquid cooling systems.
The heat transfer coefficient, denoted as h, represents the proportionality coefficient between the heat transfer rate (J/s or W), q, and the temperature difference ΔT driving the heat flow.
The flow rate ṁ of the coolant affects the heat transfer coefficient. Higher flow rates lead to better heat transfer. This is because faster flow rates promote better mixing and increase the contact area between the fluid and the exchanger's walls, facilitating heat exchange.
Now, let us come to the essential discussion of comparing the flow rate ṁ of air cooling and liquid cooling.
First, air cooling is straightforward, and we are familiar with air-based coolers, such as CPU or GPU fans, that dissipate heat. Maintenance is minimal, usually limited to occasional cleaning. However, the fan is the point of failure for air-based cooling systems. Without it, forced convection "collapses" to natural (weak) convection or conductions through the walls of the equipment's housing, and usually, this type of cost-free but slow energy dissipation is not sufficient.
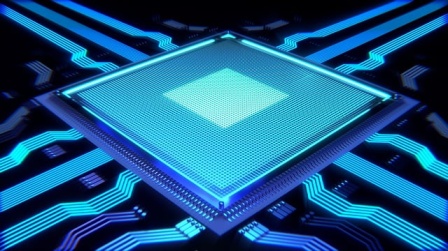
Liquids are much more efficient at transferring heat than air. Thus, liquid-cooling systems can remove substantial heat with relatively low mass flow rates.
The higher heat transfer coefficient for liquid cooling allows for more efficient heat removal. The flow rate of the liquid (ṁ) is directly related to the heat transfer coefficient:
q= ṁ x Cp x ΔT
where Cp is the specific heat capacity of the liquid in [J/kg/K].
For air at room temperature (approximately 25°C or 298 K), the specific heat capacity (Cp) is ≈ 1.005 kJ/kg/K. For common coolant liquids (water, having Cp ≈ 4.18 kJ/kg/K), ethylene glycol (commonly used in automotive coolant mixtures) has Cp ≈ 2.51 kJ/kg/K, more or less like propylene glycol (another standard coolant additive), whose Cp is ≈ 2.50 kJ/kg/K.
In terms of mass flow rate ṁ, one may think that air is easier to propel with a fan than a liquid with a pump - however, it is also essential to consider the density ρ of the coolant in the equation! Coolant liquids are much denser than air, which means they can carry more energy per unit volume. So, even though air flows faster, the denser coolant can still carry more heat energy per unit volume due to its higher density.
Assuming standard conditions (≈ 25°C or 298 K), the density ρ is around ≈ 1.225 kg/m³ for air. For common coolant liquids, let's take the density of water as an example, which is approximately ρ ≈ 1000 kg/m³.
Assuming the same energy per unit volume of liquid coolant and air, the liquid can still carry more heat energy overall due to its higher thermal capacity per unit mass (specific heat capacity). This allows liquid cooling to efficiently transfer heat away from a source with lower mass flow rates than air cooling systems.
The Cooling Medium
The choice of coolant depends on the specific application, climate, and system requirements. Water-based coolants with antifreeze are prevalent, while an electric vehicle may use specialized coolants like dielectric oils or PCMs.
Water is an "intuitive" coolant in both internal combustion engine (ICE) cars and electric vehicles (EVs). It has excellent heat-absorbing properties and is cost-effective. However, pure water has limitations, such as freezing and boiling in a relatively narrow range of temperatures. A mixture of water and antifreeze (such as the ethylene glycol or propylene glycol we introduced before) is used to address this. This mixture lowers the freezing point and raises the boiling point, making it suitable for various climates and operating conditions.
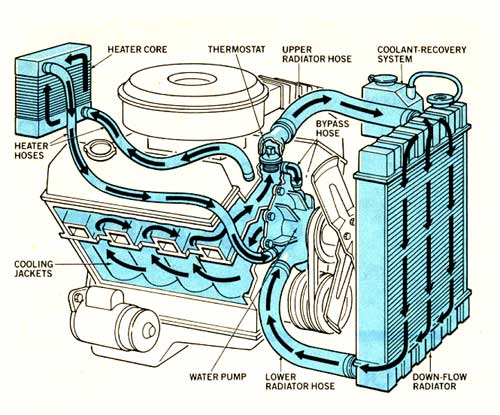
When mixed with water, antifreeze forms the coolant solution. It prevents freezing in cold weather and boiling in hot conditions. As a positive side effect, antifreeze materials contain corrosion inhibitors to protect engine components.
The most common antifreeze types are ethylene glycol-based and propylene glycol-based. Ethylene glycol is more efficient but toxic, while propylene glycol is less toxic - but less efficient.
Dielectric oils (non-conductive) are used in electric vehicles to cool components like power electronics and electric motors. These oils have good thermal properties and can effectively transfer heat away.
The Cooling Geometry
Now, we have to introduce a little bit of physical equations. A nice simplification to represent heat exchange between two bodies at temperatures T₁ and T₂ is the Newton equation
q= h x S x (T₁ - T₂) = h x S x ΔT
where q is the heat transfer rate [W], h is the heat transfer coefficient [W/m²/K], and S [m²] is the exchange surface. Now, it is pretty intuitive that to increase q, all the rest being equal (T₁ and T₂ are given and yield the temperature difference ΔT, and h is limited by physics), we can decide to operate on the exchange surface S.
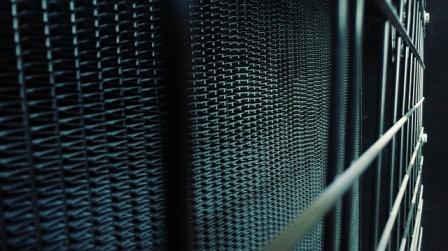
So, at the core of thermal management systems and for many types of cooling methods, we can "play" with the heat exchanger's surface area S. Since the enveloping volume V is limited, we can choose to "fold" a surface within a given space by creating channel structures, fins and so on, to increase the available exchange surface and the S/V ratio. We could say that S enshrines the shape or geometry of the cooling system.

One common approach is to increase the surface area of the cooling channels through various means, such as creating intricate patterns or using extended surfaces like fins. Fins are particularly effective in enhancing heat transfer because they provide additional surface area for convection. Due to the increased contact area, heat is transferred more efficiently when air or liquid flows over these fins.
Furthermore, the shape and geometry of these channels play a crucial role in determining the cooling system's effectiveness. For example, the cross-sectional shape of a cooling channel can influence fluid flow patterns and heat transfer rates. Engineers often utilize computational fluid dynamics (CFD) simulations to optimize channel geometry for maximum heat dissipation while minimizing pressure drop.
In addition to channels and fins, other devices such as heat sinks, heat pipes, and thermal interface materials (TIMs) are also commonly employed in thermal management systems.
Heat sinks, typically made of materials with high thermal conductivity, such as aluminum or copper, are designed to absorb and dissipate heat from a component into the surrounding environment.
Heat pipes, however, can use phase-change principles to transport heat more efficiently from one location to another.
Principles of Battery Liquid Cooling
We are ready now to tackle the specialist task of the different battery cooling systems for a battery pack and, more specifically, an EV battery cooling system.
We will now discuss the different aspects of the liquid and cooling methods, including their advantages over air cooling, the effectiveness of heat transfer between the battery and liquid, and examples of liquid cooling systems used in electric vehicles.
The Dangers of Thermal Runaways
In the introduction, we hinted at thermal runaways in battery cooling systems and their associated risks and challenges.
Thermal runaway in lithium-ion batteries can have several negative consequences. We will list three to increase the trouble. Mild cases result in battery swelling due to excessive heat. Batteries under thermal runaway may leak their internal electrolyte. Finally, in severe cases, escalating heat can lead to the battery catching fire.
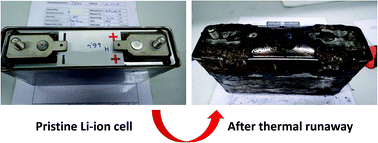
The strategies for mitigating thermal runaways are optimized cooling systems, active thermal management, and advanced battery management systems. While combining these strategies with a "holistic" c approach is essential for ensuring battery safety and preventing thermal hazards, we have focused on the cooling system in this article.
Temperature Range: Too Hot & Too Cold?
Proper temperature management is essential for optimal battery performance and safety! As a rule of thumb for lithium-ion batteries, the optimal operating range is typically between 0°C and 45°C. Let us now dive into more details about battery temperature.
Challenges of the Cold Temperature Range
Cold temperatures reduce the battery's capacity to store and deliver energy. For every 10°C drop in temperature, capacity can decrease by around 20%! Cold weather increases internal resistance, hindering current flow, which results in reduced power output and slower charging/discharging rates. Electric vehicles (EVs) experience reduced range in cold weather due to battery inefficiencies. Heating systems also draw power, further impacting electric vehicle batteries' operating range.
Challenges of the High-Temperature Range
High temperatures increase the chemical reactions inside Li-ion batteries, leading to greater performance and increased storage capacity. For example, increasing the temperature from 25°C to 45°C can result in a 20% increase in maximum storage capacity.
However, there is a bitter downside: the battery's lifecycle decreases over time at higher temperatures. Charging the battery at 45°C versus 25°C caused more significant degradation (6.7% vs. 3.3%) over the first 200 cycles. Prolonged exposure to extreme heat can severely diminish the battery's overall lifespan.
Types of Battery Thermal Management Systems
This paragraph will focus on different approaches to a liquid cooling system, such as direct and indirect cooling, contact liquid cooling, and cold plate cooling.
Direct Contact Liquid Cooling
In this method, a liquid coolant (usually water or a mixture) directly contacts the heat source. Due to direct contact, heat is efficiently transferred from the source to the coolant. The coolant then flows through a heat exchanger to dissipate the heat into the surrounding environment.
Cold Plate Cooling
Cold plates are flat metal surfaces with embedded channels for coolant flow. These plates are placed in direct contact with the heat source (e.g., cells or electronic components). The coolant absorbs heat from the source and carries it away, maintaining a consistent temperature. Cold plates are commonly used in high-power electronics and electric vehicle battery packs.
Cold plates must be exceptionally flat to ensure efficient contact with heat sources. Any surface irregularities can hinder heat transfer, so achieving a high flatness tolerance is critical for optimal performance.
Regarding manufacturing challenges, choosing materials with low thermal expansion coefficients is essential to prevent warping during temperature variations. Cold plates require precise machining to maintain flatness because any deviation could impact heat transfer performance.
Working Principle of Liquid Cooling System - Efficient Heat Transfer Mechanism
An efficient heat transfer mechanism that can be implemented in the cooling and heat dissipation of EV battery cooling system for the lithium battery pack, such as a Tesla electric car, can be the following:
Batteries are cooled by a liquid-to-air heat exchanger that circulates cooling fluids through the battery cells. The coolant is a mixture of water and ethylene glycol (similar to antifreeze). This system transfers heat from the battery cells into the air using convection or forced airflow. The cooling process involves glycol circulating through pipes within the battery pack, absorbing waste heat generated during charging. The glycol flows through an external radiator, releasing heat into the ambient air.
Utilization of Latent Heat for Temperature Control
Phase Change Materials or PCMs store and release latent heat during phase transitions. Common PCMs include paraffin waxes, salt hydrates, and organic compounds. In battery thermal management, PCMs can absorb excess heat when the battery temperature rises. The PCM releases stored heat as the battery cools down, helping maintain a consistent temperature.
PCMs can be embedded within the battery pack structure. During high-temperature conditions (e.g., fast charging), the PCM absorbs heat, preventing cell overheating. As the battery pack cools, the PCM releases heat, stabilizing the temperature.
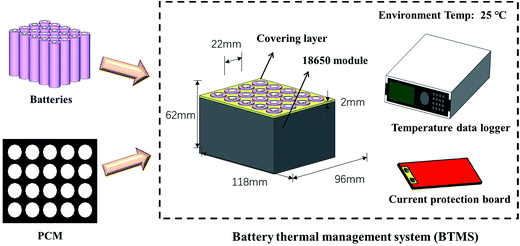
Another approach is coating the battery with PCMs, which act as a thermal barrier. The PCM absorbs heat when the battery heats up, preventing temperature spikes. This approach enhances safety and extends battery life.
Regarding battery cooling, the three general classes of PCMs that effectively serve as cooling agents are listed below.
Salt Hydrates
Salt Hydrates are salts dissolved in water. They have excellent heat-absorbing properties due to their high latent heat of fusion, such as sodium sulfate decahydrate (Glauber's salt) and calcium chloride hexahydrate.
n-Alkanes
n-Alkanes are organic PCMs derived from hydrocarbons. They exhibit phase change behavior at specific temperatures. Paraffin waxes fall into this category. Paraffin waxes have good thermal stability and can absorb and release heat during phase transitions.
Non-Paraffin Organics
Non-paraffin organics include various organic compounds other than paraffins. Examples include fatty acids (such as stearic acid) having higher thermal conductivity than paraffins. These non-paraffin organics offer a balance between thermal performance and safety.
Summary and Future Developments for Battery Thermal Management Systems
Exciting times lie ahead for electric mobility! The future of EV battery cooling involves solid-state batteries, faster charging, and more innovative system designs. These features rely on proper temperature management: optimal battery temperature is achieved thanks to liquid cooling systems. The article reviewed introductory physics, showing why liquid cooling could better control battery temperature. We reviewed the main types of cooling systems for the battery pack of electric vehicles and advanced topics such as phase change material (PCM) selection.
We will close with a historical perspective. In the early days, Nickel-Metal Hydride (NiMH) batteries were popular, but they had limitations like lower energy density and shorter lifespans. The game-changer was Lithium-ion (Li-ion) batteries, which had higher energy storage, reduced weight, and longer life cycles. Tesla's Roadster (2008) set a benchmark with its Li-ion cells, providing an unprecedented 245 miles of range. Today, some EVs promise 400 miles on a single charge.
Future advances include solid-state batteries exhibiting higher energy density, faster charging, and improved safety. These batteries replace liquid electrolytes with better-performing solid materials.
Lastly, faster electric vehicle charging is crucial for mass adoption. Innovations in charging infrastructures and battery technology aim to reduce charging times significantly for electric cars. We should expect rapid charging stations to become more widespread, making long trips convenient for electric vehicle owners who will rely on ever-better battery cooling.