How to Calculate Heat Dissipation to Prevent Overheating
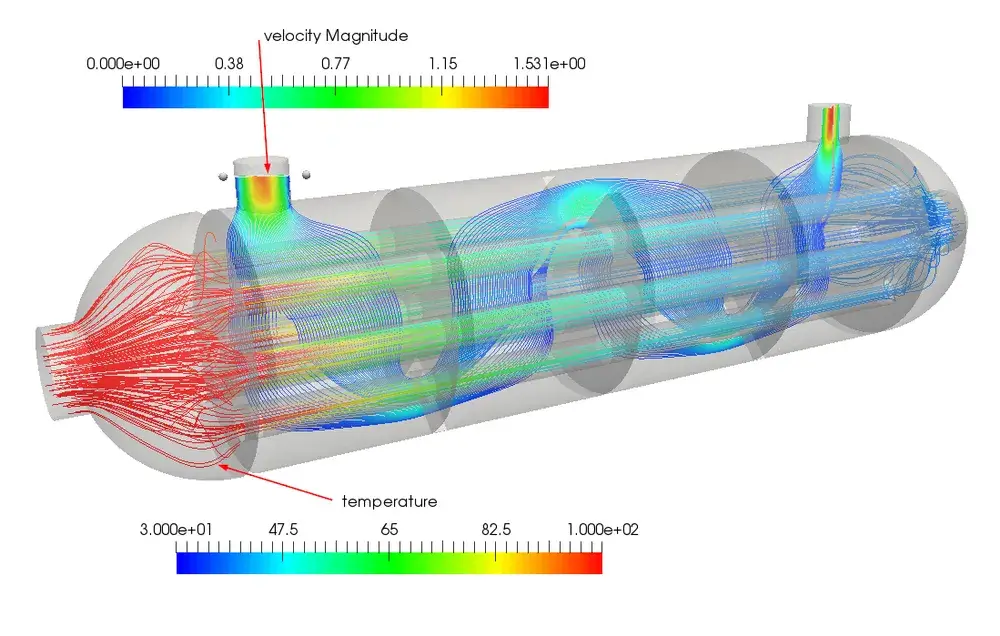
Engineering systems often generate heat, which can cause damage to their components when not adequately dissipated.
In this article, we will delve into the concept of heat dissipation and explore practical formulas that aid in the calculation of heat dissipated and power dissipated. By understanding overall system calculations or detailed 3D simulations, engineers can effectively manage heat generation, implement appropriate cooling measures, and safeguard the performance and longevity of electronic systems.
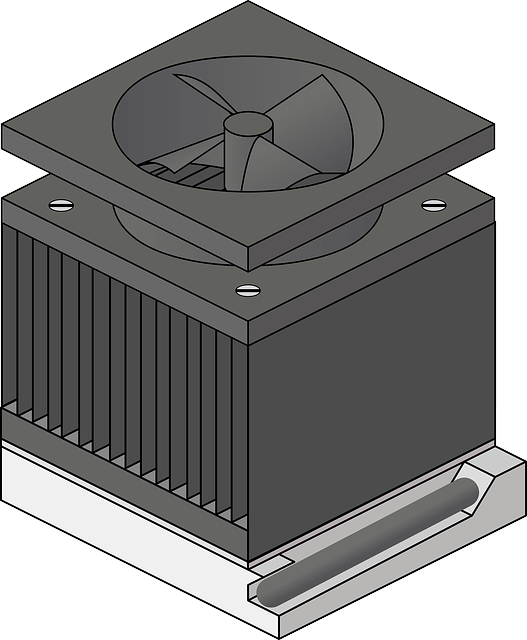
One critical example is the cooling of artificial satellites, where efficient heat dissipation is crucial for mission success. Without an effective satellite cooling system design, the electronic components could fail, compromising the entire mission. The same issue applies to all electronic devices. This emphasizes the importance of dissipating heat to maintain optimal operating conditions and prevent failures.
Another example of the need for heat dissipation is the switch-gear i.e., the electrical equipment used to control and protect power systems. It typically includes circuit breakers, disconnect switches, and fuses. Inadequate heat dissipation in the system can lead to overheating, which can cause various problems. Excessive heat can deteriorate insulation materials, reducing their lifespan and potentially leading to insulation breakdown or flashovers. Overheating can also impact the mechanical integrity of switch-gear components, resulting in malfunctions or failures.
To illustrate the "What-Why-How" of the whole process from heat generation to heat dissipation, we will start with the example of an electric power supply.
What Is Creating Heat Generation?
In the case of electric power supplies, various components are typically employed, such as transformers, rectifiers, capacitors, and semiconductors. These components generate heat due to their internal resistance, switching losses, and power dissipation.
Why Should Heat Be Dissipated?
If the heat generated is not adequately dissipated, it can lead to temperature rise, thermal stress, and potential damage to the system and its surrounding components. Effective heat dissipation is essential to maintain the system temperature within safe operating limits, ensure reliability and efficiency, and extend its lifespan. More will be explained in the next Thermodynamics section.
How Can Heat Be Dissipated?
Design engineers employ various cooling techniques and design considerations to optimize heat exchange. Let us review a few basic practical strategies for optimal heat dissipation:
- Heat Sinks: They're commonly used in power supplies to increase surface area for heat transfer. These metallic structures help dissipate heat by increasing the contact area with the surrounding air, enhancing convective heat transfer.
- Fans and Ventilation Openings: They can facilitate airflow and enhance convective heat dissipation by increasing the mass flow rate of air or any other cooling fluid, thereby carrying away the heat generated by the components. The mass flow rate refers to the amount of fluid (air) passing through a specific area per unit of time. By utilizing fans and ventilation openings, the mass flow rate of air can be increased, leading to more efficient heat transfer. The higher the mass flow rate, the greater the heat that can be carried away from the components. This increased airflow helps to reduce the temperature of the components and maintain them within their safe operating limits. By actively promoting a higher mass flow rate through the system, fans and ventilation openings play a crucial role in preventing overheating and ensuring optimal performance of electronic devices.
- Materials: Using thermal interface materials, such as thermal pads or compounds, helps improve thermal conductivity between heat-generating components and heat sinks, enhancing heat dissipation efficiency.
- Specific Heat: When a component or system generates heat, the specific heat of the surrounding materials affects how quickly and efficiently the heat is dispersed or transferred to the environment. Specific heat allows engineers to calculate the amount of heat energy required to increase the temperature of a substance, as well as the amount of heat energy that can be released when the temperature decreases. Engineers can select appropriate materials for heat sinks, heat exchangers, or other cooling components to optimize heat dissipation.
- Enclosure Design: The design of an enclosure can also impact heat dissipation. Proper ventilation, strategically placed vents, and heat-conductive materials can aid in dissipating heat effectively.
The Laws of Thermodynamics
Effective heat dissipation is important in electronic devices. Think of computers and smartphones. The same is true in industrial applications like power plants and manufacturing facilities. Heat dissipation is related to the principles of energy conservation and the increase of entropy. Those principles are outlined in the first and second laws of thermodynamics.
The First Law of Thermodynamics
The first law of thermodynamics states that energy cannot be created or destroyed; it can only be transferred or converted from one form to another. In the case of heat dissipation, the first law emphasizes that the heat energy generated by a system must be transferred or dissipated to the surrounding environment to maintain energy conservation.
The Second Law of Thermodynamics and Entropy
The second law states that in any energy transfer or conversion, the total entropy of an isolated system will either remain constant or increase.
Heat dissipation is a direct application of the second law of thermodynamics, which focuses on entropy and the direction of energy flow. The heat generated within a system is sensitive to temperature differences and tends to flow from higher to lower temperature areas, seeking equilibrium. This natural tendency to reach thermal equilibrium represents the increase in entropy as heat energy spreads out and becomes more disordered. Effective heat dissipation mechanisms facilitate this process by allowing heat energy to flow from the source (higher temperature) to the surrounding environment (lower temperature), thereby increasing entropy and maintaining the overall system balance.
Heat Dissipation Formulas
For specific situations such as electronic devices, total heat dissipation can be expressed with simplified calculation formulas. Applications can be integrated circuits (ICs), transistors, or microprocessors. With this calculation, engineers can determine the amount of heat generated and design cooling systems accordingly. This helps prevent overheating and ensures the reliable operation of electronic devices.
Heat Dissipation Formula (Specific Examples for Electronic Engineers)
Let us now explore an example of a couple of practical formulas that are commonly used by electronic engineers to calculate heat dissipation in electronic devices:
How to Calculate Heat Dissipation using Thermal Resistance
This formula calculates the heat dissipation (in W) based on the temperature difference between the junction and ambient, divided by the thermal resistance of the component:
Q = (Tⱼ - Tₐ) / Rₜₕ
In this formula:
- Tⱼ refers to the junction temperature of the component, while Tₐ represents the ambient temperature (°C)
- Rₜₕ is the thermal resistance of the component, measured in degrees Celsius per watt (°C/W).
How to Calculate the Heat Dissipation using Power and Thermal Resistance
This formula calculates how much heat is dissipated directly based on the power consumption P (W) and thermal resistance of the component Rₜₕ:
Q = P × Rₜₕ
Heat Dissipation Calculations: CAE Simulation & AI
The previous lumped formulas are useful for the overall sizing of components, but they are “lumped" (zero-dimensional) overall balances of a system in terms of details of what is happening in specific locations in space. Therefore, for detailed heat dissipation computations, CAE (Computer-Aided Engineering) simulation is essential in analyzing and optimizing the thermal performance of various systems and components in the fullness of 3D detail, coupled to digital CAD (Computer-Aided Design) representations of the component shape.
Whether it's a satellite panel, electronic device, or industrial equipment, understanding how heat is dissipated and managed is essential for ensuring reliable operation and preventing potential issues such as overheating.
The issues with traditional CAE approaches are an investment in hardware, skills required for engineers to run the application software, and wait time to get simulation results.
A solution aiming to increase efficiency in the design department was to train an AI-based simulation surrogate for thermal transfer in satellite panels. The solution was integrated within a CAD platform so that designers could modify geometries and get thermal simulation results in real-time during modifications.

The traditional simulations used to take over 20 minutes to run. Now with Deep Learning technology, results can be obtained in just a few tens of milliseconds. This means to multiply the number of possible design changes by orders of magnitude.
In conclusion: exciting times lie ahead, as we uncover the effectiveness of deep learning in revolutionizing thermal transfer simulations and heat dissipation!