Topology Optimization VS Generative Design
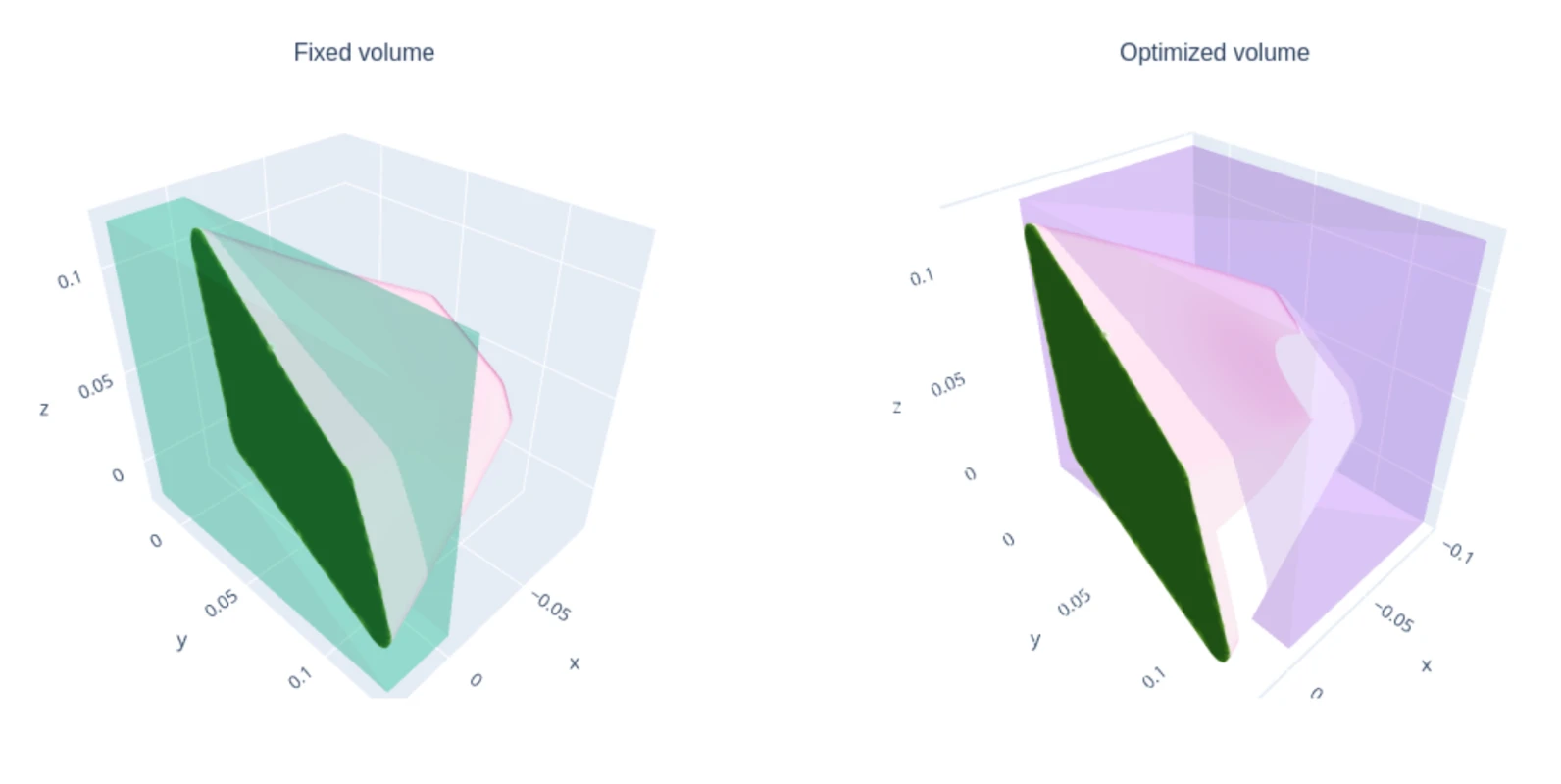
New counterintuitive designs with unprecedented performance and weight reductions have been seen in the last few years. How were they made? Generative Design and Topology Optimization, coupled with Additive Manufacturing, are key technologies behind it. However, there is confusion about which of the two approaches, topology optimization or generative design, is most desirable.
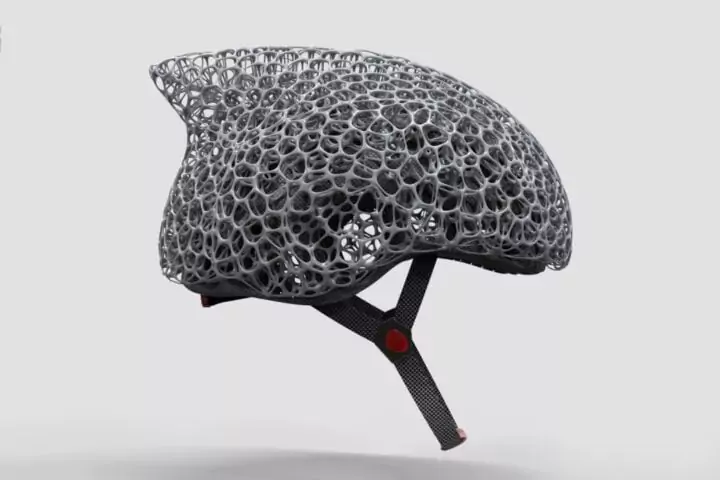
The main difference between topology optimization and generative design is the following:
- Topology optimization occurs in mature design phases, where an initial geometry is already set. Therefore topology optimization, while creating new shapes, chisels a more controlled design space.
- Generative is used in the design's starting phase, giving engineers valuable feedback for initial design possibilities. Therefore generative design can see a much wider and more innovative design space.
We will show, with use cases, how generative design can provide the most innovative solutions when coupled with AI tools such as NCShape for shape modifications and to check engineering performances.
Topology Optimization vs Generative Design — Which Way?
When engineers look for solutions to optimize product shapes with reduced weight and cost and improved functional performance, a question usually arises. Should I go for topology optimization or generative design?
The following examples from 2D and 3D optimization show how dramatically shapes can be changed by algorithms.

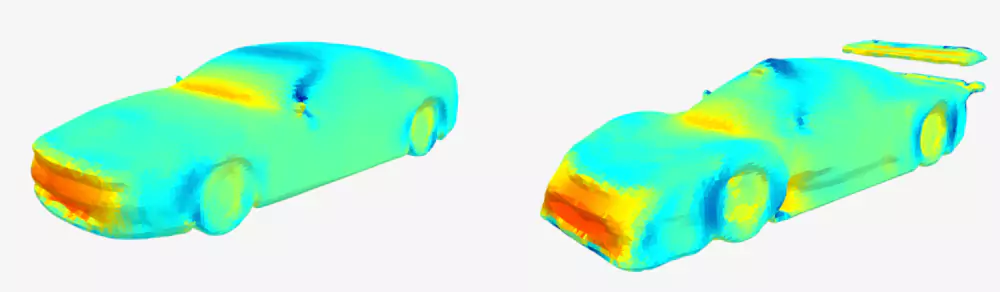
Topology Optimization
Topology optimization is applied to get optimum material distribution for a design under conditions of functionality or "constraints". The topology optimization algorithm reduces the material on a given object, allowing it to remain roughly the same shape and function as originally intended.
Topology optimization begins with a human-designed model (subject to human bias) with a baseline geometry. The process leads to an optimal design ("topology optimized") that will satisfy factors such as weight and structural integrity.
Rather than explore multiple design alternatives and get several optimized designs, the output of topology optimization will be one concept. Starting with a fully defined CAD model, in topology optimization, the user will define a design space where the topology optimization software can whittle off virtual material, subject to loads and physical and manufacturing constraints.
Example of Topology Optimization Implementation
In topology optimization, within the initial design of a mechanical part, after having assigned the geometrical region subject to optimization, the physical and manufacturing constraints must be optimized in terms of a topology optimization objective such as minimum strain energy, also known as "compliance".
The geometry is converted into a mesh so that the geometry can be coupled to CAE (computer-aided engineering) software such as finite element analysis that will, for example, compute stress levels and other functional requirements on the mesh model.
Differences Between Topology Optimization and Generative Design
In summary, Topology optimization targets convergence on a single geometry to optimize parameters such as the weight of a solid object or the pressure loss of a fluid component, starting from a baseline concept.
The generative design process considers multiple alternatives and makes them converge on a solution based on functional requirements from engineering and other requirements. It is better suited for additive manufacturing methods.
What Are the Aims of Generative Design?
We will show how generative designs can generate data-driven design solutions for projects that meet specific goals and constraints. The generative design technology will make engineers and designers more confident about their designs and better predict the design outcome.
The generative design process for a component starts with the mating criteria with the rest of the design and what parts of the design space are available after considering constraints based on geometrical obstacles and other features like holes for fastening.
Especially with lightweight designs based on lattice structures, the automated generative design ideation can produce a geometry valid also for structural integrity. This can be checked with finite element analysis.
Impact of Generative Design
Generative design enhanced by AI neural methods can span the space of all possible design solutions given the manufacturing method constraints and material layout and give a final shape designed without the bias of the human element but at the same time with a realistic consideration of the manufacturing process.
What Is the Role of AI in Generative Design?
How can we utilize artificial intelligence? How can data-driven design alternatives find optimized concepts?
CAD vendors are talking about AI, but it is necessary to link CAD data inputs with simulation data - we will show how with some use cases.
We will show how Artificial Intelligence can identify improved design outcomes and help make data-driven decisions.
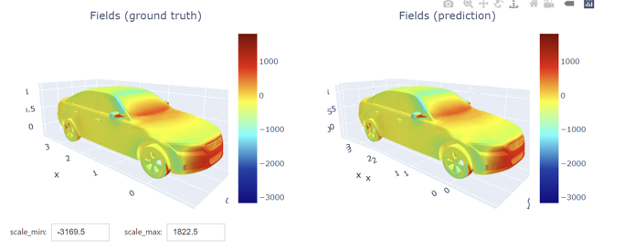
Artificial Intelligence and Generative Design: The Origins
In a pioneering research work in 2018, the founders of Neural Concept found that "Once trained, the AI can be used as a surrogate model or proxy to evaluate the effectiveness of a particular design. Not only is it fast, but it is also differentiable concerning the X coordinates that control the shape. We can therefore use a gradient-based technique to maximize the desirable property while enforcing design constraints, such as the fact that a bicycle shell must be wide enough to accommodate the rider, a car must contain a pre-defined volume for the engine and passengers, or a plane wing should be thick enough to have the required structural rigidity."
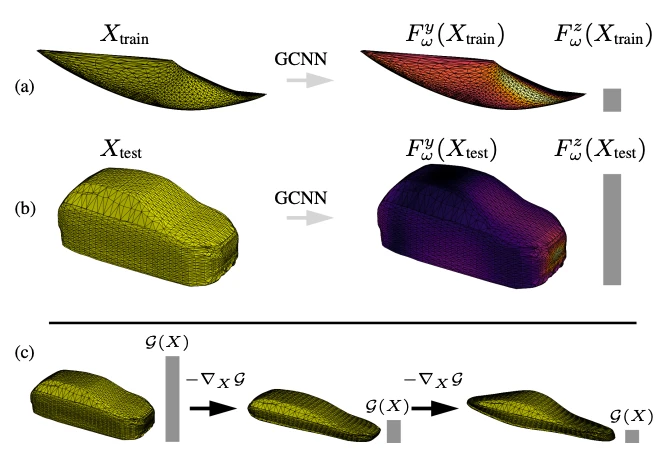
From this activity, Neural Concept was born as a start-up and became a provider of AI software tools for designers.
Interactive engineering simulation and optimization are made possible by exploiting the power of data. Predictive AI models generate physical simulations using a raw CAD model as the sole input. AI can learn from the data that engineers produce daily. These predictive models simplify processes and emulate simulation engineers’ expertise by transferring them to design engineers or generative design algorithms early in product development. The AI process makes it possible to reduce the number of iterations between teams and optimize designs.
Technical Background
Optimization is a fundamental process in many scientific and engineering applications. Optimizing a function comprises searching its domain for an input that results in the minimum or maximum value of the given objective. If we have access to an analytical expression of the objective function, the answer to the optimization problem might be straightforward. Even when it is infeasible to obtain the analytical solution directly, a gradient-based method combined with a heuristic search will bring satisfaction in most cases.
But what if we don’t have direct access to the objective function or the gradients? In many engineering applications, the form of the objective function can be very complex and intractable to analyze. Its evaluation might be computationally very expensive.
In such cases, we usually refer to the objective function as a black-box function that, when given queries for some input locations, can answer back with the true objective value we are interested in. But in engineering design problems, querying the function can be very expensive. Function evaluation time can be from minutes to hours to even days.
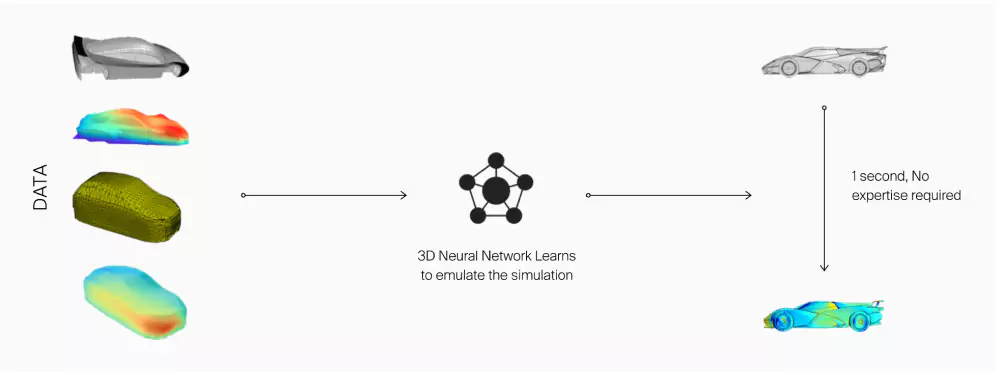
Neural Concept Shape approach (see figure) provides real-time surrogates that help generate evaluation-based designs within seconds, by extracting historical data and processing them with Deep Learning.
Use Case: Optimized Heat Exchanger
We will briefly outline a generative design application from Neural Concept and PhysicsX (UK). The objective was to optimize heat exchanger performance from the thermal exchange and fluid mechanical (local losses) point of view.
There is a wide range of acceptable designs for heat exchangers, and the number of parameters describing the heat exchanger geometry can quickly rise as the generative design becomes more and more complex. Since the corresponding numerical simulation is computationally costly, the design engineer can only afford to iterate on a few design parameters to try and improve the system.
PhysicsX collaborated with the Neural Concept team to build a reliable surrogate model to predict the performance of various heat exchanger designs with different topologies in real-time.

The AI model from Neural Concept can accurately predict the system's overall efficiency, temperature, and pressure drop at the outlets. The engineer can now interact in real time with the heat exchanger designs to iterate efficiently between different geometries and topologies.
Moreover, the AI model also predicts the flow within the volume, providing engineers with a better intuitive understanding of the phenomenon.

On top of the AI predictive model, the optimization algorithm library of Neural Concept was used, bringing substantial improvements to the final design obtained with morphing techniques.
Use Case: Optimized Rear Mirror
We will briefly outline a generative design application from Neural Concept and CAD-IT in South Korea. AI, CAD and CAE were used in a generative design software approach.
The objective was the generative design of a side mirror in a car to optimize its aerodynamic performance. CAD and simulation data were created in a previous phase of an automotive project.
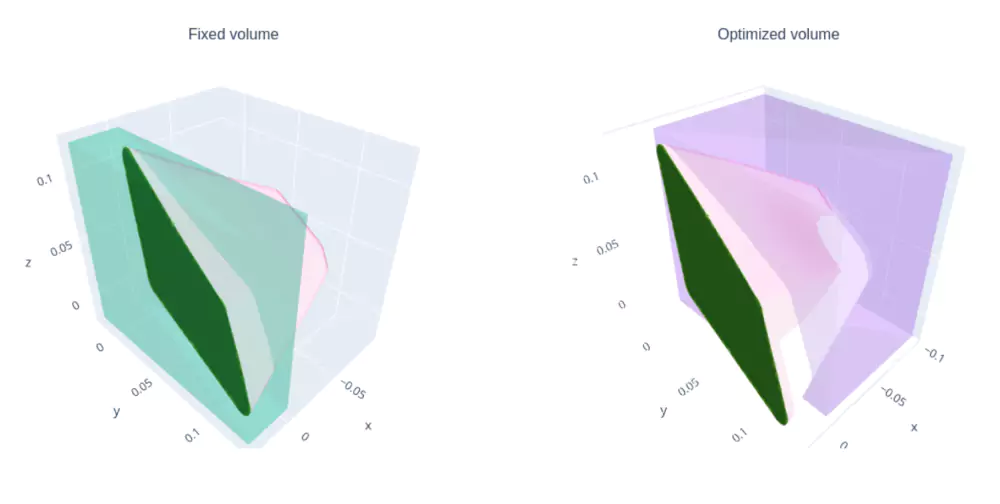
With free morphing by Neural Concept, NCShape's optimization algorithm was freed from the design constraints in the initial data; this made it possible to explore new, disruptive design spaces, in a matter of a few minutes, without the need to launch any extra aerodynamic stimulation.
How can AI "find" the optimal aerodynamic solution and produce a generative design proposal? A genetic algorithm was integrated with the aerodynamic prediction to obtain the final objectives: the drag and lift forces (see figure).
Most real-world optimization applications are formulated as multi-objective optimization problems where we seek to optimize simultaneously for multiple criteria and consider the constraints. Here, instead of finding an ultimate optimum, the goal is to recover the Pareto front of these different objectives.
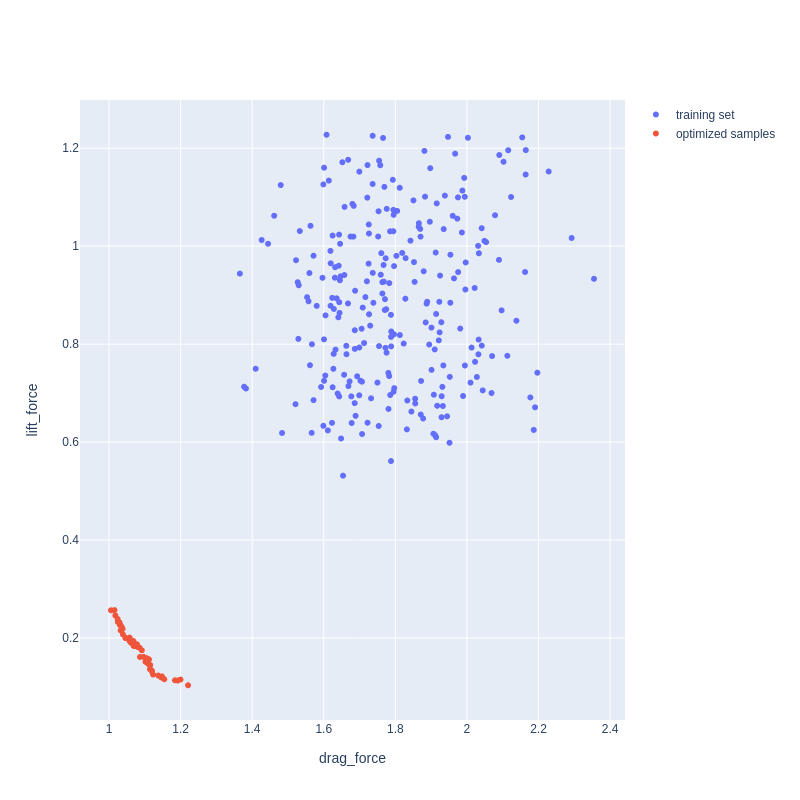
Conclusions
AI, not human operators, drove the topological concepts used for evaluation in the shown generative design examples.
Most generative design tools can, at most, consider finite element analysis; here, the more sophisticated computational fluid dynamics method was also used.
The generative design process can start from any other CAD data, and the CAD data output is checked with simulation data helping informed decisions faster.