Smarter Satellite Design for Thermal Constraints (Whitepaper)
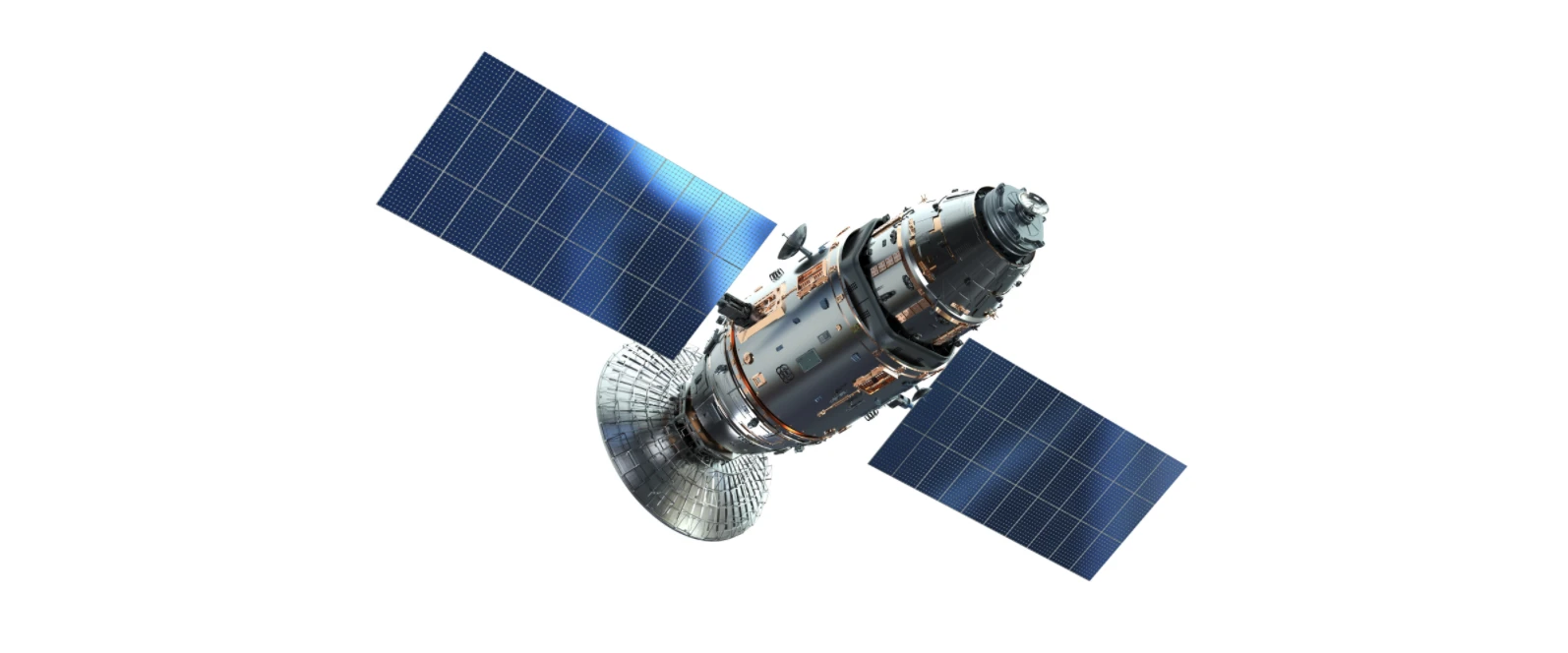
Thermal modeling on satellites panels: 3D Deep Learning on different topologies
Neural Concept (NC)
1 Introduction
In 2020, launching a 5 kg satellite costs approximately 250’000$, hence motivating active R&D in weight reduction and design optimization. Since satellites are subject to very strong and complex thermal exchanges the placement of electronic components and the efficient design of the cooling system is essential in this task.
Neural Concept Shape (NCS) brings a solution that could radically change the way satellite panels are designed by letting the engineer explore, in real time and free from any constraints, the infinite number of possible configurations. In this document, we report the performances of NCS on the problem of thermal simulations for satellite panel and we briefly discuss the potential impact of this new software on the design workflow.
2 Method Overview
2.1 Approximate Simulation using Neural Concept Shape
Numerical simulations have become of primary importance for the industry over the last decades. Nevertheless, since a simulation must be re-run each time an engineer wishes to change the shape which is being designed, it makes the exploration process slow and costly. A typical approach is therefore to test only a few designs without a fine-grained search in the space of potential variations. This is a severe limitation and there have been many attempts at overcoming it, but none has been entirely successful yet. A classical approach to reduce the computational complexity is to use Reduced Order Modeling software (ROM) or surrogate modelling via Gaussian Process (GP) regressors, trained to interpolate the performance landscape given a low dimensional parametrization of the shape space. This interpolator is then used as a proxy for the true objective to speed-up the computation. However, those regressors are only effective for shape deformations that can be parameterized using relatively few and pre-defined parameters. Therefore, the regressors are specific to a particular parameterization, which introduces a burden into the design experience. Furthermore, the topology of the designs that are used cannot vary for one example to another, which is a very severe limitation.
A recently developed software, Neural Concept Shape (NCS), empowers the engineer with a new tool, Geometric Convolutional Neural Networks, to build surrogate models of numerical solvers. It suffers from none of the drawbacks of previous surrogate or ROM methods. It is agnostic to the shape parameters as it processes directly the mesh representation of the design. Unlike other software, the engineer does not have to choose and stick to a specific parametrization from the beginning to the end of experiments and hence the predictions can be directly integrated into the normal workflow (CAD - Simulations) of the engineer. Ultimately, we will see in this report, that NCS is extremely efficient when the quantities of interest are defined as fields on the surface of a complex object with varying topologies. This is something that none of the other available solutions can handle.
To date, NCS is the only CAE-oriented Deep-Learning software that is able to process industrial scale raw unstructured, complex 3D data directly, without any preprocessing. It uses multi-scale geometric neural networks, through a combination of surface — such as geodesic — and Euclidean network architectures. It is able to learn to emulate simulators and reproduce multiple outputs such as integrated scalar values — e.g. drag forces or energy consumption — or surface and volumetric field values — e.g. pressure or temperature —.
2.2 Goals
The goal of this project was to build a NCS-based approximate simulator for thermal transfer simulations within a satellite panel. A traditional simulation simulation takes about 20 minutes to run, while we expect NCS to provide a result in a few tens of milliseconds. We will analyze in more depth the accuracy and speed of NCS to emulate the simulations despite of varying topological changes.
In this report, we evaluate the performances of Neural Concept Shape for this task and assess the feasibility of the use of NCS as a substitute to the full simulation in production cases. We also test the ability of the software to handle different topologies within a single database.
2.3 Generation of the CAD Designs
OnShape, a CAD software hosted on the cloud was used to design the satellite panel. The geometries were generated by varying up to 27 different variables, and an example is shown below:
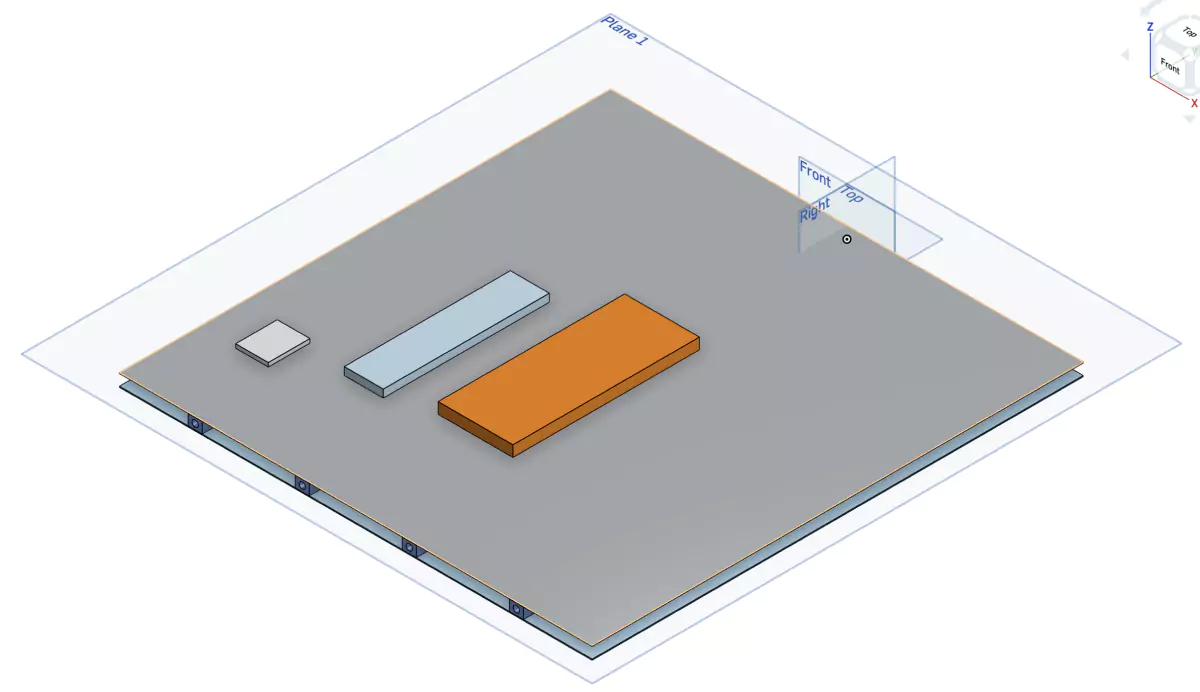
For each geometry, the 27 parameters were chosen randomly within a given range, making each sample unique and ensuring a good diversity in the geometries. The 27 parameters correspond to the size of the panel, its thickness, the location of the boxes, their respective dimensions in the 3 dimensions, pipes geometry and their number... The topology of the overall geometry was able to change because the number of boxes could vary between 1 and 3, and the number of pipes could change as well (between 2 and 8).
This parametric space allows to perform very fine design variations on the panel, and ultimately to assess the influence of each of these parameters on the thermal behavior of the geometry. To generate the training dataset, the geometries generation was automated by using the OnShape API. We defined lower and higher values for each of the parameters, and a random value was chosen at each iteration for the parameters. We were able to build a database of 1’000 geometries using this method, ensuring that each sample was unique.
2.4 Numerical Simulation with ESATAN-TMS
Agency (ESA) used ESATAN-TMS to perform the numerical simulations. ESATAN-TMS is a software for thermal modeling simulations, developed and used by ESA. In this thermal simulation, the boxes at the top of the panel represent electronic modules components that are used for the mission of the satellite. Each box of components is generating heat, with a given heat flux and he heat is then dissipated through the geometry via thermal conduction within the pipes.
2.5 Configuration of NCS
Note that the network is unaware of the underlying parametrization and shapes created with other parametrizations can easily be predicted or added to the dataset. Only the similarity to the shape present on the training set will have an effect on the accuracy. The part using convolution on the shape is illustrated in 3. The first part of the model pre-processes the input and constructs a set of features by means of the previously introduced geodesic convolution operations. These features are then used to predict the global scalars via average pooling and two dense layers. The second branch of the network generates pressure fields relying on an additional set of geodesic convolutions and point-wise operations. The new network takes advantage of a GPU efficient implementation of geodesic convolutions.
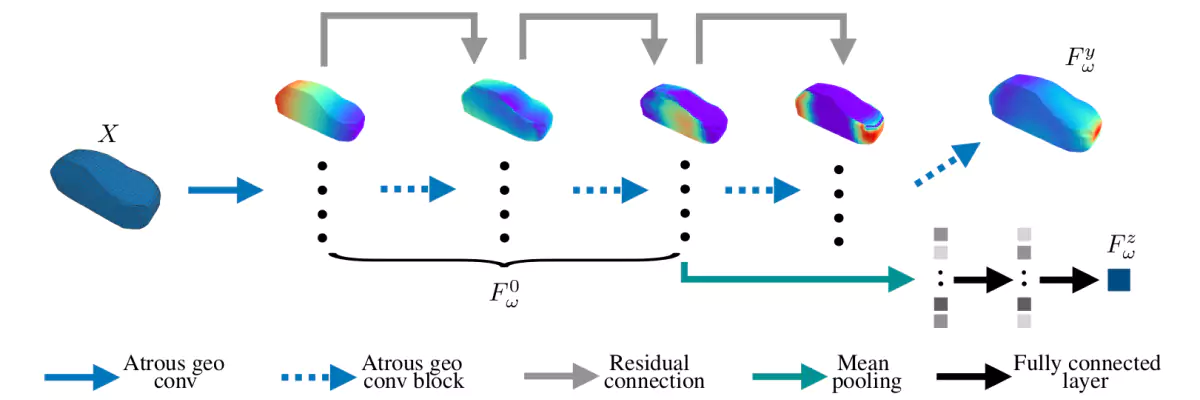
3 Results
The following metrics were computed to assess the accuracy on the test 1 set:

The distribution of the error is shown below (choosing L1 relative as the reference metric). We can see that most of the samples exhibit a L1 relative error between 0.5% and 1.5%. As expected, the performances are better on the training set.
3.1 Predictions
3.1 Predictions Overall, the network is able to successfully assign the corresponding heat flux to each component and propagate it within the panel. It is also able to detect the thermal conduction through the pipes (as the number of pipes is varying). Let us compare visually a prediction made by the neural network and the ground truth (the simulation made by ESATAN-TMS). Here, a test sample with a standard performance (L1 relative error = 1.12%) is shown with figure 5:
1A default model from Neural Concept was used for this project. Hyper-parameters were tuned on previous dataset and based on Neural Concept’s experience, but not specifically for this use-case.
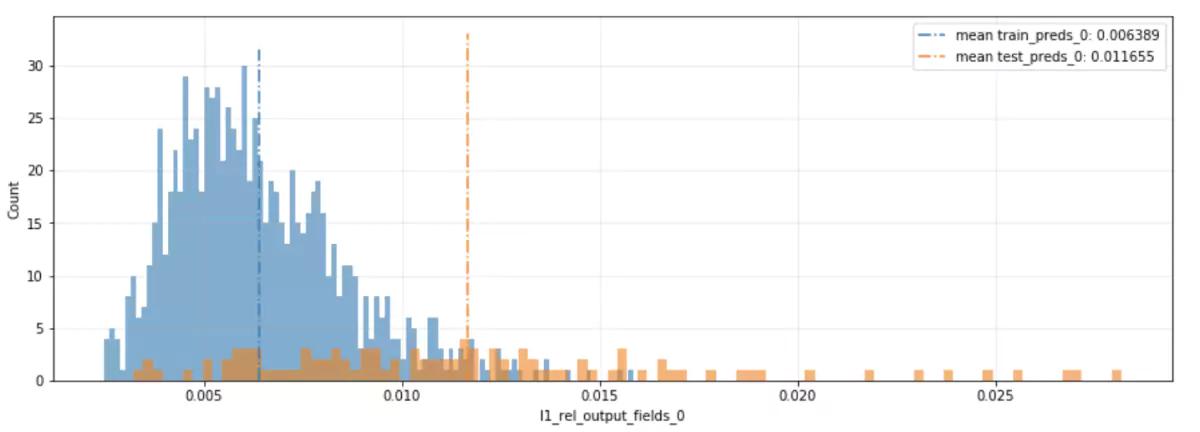
3.2 Influence of the dataset size
Varying numbers of training samples were used to assess the robustness of the neural network with the training dataset size. The results shown here were obtained with 900 training samples. However, we note that very similar performances are achieved with only 750 or 500 training samples, as shown in the following tables and the corresponding visualizations in figures 6, 7, 8 and 9, in the Appendix A 2.


Using 200 samples, the neural network is over-fitting during the training process and the performances drop slightly, but remain acceptable, with a L1 relative error reaching 1.56% and a R2 score of 0.880 of the test set. The neural network does not generalize as well as for the other splits described above.
The samples visualized here were chosen randomly from the test set, and exhibit a standard performance with respect to the rest of the dataset. Feel free to reach out to Neural Concept to discuss further theses results.
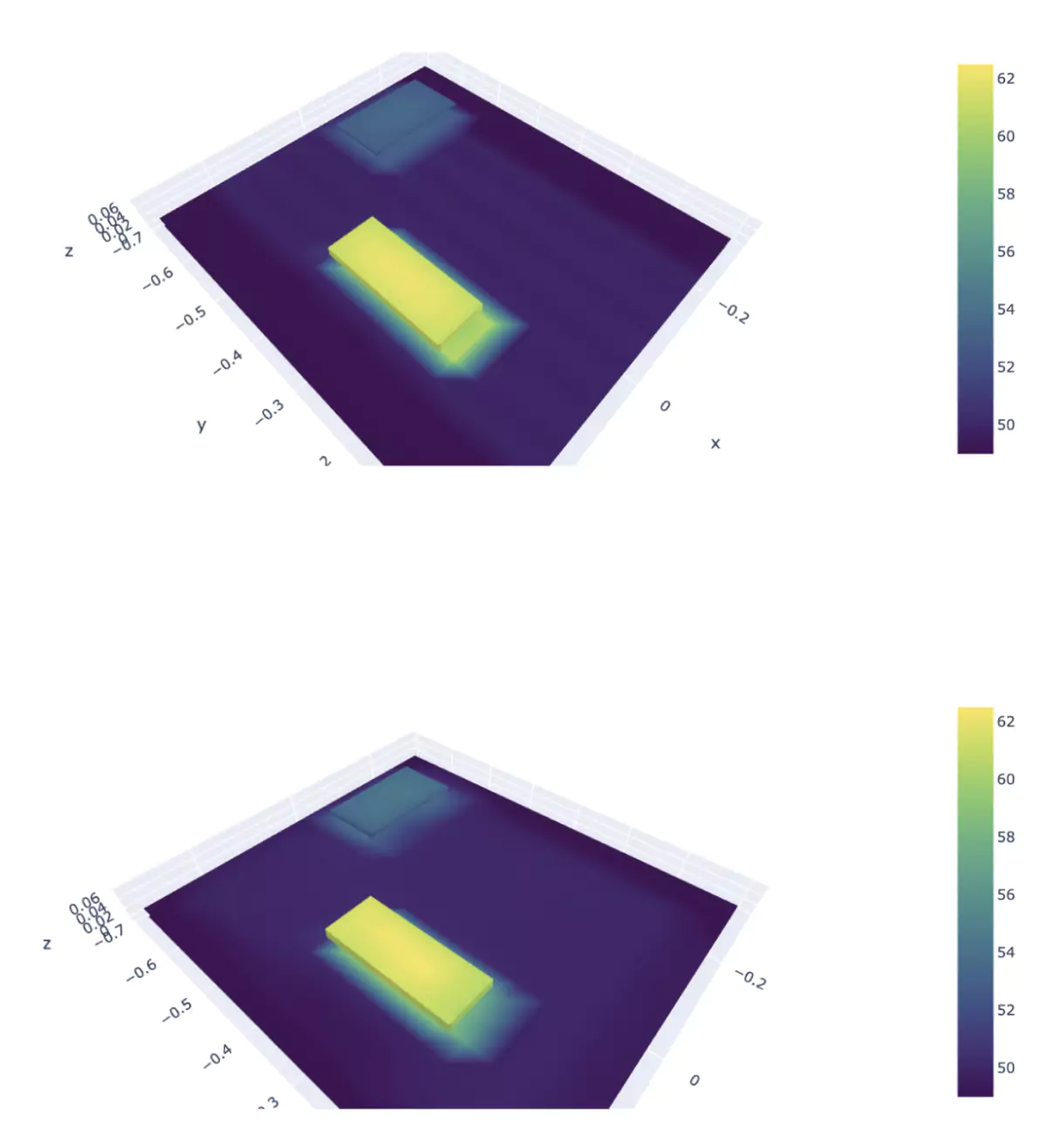
4 Conclusion
4 Conclusion We demonstrated that NCS is able to emulate a complex thermal simulator with high accuracy, therefore providing response times in the order milliseconds, versus 20 minutes for the traditional simulation.
NCS reaches a very good accuracy with a 1.17% error with only 500 training samples, which only slightly drops to 1.56% when 200 samples are used. Importantly, we saw that varying topologies were handled within a single dataset, while NCS successfully identified the sources of heat, and scaling them adequately. On top of accuracy, this is one of the major strengths of NCS, as this is not possible using traditional approaches. Moreover, the network is unaware of the underlying parametrization and geometries created with other parametrizations can easily be predicted or added to the dataset. This report also validates the usage of Neural Concept Shape on thermal modeling problems for satellites, and shows that a good accuracy can be reach using a default configuration of NCS. Using this method, ESA’s engineers will now be able to interact in real-time with the design, by having a direct feedback on geometry modifications, directly from their CAD design platform. This opens the door to a fine-grained optimization of the design of the satellite panels according to thermal constraints, to ultimately find new geometries, outperforming the existing ones.
5 Appendix A: Additional figures
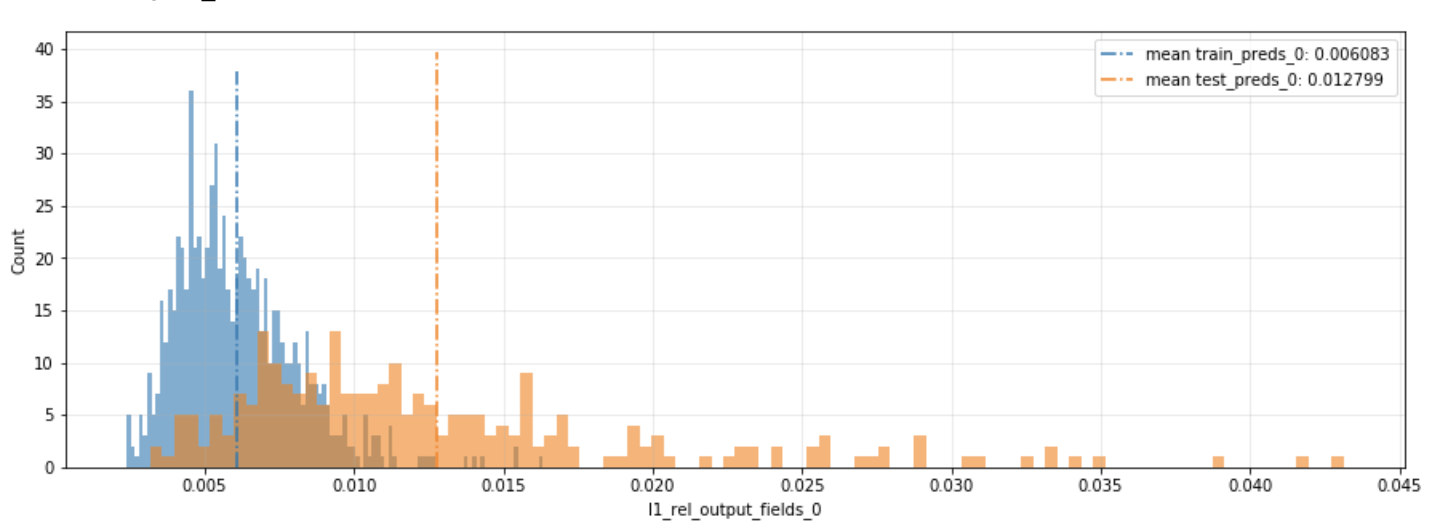
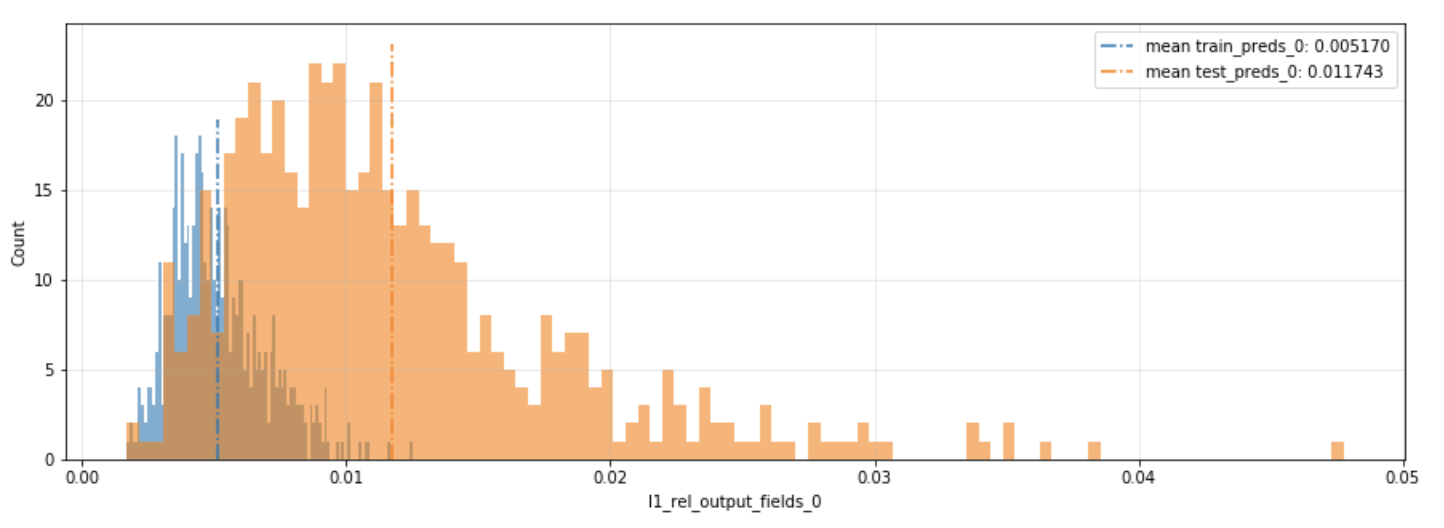
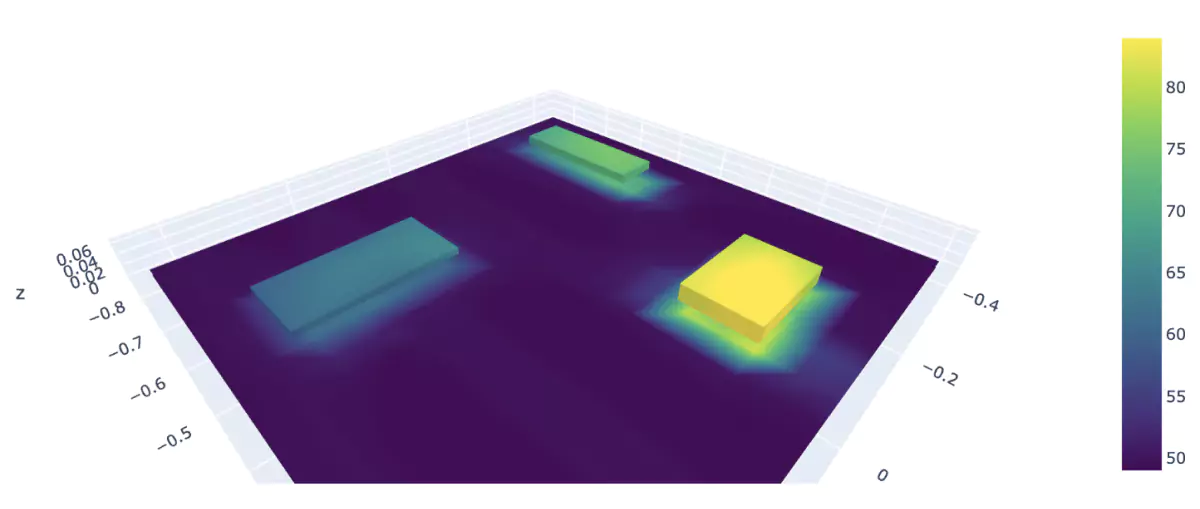
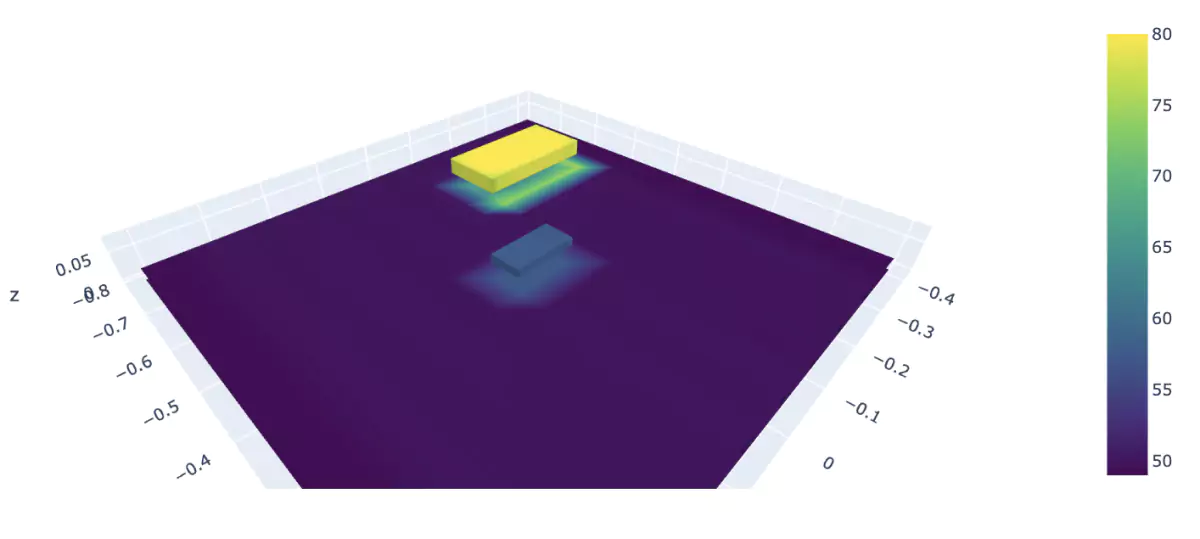
Figure 8: Comparison between ground truth and prediction for a test sample, when using 750 training samples
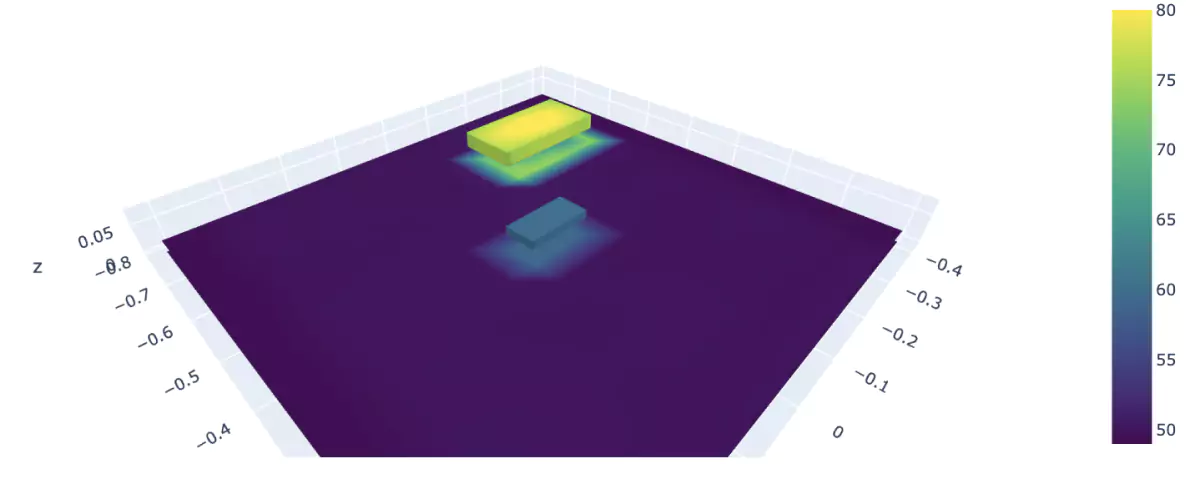
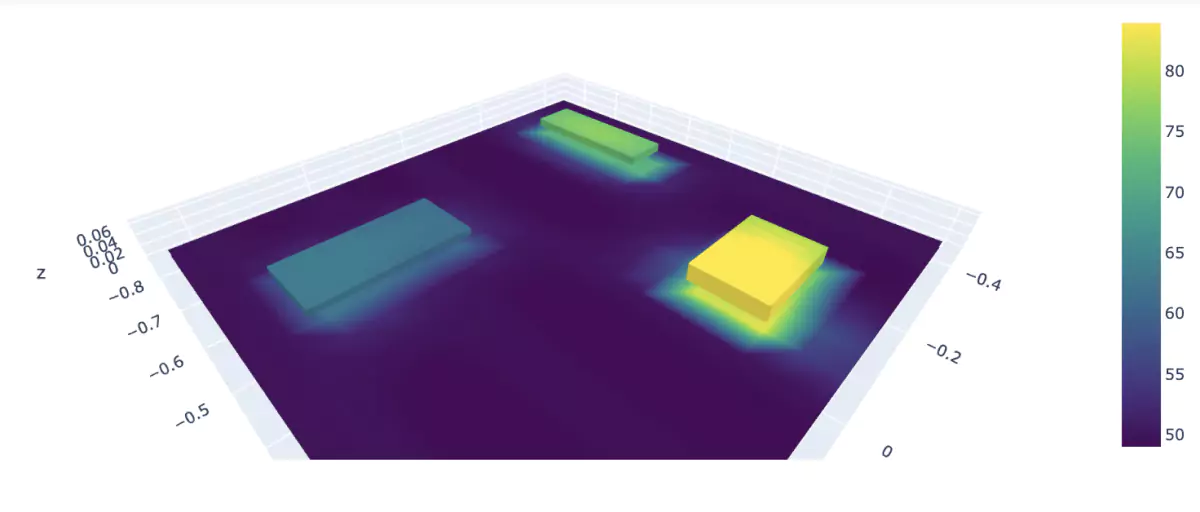
Figure 9: Comparison between ground truth and prediction for a test sample, when using 500 training samples