Product Development Automation: Shaping the Future
How are companies staying ahead of the curve in today’s fierce market competition? Automation in product development is one of the answers! Automation transforms how products are conceived, designed, and brought to market. Our article focuses on the technical aspects of product development automation, exploring the methodologies shaping the future of product creation. This subject is relevant for product development specialists and organizations seeking to maintain or win a competitive edge.
Introduction to Product Development Automation
The tangible effect of automation in product development is to automate repetitive tasks to reduce time to market, improving product quality while lowering production costs. Let us first define product development automation tools and what are the most critical product development processes.
Product development automation uses technologies to streamline and optimize various product lifecycle stages. This includes initial design, simulation, prototyping, manufacturing, and even post-production maintenance. In engineering terms, automation integrates with PLM (Product Lifecycle Management) systems, enabling seamless transitions between CAD (Computer-Aided Design), CAM (Computer-Aided Manufacturing), and CAE (Computer-Aided Engineering) workflows.
With those process automation tools, product development automation streamlines industrial processes and enhances the product lifecycle stages.
Automation in product development is not a novel concept. However, recent artificial intelligence (AI) and data analytics advancements have accelerated its adoption. Let us reconstruct the history of automation tools with a simple example.
A Short History of the Circle
Let’s take a super simple problem—drawing a circle!
As it can be approached at different levels, reconstructing the circle's “history” is, in a sense, retracing the history of automation in product development!
So, how can we build a circle, and what can we do about it?
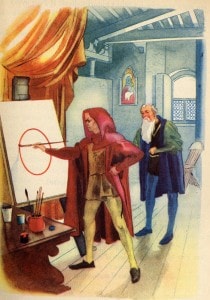
First, we can draw a circle by hand, but reproducibility is uncertain. Human ability is the most relied-on factor, with extremely poor results in an industrial context where "anyone" should be empowered to draw a circle.
As a second step, we can use analog tools, such as a drafting compass. This process is reproducible, but it takes a long time and has high costs. Relying on a human using a mechanical tool produces acceptable results in an industrial context where no other competitive tools exist. Also, at this stage, we wonder if there is a way of automating repetitive tasks such as using the drafting compass.
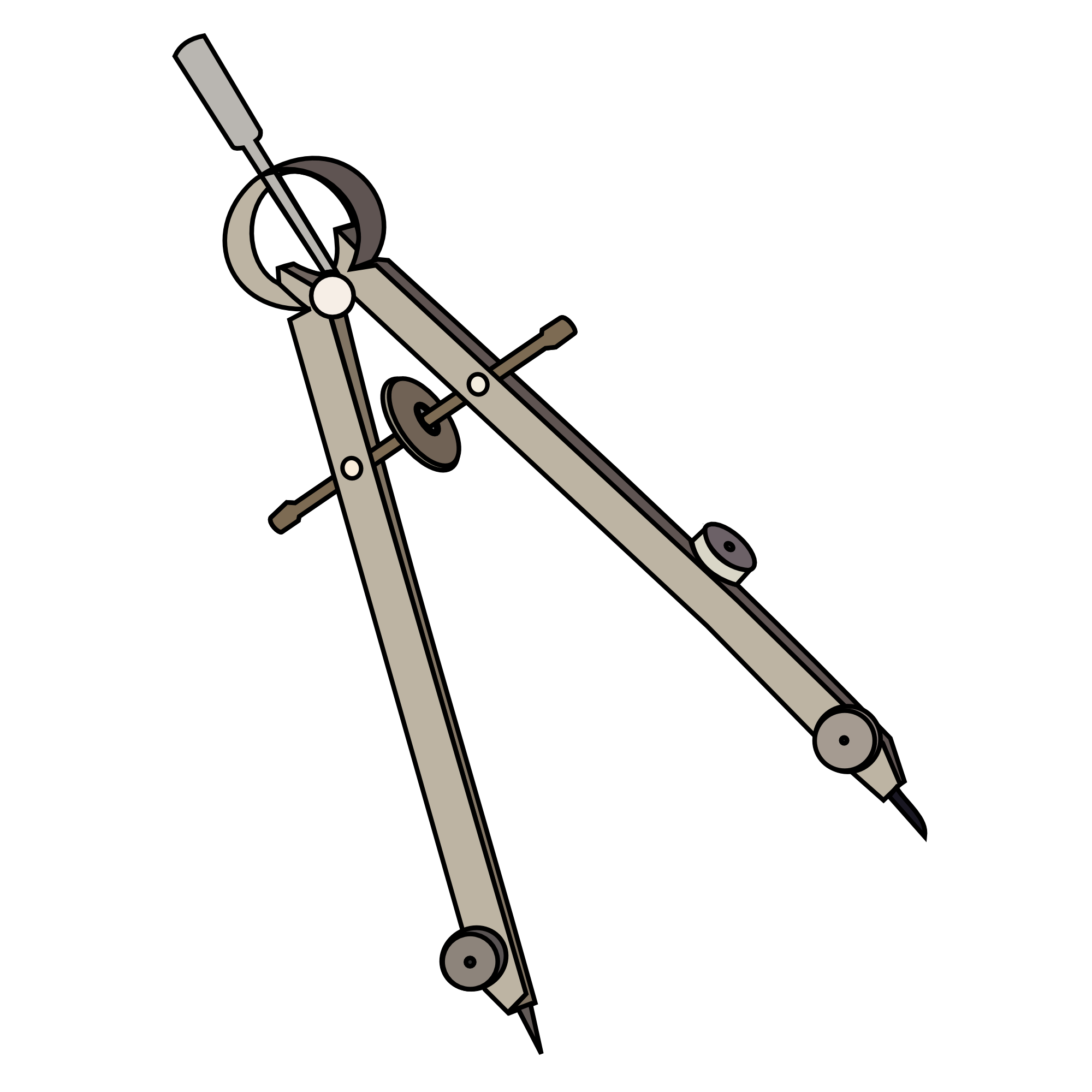
Now, imagine using Computer-Aided Design to throw away your drafting compass and draw a circle—any circle, say from 0.0001 to 100 m. In this case, we have a digital tool that is fast and reproducible in an industrial setting.
We can also associate other functionalities with the CAD representation of the circle, for instance, treating the circle as the section of a sphere submerged in a liquid or a cylinder under compression. We could calculate many hydrodynamic or mechanical properties using computerized tools like CAE (Computer-Aided Engineering), such as in the aerodynamics simulation shown in the figure.
Finally, suppose the circle is created parametrically with a radius “R” and center “XYZ,” these values are called upon in an automated process. In that case, we now have an instantaneous digital tool capable of producing thousands of circles in a fraction of a second.
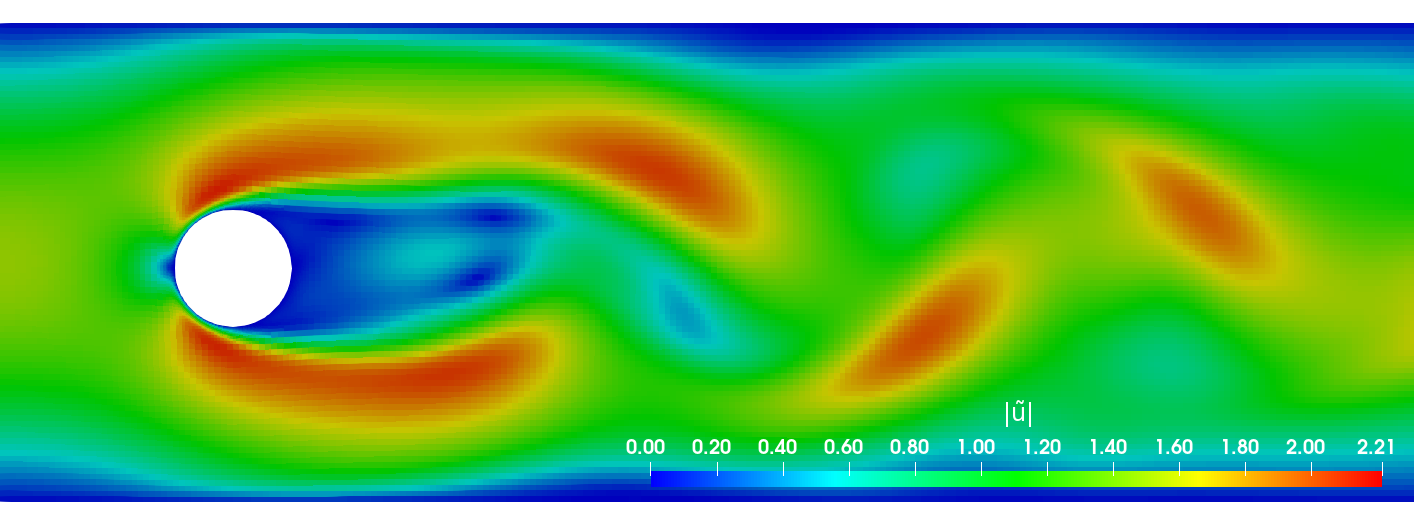
As the “icing on the cake,” Artificial Intelligence (AI) with 3D Deep Learning allows us to process the data generated by CAD, experimentation (CAT), and simulation (CAE) and create a new type of pressure based on data-driven learning. Combined with AI-guided CAD design modifications, this leads to generative design.
Implementing Automation in Product Design
As anticipated, product design automation is moving from traditional processes that rely on manual tasks such as drafting and prototyping physical parts to be sent to testing labs. Those expensive “physical cycles” have been replaced by sophisticated software tools that automate various aspects of design, simulation, and testing.
Generative Design
What is the role of AI in engineering? Generative design software uses AI and ML algorithms as automation tools for optimized design solutions based on specific constraints and requirements. Designers input parameters like material, weight, strength, or cost, and the software generates multiple design options that meet these criteria.
Automation tools permit a deeper exploration of design possibilities, leading to innovative and unconventional solutions that would be hard to develop manually. Additionally, generative design can cut down on material usage and improve product performance by identifying the most efficient design configurations.
Simulation and Testing Automation
With CAD alone, we would have a lot of functionality. Still, we would not know how the product behaves, for instance, a mechanical part subject to fatigue or a satellite subject to vibrations during the launch of its vector. This can be done in a laboratory or virtual testing.
Testing and virtual testing, i.e., simulation, are critical components of the product development process. With testing and simulation, we ensure that designs meet performance and safety standards before moving to production. Simulation software can model complex physical phenomena, such as fluid dynamics (CFD), structural integrity (FEA), and thermal behavior. Advancements in simulation software have driven automation in this area.
Automated simulation tools enable engineers to perform virtual testing on digital prototypes, reducing the need for physical prototypes and accelerating the development process. Furthermore, these tools can run multiple simulations in parallel on the cloud, exploring different scenarios and identifying potential issues earlier in the design phase.
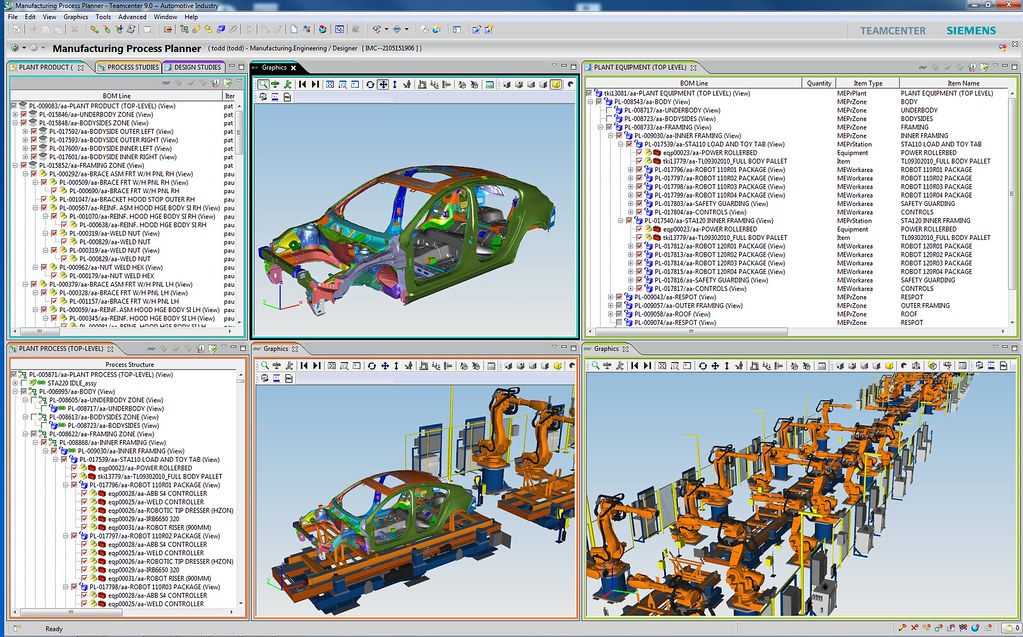
Automation in Product Lifecycle Management (PLM)
Product Lifecycle Management (PLM) refers to managing a product’s entire lifecycle, from initial concept to end-of-life disposal. Automation within PLM systems facilitates the coordination of various stages of the product and development cycle, ensuring that all stakeholders have access to up-to-date information and that processes are streamlined.
PLMs establish a centralized repository for all product-related information. PLM fosters collaboration among teams while reducing the likelihood of errors or delays.
Automated PLM systems facilitate industry standards and regulations by ensuring the maintenance and accessibility of all requisite documentation throughout the product’s lifecycle.
Integration with ERP and CRM Systems
PLM systems are often integrated with Enterprise Resource Planning (ERP) and Customer Relationship Management (CRM) systems for maximum efficiency. ERP manages business processes such as procurement, production, supply chain, and inventory management together, while CRM systems handle customer interactions and feedback.
Integration with CRM systems can provide valuable insights into customer expectations, preferences, and feedback, guiding future product development efforts. Thus, this automation ensures product development activities align with business objectives and customer needs.
Workflow Automation
Workflow automation within PLM systems streamlines the various processes involved in product development, including time-consuming tasks such as approvals, reviews, or document management. Automated workflows ensure that tasks are completed in the correct sequence and that all necessary stakeholders are involved at the right time.
Software Development Automation
The following sections explore critical aspects of software development automation.
Continuous Integration and Continuous Deployment (CI/CD)
Continuous Integration (CI) and Continuous Deployment (CD) are fundamental practices in modern software development. CI automatically integrates code changes from multiple contributors into a shared repository, where automated tests are run to detect any issues early in development.
With automated processes, teams can release software updates more frequently and with greater confidence, reducing the risk of bugs and ensuring that new features reach users faster.
Automated Testing
Automated testing is another aspect of software development automation. It involves using scripts and testing frameworks to automatically execute test cases and verify that the software behaves as expected. Automated testing can include unit, integration, functional, or performance tests.
Developers can quickly identify and fix issues. Thus, they ensure that code changes do not introduce new bugs or regressions. Automated testing also enables continuous testing. Tests are run continuously throughout the development process, providing real-time feedback to developers.
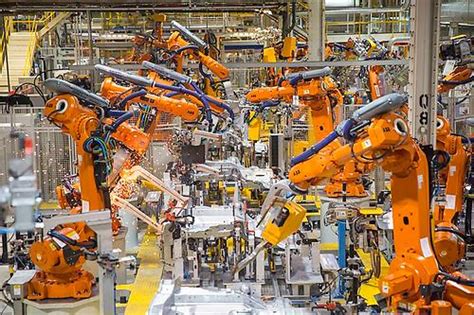
Automation in Manufacturing
Automation has long been a driving force in the manufacturing industry. Manufacturers can achieve higher throughput and consistent product quality by automating repetitive tasks.
For example, robots have become integral to assembly lines; think of automotive. These robots are designed to perform tasks that require precision, consistency, and speed, such as welding,
Robotics and Industrial Automation
Robotics and industrial automation are involved whenever products are assembled, packaged, or inspected. They also paint, solder, and assemble components. Modern industrial robots are equipped with advanced sensors and AI algorithms. They adapt to variations in the assembly process and work alongside human operators in collaborative environments (“cobots”). Thus, robots learn to automate complex tasks.
Additive Manufacturing (3D Printing)
Traditional subtractive manufacturing methods involve cutting and shaping material. Additive manufacturing (a.k.a. 3D Printing) builds objects layer by layer, allowing for greater design flexibility and customization.
With 3D Printing, designers can quickly produce physical prototypes, test them, and make iterative improvements. This rapid prototyping capability significantly reduces the time required to develop and refine new products.
3D Printing further boosts product development by enabling the production of complex geometries that would be difficult or impossible to achieve with traditional manufacturing methods. This opens up new possibilities for innovation and customization to market demands.
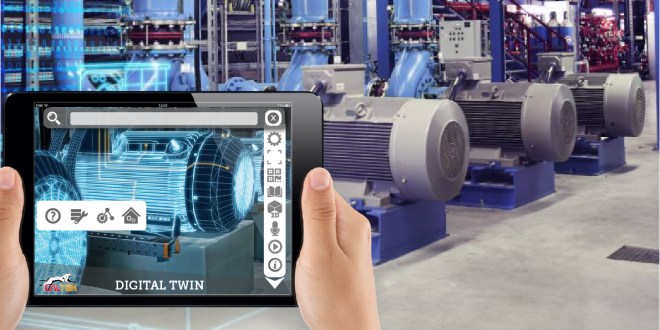
Digital Twins and Smart Factories
Digital twins and smart factories represent the next frontier in manufacturing automation.
A digital twin is a virtual replica of a physical asset, such as a machine, production line, or entire factory. It is continuously updated with real-time data from sensors and IoT devices, allowing manufacturers to monitor and optimize operations in a virtual environment.
Simulation and Optimization
With digital twins, manufacturers can simulate and analyze production processes in a virtual environment before implementing changes in the physical world.
A digital twin of a production line can be used to simulate the impact of introducing a new product variant or adjusting production parameters.
Predictive Maintenance
By continuously monitoring the condition of machines and equipment, digital twins can predict when maintenance is needed, reducing the likelihood of unexpected breakdowns and minimizing downtime. This is the so-called “predictive maintenance.” Maintenance activities can be scheduled at the most reasonable times, reducing costs and extending the lifespan of equipment.
Smart Factory Integration
In a smart factory, automated systems can adjust production schedules in real-time based on demand, optimize energy usage, and ensure that all processes operate at peak efficiency. The result is a highly flexible and efficient manufacturing environment that can quickly respond to changes in market conditions and meet customer expectations and needs.
Smart factories represent the culmination of automation technologies!
Data-Driven Product Development
The increasing availability of data and advancements in analytics technologies have given rise to data-driven product development.
Big Data and Analytics
Big data refers to the massive volumes of structured and unstructured data generated by various sources, including sensors, social media, customer behavior, and production systems.
Data Collection and Integration
Automating the collection and integration of data from multiple sources is a critical step in a data-driven product development process. This includes data from internal systems, such as ERP and CRM, and external sources, such as social media and customer feedback.
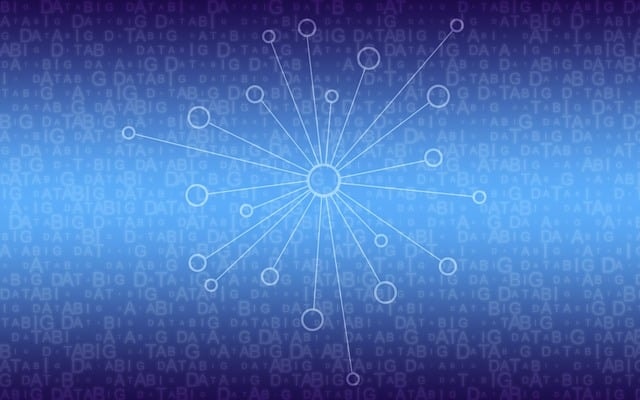
Advanced Analytics and Insights
Once data is collected and integrated, advanced analytics tools can extract meaningful insights. This includes techniques such as data mining and predictive analytics. In product development, these insights can inform decisions about product design and marketing strategies. Analytics can reveal which product features are most popular among customers, enabling companies to prioritize those features in future product iterations.
AI and Machine Learning in Product Development
AI and machine learning transform product development by automating complex tasks and creating more innovative and personalized products. Let’s see how.
AI-Driven Design Optimization
AI and machine learning algorithms can crunch tons of data to find the best design solutions. This involves generative design, where AI comes up algorithmically with design options based on specific constraints, and topology optimization, where AI figures out the best way to distribute materials within a given design space.
These AI-powered design tools do the hard work of exploring design alternatives so engineers can quickly spot the best solutions and reduce the time needed for design changes. AI can also fine-tune designs for specific manufacturing processes, ensuring products are easy to make and cost-effective.
AI in Predictive Modeling
What’s next?!
AI is also used in predictive modeling. Here, algorithms analyze historical data to predict future outcomes. In product development, predictive modeling can predict product performance in unprecedented short times. These almost real-time predictions can guide product development and operational costs and ensure that resources are focused on the most promising opportunities.
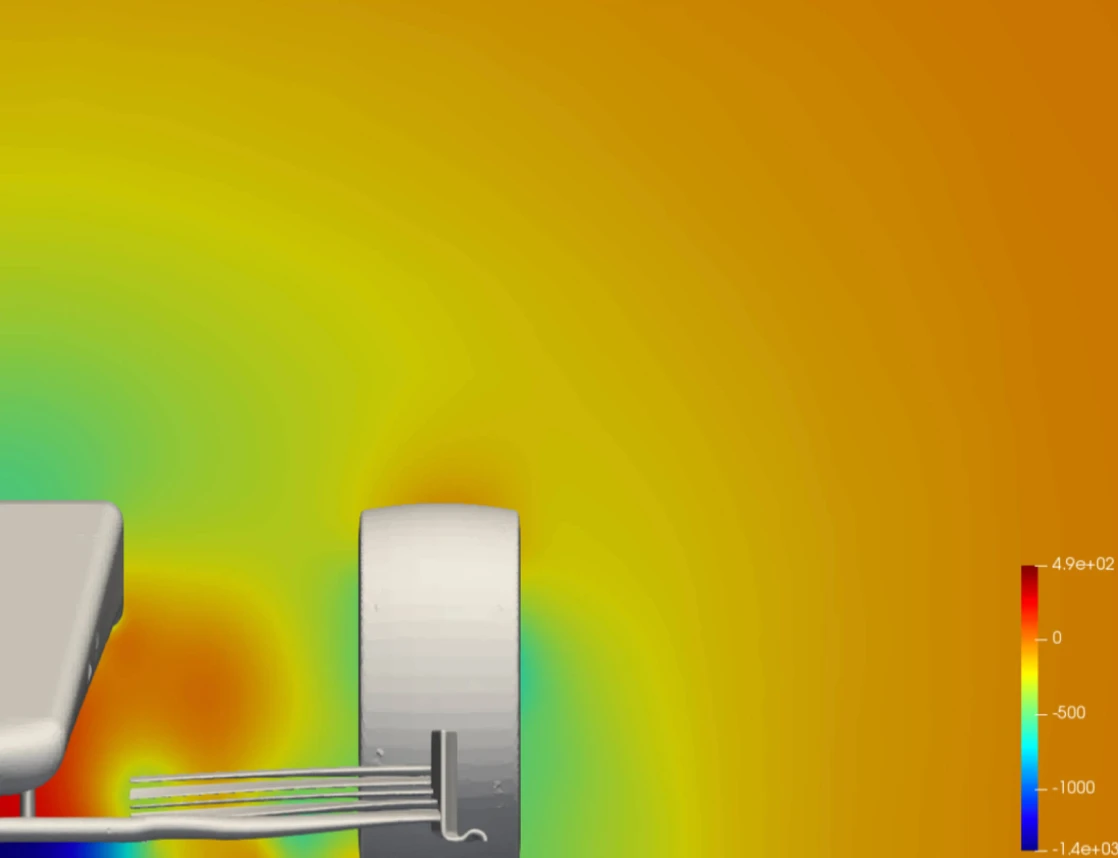
Predictive Maintenance and Quality Control
As we saw earlier, predictive maintenance is an essential data-driven piece of product development.
In addition to predictive maintenance and continuous improvement, ML algorithms can analyze data from sensors on a production line to detect manufacturing process anomalies, such as temperature, pressure, or vibration variations. When an anomaly is detected, the system can automatically adjust the process parameters or alert human operators to take corrective action. This level of automation ensures consistent product quality and reduces waste and rework, leading to cost savings and enhanced customer satisfaction.
Challenges and Considerations in Product Development Automation
While product development automation offers significant benefits, organizations must successfully address several challenges and considerations to implement and leverage these technologies’ numerous advantages successfully.
Technical Challenges
Challenges span technical, ethical, and security-related domains and require careful planning and management.
Integrating various systems and tools is one of the primary technical challenges in product development automation. Product development often involves multiple software platforms, such as CAD, PLM, ERP, and manufacturing execution systems (MES).
Interoperability between those different systems can be challenging. Differences in data formats and protocols, not to mention vendor-specific implementations, can be the bottleneck.
Organizations may need to invest in middleware or custom integration solutions that facilitate data exchange and process automation across disparate systems.
Scalability
Scalability is a critical concept for large organizations with complex product development processes. Systems must scale to handle increasing volumes of data and transactions.
As the number of connected devices and sensors in an intelligent factory grows, the underlying data infrastructure must be capable of processing and analyzing large datasets in real-time.
Similarly, automated testing frameworks in software development must be able to handle large codebases and numerous test cases without compromising performance.
Ethical and Workforce Implications
One of the most significant ethical considerations in product development automation is the potential impact on the workforce. Automation can lead to job displacement, particularly in roles that involve repetitive tasks, such as assembly line workers, data entry clerks, or quality inspectors.
To address this challenge, organizations must invest in reskilling and upskilling programs to help employees transition to new roles requiring higher creativity and technical expertise.
Workers displaced by automation in manufacturing may be retrained for robotics maintenance, data analysis, or process optimization roles.
AI and machine learning algorithms are increasingly used in product development but are not immune to bias. If the data used to train these algorithms is biased or unrepresentative, the resulting models may produce biased outcomes, leading to unfair or discriminatory decisions.
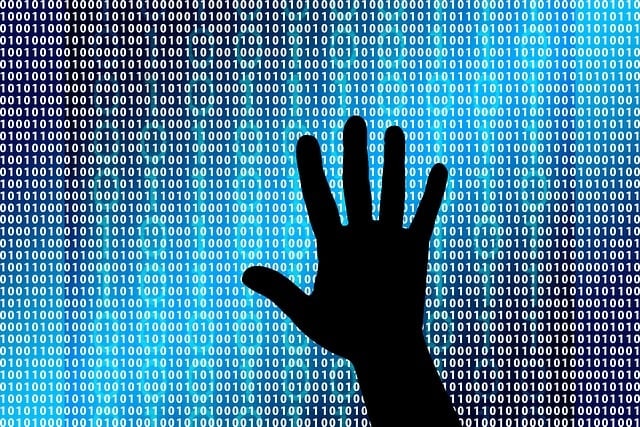
Security Concerns
As automation technologies become more integrated and interconnected, they become more vulnerable to cybersecurity threats. Automated systems, particularly those that rely on IoT devices and cloud-based platforms, are attractive targets for cyberattacks, which can disrupt operations, steal sensitive data, or compromise product quality. Organizations are implementing robust cybersecurity measures like encryption, multi-factor authentication, or intrusion detection systems.
Automated systems must be reliable and resilient to ensure product development processes are not disrupted by technical failures or external events, such as power outages or natural disasters. This requires implementing redundancy, backup, and disaster recovery systems that quickly restore operations in case of failure.
The Future of Product Development Automation
The future of product development will likely be characterized by even greater efficiency and customization.
Emerging Technologies
The following sections explore emerging technologies and trends expected to shape the future of product development automation.
Artificial Intelligence
AI and machine learning will become increasingly central in product development automation. Advances in AI algorithms, such as deep learning and reinforcement learning, will enable more sophisticated automation capabilities, such as autonomous design generation and real-time process optimization, to enhance our predictive decision-making capabilities.
Similarly, AI-powered manufacturing systems may autonomously adjust production parameters in real-time to lower operational costs and reduce waste.
Quantum Computing
Quantum computing has the potential to revolutionize product development by solving complex optimization problems that are currently intractable for classical computers. While quantum computing is still in its early stages, ongoing research and development efforts are expected to bring practical quantum computing applications to the product development domain in the coming decades.
Advanced Robotics and Human-Robot Collaboration
The next generation of robotics is expected to feature more advanced capabilities, such as greater skill, adaptability, and cognitive functions. These advancements will enable robots to perform more tasks and collaborate more effectively with human workers in hybrid work environments.
Future robots may be able to learn new tasks on the fly through machine learning and natural language processing, allowing them to work alongside human operators in dynamic and unstructured environments. This will open up new possibilities for automation in industries traditionally relying on manual labor.
Impact on Industries
We will shortly review the impact on the automotive and life science industries.
Automotive Industry
The automotive industry will likely be one of the most impacted by product development automation. As electric vehicles (EVs) and autonomous vehicles (AVs) become more prevalent, automakers will increasingly rely on automation to design, manufacture, and maintain these vehicles.
Generative design and simulation tools will create lightweight, energy-efficient vehicle components. At the same time, AI-driven manufacturing systems will optimize production processes for key components such as EV batteries and AV sensors. Automated maintenance and repair systems will also be developed to service these vehicles.
Life Sciences Industry
Product development automation will also benefit the healthcare and medical device industries. Automation technologies will enable the rapid development and production of personalized medical devices, such as custom implants and prosthetics, and the automation of drug discovery and clinical trials.
AI-driven design tools will create personalized medical devices tailored to individual patients’ anatomies, while automated manufacturing systems will produce these devices with high precision and consistency. AI and machine learning will also be critical in analyzing medical data and identifying new drug candidates.
Think of traditional vaccine development with a timeframe typically 10–15 years and cost around $500 million to $1 billion, and compare it to AI-supported clinical trials starting in less than two months, compared to the usual 3–5 years for preclinical testing. This helped Moderna design the mRNA structure for their vaccine candidate in just two days after receiving the virus’s genetic sequence
Human Involvement and Idea Generation
Human creativity and ingenuity will remain central to creating new product ideas despite the increasing automation of product development processes. While machines can automate routine tasks, they cannot think abstractly, make intuitive leaps, and promote idea generation.
In the future, human designers, engineers, and product managers will work alongside automated systems, automating tasks while leveraging their unique creative abilities to guide and enhance the automated processes. This collaboration between human creativity and machine efficiency will result in groundbreaking innovations and more personalized, user-centric products.
Automation tools will increasingly serve as creative partners for humans, augmenting their abilities rather than replacing them. For example, AI-driven generative design tools can explore many design possibilities. The outcome of the exploration is to present human designers with various innovative options they might not have considered independently.
Automation technologies, particularly AI-powered, will significantly enhance decision-making processes in product development. With data-driven insights and predictive analytics, these tools will help human decision-makers assess risks and evaluate trade-offs.
For instance, in the early stages of product development, AI-driven market analysis tools can help product managers identify emerging trends and customer needs, guiding the development of products more likely to succeed in the market. During the design phase, simulation tools can predict the performance of different design alternatives under various conditions, enabling designers to select the most promising options.
9. Conclusion
In conclusion, augmented creativity and facilitated decision-making will improve engineers’ lives and orient them to concept work rather than tedious, repetitive tasks!