Response Surface Methodology Overview & Applications
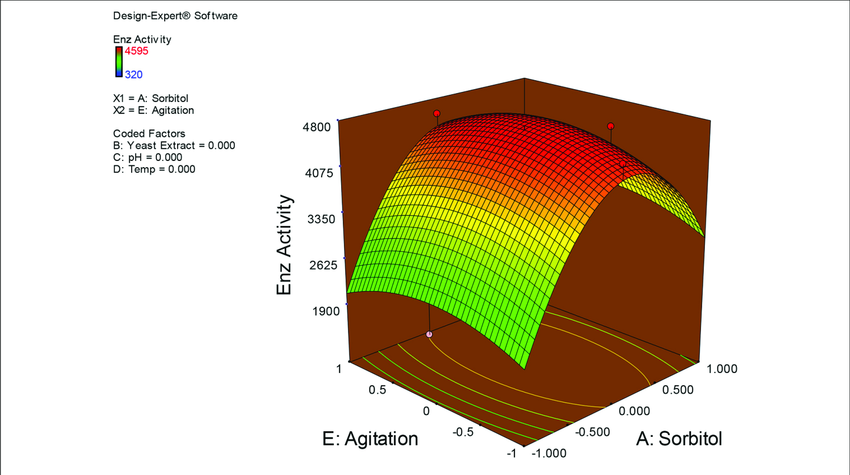
Response Surface Methodology (RSM) is a statistical approach widely used in designing and optimizing experiments involving multiple variables. This article provides an overview of Response Surface Methodology, delving into its history and purpose. We will review the design of experiments, data analysis, optimization, applications, challenges, and frequently asked questions on response surface optimization and modeling. We will also explore the possibility of collaboration between RSM and Reduced-Order Modeling and applications in product design.
The Response Surface Method is a data analysis tool with direct business implications. RSM provides actionable insights by clarifying the process of fitting models to collected data. These insights empower executives to make informed decisions, optimize operations, and drive real business results.
In the modern realm of advanced product design tools such as generative design, topology optimization, and AI, RSM stands out for its simplicity and connection to experimental test data and its wide generality. It is a technique for designing experiments, optimizing processes, and understanding the relationships between multiple variables.
What Is Response Surface Methodology?
Response Surface Methodology or Response Surface Modeling (RSM) is a collection of mathematical and statistical techniques used for modeling and analyzing complex relationships between multiple independent variables and the responses they produce on the dependent variable Y. Response Surface Modeling is used in product and process design since it helps optimize processes and understand the interplay between various factors, which is sometimes very intricate because of the concurrent presence of several independent variables.
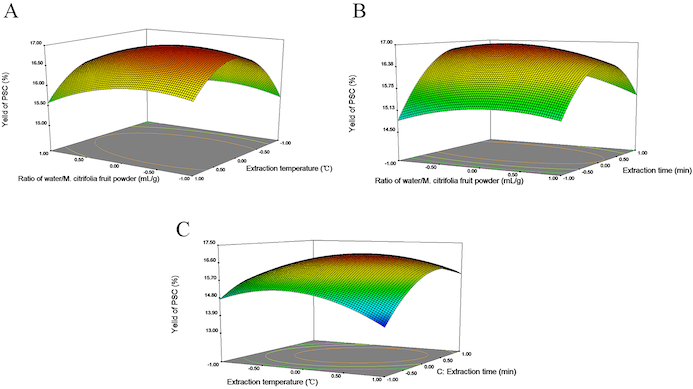
Response Surface Methodology is a subset of Design of Experiments (DOE). DOE is a broader statistical approach to planning, conducting, analyzing, and interpreting experiments. Conversely, RSM is a specific technique within DOE that focuses on modeling and optimizing complex relationships between multiple variables.
History of RSM
The roots of Response Surface Methodology can be traced back to the mid-20th century when statisticians and engineers sought more systematic approaches to experiment design. The seminal work of George E.P. Box and K. B. Wilson in the 1950s laid the foundation for what would later become RSM. Box and Wilson introduced the concept of response surfaces as a way to model the relationship between multiple variables and responses in a systematic and mathematically rigorous manner. Their landmark paper, "On the Experimental Attainment of Optimum Conditions," published in 1951, marked a significant milestone in developing RSM methodologies.
Throughout the 1960s and 1970s, Response Surface Modeling became an indispensable tool in industrial experimentation.
The publication of Box and Draper's influential book, "Empirical Model-Building and Response Surfaces" in 1987, provided a comprehensive guide to the RSM application in various fields. RSM's systematic approach to optimizing complex processes and its ability to reduce the number of experimental runs revolutionized industrial practices. The methodology succeeded in chemistry, engineering, and manufacturing industries, where intricate relationships between variables needed careful consideration for process improvement.
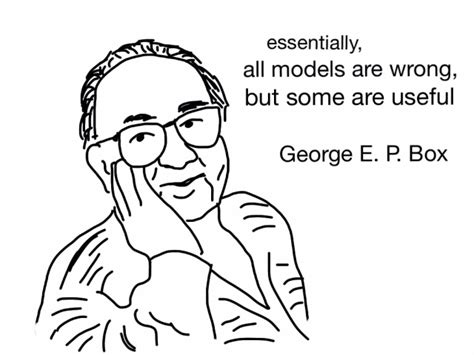
Major Milestones and Advancements in Response Surface Methods
In the ensuing decades, RSM witnessed significant milestones and advancements. The introduction of factorial experiments within the framework of Response Surface Modeling provided researchers with a powerful statistical tool to vary multiple factors simultaneously and understand their combined effects. Central Composite Design (CCD), developed by Box and others in the 1950s, emerged as a pivotal experimental design, balancing precision and resource efficiency. In the 1960s, Box and Draper extended RSM with the Box-Behnken Design (BBD), providing an alternative to CCD and factorial designs with fewer experimental runs.
Recent Developments and Integration
In recent years, Response Surface Methodology (RSM) has continued to evolve, incorporating modern statistical techniques and computational methods. Integrating artificial intelligence and machine learning technologies has expanded RSM's capabilities for modeling complex systems with non-linear relationships. Researchers and practitioners now leverage advanced statistical tools and software to implement RSM more efficiently and effectively in diverse fields.
Designing Response Surface Experiments
Designing Response Surface Experiments involves strategic planning to ensure systematic and comprehensive data-gathering response surface design. This process includes considerations of factors, levels, and the selection of experimental designs, laying the foundation for effective experimentation.
Planning an RSM Experiment
Planning an RSM experiment is a crucial initial step that requires meticulous attention to detail. The goal is to design an experiment that systematically explores the factors affecting the measured response variable. The key components in planning include:
Identification of Factors: Clearly define the factors that may influence the response. These input variables could be process parameters, material properties, or other relevant variables.
Selection of Factor Levels: Determine the range and levels at which each factor will be tested. This ensures a comprehensive understanding of the factor space.
Experimental Design: Choose an appropriate experiment design that optimally utilizes resources while providing robust information. Common designs include factorial experiments, Central Composite Design (CCD), and Box-Behnken Design (BBD).
Example
Consider a chemical process with factors like temperature, pressure, and concentration. Planning the RSM experiment involves specifying the temperature range, pressure levels, and concentration variations and selecting an experimental design that suits the available resources.
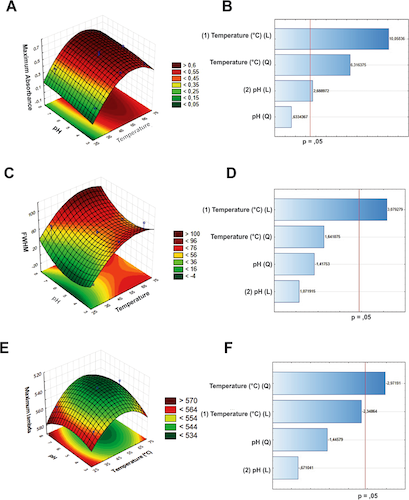
Factorial Design
Factorial experiments are integral to RSM, allowing researchers to study the effects of multiple factors simultaneously. Each factor varies at different levels in a factorial design, and all possible combinations are tested. The general formula for a factorial experiment with k factors each at levels a, b, c, ..., is:
Number of Runs=a×b×c×...
This comprehensive exploration enables the assessment of main effects and interactions among factors, providing valuable insights into their joint influence on the variable.
Example
For a 2^3 factorial experiment with factors A, B, and C at two levels each, the total number of runs is 2^3 = 8, and all combinations (2 levels for A × 2 levels for B × 2 levels for C) are included in the experiment.
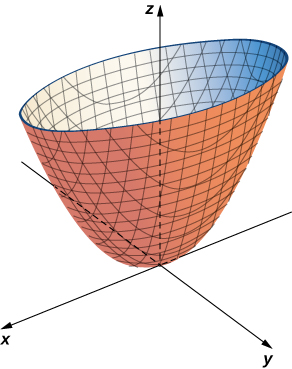
Central Composite Design (CCD)
Central Composite Design is a versatile experimental design combining factorial points with additional center and axial points. It allows for efficient exploration of the factor space, balancing precision and resource requirements. The formula for the number of runs in a Central Composite Design is given by:
Number of Runs=2k+2k+n_c
Here, k is the number of factors, and n_c is the number of center points. Central Composite Design facilitates the estimation of quadratic response surfaces, enabling the investigation of curvature in the model.
Example
For a Central Composite Design with three factors (k = 3) and two center points, the total number of runs is
2×3+2×3+2=142×3+2×3+2=14
Box-Behnken Design (BBD)
Box-Behnken Design is a choice when a full factorial experiment is impractical due to resource constraints. It efficiently explores the factor space with fewer experimental runs than a full factorial design. The formula for the number of runs in a Box-Behnken Design is given by:
Number of Runs=k²+k+n_c
Like in Central Composite Design, k is the number of factors, and n_c is the number of center points.
Box-Behnken Design is particularly useful for exploring quadratic response surfaces.
Example
For a BBD with three factors (k = 3) and one center point, the total number of runs is
32+3+1=1332+3+1=13
Data Analysis and Model Fitting in Response Surface Methodology
Data analysis and model fitting are essential for extracting meaningful insights with Response Surface Methodology.
This section describes how experimental data are collected and the steps of response surface models, validating and selecting models, and interpreting coefficients.
These processes collectively contribute to understanding the relationships between variables in Response Surface Methodology experiments.
Collecting Experimental Data in Response Surface Methodology
In Response Surface Methodology experiments, data acquisition follows a systematic process, including executing planned experimental runs and recording corresponding responses meticulously. The primary objective is to construct a comprehensive dataset that accurately reflects the interactions between specific independent variables and the response variable.
Data collection is crucial for robust statistical analysis and meaningful insights into the relationships within the experimental system.
Meticulous data acquisition can be exemplified by the systematic execution of planned experimental runs and the precise recording of the corresponding responses. For instance, in a chemical manufacturing study optimizing a reaction process, planned runs could involve variations in factors like temperature, pressure, and concentration. Meticulous recording entails capturing the exact measurements of yield, reaction time, and purity corresponding to each set of experimental conditions. This approach ensures that the dataset assembled is extensive and accurately captures the nuances of the interactions between independent variables and the response variable.
Fitting Response Surface Models
After gathering data in your Response Surface Methodology experiment, the next step is fitting models. Think of it as combining the pieces to create a mathematical model describing how your variables interact.
The Quadratic Model Equation
Now, you have your response dependent variable (let's call it Y), and you want to find a formula explaining how Y responds to changes in your independent variables (say Xi and Xj). So, we are looking for some Y = Y (Xi, Xj).
We will present an "awesome" quadratic model and break it down in plain English.
The equation for a quadratic response surface model is expressed as:
Y = β0 + ∑ βiXi + ∑i ∑j βij Xi Xj + ε
Here:
- β0 is the intercept - a starting point for Y when all other variables are zero.
- βi are the linear coefficients - they tell you how much Y changes for each unit change in a single Xi.
- βij are the interaction coefficients: they show how Xi and Xj team up to influence Y.
- Xi and Xj are the independent variables - they're the ones you tweak to see how they affect Y.
- and ε is the error term, like little glitches in your data that the model can't explain.
Model Validation and Selection in Response Surface Methodology RSM
The validation and selection of a response surface model involve scrutinizing its predictive accuracy and generalizability to unseen data.
Techniques such as cross-validation and goodness-of-fit measures aid in assessing the model's robustness and applicability beyond the observed data.
Interpreting Model Coefficients in Quadratic Models
Interpreting the coefficients within the response surface model is pivotal for discerning the quantitative impact of each variable on the predicted response amount.
The coefficients βi (linear coefficients) and βij (interaction coefficients) translate the strength and direction of the relationships:
- The strength of a coefficient βi tells us how much Y changes when the corresponding independent variable changes by one unit. Think of it as the power of influence each variable wields.
- The direction βij is where it "gets exciting". A positive coefficient implies a positive influence on Y. Picture it as your variable being a cheerleader, lifting the Y higher. Conversely, a negative coefficient suggests a negative impact, like a subtle force pulling the Y in the opposite direction.
Technical Examples for βi and βij
Linear Coefficient (βi)
Imagine β1, a linear coefficient, is associated with the process variable "Temperature" in a chemical process.
- If β1 is 2, it means for every one-unit increase in temperature, our Y (let's say, product yield) increases by two units.
- If β1 is -1, it means for every one-unit increase in temperature, our product yield decreases by 1 unit.
- Interaction Coefficient (βij) with two process variables
Now, consider β12, an interaction coefficient linked to process variables "Temperature" (X1) and "Pressure" (X2).
- If β12 is 3, increasing both temperature and pressure as process variables enhances our response variable in a synergic or collaborative way.
- If β12 is -2, it implies that simultaneously increasing temperature and pressure has a dampening effect on the response variable.
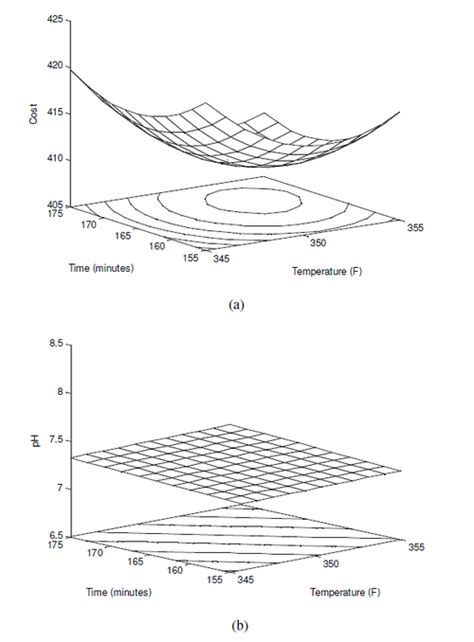
Optimization Using Response Surface Methodology
In Response Surface Methodology, optimization is the toolset guiding engineers toward efficiency and performance goals. Let's explore the tools and considerations that make optimization an actionable toolset in the Response Surface Method.
Desirability Function Approach
Think of the desirability function approach as your guide or compass through the optimization journey.
This method doesn't settle for just one target; it simultaneously plays with multiple response variables and their respective targets. This is like a skilled juggler keeping multiple balls in the air – the desirability function helps find the "sweet spot" where all variables align with their desired outcomes.
The formula for desirability (D) encapsulates your "aspirations" for each response variable:
D = (d1 × d2 × … × dk)^(1/k)
Here, d1, d2, …, dk are individual desirabilities for each response, and k is the number of responses.
Identifying Optimal Process Conditions
RSM acts as a "treasure map" in our quest for optimal process conditions. By tweaking the factor level, we aim to find "gold"; to be more technical, the combination that maximizes or minimizes our response variable.
Picture it as exploring a terrain where each adjustment brings you closer to the optimal summit. Through its systematic approach, RSM ensures you reach the highest peaks or navigate the deepest valleys, depending on your process optimization goal.
Practical Considerations in Optimization
When we optimize processes using the Response Surface Method, it's like fine-tuning a machine – a systematic approach to make things work better. As we dive into this optimization journey, practical considerations become our tools, ensuring we make wise decisions in the face of challenges.
One vital consideration is 'addressing constraints.' Simply put, it means dealing with the limits of the system. For example, if we're optimizing a manufacturing process, constraints might be the time available, the budget, or the capacity of equipment. By working within these limitations during optimization, we guarantee that our solutions are practical and doable, avoiding unrealistic or impossible scenarios.
Another important aspect is 'ensuring robustness.' This means making our optimized solutions strong enough to handle unexpected problems. In a product design context, it could involve testing the design in various real-world conditions or tweaking it to withstand input variations. This way, we ensure that our optimized solution remains effective and tough, even when faced with uncertainties or changes in the working environment.
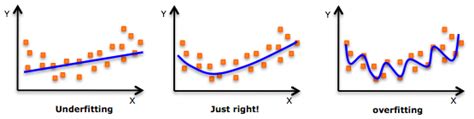
Last but not least, 'avoid overfitting.' Avoiding overfitting is like not getting lost in the details. In optimization, overfitting happens when we tailor the solution too closely to the specific data used for optimization, making it less applicable to other situations. To steer clear of overfitting, we focus on extracting essential patterns and relationships without getting bogged down in unnecessary details. This ensures our optimized solutions work well in the lab and the real world.
Applications of Response Surface Methodology
The Response Surface Methodology holds significance for its practical applications in optimizing processes and enhancing product performance. Using technical examples, let's delve into its role, specifically within the automotive industry, a competitive arena where new methodologies such as AI and generative design are tested, and statistical analysis is well known in design and manufacturing departments.
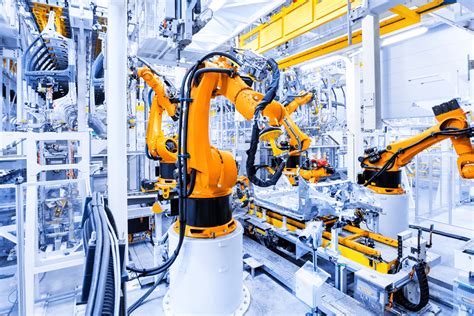
Efficiency in Parameter Optimization
In engineering, particularly in the automotive sector, RSM is crucial in optimizing multiple parameters in the design space. For instance, in automotive design, RSM can optimize fuel efficiency by considering factors such as engine compression ratio, fuel injection timing, and air-fuel mixture.
Accelerated Product Development
The Response Surface Method can accelerate the product development processes within the automotive industry.
Engineers can iterate designs more quickly by reducing the need for physical prototypes through virtual experimentation.
For example, the Response Surface Method could streamline the developing of a vehicle's suspension system by optimizing factors like spring rates and damping coefficients.
Robustness in Design
In the competitive automotive landscape, robust design is essential. RSM contributes to ensuring that designs are not only optimized but also robust across various operating conditions. For instance, it can aid in designing a robust braking system by considering factors such as brake pad material, disc diameter, and temperature variations.
Cost Reduction Through Optimization
RSM assists engineers in finding a balance between performance and cost. By optimizing factors like material usage or manufacturing processes, automotive engineers can design cost-effective yet high-performance components. An example is optimizing composite materials in automotive body panels to balance strength, weight, and cost.
Real-world Testing Reduction With the Response Surface Method
Physical testing is resource-intensive in automotive product development. Cost reduction is possible thanks to the benefits of generative design. The Response Surface Method helps reduce reliance on extensive real-world testing by accurately predicting how changes in design variables will impact performance. This is exemplified in aerodynamics, where RSM can optimize vehicle shapes for reduced drag without requiring numerous wind tunnel tests.
Environmental Impact Mitigation with Response Surface Modeling
Environmental considerations are integral to automotive design.
Response Surface Modeling aids in optimizing designs for reduced environmental impact, such as enhancing fuel efficiency, reducing emissions, and optimizing electric vehicle battery performance.
In summary, RSM is a valuable engineering and product design tool, particularly within the automotive industry. Its technical applications contribute to optimizing processes, faster product development, robust design, cost-effective solutions, reduced reliance on real-world testing, and environmentally conscious designs.
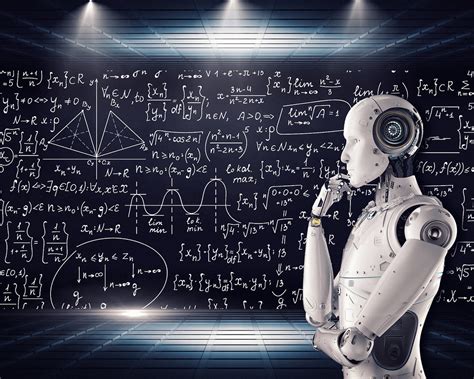
Combining Response Surface Modeling and ROM
Finding the right balance between accuracy and efficiency is a constant challenge in engineering and computer modeling. Combining Response Surface Modeling and Reduced Order Modeling (ROM) provides a powerful strategy to reduce costs in building surrogates for complex systems significantly.
Starting with Response Surface Modeling, the initial goal is to understand complex relationships through well-designed experiments. RSM is cost-effective in this phase, offering valuable insights with fewer experimental runs than high-fidelity simulations. It identifies key features and variables crucial to the system's behavior.
Building on insights from the Response Surface Method, we shift to ROM, creating a model that captures essential dynamics with fewer computational resources. ROM, being efficient, significantly reduces computational costs by representing the system with a simplified set of basis functions or modes. This model, developed based on RSM insights, is now a cost-efficient surrogate.
Consider the optimization of a battery system's performance in automotive engineering. RSM guides initial experiments, identifying key parameters such as charge-discharge rates, temperature, and electrode material composition. Transitioning to ROM, a model is constructed based on these parameters, serving as a surrogate for rapid simulations and optimizations. This integrated approach speeds up the iterative optimization process, allowing engineers to fine-tune designs cost-effectively and navigate the complexities of battery system modeling.
Bibliography
- Box, G. E. P., & Wilson, K. B. (1951). On the Experimental Attainment of Optimum Conditions. Journal of the Royal Statistical Society: Series B (Methodological), 13(1), 1-45.
- Box, G. E. P., & Draper, N. R. (1987). Empirical Model-Building and Response Surfaces. John Wiley & Sons.
- Myers, R. H., Montgomery, D. C., & Anderson-Cook, C. M. (2016). Response Surface Methodology: Process and Product Optimization Using Designed Experiments (4th ed.). John Wiley & Sons.
- Khuri, A. I., & Cornell, J. A. (1996). Response Surfaces: Designs and Analyses. Marcel Dekker.
- Draper, N. R., & Box, G. E. P. (2007). Response Surface Designs: A Literature Survey. Technometrics, 49(2), 121-135.