Innovations in Aerospace Product Design
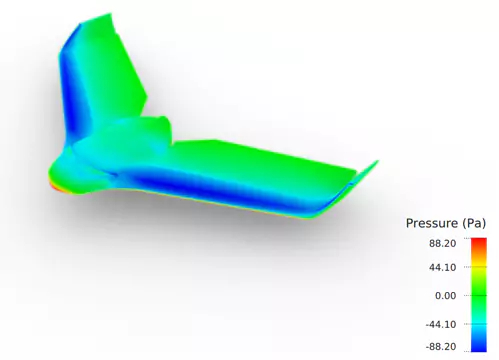
There is a "secret ingredient" for industries leading technological advancement: their product design approach, which is the focus of our article. Product design in the aerospace sector combines engineering principles with creative problem-solving to develop the aircraft and spacecraft of tomorrow.
We will explore the engineering innovations that shaped aerospace product design, such as structural analysis. We will examine how, nowadays, technologies and methodologies are helping engineers create complex aerospace components. Finally, we will shortly update you on the present and future role of AI in aerospace. AI assists engineers in meeting the challenges related to design time and cost reduction without compromising safety.
Aerospace Product Design: Yesterday, Today and Tomorrow
Since the Wright brothers first took to the skies, it's been a long way in aerospace engineering!
The design process has genuinely evolved. From simple drafting tables of the past, we are now using sophisticated software tools with ever shorter learning curves.
As an example of radically different approaches, drafting tables are now 100% replaced by computer-aided design (CAD). CAD allows aerospace engineers to create 3D models and share them instantly across their organizations.
Furthermore, Computer-aided engineering (CAE, i.e. numerical simulation) tools digest CAD files virtually, resulting in a "virtual engineering reality."
Virtual representations have degrees of precision in structural analysis with tools like NASTRAN that helped CAE gain respect in the sector and are even recognized in certification processes. These tools and procedures provide critical data at the highest required levels of fidelity for certification (FAA and international).
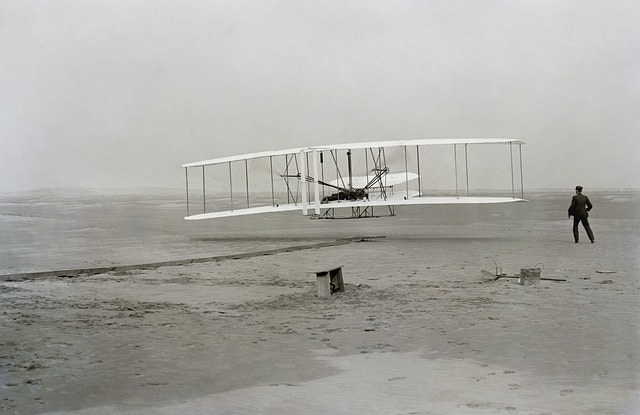
This evolution in engineering software tools has been driven by the need for ever-more reliable and performant aerospace structures. Beyond structures, engineering performance includes reduced fuel consumption, for instance, to guarantee the desired autonomy range of crewless vehicles (UAVs).
Aerospace product engineers always search for cutting-edge technologies to create tomorrow's aircraft. This search ranges from the widespread adoption of advanced composite materials to the integration of CAE and, lately, AI in the design process. For instance, with upfront aerodynamics simulation, aerodynamic performance can be evaluated way before any prototype is built. At the same time, the degree of precision required in aerospace engineering ("failure is not an option") requires that every new tool in aerospace engineering be validated.
Thus, aerospace engineering evolves rapidly, with new challenges and opportunities emerging as technology advances since validation is not a whim, but it's a must!
As we look to the future, aerospace engineering will be crucial in pushing the boundaries of what's possible in the skies... and beyond!
Challenges in Innovation: Advanced Materials in Aerospace Design
One of the most interesting developments in aerospace product design has been the introduction of advanced composite materials. Advanced composites have revolutionized the way engineers approach design and aerospace parts manufacturing. Advanced composites offer a unique combination of weight and durability. This makes them ideal for aerospace structures.
Lightweight Advanced Composites
Carbon fiber-reinforced polymers consist of carbon fibers embedded in a polymer matrix. They are perhaps the most advanced composite materials in aerospace engineering.
What's the outcome? A material that is stronger than steel but much lighter!
Unsurprisingly, aerospace companies increasingly use carbon fiber-reinforced polymers to construct aircraft fuselages and wings. These advanced composite materials have reduced aircraft weight.
High-Strength Alloys
Advanced composite materials have gained prominence. However, alloys are also important in aerospace. Titanium alloys offer an excellent strength-to-weight ratio and resistance to corrosion and fatigue. These make them ideal for aircraft engines and other elements subjected to typically extreme temperatures and stresses. We thus employ advanced composite materials and advanced alloys to optimize parts' performance and structural integrity.
Digital Twins and Simulation in Aerospace Engineering
Another innovation in aerospace product design is digital twins. A digital twin is a virtual representation of a physical product or system. In aerospace engineering, digital twins are increasingly used to model entire aircraft. This allows us to test and optimize designs before a single physical component goes to production.
The use of digital twins offers several benefits, both in design and production.
Aerospace engineers can identify potential issues in the design process upfront, reducing the need for costly physical prototypes and accelerating development cycles. Simulating under various conditions, we can optimize aerodynamics and structural integrity designs.
Downstream of design, digital twins enable aerospace companies to predict maintenance needs and optimize aircraft performance throughout their lifecycles. This technology can revolutionize aircraft maintenance practices. The outcome? Improved safety and reduced downtime.
Additive Manufacturing (3D Printing) for the Aerospace Industry
Additive manufacturing, known as "3D Printing", is a game-changing technology in product design. It can create components that would be difficult or just impossible for traditional manufacturing techniques.
In aerospace engineering, additive manufacturing can create virtually everything, from small brackets to large structural elements. Advantages over conventional production processes are, for instance:
- More Design Freedom: Additive manufacturing has fewer constraints in creating geometries that can optimize the performance of components
- Material Efficiency: Additive manufacturing is a near-net-shape approach that produces parts that require minimal post-processing, reducing material waste
- Quicker Prototyping: 3D Printing can rapidly produce prototypes for testing and validation, accelerating the design process.
AI and ML in Aerospace Product Design
Artificial Intelligence (AI) and Machine Learning (ML) are increasingly present in the design processes. These technologies help us to streamline development, for instance:
- predicting performance via surrogates of simulation tools, acting in almost real-time
- optimizing designs with generative design, reaching unexplored regions of the design space
AI impacts aerospace structures in optimization.
Optimization means that:
first, AI analyzes datasets collected and stored from simulation and real-world test experiences over the last few years;
Second, AI algorithms suggest design modifications that, for instance, improve aerodynamics or enhance structural integrity.
What is the secret of AI? Its algorithms can predict the performance of systems or subsystems by recycling historical data. These algorithms can learn to predict how a component will behave in real-world scenarios. This predictive capability helps engineers identify potential issues early in the design process.
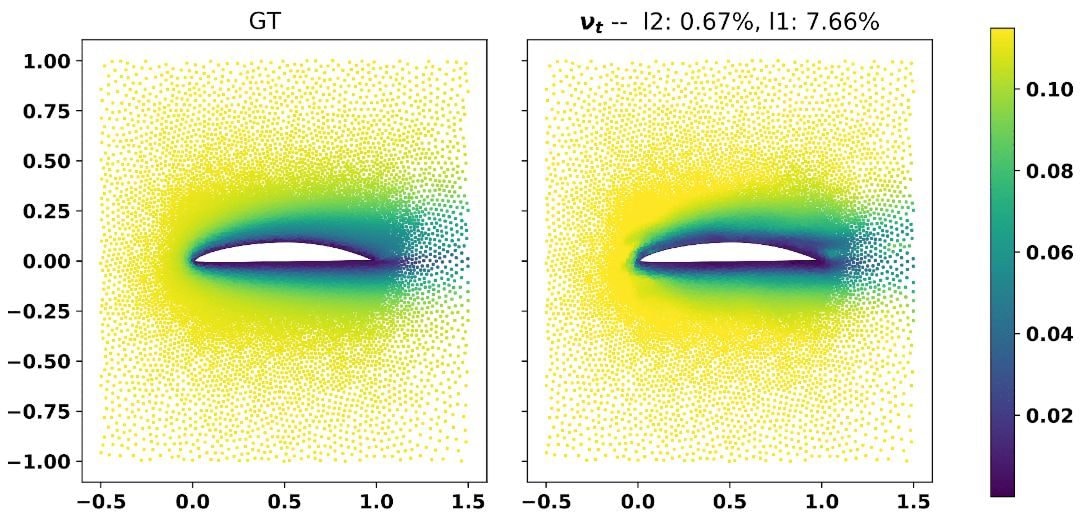
Furthermore, AI and ML are crucial in automating certain aspects of the design process. AI-powered generative design tools can algorithmically interact with CAD to create optimized designs based on specified parameters and constraints. This saves time and allows us to explore a broader range of design possibilities.
Integrating AI and ML into design for the aerospace industry is in its early stages, but the potential benefits are enormous. These technologies will likely become indispensable to the engineer's toolkit as they evolve in the next few years (or maybe months!).
Aerodynamic Innovations in the Aerospace Industry
Advancements in aerodynamic design have been a constant driver of innovation in the aerospace industry. Pursuing more efficient and performant aircraft has led to the development of sophisticated tools and methodologies for optimizing aerodynamic properties.
One of the most noteworthy innovations in this area has been the widespread adoption of Computational Fluid Dynamics (CFD) in design in the aerospace industry. CFD allows us to simulate airflow around an aircraft, providing insights into its aerodynamics. This capability has changed our approach to aerodynamic design, enabling us to iterate designs more quickly and cost-effectively than with physical testing.
New aerodynamic concepts have emerged to improve aircraft efficiency. Developing winglets—small, vertical extensions at the tips of wings—has improved fuel efficiency by reducing drag. Similarly, exploring laminar flow control techniques promises to reduce drag further and improve aircraft performance.
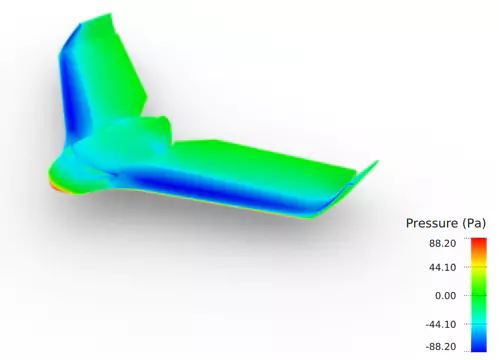
Sustainable Aerospace Design
As environmental concerns become increasingly pressing, the aerospace industry emphasizes sustainable design practices. This focus on sustainability is driving innovations in several aerospace industry design areas.
Fuel Efficiency and Reduced Emissions
Improving fuel efficiency and reducing emissions are top priorities for aerospace companies.
This has led to:
- the development of more efficient engines,
- the use of lightweight materials,
- and the optimization of designs for better aerodynamics.
Advanced composite materials play a crucial role in this effort, allowing for the creation of lighter aircraft that consume less fuel.
Aerospace engineers are also exploring alternative propulsion technologies, such as electric and hybrid-electric systems, to reduce aviation's environmental impact further.
While these technologies are still in the early stages of development for large commercial aircraft, they show promising potential for reducing emissions and dependence on fossil fuels.
Recyclable Materials
The use of recyclable materials in design is gaining traction as the aerospace industry seeks to reduce waste and improve the lifecycle sustainability of their products. This includes the development of recyclable advanced composite materials. Another example is the exploration of bio-based materials for specific applications.
The aerospace industry is also improving the recyclability of existing materials used in construction. This means designing with end-of-life considerations in mind. The end-of-life approach will make disassembling and recycling material easier at the end of their service life.
Eco-Friendly Design Practices
Beyond materials and propulsion, companies implement eco-friendly design practices throughout the product lifecycle. This includes optimizing manufacturing to reduce energy consumption and waste. The objective is to design for easier maintenance and repair to extend the product lifespan. Incorporating lifecycle analysis into design helps to minimize environmental impact.
Challenges and Future Trends
Despite the advancements in aerospace product design, the industry still faces numerous challenges.
One of the most pressing is balancing innovation with the stringent safety and certification requirements that govern the aerospace industry.
New manufacturing processes and design methodologies must undergo rigorous testing and validation before being implemented in commercial aircraft.
Another challenge lies in managing the increasing complexity of aerospace systems.
Ensuring the reliability and compatibility of all components becomes more challenging. Aircraft become more sophisticated, with more integrated electronic and software systems. Engineers in the aerospace industry must navigate this complexity. At the same time, they must still deliver products that meet strict performance and cost requirements.
Future Trends
In the future, several trends will likely shape the field of design.
Trend 1 - Automation: Increased automation in design and manufacturing processes, driven by advancements in AI and robotics.
Trend 2 - Integration: Greater integration of sustainability considerations into all aspects of product design.
Trend 3 - Propulsion: The development of new propulsion technologies, including electric and hydrogen-powered systems.
Trend 4—Lighter, stronger: Continued development in materials science is creating aerospace materials that are lighter but also stronger and more durable.
Trend 5—New configurations: Advances in materials and manufacturing technologies have enabled the emergence of new aircraft configurations, such as blended wing body designs.
Engineers will continually adapt and innovate to meet the industry's changing demands and contribute to the above trends.