Truck Aerodynamics - Enhancing Performance & Fuel Economy
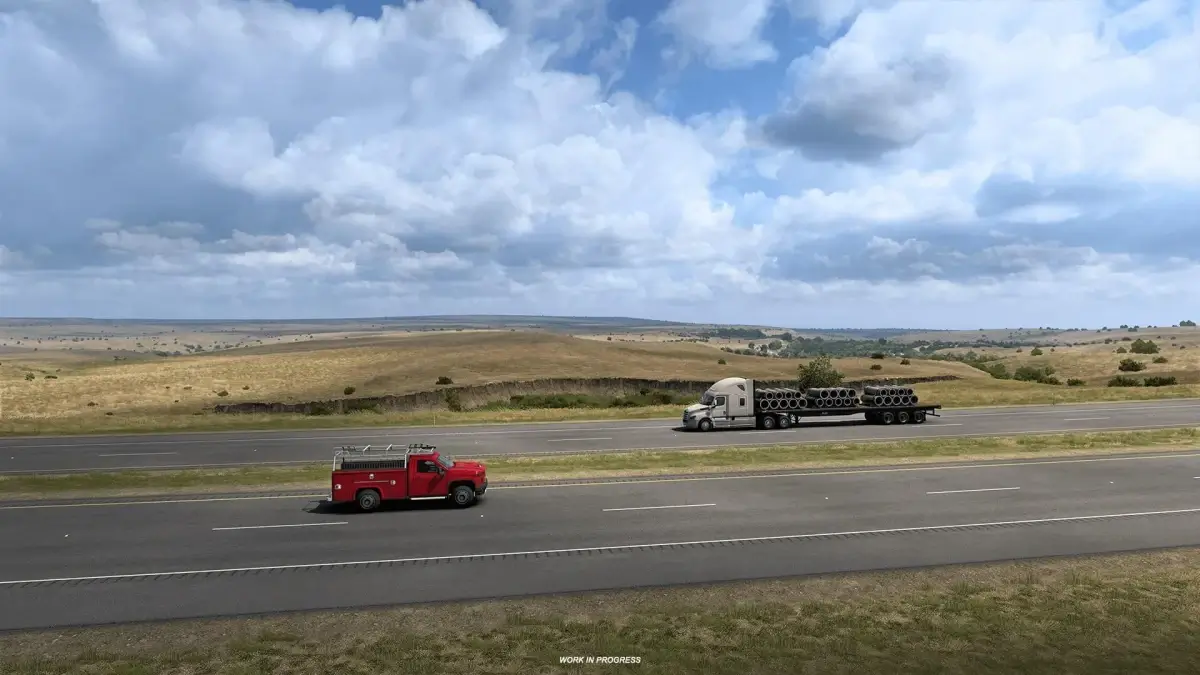
Trucks are often perceived as a hindrance to highway car drivers due to their slower speed, but they are an indispensable component of our daily lives and crucial to our economy.
Trucks ensure the smooth transport of essential goods, such as food supplies to supermarkets and furniture to new homes.
While speed may not be a top priority for trucks, their aerodynamics plays a crucial role. This article will therefore delve into the various methods available to enhance truck aerodynamics, including cutting-edge tools for designers like wind tunnels, CFD, and the latest progress in Deep Learning.
As a start, we will examine the challenges the truck industry faces. Examples are market demands and international regulations. We will highlight the differences between truck aerodynamics and motorsport or passenger cars.
We will also touch on specific truck aerodynamics topics, such as the role of snow on truck aerodynamics and the aerodynamics of buses and semi-trucks concerning trucks. Also, we will discuss the special needs of EV trucks.
We will summarize some theories presented here with a concrete case history in truck aerodynamics.
Market Pressure - Enhancing Aerodynamics for Compliance
The trucking industry is constantly pressured to reduce costs, increase efficiency, and minimize environmental impact. Fuel consumption is a high cost for trucking companies, and fuel prices are volatile, making fuel savings and efficiency a critical factor in the industry's success. Improved aerodynamics tractor design can reduce fuel consumption and, in turn, costs for trucking companies.
Truck manufacturers are also under customer pressure to produce more environmentally friendly trucks. Many companies have set sustainability targets, and they expect their suppliers to contribute to achieving these goals. Improved aerodynamics can lead to lower fuel costs and reduced emissions, which can help truck manufacturers meet these targets.
In response to the growing concern over emissions from heavy-duty vehicles, the European Union has implemented a comprehensive set of regulations to reduce CO2 emissions. These regulations specifically target trucks, placing stringent requirements on manufacturers to enhance fuel efficiency and lower their environmental impact.
Truck manufacturers are tasked with finding innovative solutions to reduce fuel consumption to meet the set emission reduction targets. One of the key areas of focus lies in improving truck aerodynamics. By optimizing the design and shape of trucks, manufacturers can minimize air resistance, thus improving overall fuel efficiency.
Compliance with the EU regulations requires truck manufacturers to measure CO2 emissions and fuel consumption accurately. This measurement process is conducted in controlled environments, where various parameters are considered. Among these parameters, truck aerodynamics plays a crucial role in ensuring the accuracy and reliability of the tests.
Improving truck aerodynamics becomes essential for complying with the EU regulations due to its impact on the measurement process. By fine-tuning the aerodynamic characteristics of trucks, manufacturers can ensure that the recorded emissions and fuel consumption data align with real-world conditions. This alignment is vital for accurate assessments and effective implementation of emission reduction strategies.
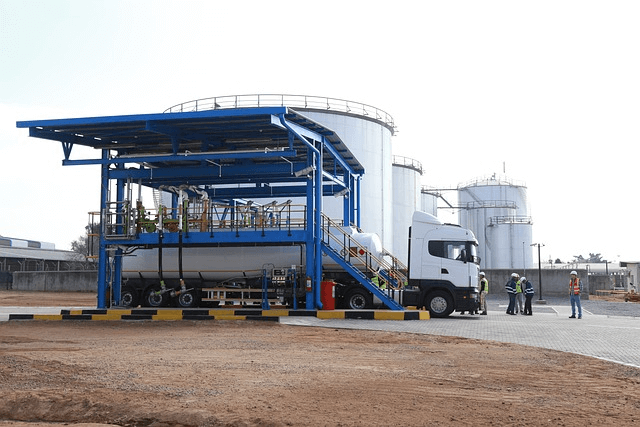
Furthermore, truck aerodynamics contribute to compliance and offer additional benefits to the manufacturers and the environment. Enhancing aerodynamics can reduce truck operators' fuel costs, promoting economic sustainability. Moreover, as trucks become more streamlined, they generate fewer emissions and lessen their carbon footprint, aligning with broader environmental goals.
The EU truck regulations have emphasized improving aerodynamics to meet emission reduction targets and enhance fuel efficiency. By optimizing the design and shape of trucks, manufacturers can achieve compliance, ensure accurate measurements of CO2 emissions and fuel consumption, and contribute to a greener and more sustainable future.
An Aerodynamics Primer: Understanding the Basics of Fluid Dynamics and Aerodynamics for Truck Designers
In truck design, a solid grasp of fluid dynamics and aerodynamics principles is paramount to optimizing performance, fuel efficiency, and overall vehicle design. Fluid dynamics governs the behavior of fluids, while aerodynamics specifically focuses on the interaction between air and solid objects.
The following "primer" aims to provide truck designers with a short overview of the fundamental concepts and physics underlying fluid dynamics and aerodynamics, offering insights that apply to their field.
Fluid Dynamics: The Basics
Fluid dynamics is a branch of physics that studies the behavior of fluids, including gases and liquids, when they are in motion or at rest. It is a fundamental field of study with broad applications in various industries, including automotive engineering. In the context of truck design, applying the basic principles of fluid dynamics is essential for optimizing aerodynamics, reducing drag, and improving fuel efficiency.
Fluid Dynamics. Conservation of Mass
One of the fundamental principles in fluid dynamics is the conservation of mass. This principle states that the mass of fluid entering a control volume equals the mass exiting the volume, assuming no mass is created or destroyed within the system.
This concept is crucial in understanding truck aerodynamics, as it helps designers analyze how the fluid interacts with the vehicle's surface and flows through the various components.
Fluid Dynamics. Conservation of Momentum
Another fundamental principle is the conservation of momentum. According to this principle, the rate of change of momentum of a fluid is equal to the net force acting on the fluid. In the context of truck aerodynamics, momentum conservation is vital for understanding how the air particles interact with the truck's surface, creating the basic truck aerodynamics forces such as drag or lift.
By applying momentum conservation principles, design engineers can quantitatively assess truck aerodynamics and make informed decisions to optimize the vehicle's shape and features.
Fluid Dynamics. Conservation of Momentum
Energy conservation is another crucial principle in fluid dynamics. This principle states that the total energy of a fluid, which includes the sum of its kinetic energy, potential energy, and internal energy, remains constant - unless there is an external energy transfer.
Leveraging energy conservation principles allows truck designers to analyze the energy distribution in the flow field around the vehicle and identify areas where energy losses occur due to aerodynamic drag or other factors.
This knowledge can then be used to develop design modifications that minimize energy losses and improve fuel efficiency.
Aerodynamics: Introduction and Key Principles
Aerodynamics is a subset of fluid dynamics that focuses on the study of air or gas flow around solid objects. Key principles in truck aerodynamics include: airflow, drag, lift, and turbulence. Understanding these principles is crucial for truck designers aiming to optimize performance and fuel efficiency. More detail follows.
Airflow
Airflow refers to the movement of air over and around a truck. Truck aerodynamics involves analyzing how air particles interact with the truck's surface. Airflow can be characterized as laminar (smooth and predictable) or turbulent (chaotic and irregular). Achieving smooth and controlled airflow is essential for reducing drag and improving vehicle performance.
Drag & Lift
Drag is the resistance a truck experiences as it moves through the air. It is caused by the interaction between the truck's shape and the airflow. The two primary types of drag are pressure drag and friction drag. Pressure drag results from the air pressure difference around the front and rear surfaces of the truck, while friction drag is caused by the friction between the air and the truck's surface. Minimizing drag is crucial for optimizing fuel efficiency.
Lift is commonly associated with aircraft but also plays a role in truck aerodynamics. A lift is an upward force generated when airflow creates a pressure difference between an object's top and bottom surfaces. In truck design, minimizing lift is important to maintain stability and prevent issues such as reduced tire contact with the bottom road surface or instability at high speeds.
Turbulence
Turbulence is connected to airflow. Turbulence occurs when airflow in truck aerodynamics becomes chaotic and irregular. It can increase drag and negatively impact vehicle performance. Truck designers must aim to reduce turbulence by optimizing the vehicle's shape, managing airflow around the vehicle, and minimizing sharp edges or abrupt transitions.
Boundary Layer
The boundary layer is a subtle concept, but it is paramount for truck aerodynamics.
It refers to the thin layer of air that flows along the surface of an object.
It can be divided into two regions (see figure):
- laminar boundary layer
- turbulent boundary layer
Managing the boundary layer is crucial for reducing drag and optimizing aerodynamic performance.
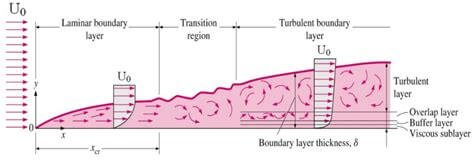
How Is Truck Aerodynamics Different from Car Aerodynamics?
Motorsport car aerodynamics, passenger car aerodynamics, and truck aerodynamics have different objectives and challenges, which lead to differences in design and optimization strategies. Let us analyze them in more detail.
Cars - Motorsport Car Aerodynamics
Motorsport (mainly Formula 1) car aerodynamics is about maximizing the car's performance and speed on the racetrack.
F1 Engineers focus on designing the car's body shape to generate maximum downforce and reduce aerodynamic drag. They investigate and optimize the shape of the car's front splitter, underbody, diffuser, and wings to generate downforce, which increases the car's grip and stability during high-speed cornering.
Engineers in motorsport also minimize drag by reducing the car's frontal area, smoothing the body surface, and designing efficient air ducts to cool the brakes and engine.
F1 aerodynamics simulation is highly focused on maximizing performance, and optimizing the body shape is critical to this process.
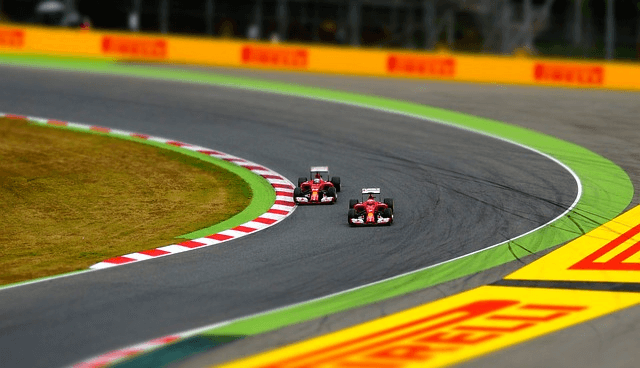
Cars - Passenger Car Aerodynamics
On the other hand, passenger car aerodynamics is focused on fuel economy, efficiency, comfort, and reducing wind noise.
The objective is to design a car with low drag and a high lift-to-drag ratio (L/D), which means the car requires less power to maintain a certain speed.
Automotive engineers investigate and optimize the car's body shape, wheel arches, roofline, and rear end design to reduce aerodynamic drag while also minimizing lift at high speeds to ensure the car remains stable thanks to downforce "pulling" the car to the ground.
Automotive engineers also look to design the car's shape to minimize wind noise (aeroacoustics) and create a comfortable cabin environment (HVAC management).
Passenger car aerodynamics is, thus, a balance between at least 3+1 factors:
- performance
- comfort
- fuel efficiency
The fourth influential factor is the appeal of the car's shape, i.e. the car style.
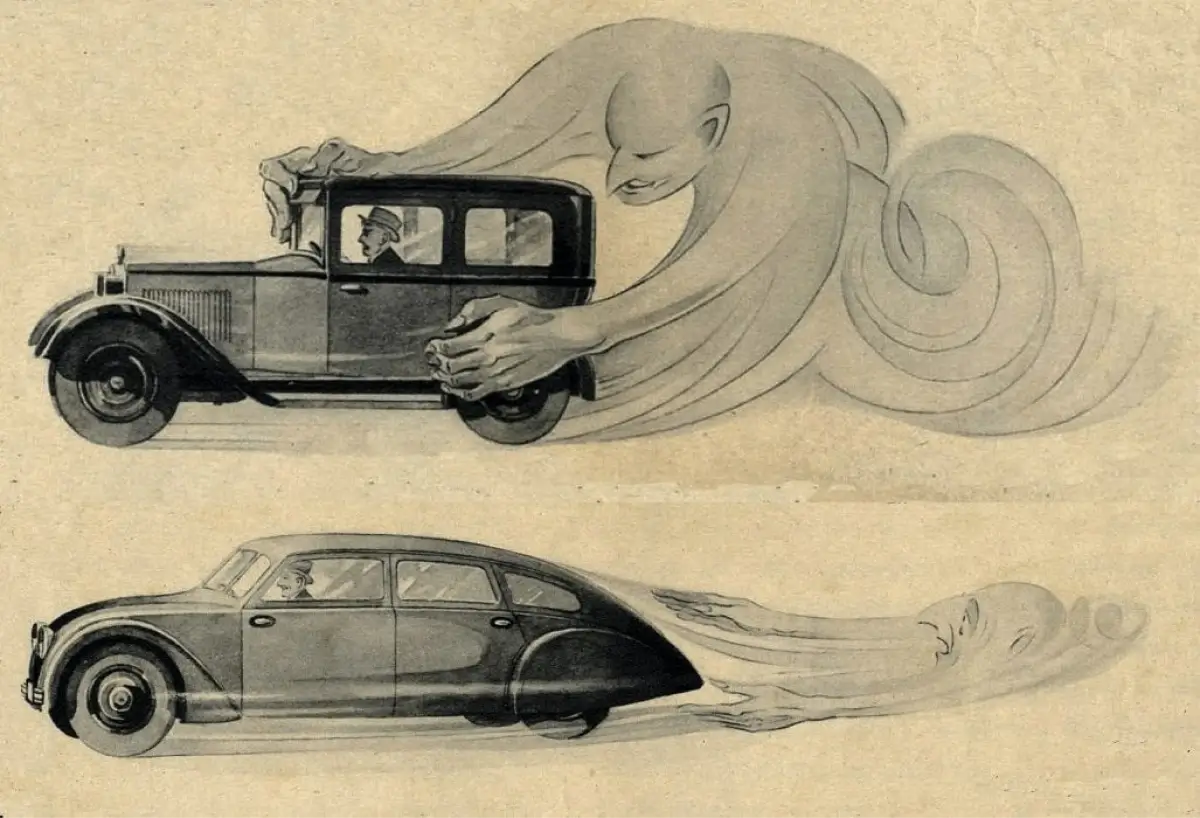
Truck Aerodynamics
Truck aerodynamics is focused on reducing drag, fuel consumption and improving truck stability on the highway.
Engineers design the truck's body shape to minimize aerodynamic drag and improve the L/D ratio, which results in a much more fuel-efficient truck.
They investigate and optimize the shape of the truck's front end, underbody, and trailer to reduce aerodynamic drag while minimizing crosswind sensitivity and improving stability.
They also look to design the truck's shape to reduce the impact of turbulence caused by passing vehicles.
The optimization of the truck's body shape and the design of efficient air management systems are critical components of improving the truck's fuel efficiency.
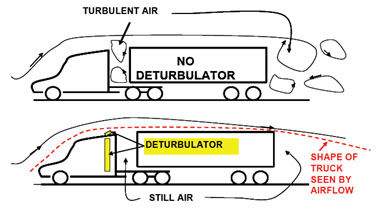
Aerodynamic Forces on a Truck
After clarifying the differences between trucks and other automotive aerodynamics, we will now analyze truck aerodynamics more closely and break down aerodynamics into a few main aspects.
Aerodynamic forces on a truck can indeed be broken down into two main categories — drag and lift forces:
Drag forces
They are the forces that oppose the direction of motion of the truck and are caused by the resistance of the air to the motion of the truck.
Lift forces
They are the forces that act perpendicular to the direction of motion of the truck and are caused by the pressure differences on the truck's surfaces.
Let us now explore aerodynamic forces in more detail!
Aerodynamic Drag Forces
The aerodynamic drag forces acting on a truck are primarily attributed to the pressure variations between the front and rear of the vehicle and the flow separation that occurs around its surfaces. These phenomena are crucial for optimizing truck design and improving fuel efficiency.
As a truck moves through the air, it experiences a phenomenon known as pressure distribution. The air is compressed at the front of the truck, resulting in a high-pressure zone. This compression is caused by air displacement as the truck moves forward.
The high-pressure zone gradually transitions to lower pressures as the air flows around the truck's sides and expands at the rear. This expansion generates a low-pressure zone behind the truck.
To analyze these pressure variations mathematically, we can consider Bernoulli's principle, which states that the total energy of a fluid flow remains constant along a streamline. Bernoulli's principle states that a fluid's total energy per unit mass remains constant along a streamline in an idealized, incompressible, and inviscid flow.
The equation combines, to represent the conservation of energy in the fluid flow, the following terms:
- a static pressure term (p),
- a kinetic energy term (½ ρ v²), also known as dynamic pressure,
- a potential energy term (ρ g h)
The sum of these terms remains constant along the streamline.
The meaning of the above-utilized symbols is:
- p represents the pressure of the fluid at a specific point in the flow. In the context of the equation, it refers to the pressure exerted by the air.
- ρ denotes the density of the fluid. The equation refers to the density of the air.
- v representing the velocity of the fluid at a specific point in the flow. This equation represents the velocity of the airflow.
- g denotes the acceleration due to gravity. It is a constant value and is typically equal to 9.81 m/s².
- h represents the height or elevation of the point in the flow above a reference level. In this equation, it represents the elevation at which the pressure is measured.
Therefore in the case of an incompressible, inviscid flow (i.e., neglecting friction and heat transfer effects), Bernoulli's equation can be expressed as static pressure + kinetic term + potential term = constant i.e.
p + ½ ρ v² + ρ g h = constant
The above equation can also be written simply as
p₀ + ρ g h = constant
where p₀ is the stagnation pressure, i.e. the sum of the static pressure p and dynamic pressure ½ ρ v².
Considering the truck's airflow, we can observe that the high-pressure zone at the front corresponds to a higher pressure value (p_front) compared to the lower pressure (p_rear) in the region behind the truck.
The pressure difference between these two zones generates a force that opposes the truck's motion, known as the aerodynamic drag force (F_drag).
This force can be mathematically expressed as:
F_drag = ½ ρ A C𝒹 v²
where
- ρ is the air density
- A represents the reference area of the truck
- C𝒹 denotes the aerodynamic drag coefficient
- v is the velocity of the truck relative to the air.
- The aerodynamic drag coefficient (C𝒹) accounts for the shape and surface properties of the truck and can be obtained experimentally or through CFD simulations.
Flow separation is another significant factor contributing to aerodynamic drag forces besides the pressure differences.
Flow separation occurs when the air separates from the truck's surfaces due to adverse pressure gradients caused by the shape of the truck. The adverse pressure gradient hinders the smooth flow of air, leading to separation and forming a turbulent wake behind the truck. This turbulent wake increases the aerodynamic drag force acting on the truck.
More complex equations and numerical methods are required to model and analyze flow separation. The Navier-Stokes equations, which describe the conservation of mass, momentum, and energy in a fluid flow, can be employed.
These equations can be solved numerically using CFD techniques to capture the intricate flow patterns and the separation regions around the truck.
Minimizing flow separation is crucial for optimizing truck design and reducing aerodynamic drag. Design modifications such as streamlined shapes, fairings, and strategically placed spoilers can help mitigate flow separation and decrease the resulting aerodynamic drag forces.
We have seen that aerodynamic drag forces acting on a truck are primarily caused by pressure differences between the front and rear of the vehicle and flow separation around its surfaces.
The pressure variation creates an aerodynamic drag force opposing the truck's motion, while flow separation contributes to increased aerodynamic drag reduction devices by creating a turbulent wake.
By utilizing mathematical principles, equations, and numerical simulations, engineers can analyze and optimize truck designs to minimize drag, enhance fuel efficiency, and improve overall performance.
Lift Forces
Truck aerodynamic lift forces are an essential aspect to consider in optimizing vehicle design and improving overall performance. Lift forces are generated due to pressure differences on the surfaces of the truck as it interacts with the airflow. The mechanisms behind lift forces are crucial for maintaining stability, reducing fuel consumption, and enhancing safety.
When a truck moves through the air, the airflow interacts with its surfaces, resulting in varying pressure distributions. The lift phenomenon can be attributed to the pressure difference between the upper and lower surfaces of the truck.
As the air flows over the surfaces, it tends to follow the shape's contour, creating a relatively low pressure on the upper surface and a relatively high pressure on the lower surface.
To analyze the lift forces mathematically, we can utilize Bernoulli's principle, which relates the pressure and velocity of a fluid flow.
In the context of truck aerodynamics, we observe that the airflow speed increases over the upper surface due to its curvature. According to Bernoulli's principle, this increase in airflow speed corresponds to a decrease in pressure.
Hence, the upper surface of the truck experiences relatively low pressure (p_upper) compared to the relatively high pressure (p_lower) on the lower surface.
The pressure difference between the upper and lower surfaces creates a force perpendicular to the direction of motion, known as the lift force (F_lift).
This lift force can be mathematically expressed as:
F_lift = ½ ρ A Cₗ v²
Here,
- ρ represents the air density;
- A denotes the reference area of the truck;
- Cₗ is the lift coefficient;
- v represents the velocity of the truck relative to the air.
The lift coefficient Cₗ accounts for the truck's shape, angle of attack, and other aerodynamic characteristics. Cₗ is typically determined experimentally, through advanced CFD simulations, or with data-driven simulation technology.
The lift coefficient is influenced by various factors, including the shape of the truck's surfaces, the angle of attack (the angle between the truck's reference line and the oncoming airflow), and the presence of aerodynamic devices such as spoilers or wings.
These factors affect the airflow patterns, pressure distributions, and, ultimately, the lift forces experienced by the truck.
Maintaining a balanced lift distribution across the truck is crucial for stability. Excessive lift on the truck's front or rear can lead to instability, causing the vehicle to exhibit unwanted pitching or rolling motions.
Thus, aerodynamic design optimizations aim to achieve a neutral or slightly negative lift distribution to enhance stability and improve road handling.
In the context of most commercial trucks, it is important to note that while lift forces may be desired in specific applications, such as high-performance racing vehicles or certain aerodynamic trailers, minimizing lift forces is a key objective.
Reducing lift forces helps enhance fuel efficiency by reducing the energy required to overcome lift-induced drag.
Various design strategies can be employed to mitigate lift forces, such as optimizing the shape and contour of the truck, adding fairings or skirts to minimize airflow separation, and implementing devices like spoilers or vortex generators to control the airflow and pressure distributions.
Re-capping: lift forces on a truck are generated due to pressure differences on the upper and lower surfaces of the vehicle. The pressure variation creates a lift force perpendicular to the direction of motion, influencing the stability and overall performance of the truck.
Utilizing mathematical equations and employing aerodynamic design strategies, engineers can optimize truck designs to minimize lift forces, reduce drag, enhance stability, improve fuel efficiency, and ensure safe and efficient transportation.
A Case History of Truck Instability
In this fictional case, alas, based on assembling real facts, a truck carrying a heavy load became involved in a tragic accident due to poor truck stability caused by inadequate aerodynamic design.
"On a particularly windy day, the truck encounters a sudden instability that leads to the loss of control and a catastrophic outcome. Investigations into the accident reveal several factors that contributed to the poor truck stability:
- High Center of Gravity: The truck's cargo was improperly loaded and distributed, resulting in a high center of gravity. This imbalance made the truck more susceptible to lateral forces, such as crosswinds, increasing the risk of instability.
- Insufficient Aerodynamic Features: The truck's design lacks proper aerodynamic features to mitigate the effects of crosswinds. With large, flat surfaces and inadequate shaping of the truck body, wind resistance is increased, amplifying the instability caused by the high center of gravity.
- Lack of Stability Control Systems: The truck lacks advanced stability control systems, such as electronic stability control (ESC). These systems use sensors and algorithms to detect and correct instability by applying individual wheel braking or reducing engine power. In the fictional case, the absence of such systems exacerbates the truck's instability issue.
The consequences of this tragic accident are significant, resulting in loss of life, property damage, and disruptions to traffic."
This case history should be useful as a reminder of the importance of addressing aerodynamic deficiencies in aerodynamics truck design to ensure optimal stability and prevent similar accidents from occurring in real life.
While the case history is fictional, it is based on real-world considerations and highlights the importance of proper aerodynamics in truck design.
Manufacturers and designers can take proactive steps to optimize aerodynamics, improve load distribution, and implement advanced stability control systems by fully understanding the potential consequences of poor truck stability.
These measures can enhance truck stability, minimize the risk of accidents, and ensure safer transportation for all road users.
Relationship Between Fuel Consumption Reduction and Aerodynamic Drag Reduction in Trucks
The fuel consumption of a truck can be approximated using the following formula:
Fuel Consumption = Drag Force x Distance / Energy Content of Fuel
The drag force acting on a truck is directly proportional to the square of its velocity (v), the air density (ρ), and the reference area (A) of the truck. As we have seen before, this can be represented as F_drag = ½ ρ A C𝒹 v²
This formula shows that reducing the aerodynamic drag force C𝒹 acting on the truck leads to a corresponding reduction in fuel consumption. By decreasing the drag coefficient of drag C𝒹, truck manufacturers can significantly improve fuel efficiency.
This reduction in drag can be accomplished through various aerodynamic enhancements, such as optimized underbody panels, streamlined fairings, and improved trailer designs.
Studies have shown that even a modest reduction in aerodynamic drag can yield substantial fuel savings.
For example, a 10% reduction in drag coefficient can reduce fuel consumption by around 5% to 7%.
Similarly, a 20% reduction in drag coefficient can lead to fuel consumption reductions of approximately 10% to 14%.
These figures highlight the direct relationship between aerodynamic drag reduction and truck fuel consumption reduction.
Furthermore, it is important to note that the benefits of aerodynamic improvements are most pronounced at higher speeds. Trucks traveling at highway speeds experience more significant drag forces, making aerodynamic enhancements particularly impactful.
Therefore, designing trucks with streamlined shapes and optimizing their aerodynamics can result in substantial fuel savings during long-haul journeys.
In addition to fuel consumption reduction, aerodynamic drag reduction contributes to other operational advantages. Improved aerodynamics can enhance vehicle stability, reduce wind-induced vibrations, and improve handling characteristics, ensuring a safer and more comfortable driving experience.
These factors further emphasize the importance of prioritizing aerodynamic design in the trucking industry.
What Are the Factors that Influence Truck Aerodynamics?
We have seen the main aerodynamic forces on the truck - but where do they come from?
Several factors can influence the aerodynamic forces on a truck, including the truck's geometry, speed, and environmental conditions.
We will review them and conclude by linking aerodynamic forces with effects on the efficiency and stability of the vehicle.
Geometry and Aerodynamics
The shape and size of a truck play a crucial role in determining its aerodynamic forces, including drag. Streamlining the truck's design by minimizing sharp edges and incorporating aerodynamic features, such as fairings, can greatly enhance its aerodynamic performance.
The Role of Fairings in Aerodynamics
Fairings are external components or devices strategically added to the truck's structure to modify the airflow around the vehicle. Aerodynamic fairings are designed to reduce aerodynamic drag forces by optimizing flow patterns and minimizing turbulence.
One of the primary purposes of fairings is to mitigate the separation of airflow from the truck's surfaces. As a truck moves through the air, adverse pressure gradients caused by the vehicle's shape can lead to flow separation.
Flow separation occurs when the airflow detaches from the truck's surfaces, creating turbulent wake regions and increasing drag forces.
Fairings are strategically positioned to redirect the airflow and reduce the adverse pressure gradients. They work by altering the local flow conditions and promoting smoother airflow over critical regions of the truck, such as the trailer, cab, and sides.
By using wind resistance, minimizing flow separation, and reducing turbulence, fairings help to maintain attached airflow and minimize the formation of drag-inducing wake regions.
There are various types of fairings designed for different parts of the truck.
Types of Fairings
Trailer fairings are typically placed along the sides and rear of the trailer.
Side skirts, which extend from the bottom of the trailer to the ground, help streamline the airflow beneath the trailer, reducing the air that gets trapped in the space between the tractor and the trailer front wheels and reducing drag.
Rear fairings, also known as boat tails or rear boat tail panels or fairings elsewhere, are located at the back of the trailer and serve to reduce the size and turbulence of the wake generated by the trailer.
Cab fairings are another common type of fairing used in truck aerodynamics. They are often installed on the front of the truck's cab, and roof fairings are designed to optimize the airflow around the driver compartment.
Cab fairings help to reduce the pressure difference between the front and rear of the truck, minimizing aerodynamic drag. They are typically shaped to guide the airflow over the cab smoothly and seamlessly blend with the overall truck design.
The effectiveness of fairings in reducing drag forces and improving aerodynamic performance has been demonstrated through extensive research, wind tunnel testing, and computational simulations.
Engineers and designers strive to optimize fairing designs to achieve the greatest aerodynamic benefits and drag reduction while considering weight, structural integrity, and practicality.
It is important to note that fairings are most effective when integrated into a holistic aerodynamic design approach. Combining fairings with other aerodynamic enhancements, such as streamlined body shapes, optimized underbody panels, and optimized wheel covers, can yield even greater improvements in truck aerodynamics.
The Role of Deturbulators in Truck Aerodynamics
Deturbulators play a significant role in truck aerodynamics, aiding in managing boundary layer airflow and reducing drag forces. These small, protruding devices are strategically placed on the truck's surfaces to manipulate the airflow, promote better attachment, improve aerodynamics, and minimize flow separation.
The boundary layer refers to the thin layer of air that adheres to the truck's surface as it moves through the air. Within this layer, there is a gradual transition from the stationary air close to the surface (known as the laminar flow) to the faster-moving air in the outer layer (known as the turbulent flow).
Proper boundary layer management reduces aerodynamic drag and improves overall truck performance.
Deurbulators are designed to disrupt the smooth laminar flow and induce controlled turbulence in the boundary layer. By doing so, they delay the transition from laminar to turbulent flow, thus maintaining a thinner boundary layer and reducing the area of flow separation.
The controlled turbulence introduced by deturbulators promotes better airflow mixing, preventing the formation of larger turbulent regions that could lead to increased drag. This improved mixing helps to maintain the gap between the tractor and attached airflow, reducing the size and intensity of the separated flow regions behind the truck.
Deturbulators can take various forms, such as small fins, vortex generators, or rib-like structures. They are strategically positioned on specific truck surfaces, such as the truck and trailer sides, rear, or cab.
The number, size, and placement of deturbulators are determined through extensive research, computational simulations, and wind tunnel testing to optimize their effectiveness in managing the boundary layer and reducing drag.
Using deturbulators, engineers can tailor the airflow patterns around the truck to minimize drag forces and improve aerodynamic performance.
To achieve optimal results, deturbulators work in synergy with other aerodynamic enhancements, such as fairings, streamlined shapes, and optimized underbody panels.
Optimized Underbody Panels for Truck Aerodynamics
One area that plays a significant role in truck aerodynamics is the underbody. By employing optimized panels in the underbody, truck manufacturers can substantially improve efficiency and cost.
Panels are designed to streamline the flow of air underneath the truck, reducing aerodynamic drag and improving fuel efficiency. Traditional truck designs often neglected the underbody, resulting in a turbulent airflow that increased aerodynamic drag and fuel consumption.
However, recent advancements in aerodynamic research and technology have led to the development of optimized panels that greatly improve the aerodynamic performance of trucks.
One key aspect of optimized panels is their ability to manage airflow around the tires and wheels. Airflow disruptions in this region can create significant aerodynamic drag.
Manufacturers can redirect airflow smoothly around the tires by employing carefully designed panels, reducing aerodynamic drag and improving fuel efficiency. These panels often feature integrated fairings and deflectors that guide the air around the wheels, minimizing turbulence.
Another crucial component of optimized panels is the inclusion of aerodynamic skirts. These panels extend along the truck's sides, creating a continuous surface from the front bumper to the rear. The skirts prevent air from getting trapped in the wheel well area, reducing aerodynamic drag caused by air eddies.
Additionally, they minimize the airflow underneath the truck, preventing air from flowing into the open space between the wheels and the chassis. This reduction in aerodynamic drag can lead to substantial fuel savings, especially during highway driving, where trucks spend a significant amount of time.
Furthermore, optimized panels often incorporate rear fairings and diffusers. Rear fairings streamline the airflow around the back of the truck, reducing the aerodynamic drag caused by the wake turbulence.
Conversely, diffusers work to gradually slow down and disperse the airflow as it exits the vehicle. By carefully managing the airflow at the truck's rear, these features contribute to a more streamlined design, reducing fuel consumption and improving stability.
Regulatory and market requirements have driven the development and implementation of optimized underbody panel for trucks.
Governments worldwide are introducing stricter fuel efficiency standards and emissions regulations, prompting truck manufacturers to invest in aerodynamic improvements.
Additionally, trucking companies are realizing the economic benefits of improved fuel efficiency, as it directly translates to cost savings over the lifespan of their fleet.
Speed and Aerodynamics
The truck's speed can also impact its aerodynamic and pressure aerodynamic drag forces. As the speed of the truck increases, the drag force increases exponentially due to the increased air resistance. Lift forces can also increase with speed, especially if the truck's geometry is not optimized for high-speed aerodynamics.
Environmental Conditions and Aerodynamics
Environmental conditions, such as wind speed and direction, can also impact the aerodynamic forces on a truck.
Crosswinds can create additional drag and lift forces on the truck, while tailwinds can reduce the aerodynamic drag force.
Headwinds can increase the drag force and improve the engine's efficiency by reducing the relative velocity of the air passing over the truck.
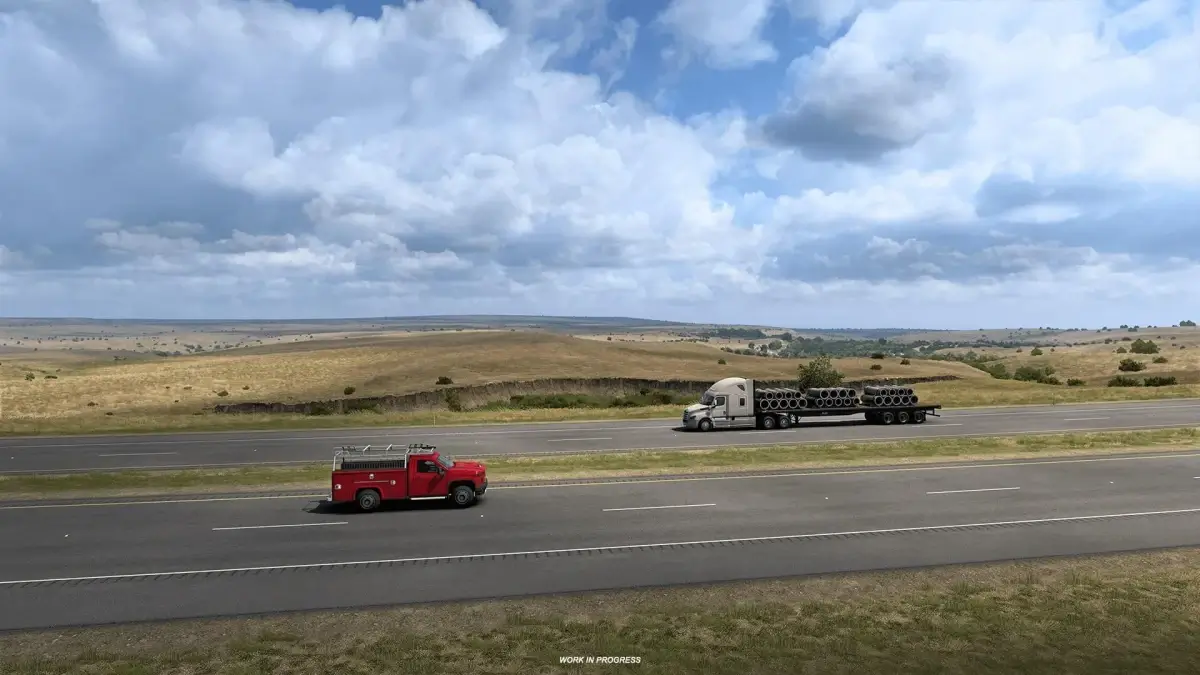
Why Truck Aerodynamics Is Important for Performance
The aerodynamic forces on a truck can significantly impact its performance, including its fuel efficiency, stability, and handling.
Fuel Efficiency
Aerodynamic drag forces are the primary factor that impacts a truck's fuel efficiency. Higher drag forces require more power from the engine to maintain the same speed, which leads to higher fuel consumption. Optimizing the truck aerodynamics can also improve fuel economy and efficiency and reduce operating costs.
Truck Stability
The lift forces on a truck can also impact its stability. While per se it is difficult to imagine such a lift force making a truck "airborne", the lack of adherence combined with crosswinds can have devastating effects.
Crosswinds can create significant lateral forces on a truck, which can cause it to sway or even tip over if the forces exceed the truck's stability limits. Lift forces can exacerbate this effect by reducing the downward force on the truck's tires.
This reduction in downward force can lead to reduced traction and increased risk of skidding or sliding, especially on slippery roads.
To mitigate these effects, truck designers often incorporate aerodynamic features such as side skirts, which can reduce the airflow around the truck's sides and the lateral forces.
Additionally, some trucks have devices such as active yaw control or tractor-trailer sway control, which can help the tractor and the trailer driver maintain control in crosswind conditions.
EV Trucks & Aerodynamics: Differences with Respect to the Past
The emergence of electric vehicles (EVs) has revolutionized the transportation industry, and trucks are no exception.
As the shift towards electric trucking gains momentum, it is crucial to understand the differences in aerodynamics between EV trucks and their traditional counterparts.
Aerodynamic design plays a significant role in vehicle efficiency and range, and the unique characteristics of EVs necessitate specific considerations.
The EV Truck Front End
One of the key differences lies in the design of the vehicle's front end. In traditional trucks with internal combustion engines, the front grille serves as an intake for cooling air. However, in EV trucks, the absence of a large cooling radiator allows for a smoother and more streamlined front fascia.
EVs often feature closed grilles or minimal openings to reduce aerodynamic drag. This streamlined design improves efficiency by minimizing air resistance, allowing the truck to glide through the air with reduced energy consumption.
Battery Packs
Another aspect that sets EV trucks apart is the presence of battery packs. These battery packs are typically located in the underbody or chassis of the vehicle, leading to a lower center of gravity. While this design element enhances stability and handling, it also presents an opportunity to optimize aerodynamics.
By incorporating panels and fairings, EV truck manufacturers can effectively manage the airflow around the battery packs, reducing drag and further improving efficiency.
Charging Infrastructure
Moreover, EV trucks may have unique aerodynamic considerations related to their charging infrastructure. Some EV trucks are equipped with external charging connectors, which need to be carefully integrated into the overall vehicle design to minimize disruption to airflow.
Ensuring that the charging ports and connectors are streamlined and seamlessly integrated into the truck's body can help maintain optimal aerodynamics during charging and driving operations.
Braking System
Additionally, EV trucks often employ regenerative braking systems, which utilize the electric motor's resistance to slow down the vehicle and convert kinetic energy into electrical energy. This feature reduces wear on traditional brake systems and provides energy-saving benefits.
However, regenerative braking systems can introduce additional airflow patterns and considerations. Optimized aerodynamic design can help mitigate any disruptions caused by these systems, ensuring that the energy-saving benefits are maximized.
EV Trucks and New Design Tools
The advent of EV trucks also brings advancements in technology and simulation tools. With the aid of computational fluid dynamics (CFD) simulations, manufacturers can precisely analyze and optimize the aerodynamics of EV trucks during the design phase.
These simulations allow for comprehensive assessments of different components, such as body shape, side mirrors, and airflow around the battery packs.
The ability to virtually test and fine-tune the aerodynamic performance of EV trucks empowers manufacturers to achieve greater efficiency without relying solely on physical prototypes and real-world testing.
In the next section, we will have more to say about new design tools for truck aerodynamics designers.
Design - Tools Available for Truck Aero
Wind Tunnel Testing
Wind tunnels have been used for over a century and are still valuable tools for improving truck aerodynamics.
Wind tunnels provide a controlled environment where designers can measure aerodynamic performance accurately on prototypes before proceeding to production.
Wind tunnels use a model truck inside a chamber where the air is forced over the truck at high speeds.
The designers can measure the aerodynamic forces acting on the truck model and use the data to refine the design.
Wind tunnels are expensive to build and operate, but they provide accurate data that can help improve truck aerodynamics significantly.
As part of experimental facilities for vehicle development, climatic chambers. Climatic chambers are large, insulated rooms that can be heated, cooled, and humidified to simulate various environmental conditions.
CFD Simulation
Computational Fluid Dynamics (CFD) is a powerful numerical simulation technique used in engineering to study and analyze the complex behavior of fluid flow around various objects, such as trucks. It enables designers to evaluate and compare the aerodynamic performance of different truck designs without needing costly and time-consuming physical model testing.
CFD is a sophisticated simulation technique that leverages mathematical equations and numerical algorithms to analyze and optimize the aerodynamic performance of trucks.
By accurately modeling the airflow around a truck and considering various design iterations, CFD empowers designers to make informed decisions that enhance efficiency, reduce fuel consumption, and improve overall vehicle performance.
At its core, CFD relies on solving intricate mathematical equations known as the Navier-Stokes equations, which describe the conservation of mass, momentum, and energy in a fluid flow.
These equations govern fluid flow behavior and are supplemented by additional equations to model turbulence, heat transfer, and other relevant phenomena.
The fundamental equations of fluid flow in CFD are based on the principles of conservation, expressed mathematically as follows:
Conservation of mass: ∇ · ρu = 0
Conservation of momentum (Navier-Stokes equations): ρ (∂u/∂t + u · ∇u) = -∇p + ∇ · τ + ρ g
where
- ρ represents the density of the fluid,
- u is the velocity vector,
- t denotes time,
- p is pressure,
- τ represents the viscous stress tensor,
- and g denotes the gravitational acceleration vector.
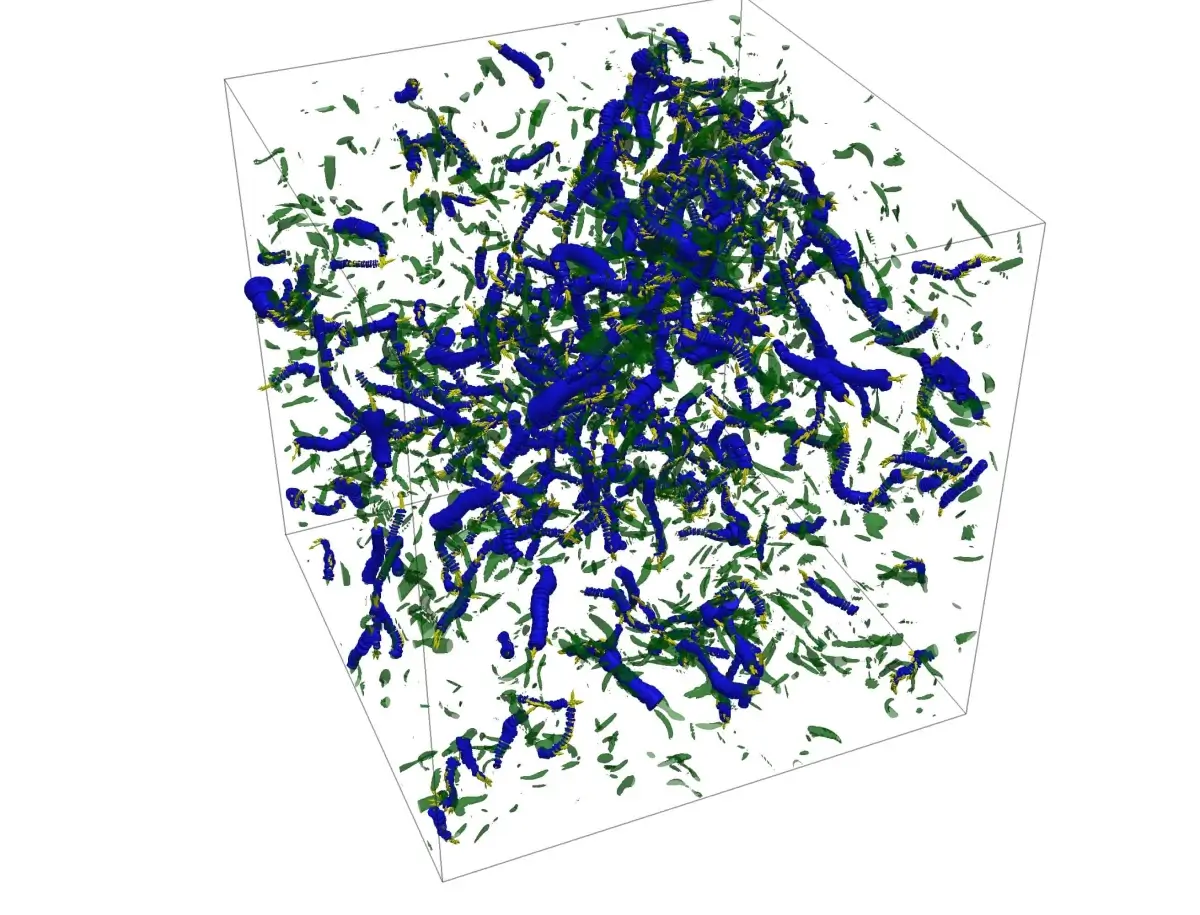
CFD software employs advanced numerical algorithms to solve these equations, such as finite difference, finite volume, or finite element methods. These algorithms discretize the continuous governing equations into a computational grid, dividing the computational domain surrounding the truck into numerous small control volumes or elements.
The CFD software approximates the fluid flow variables within each control volume, including velocity, pressure, and other properties. By applying numerical techniques, such as discretization and iterative solvers, the software computes the values of these variables at discrete points in space and time.
CFD software also incorporates boundary conditions to mimic the influence of the surrounding environment on the truck. These boundary conditions specify the inflow velocities, pressures, and temperatures, as well as the characteristics of the truck's surface, such as roughness or slip conditions.
Properly defining these boundary conditions is crucial for accurate simulations resembling real-world scenarios.
Once the computational grid and boundary conditions are set up, the CFD software solves the discretized equations iteratively, advancing the solution in time until it converges to a stable and realistic result.
This solution process involves the calculation of intermediate values, such as turbulent eddy viscosity or heat transfer coefficients, which further refine the accuracy of the simulation.
By simulating the airflow around a truck using CFD, designers can obtain valuable insights into the aerodynamic characteristics of different designs. They can analyze factors like aerodynamic drag, lift, and flow separation. Those factors significantly impact a truck's fuel efficiency, stability, and overall performance.
Advantages of CFD
Compared to traditional wind tunnel testing, CFD offers several advantages:
- First, it eliminates the need for physical prototypes, saving both time and resources.
- Second, it provides quick results, allowing designers to rapidly iterate and optimize their designs.
- Third, CFD simulations can capture intricate flow details that may be challenging to measure experimentally.
Turbulence Modelling in CFD for Truck Aerodynamics
The selection of the best turbulence model for truck aerodynamics depends on various factors, such as the flow conditions, the level of detail required, and the computational resources available. However, some commonly used turbulence models in truck CFD simulations are:
The k-epsilon Model
The k-epsilon model is a two-equation turbulence RANS (Reynolds-averaged Navier–Stokes) model widely used in CFD simulations. This model is relatively simple and computationally efficient, making it popular for simulating truck aerodynamics, maybe for entry-level or demo purposes
The k-omega Model
The k-omega model is a two-equation RANS turbulence model similar to the k-epsilon model. However, it performs better in regions of high shear and near-wall flows. This model is commonly used in truck CFD simulations and is more accurate than the k-epsilon model.
Detached Eddy Simulation (DES)
The Detached Eddy Simulation model is a hybrid turbulence model that combines the benefits of RANS and LES (Large-Eddy Simulation).
The DES strategy is the following:
- use the RANS model in the near-wall regions
- use LES in the outer regions
This model provides accurate flow field predictions for both attached and separated flows and is considered more accurate than the k-omega and k-epsilon models.
In conclusion, selecting the best turbulence model in CFD for truck aerodynamics depends on various factors, including the level of detail required, the computational resources available, and the flow conditions.
The k-epsilon, k-omega, and DES models are commonly used in truck CFD simulations, and each has its advantages and disadvantages regarding the accuracy and computational resources.
How to Improve Truck Aerodynamics and Fuel Efficiency: Platooning
As the demand for efficient and sustainable transportation continues to grow, the trucking industry constantly seeks innovative solutions to improve fuel efficiency and reduce carbon emissions.
One promising approach is truck platooning, which leverages advanced technology to optimize truck aerodynamics and enhance fuel efficiency.
This section explores the concept of truck platooning, its benefits, and how it can significantly improve both aerodynamics and fuel efficiency in the trucking industry.
Understanding Truck Platooning
Truck platooning involves the formation of a convoy of trucks, where a series of trucks follow closely behind a lead truck. Through advanced vehicle-to-vehicle (V2V) communication systems and automated driving technologies, the trucks maintain a short and consistent distance between each other, often referred to as "platoon gaps."
This synchronized movement allows the trucks to operate more efficiently as a unit, minimizing aerodynamic drag and optimizing fuel consumption.
Aerodynamic Benefits of Platooning
One of the primary advantages of truck platooning lies in its significant impact on aerodynamics. By driving close to one another, the trucks effectively reduce the drag caused by air resistance.
The lead truck creates a streamlined path for the following trucks, which experience reduced turbulence and air resistance due to the partial shielding provided by the lead vehicle. This streamlined airflow substantially reduces overall aerodynamic drag for the platoon, leading to improved fuel efficiency.
Fuel Efficiency Gains
Reducing aerodynamic drag through platooning can lead to substantial fuel efficiency gains for trucks.
Studies have shown that trucks driving in a platoon can achieve fuel savings of up to 10-15% for trailing vehicles.
The reduced drag allows the trucks to overcome less resistance, resulting in lower fuel consumption and decreased carbon emissions.
These fuel efficiency gains directly impact operational costs and contribute to a more sustainable and environmentally friendly trucking industry.
Safety and Automation
Truck platooning also offers additional benefits beyond aerodynamics and fuel efficiency. V2V communication and automated driving technologies enhance safety by reducing human error.
The close coordination between trucks within a platoon ensures synchronized braking and acceleration, minimizing the risk of accidents caused by delayed reactions or human-related factors. Moreover, automated systems can provide real-time updates on traffic conditions, optimizing route planning and reducing overall travel time.
Infrastructure and Policy Considerations
Appropriate infrastructure and supportive policies are essential to fully realizing the potential of truck platooning. Dedicated lanes with V2V communication systems and sensors can facilitate safe and efficient platooning operations.
Furthermore, regulatory frameworks must be established to address the associated legal and liability issues of platooning, ensuring that necessary safety standards are met.
Future Developments
Truck platooning is a rapidly evolving field, and ongoing research and development are exploring new possibilities for further optimization. Advancements in vehicle automation, connectivity, and sensor technologies continue to enhance the feasibility and efficiency of platooning systems.
Additionally, integrating platooning with other emerging technologies, such as electric and hybrid powertrains, can unlock even greater fuel efficiency gains and environmental benefits.
Aerodynamic Simulation Resources: Trucks Vs Cars
Truck aerodynamics simulations typically require larger computational domains and finer mesh resolutions than car aerodynamics simulations.
Trucks are generally larger and more intricate than cars, with bigger surface areas and complex geometries. Due to this complexity, accurately capturing the flow physics around a truck requires more mesh volume elements, especially in areas with high flow separation.
Creating a computational mesh of a truck for CFD simulations can be time-consuming, and once completed, managing the solver to obtain results in reasonable times (overnight) requires significant computational resources.
Typically, aerodynamic simulations run on tens or hundreds of processors in local facilities or the cloud.
Deep learning, a subset of Artificial Intelligence (AI) and Machine Learning, uses artificial neural networks to tackle these challenges in truck aerodynamics without explicitly being instructed on how to solve specific problems rather than learning from provided data.
Can we leverage AI to speed up design cycles?
Deep Learning for Truck Aerodynamics
Deep learning has become more popular in recent years due to advancements in computer technology and the availability of large datasets.
Deep learning algorithms can analyze large amounts of data and identify patterns that may not be apparent to human designers.
Therefore, deep learning can help truck manufacturers optimize the aerodynamic design of trucks and reduce fuel consumption and emissions.
As a part of the large amounts of data owned by truck manufacturers, CAD geometries and CFD simulations can be combined in a learning process to create truck aerodynamics AI predictions.
Deep learning algorithms require large datasets to train. Truck manufacturers should invest in mining their stored data to use this tool and empower all engineers without specialist CFD skills to speed up design cycles with real-time AI predictions.
Semi Truck Aerodynamics: Importance, Differences from Truck Aerodynamics
Semi-trucks, also known as tractor-trailers or 18-wheelers, play a major role in the transportation industry, hauling goods across long distances. Optimizing semi-trucks' aerodynamics is paramount, as it directly impacts fuel efficiency, stability, and overall performance.
This section explores the importance of semi-truck aerodynamics, highlighting the key differences from traditional truck aerodynamics and discussing the unique considerations and challenges involved.
Differences between Semi Truck Aerodynamics and Traditional Truck Aerodynamics:
- Trailer Considerations: One significant difference in semi-truck aerodynamics is the trailer's presence. The trailer's aerodynamics, shape, rear-end design, and the interaction between the truck and trailer must be carefully considered to optimize overall performance. The trailer's presence increases the aerodynamic interactions' complexity and requires specific design considerations.
- Streamlining the Gap: The gap between the truck and trailer, known as the "tractor-trailer gap," presents a unique challenge in semi-truck aerodynamics. Airflow separation and turbulence occur in this region, leading to increased drag. Innovative design solutions such as side fairings, gap reducers, and underbody panels can help reduce drag and improve aerodynamic performance.
- Length and Shape: Semi trucks are significantly longer than traditional trucks, which affects their aerodynamic characteristics. The elongated shape and increased frontal area require careful shaping and streamlining to minimize drag. Rounded edges, tapered surfaces, and optimized contours help to reduce aerodynamic resistance and improve overall efficiency.
- Weight Distribution: Semi trucks often carry varying loads, impacting aerodynamic performance. Uneven load distribution can lead to imbalances in aerodynamic forces and affect stability. Proper load distribution and management are essential to maintain optimal weight distribution and balance the semi truck aerodynamics.
Snow and Ice Accumulation and Shedding - The Role of Truck Aerodynamics
Winter conditions present unique challenges for trucking operations, particularly regarding snow and ice accumulation on the exterior surfaces of trucks. These accumulations can lead to increased weight, reduced visibility, and compromised aerodynamic performance.
This section explores the role of truck aerodynamics in managing snow and ice accumulation and shedding, highlighting the importance of effective design strategies to maintain safety and efficiency in cold weather conditions.
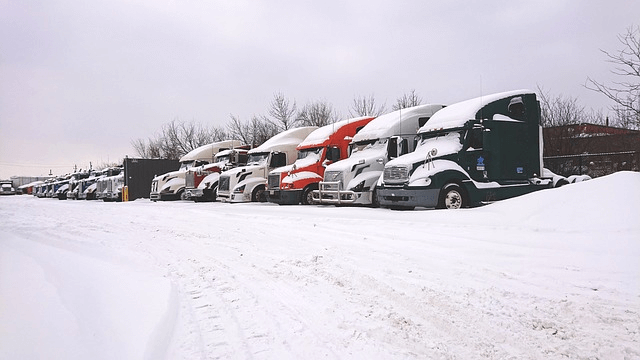
Snow and Ice Accumulation Challenges
Increased Weight: As snow and ice accumulate on a truck's surfaces, they add weight to the vehicle.
This additional weight can exceed the recommended limits, affecting fuel efficiency, braking distance, and overall handling.
Reduced Visibility: Snow and ice accumulation on windows, mirrors, and lights impair the driver's visibility, increasing the risk of accidents.
Limited visibility can hinder the driver's ability to anticipate and react to road conditions, obstacles, or other vehicles.
Aerodynamic Impact: Snow and ice formations disrupt the smooth air flow around the truck, creating drag and reducing aerodynamic efficiency.
This increases fuel consumption, making it costlier to operate the vehicle and decreasing overall fuel economy.
Role of Truck Aerodynamics
Streamlined Shapes
Aerodynamically optimized truck designs can help reduce snow and ice buildup. Smooth, rounded surfaces, tapered edges, and strategically placed airflow control devices minimize areas where snow and ice can accumulate.
Sloped Surfaces
In designing truck cabs and trailers, incorporating sloped surfaces helps reduce the likelihood of snow and ice sticking to the truck's exterior.
By minimizing flat areas, manufacturers can promote shedding and prevent excessive accumulation.
Active De-icing Systems
Some trucks employ active de-icing systems to mitigate snow and ice buildup. These systems use heating elements or fluid-based solutions to prevent or remove accumulations in critical areas such as mirrors, lights, and sensors.
Side Skirts and Underbody Panels
Installing side skirts and panels in the underbody improves trucks' aerodynamic performance while reducing snow and ice accumulation.
These devices create a smooth airflow pattern, minimizing drag and preventing snow and ice from being trapped in recessed areas.
Wiper Systems
Efficient wiper systems are essential for maintaining clear visibility during winter conditions. Advanced wiper technologies with multiple blades, heating elements, and high-speed capabilities can effectively remove snow and ice from windshields, mirrors, and headlights.
Bus Aerodynamics: Importance, Differences from Truck Aerodynamics, and Aerodynamic Devices
While much attention is given to the aerodynamics of trucks and passenger cars, the aerodynamics of buses is often overlooked.
However, bus aerodynamics play a crucial role in improving fuel efficiency, reducing emissions, enhancing stability, and improving passenger comfort.
This chapter explores the importance of bus aerodynamics, highlights the differences from truck aerodynamics, and discusses the aerodynamic devices specifically designed for buses.
Importance of Bus Aerodynamics
- Fuel Efficiency: Just like trucks, buses encounter aerodynamic drag that increases with speed. Improving bus aerodynamics can significantly reduce drag and improve fuel efficiency, resulting in cost savings and reduced carbon emissions.
- Emissions Reduction: By reducing drag, buses can achieve better fuel economy, leading to lower emissions of greenhouse gases and pollutants. This helps improve air quality and supports environmental sustainability.
- Stability and Safety: Aerodynamic enhancements can improve bus stability by reducing the effects of crosswinds and enhancing handling. This contributes to increased safety for both passengers and drivers, especially in adverse weather conditions.
Differences between Bus and Truck Aerodynamics
- Vehicle Shape: Buses typically have a box-like shape with more vertical surfaces than trucks, which often have streamlined shapes. The boxy design of buses presents unique aerodynamic challenges, as the flat front, large windows, and vertical sides create more drag.
- Size and Proportions: Buses are generally larger and taller than trucks, affecting the vehicle's airflow patterns. The increased size and height of buses result in different flow separation and pressure distribution, requiring specific aerodynamic solutions.
- Passenger Considerations: Buses are designed to carry passengers, which introduces additional factors in aerodynamic design. Large windows, doors, and passenger entry and exit areas require careful optimization to minimize drag while maintaining passenger comfort and convenience.
Aerodynamic Devices for Buses
- Front-End Design: Optimizing the front-end design of buses is crucial for reducing aerodynamic drag. Incorporating streamlined features such as sloped windshields, curved edges, and smooth transitions from the front to the sides can minimize air resistance.
- Roof Spoilers: Roof spoilers or air deflectors installed at the rear of the bus roof can help improve airflow by reducing the separation of the airflow and minimizing drag.
- Wheel Covers: Installing wheel covers on bus wheels can help streamline the airflow around the tires, reducing turbulence and drag. This simple aerodynamic device can contribute to improved fuel efficiency.
- Side Skirts: Side skirts are panels that cover the space between the wheels on the side of the bus. They help smoothen the airflow along the sides, reducing the drag caused by the exposed wheel wells.
- Rear Diffusers: Rear diffusers are devices installed at the rear of the bus, designed to manage the airflow and reduce turbulence as the bus moves. They help minimize the low-pressure zone behind the vehicle, reducing drag.
Truck Aerodynamics: A Case History - The Volvo FH16
The optimization of truck aerodynamics is a key area of focus for manufacturers aiming to enhance fuel efficiency and reduce carbon emissions. One remarkable case in truck aerodynamics improvement is the Volvo FH16, a flagship heavy-duty truck known for its power and performance.
Background and Challenges
The Volvo FH16 was already renowned for its reliability and long-haul capabilities. However, Volvo Trucks recognized the potential for further advancements in aerodynamic design to increase efficiency and reduce fuel consumption.
The main challenge is optimizing the truck's aerodynamics without compromising its durability and robustness.
Specific Improvements on the Volvo FH16
The following are some specific improvements on the Volvo FH16.
Cab Roof Deflector:
One significant improvement on the FH16 is the addition of a cab roof deflector. This feature, located at the top rear end of the cabin, redirects airflow, reducing the drag caused by the cabin's square shape.
The deflector effectively guides the air over the truck and trailer itself, improving the overall aerodynamic performance of the truck.
Side Air Deflectors:
Volvo Trucks introduced side air deflectors on the FH16 to further optimize airflow. These deflectors are positioned on the sides of the cab and help guide the air smoothly along the truck's body.
By reducing turbulence and preventing air from getting trapped in the vehicle's wake, the side air deflectors minimize drag and improve overall aerodynamic efficiency.
Chassis Side Fairings:
Another key improvement implemented on the Volvo FH16 is the integration of chassis side fairings. These fairings cover the space between the wheels and the chassis, reducing the turbulence caused by air flowing through the wheel arches.
The side fairings significantly contribute to drag reduction and fuel efficiency improvements by streamlining the airflow around this area.
Trailer Aerodynamics:
Volvo Trucks also recognizes the importance of trailer design in overall truck efficiency. To complement the aerodynamic enhancements on the truck itself, Volvo Trucks offers trailer aerodynamic options that can be combined with the FH16.
These options include trailer side skirts and rear diffusers, improving airflow management and reducing drag on the truck-trailer combination.
Results and Impact:
The aerodynamic improvements implemented on the Volvo FH16 have yielded impressive results regarding fuel efficiency and overall performance. Fuel consumption has been significantly reduced by reducing drag and optimizing airflow compared to previous models.
These improvements translate into cost savings for truck operators and contribute to a more sustainable transportation industry by reducing carbon emissions.
Conclusion
The truck industry is currently facing major challenges, especially when it comes to managing fuel expenses and keeping trucks on the road. To tackle these issues, truck companies are now prioritizing the improvement of their fleets' efficiency. They are exploring innovative solutions, such as enhancing truck aerodynamics and incorporating new products and devices to minimize losses. As part of these efforts, engineers are utilizing both CFD and deep learning prediction to develop effective aerodynamic solutions.