Leveraging Engineering Data to Speed-up Design Cycles
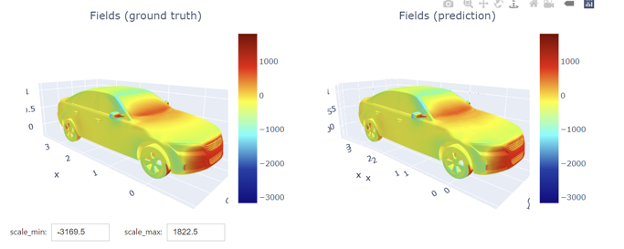
How to massively accelerate product design cycles by leveraging existing data, without compromising on product quality?
In this external car aerodynamics use-case, you will discover how using Neural Concept Shape (NCS) decreased by 97,5% the number of CFD simulations needed to design a new car, while meeting all functional requirements.
Thanks to knowledge transfer across different categories of design with only a few samples, NCS makes introducing significant changes possible while leveraging existing simulation data.
Transfer learning process
By leveraging existing data coming from a design iteration of a car concept (A), we explored a new concept (B). In this case, dataset A consists of 400 design variations with associated CFD runs, while dataset B has an additional part (a rear spoiler). In a traditional approach, another 400 CFD simulations would be required to explore the variations of dataset A on dataset B.
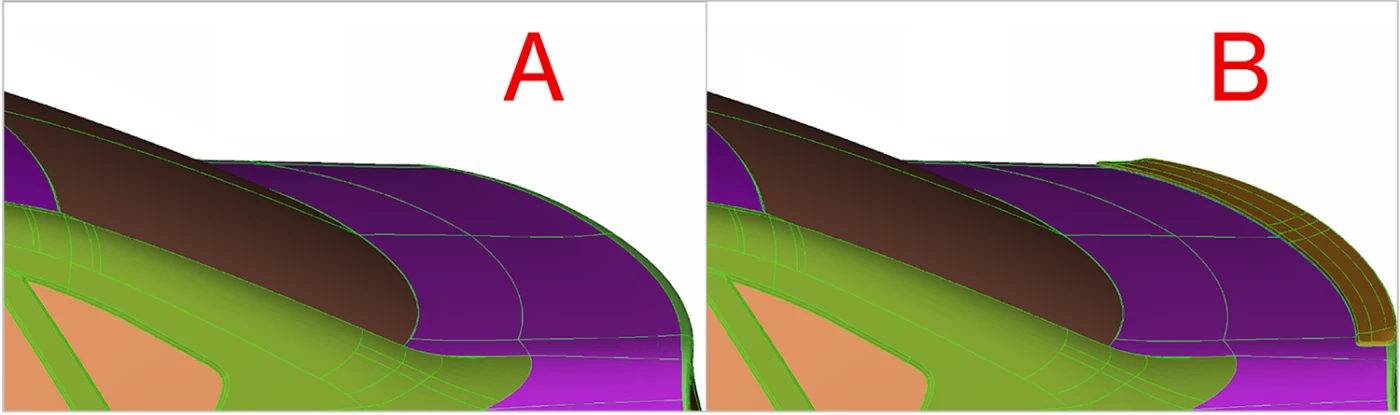
The first step is to train a surrogate model on dataset A and evaluate its performances. As shown below, the R2 score (representing the model’s ability to capture variation and predict accurately) reaches 0.965 (1 being perfect) on the CD (Drag Coefficient), which corresponds to a mean relative error of 0.6%.
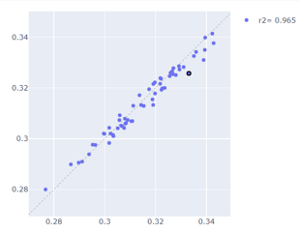
In a second step, we retrained the model using only N=10 simulations of dataset B. This is sufficient to reach an R2 of 0.945 corresponding to a mean relative error of 0.7%, which is enough for exploration.
For validation, we compared these performances using 540 CFD simulations of the dataset B.
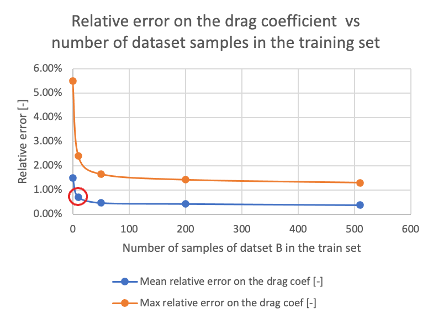
By running this sensitivity analysis, we can measure the trade-off between performance and additional (N=10, 50, 200, 540) CFD simulations of the dataset B in order to evaluate how many new samples we need for our new design. The results shows that only 10 samples of dataset B are needed to decrease relative error significantly.
Once the AI-model has been enhanced by these 10 designs of dataset B, the design engineers can explore variations in real-time, as shown in the video below.
On top of that, Neural Concept Shape (NCS) accurately predicted fields on the surface of the car as well as the volumetric fields around it, as shown below.
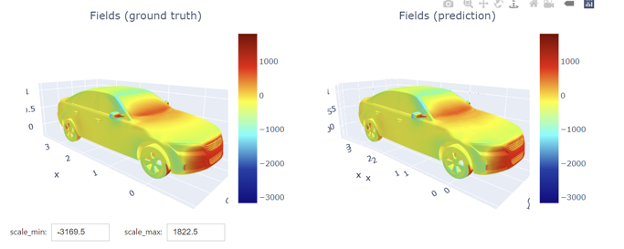
Concretely what does this mean?
Neural Concept Shape technology is able to transfer knowledge across different categories of design with only a few samples. You can introduce significant changes and still leverage existing simulations.
For example, when the CAD team wants to try macroscopic changes (such as adding a spoiler like illustrated in this use case), the CAE team doesn’t need to run all the simulations. They only need to run 5 to 10 simulations for the design engineers to be able to reliably explore the same design space in real time. Moreover, no historical data is lost.
With this improved workflow, CAD teams can iterate much faster than today, and more independently from CAE teams. Additionally, design engineers are able to create designs beyond what is normally achievable with conventional design tools, with less CFD simulations.
Data origin: Jacob, S., Mrosek, M., Othmer, C., and Köstler, H., “Deep Learning for Real-Time Aerodynamic Evaluations of Arbitrary Vehicle Shapes,” SAE Int. J. Passeng. Veh. Syst. 15(2):2022, doi:10.4271/15-15-02-0006