Mubea using Neural Concept Shape for the Design of Innovative Lightweight Components
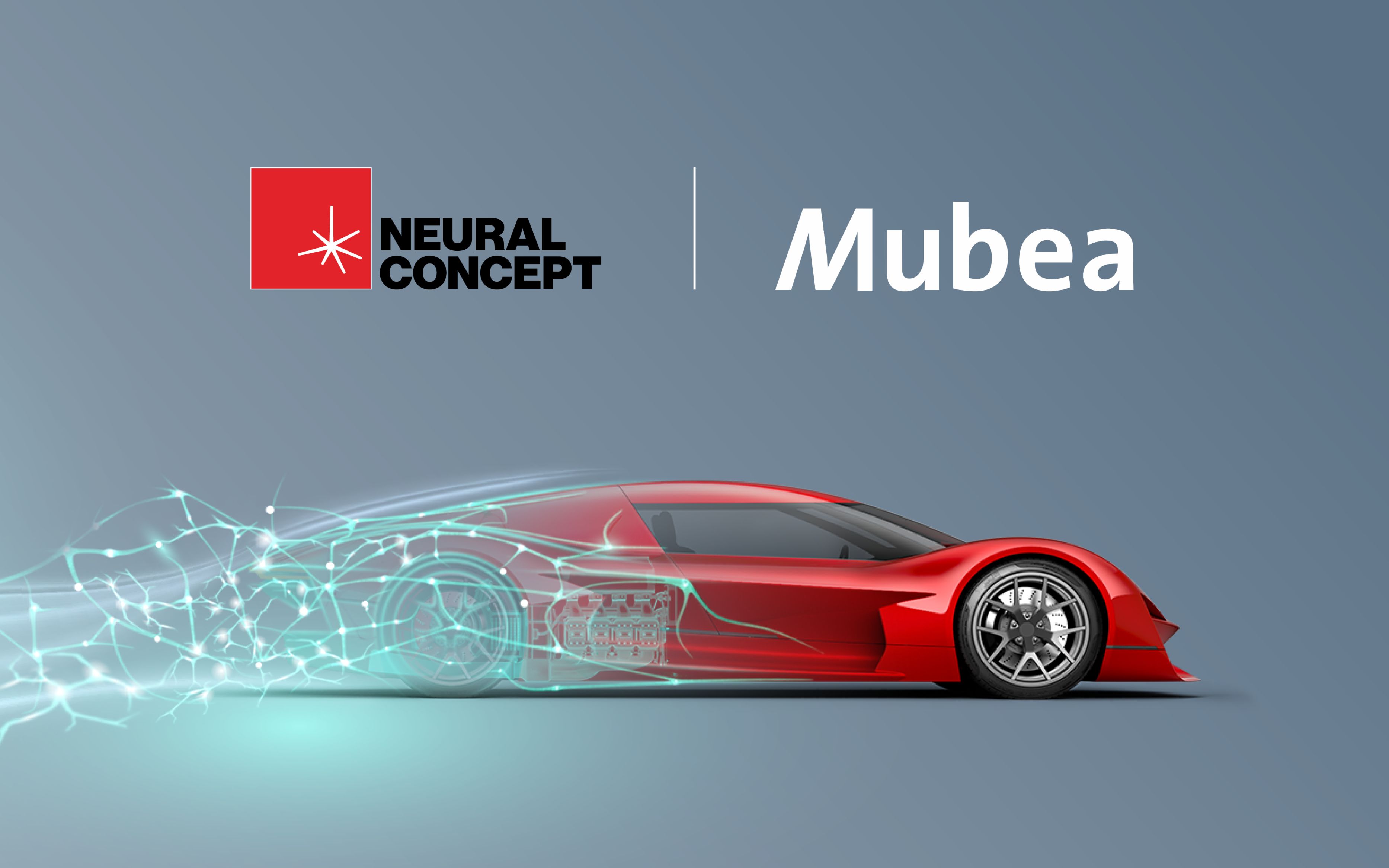
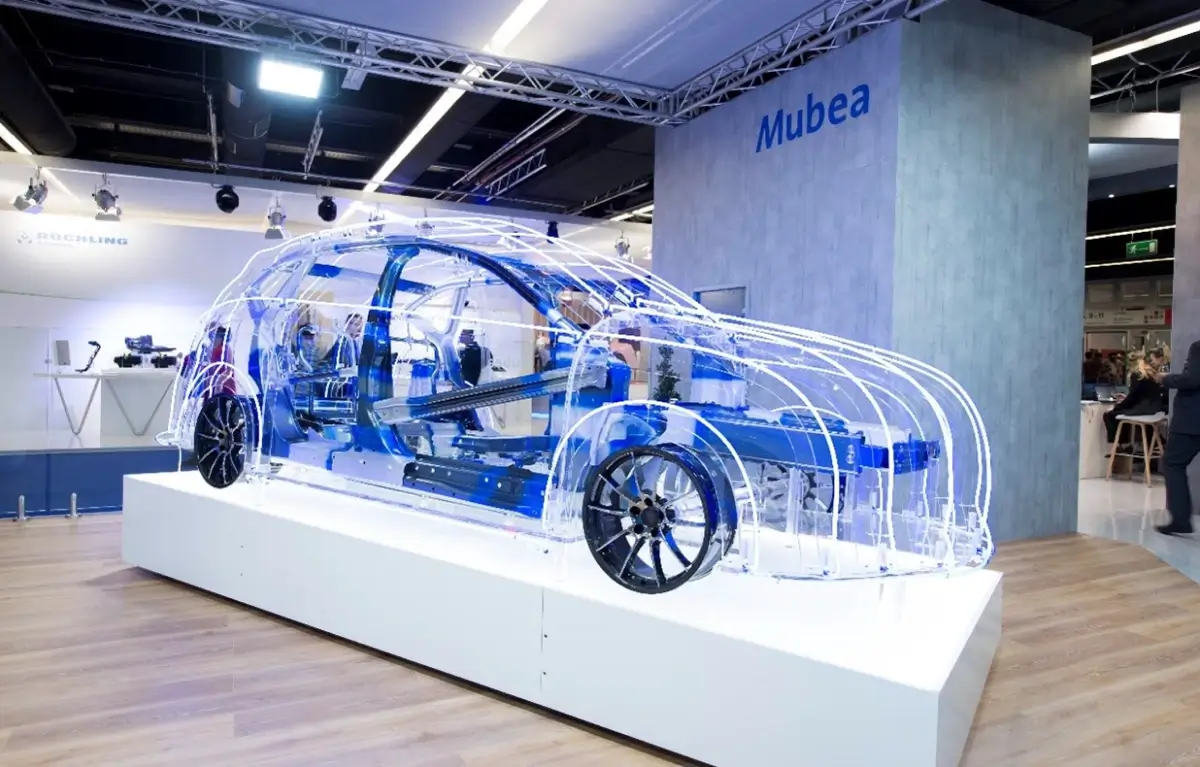
Solving a Design Challenge of Car Electrification: Lighter and Crashworthy Vehicles. The Role of Innovative AI Solutions
The drive towards full electrification of the car is an opportunity but also a challenge. Certain elements of the drivetrain will disappear, such as exhaust systems. On their turn, components such as the battery are now becoming prevalent.
Innovative solutions for lighter vehicles
Mubea is an international partner to the automotive industry and an innovative lightweight specialist. As an owner operated family company, Mubea is synonymous with long-term, sustainable commercial success.
With the global presence at 45 locations in 20 countries Mubea is a family run global player with its headquarter in Attendorn, Germany.
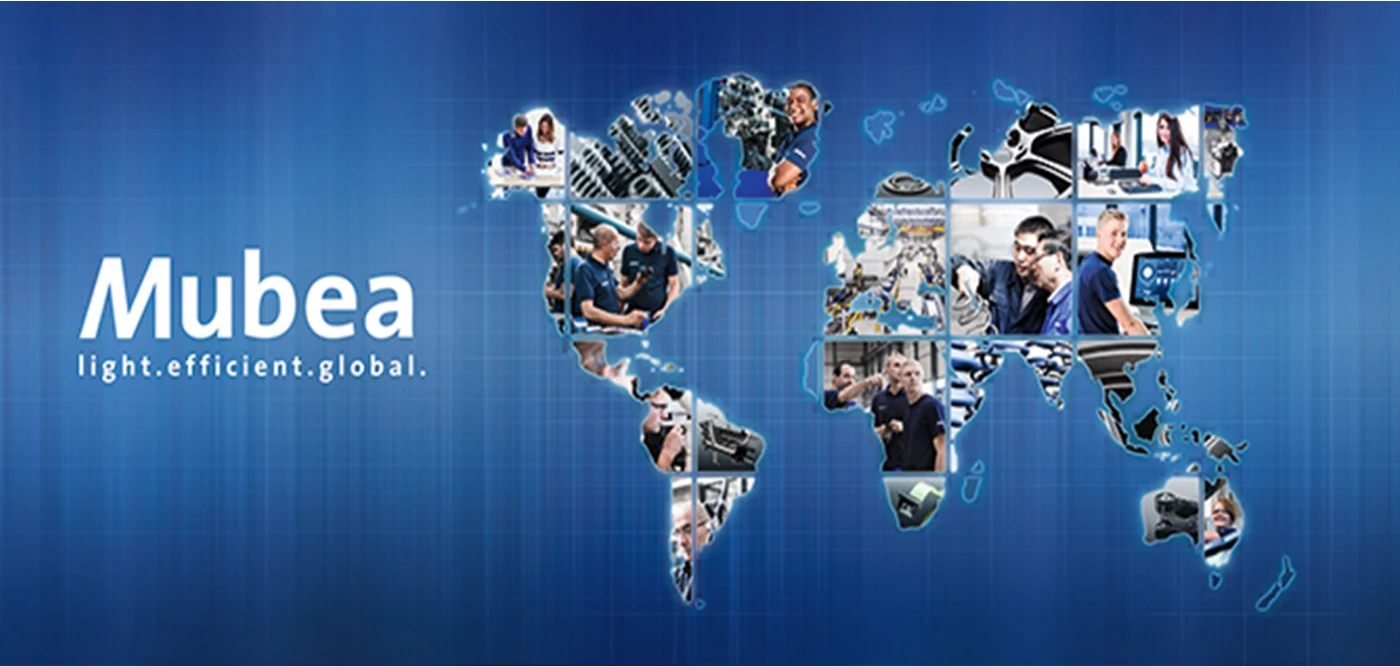
The Mubea Group contributes to the success of vehicles with conventional and electrified drivetrains with its core competence, the development and production of innovative light weight components. Furthermore, Mubea also successfully establishes their core know-how in other mobility sectors, especially in the aviation industry.
Over the decades, Mubea evolved to a top Tier 1 supplier for the automotive industry with its products for Chassis, Body and Powertrain. The product development process is as unique and tailored as the products themselves. Each Mubea design is the outcome of design explorations to find optimal compromise between all the contrasting requirements such as weight, reliability and cost.
"At Mubea we heavily rely on design optimization techniques in order to find the product configuration tailored to our customer's needs. The current design optimization process makes use of high fidelity finite element analysis (FEA). Design alternatives are automatically evaluated based on a special CAE process chain. We use metamodel-based optimization to find optimal part shapes or thickness distributions.
In this procedure, we extract key results (max. displacements, forces, etc.) as scalar values and approximate them with a model that allows us to quickly evaluate designs without the need of full-blown FEA analysis. This approach worked quite well in most cases, but with Neural Concept Shape, we are now able to
1. utilize the complete model behavior and the underlying physics and not only single key results,
2. make use of historical simulation results from old projects to reduce the model training effort further."
- Dr. Niklas Klinke, Team Lead - Engineering Tools and Methods, New Body Development
In this white paper we focus on showing how Mubea approached the following issues:
● How to predict 3D-field responses for a given data set
● How to envisage a design verification tool potentially in the hands of designers
● How to capitalize on Mubea’s accumulated knowledge and experience, in terms of stored data
The following figure shows a typical design for a battery housing:
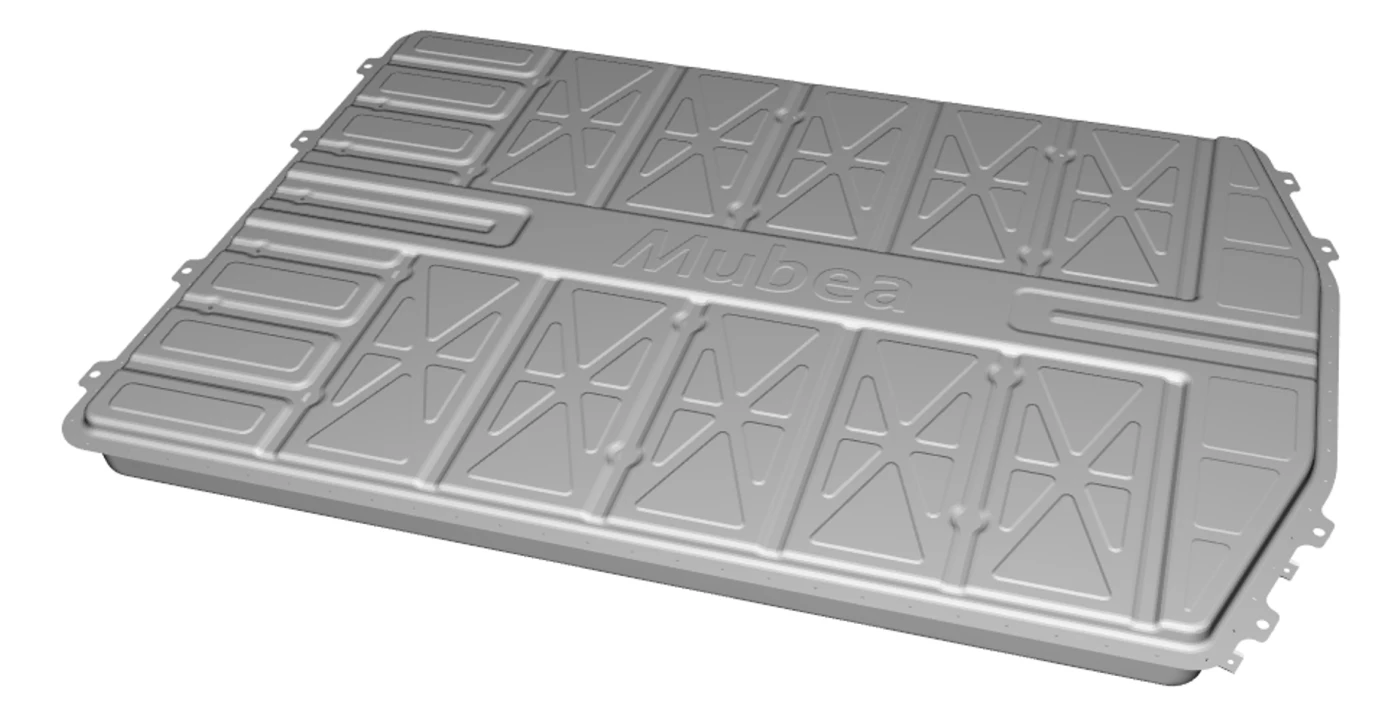
Innovation Project: The Mission
Neural Concept is on a mission to guide engineers towards radically better designs while speeding up their workflow. In this article, we show how Mubea and Neural Concept have been collaborating for the design of battery housing for EV. The solution shown in this white Paper is Neural Concept Shape (NCS), a Deep Learning approach that allows all engineers in a company to access quasi-real-time simulation, thanks to the possibility to utilize company data for CAD and 3D Simulation (CAE) to create AI-based Apps.
The mission critical aspect, for design engineers, is to verify that a certain design proposal, subject to side pole impact, guarantees the structural integrity of the battery. Several hundreds of design options, coming from requirements of lightweight and packaging, need therefore to be verified in terms of this functional requirement.
Innovation Project: The Execution
In this particular project, the task was to guarantee, that the side rails of the battery housing do not touch the battery. The common approach is to create a report template that measures either the distance between the components of the contact force.
"With our legacy approach we setup a thickness optimization where the contact force was set to be zero. The meta model quality of this approach was very bad because of the underlying non-linearity and the unsmoothness of the response near zero. Hence, we were looking for a solution that is able to predict the 3D deformation field, such that we can measure distance and collision events on predicted 3D field."
The task for the Neural Concept team was therefore that of building an AI-based App working in quasi-real-time and being able to give answers to designers while not “cutting curves” of oversimplified approaches. The most critical aspect is to be able to predict if a specific design configuration will produce battery contact during the crash simulation. A measure of confidence would be, to have no “false positives”, i.e. no case where the App predicts a contact when in reality there is no contact, and the minimum number of “false negatives”, i.e. situations when the App misses to highlight a contact situation.
Over hundreds of designs fed into the App, the underlying software Neural Concept Shape (NCS) predicted only one case of false negative and produced no false positives. This is of utmost importance and allows us to use this surrogate model to perform optimization on the design of the battery housing.
A more detailed analysis was carried out on the prediction quality of XYZ displacement and maximum force. A fair measure of the accuracy of the underlying predictive engine (NCS) is the so-called coefficient of determination R2. The surrogate model reached a very high accuracy, with the following R2-score on the test set, given in Table 1:
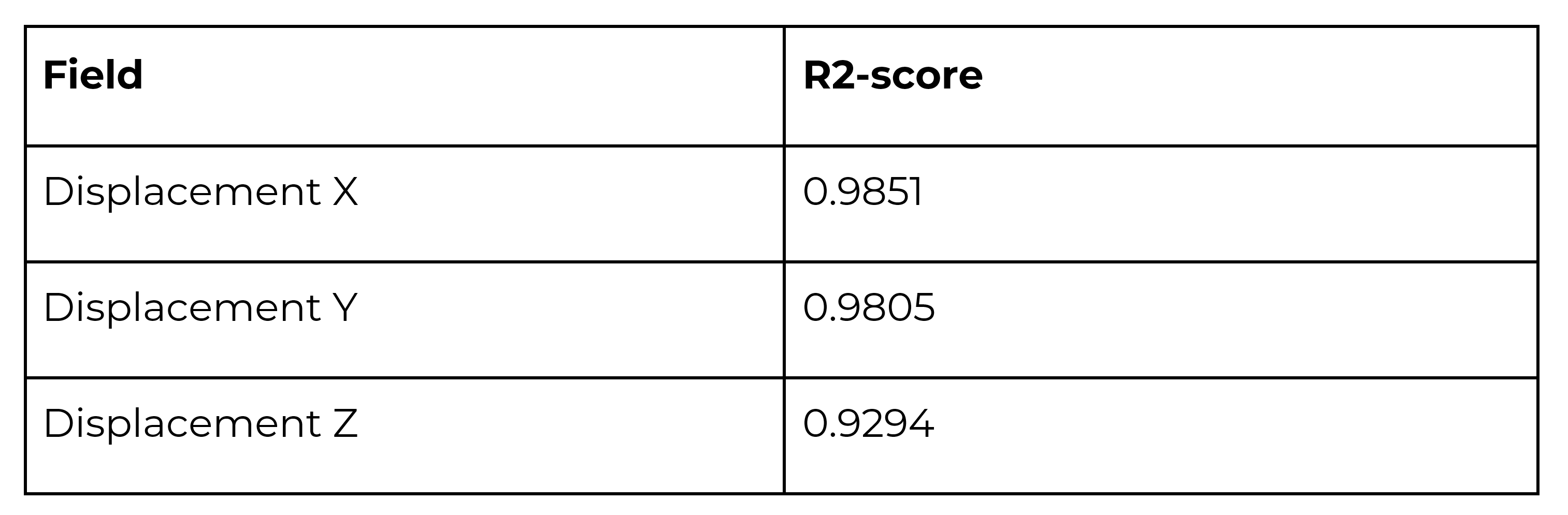
"With NCS we learned that the neural network is capable of learning the physics of the problem. The deformation response of each node tends to be much smoother than a minimum distance response and thus the result quality increases drastically. Our legacy solution showed R² of 85% with a 30 % error rate. This result opens room for further applications"
In addition to utilizing the prediction of the 3D field response solely inside of an optimization loop, NCS created a little Web-App that allows visualizing the predictions of the model without an additional solver call. Figure 2 shows the results of a prediction from NCS compared to the FEA simulation, on a test geometry:
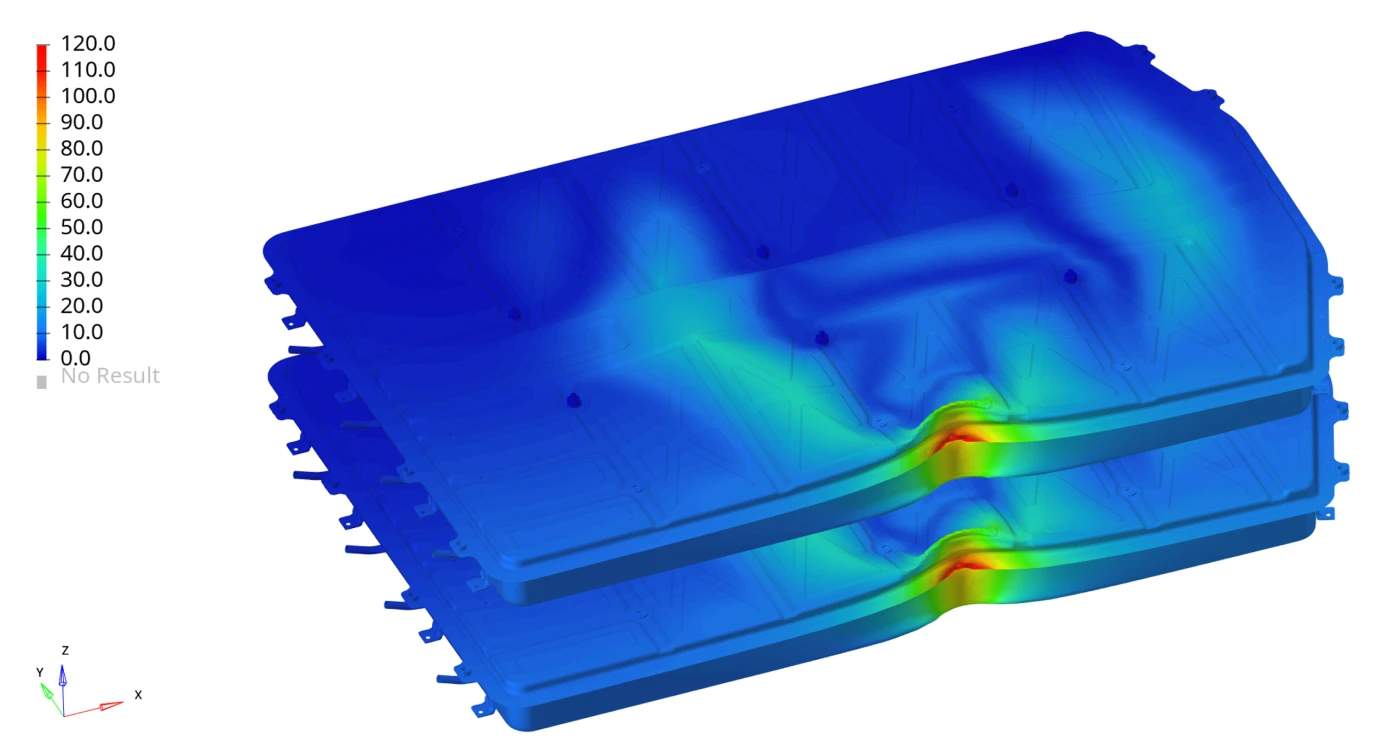
"With such a web-app we can enable the designer to get a direct feedback for a design without the need of a full-blown FEA analysis. Often the experience of the designers are crucial for achieving a well-defined and thus robust deformation behavior. Here it is of utmost importance, that the model quality is known in order to not misguide the engineer."
Reliability at the Core of the Process
As a reinforcement of the concept of design reliability of NCS: engineers can use a confidence indicator given with each prediction, to decide whether to trust a prediction made by NCS. The figure 3 shows that if the user chose an acceptance threshold to not trust about 10% of the predictions, based on this indicator, the R2 score on the 90% of predictions that are trusted, would be0.95 for the Maximum Force. Concerning the remaining 10% of predictions below the chosen acceptability threshold, if needed they could be simulated with high-fidelity CAE. An advantage is that these new simulations can be used to teach the underlying AI (Deep Learning) model how to make better predictions in the future.
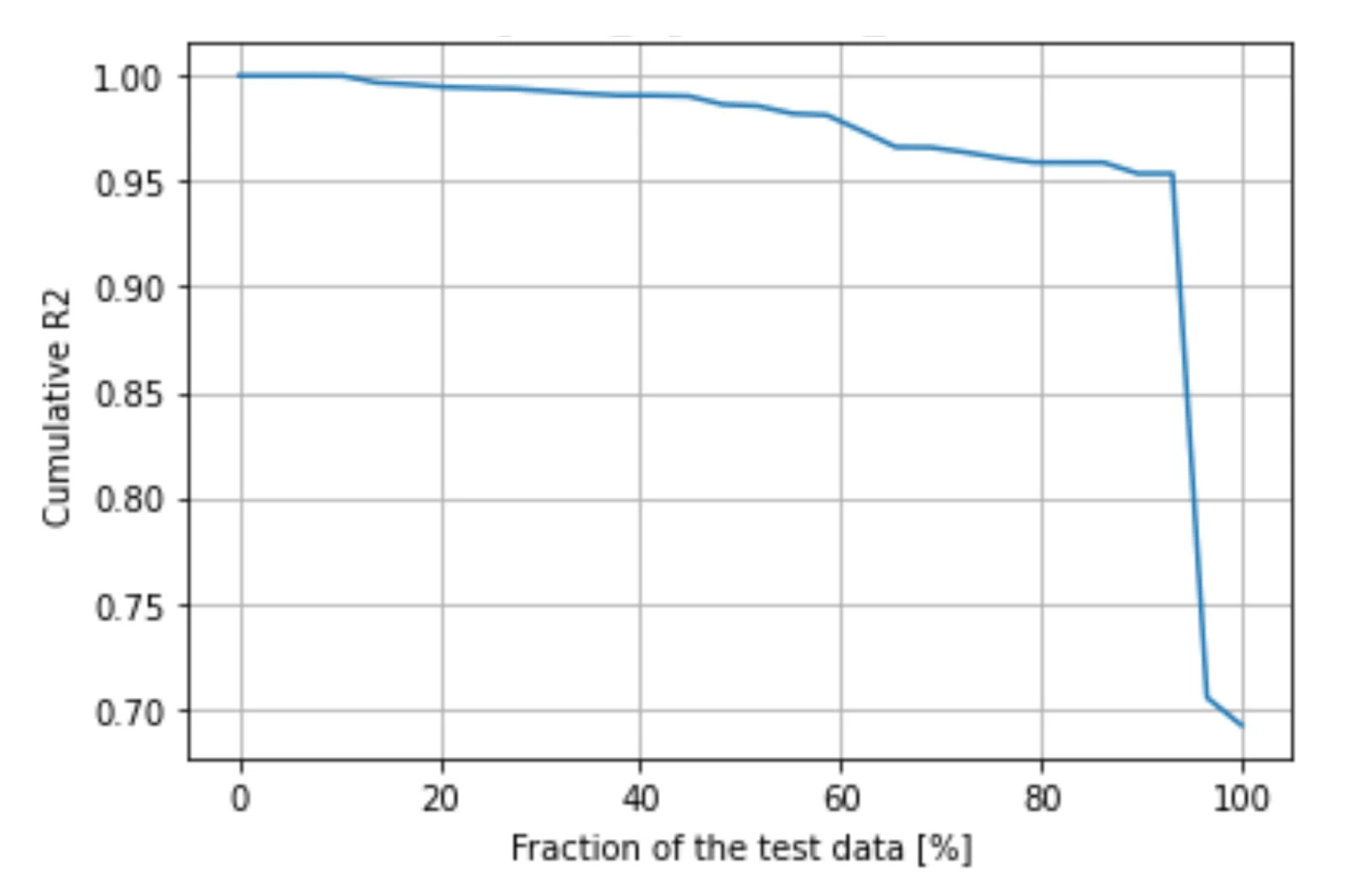
The described method was applied to a set of simulations generated in batch based on well-defined parameters. With NCS it is also possible to utilize arbitrary, historical designs to train a network. Therefore, knowledge from previous projects could be utilized to achieve optimal designs faster.
"Even though we did not evaluate this particular feature, we are highly interested into future applications. With lots of data properly stored and classified in SDM systems, we can apply this technique to achieve optimal design of known products way faster."
In Conclusion: High-Fidelity Simulation for Designers
The described process, where in the order of a second a designer without specific crash simulation skill can obtain displacement and maximum force, is a revolution with respect to the usual lead time of hours between design conception and CAE verification.
With the presented innovative approach, the objective of simulation-driven design is fulfilled. Even more promising evolutions are waiting in the future, such algorithm-driven design(optimization algorithms driving design changes).