Predictive Engineering Analytics: Overview & Benefits
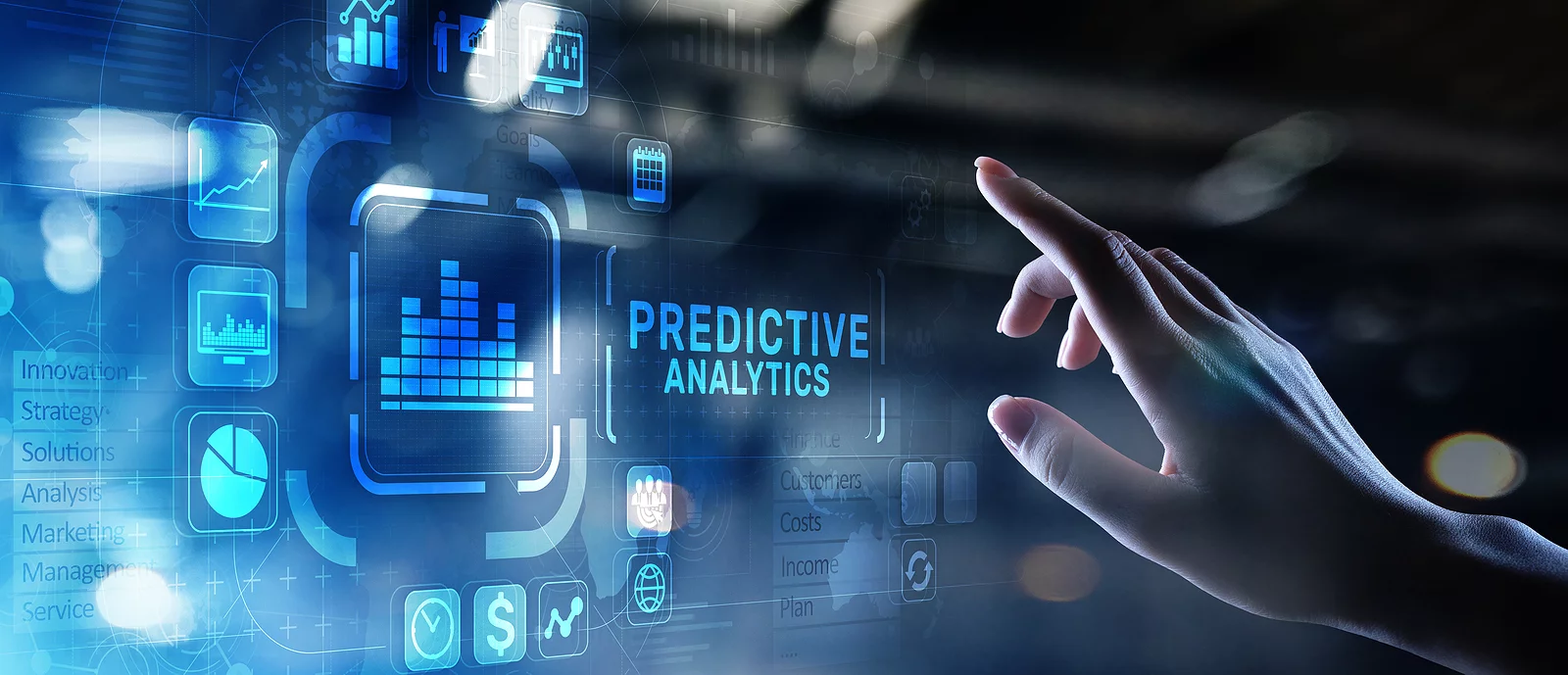
AI predictive engineering analytics combines data analytics with predictive models. Predictive models are known to be active in applications ranging from consumer behavior to weather pattern forecasts (Fig. 1). Is predictive analytics the same as computer-aided engineering? How are the two related? Follow us in the article to learn more!
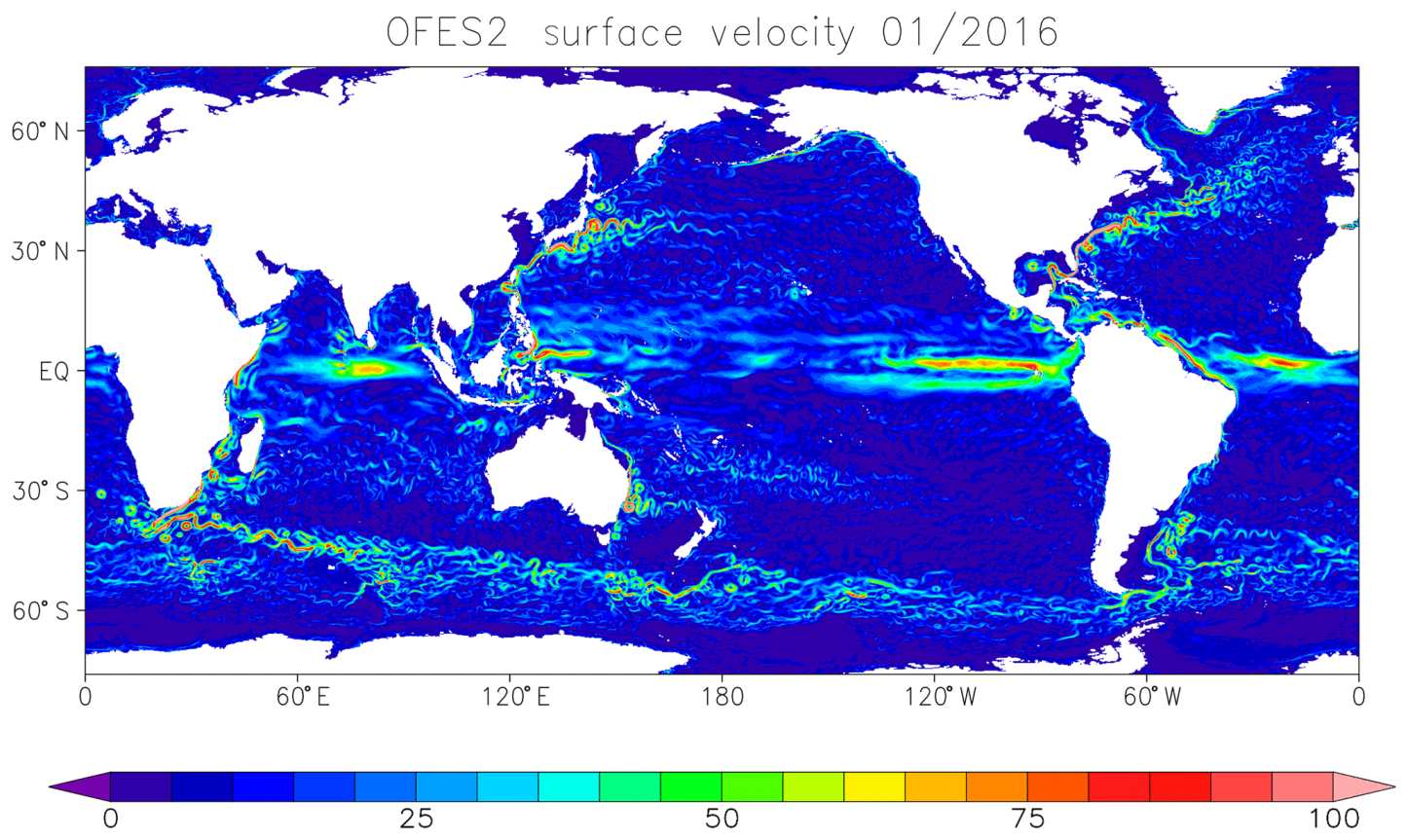
Data analytics involves using data to provide insights and support decisions. For instance, Large language models are popular AI systems that excel in "human-like" conversations based on data analytics. As another example, Digital Twins are (ideally) replicas of real-world physical products, systems, or processes used in predictive maintenance that are claimed to replicate reality because of predictive analytics capabilities.
We will focus on predictive engineering analytics within the above broad predictive analytics concepts. We will introduce predictive engineering driven by physics to appreciate the concept in its historical development and move on to present AI systems-driven product development.

As in the example in Fig. (2), we see the full potential of predictive engineering analytics, not only predicting, but also proactively (generatively) minimizing the aerodynamics of a shape in a constrained optimization case.
The simple example can be extended to more complex products such as today's products: the initial prompt of the actual product leads to product development via predictive engineering analytics. The potential risk of failure with this technology of low accuracy prediction can be prevented by a combination (or "sync" or "transfer learning") with high-fidelity tools, leading to success in research and concept development and thus minimizing the risk of lack of accuracy.
Predictive Engineering Analytics Vs General-Purpose Analytics
Engineering of complex systems traditionally leveraged expensive and lengthy physical testing methods - see Fig (3), such as building a prototype, sending it to the test lab, and receiving the results.
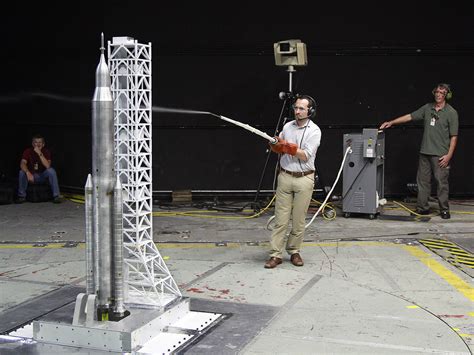
Computer-aided engineering (CAE) simulation has become more popular than the physical testing cycle. CAE answers continuous market challenges due to cost-effectiveness or compliance with environmental restrictions, requiring innovation with ever-changing solutions to adapt products to markets. In practice, changes are made to CAD or CAID, as in Fig. (4) and Fig. (5).
Manufacturing methods or product development with new concepts cannot rely on the simple reproduction or "analysis" of the products designed in the past; instead, they must be oriented to seek new solutions for today's products.
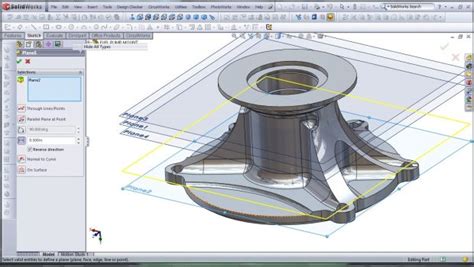
Predictive engineering analytics tools are becoming useful for complex product development and test phases. AI product design methodologies add data analytics capabilities to exploit the accumulation of simulation data. Simulation and simulation engineers will not "disappear" since users of AI apps need them to keep AI accuracy in sync with physics-based simulation. This vital layer of implementation may be invisible to end-users concerned with the final application.
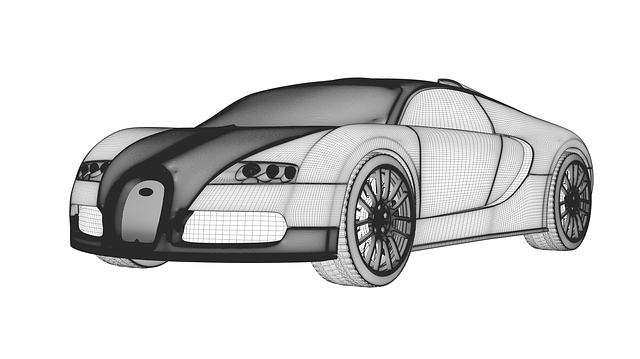
Physics-Based and Data-Driven Technologies
Before artificial intelligence, we could predict future events relevant to engineering. Examples are a car's response to crashworthiness testing or the durability of parts with mechanical functions via physical models at the core of numerical analysis solvers. Solvers give quantitative answers based on inputs such as an object's CAD (Fig. (6)), boundary conditions, and materials.
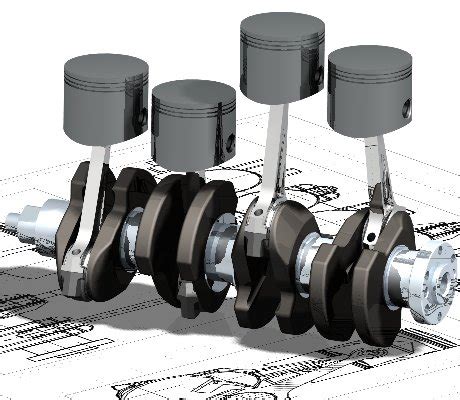
Thus, before the actual product (Fig. (7)) or even before prototypes and testing, virtual engineering gave increasingly accurate insights into product development, from pioneering FEA in the '60s to mass deployment of CFD in the 2000s. This revolution was supported by independent software vendors, who recently (2016-2024) were acquired by larger companies, mainly in the electronics design automation (EDA) or energy and electrification sectors.
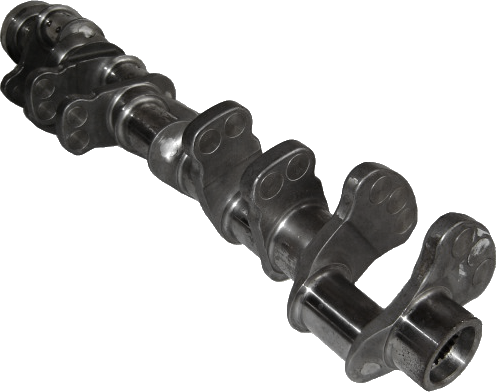
The next image shows how computer-aided engineering generates a failure prediction via simulation (in minutes or hours) starting from CAD (with info on materials and loads). In Fig. (8), colors indicate the stress 3D map based on numerical analysis, allowing engineers to predict if the component will fail.
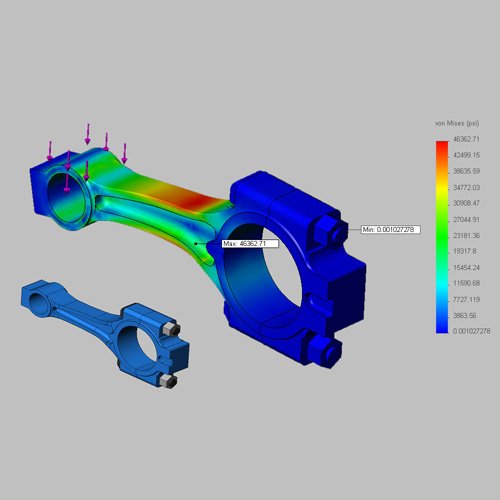
Thus, physics-based simulations use physical models of solid or fluid mechanics to accurately give engineers predictive engineering analytics insights.
Learning high-fidelity simulation tools, as in Fig. (9), is challenging for product design engineers because of the foundations needed in the software's physical modeling. Also, the more detailed the simulation models, the heavier the hardware resources required. Thus, we have issues with greater confidence, which is needed, combined with response time.
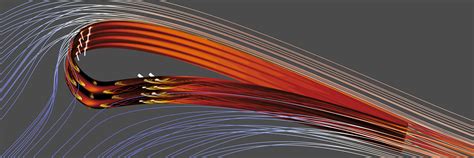
This is why 3D simulation tools are generally not true "digital twins" as in Fig. (10) —the simulation solver is orders of magnitude slower than in real life. This is not an engineering concept and design issue, but it can bottleneck the application to real-life events. Some vendors claim that sparse collections of offline 3D simulations represent digital twins; maybe this is not real-time coupling, but let's leave them at that.
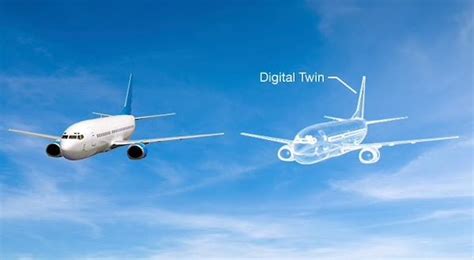
AI-based predictive engineering analytics can tackle complex systems while having rapid response time. Because they are in sync with data, we will see how these new technologies can be used more confidently than in the past. The "true" answer, as far as AI knows, is always the ground truth data used for the machine learning itself.
What Is Predictive AI?
Predictive AI is a branch of Artificial Intelligence that leverages historical data points to create predictive models that help humans identify patterns and trends in data. The most evolved declension is Deep Learning, based on layers of artificial neural networks, as in Fig. (11), that learn via the phases of train and testing.

Predictive modeling AI is useful when data are available, making it difficult or impossible for humans to handle raw data and find patterns. A data-driven predictive model benefits situations with high uncertainty or where outcomes are difficult to predict based on rules or knowledge.
What Is Predictive Engineering Analytics?
In general, a data-driven prediction is based either on historical data, analytics of physical simulation models from simulation platforms, or patterns and trends found in test laboratories or during production and test operations. Predictive engineering analytics leverages the analysis of simulation and testing data with data science methods exploiting advances in artificial intelligence.
The Phases of Predictive Engineering Analytics
Let us follow the phases of development: Data management, learning, and deployment, which characterize deep learning projects.
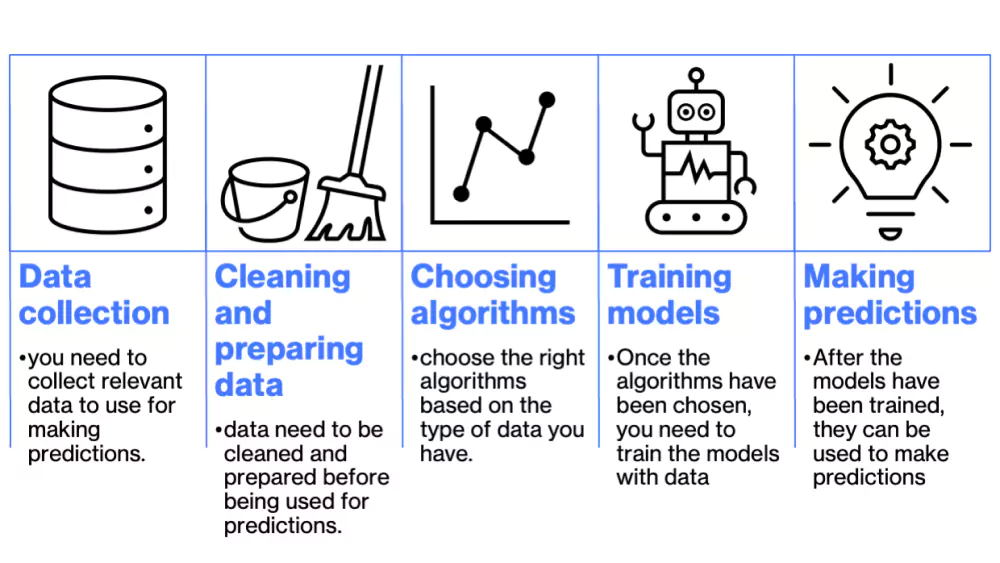
Phase 1: Data Collection for Predictive Engineering Analytics
The first stage of predictive engineering analytics is data collection. Data can range from physics-based simulation software datasets such as Computer-Aided Engineering to data from physical testing or data from manufacturing. Once companies adopt the concept, this data analysis stage is straightforward. Imagine every physics-based simulation software operating; intelligent reporting produces data ready to be recycled by AI.
We cautiously inserted a data cleaning and algorithm tuning phase in the above graph - Fig. (12).
Phase 2: (Deep) Learning from Data
The second stage of predictive engineering analytics is still preparatory. It involves implementing data analytics and learning from data—CAD with CAE or other sources (experimental test). A branch of AI called deep learning is used to learn how to predict future events without being explicitly programmed, like in traditional simulation software.
Phase 3: Deployment into Actionable Software for Predictive Engineering Analytics
The third stage of the predictive engineering analytics approach is deployment. It represents the external or executable layer for end users. With 3D Deep Learning technology, as in Fig. (13), software with predictive analytics capability can emulate traditional system simulation software but with greater ease of use and unprecedented response time. This gives designers greater confidence than using rules of thumb. The crucial role of simulation experts as "real world behavior" or "ground truth" should never be forgotten, though!
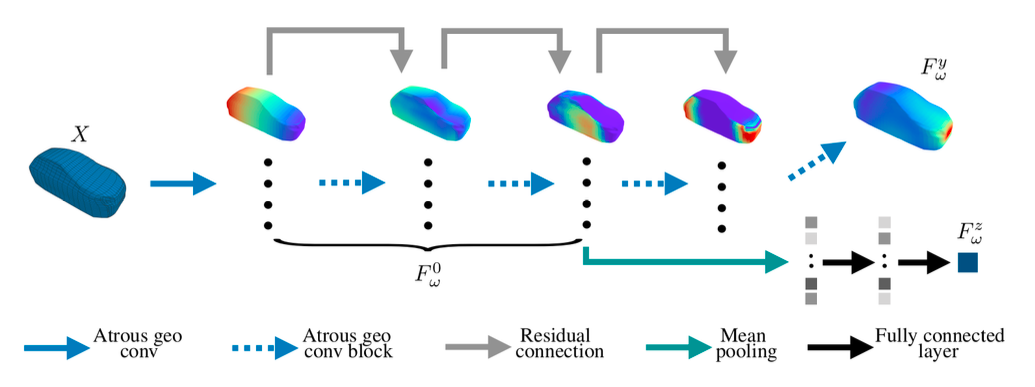
Benefits of Predictive Engineering Analytics
Predictive engineering analytics driven by data provides accurate and fast predictions about future outcomes.
Thus, predictive engineering analytics can help make better decisions in several sectors, from electronics to automotive.
Automating many processes through predictive engineering analytics can support a broader and deeper exploration of the design space. When both customers and suppliers are engineers, predictive engineering analytics can assist customers' needs by facilitating interactive discussions and reducing meeting iterations.
Thus, predictive analytics models streamline design processes in automotive or electronics engineering. With predictive modeling, engineers can make decisions based on physics-based simulations and data. Machine learning has evolved to create 3D real-time surrogates of High-Fidelity simulation software.
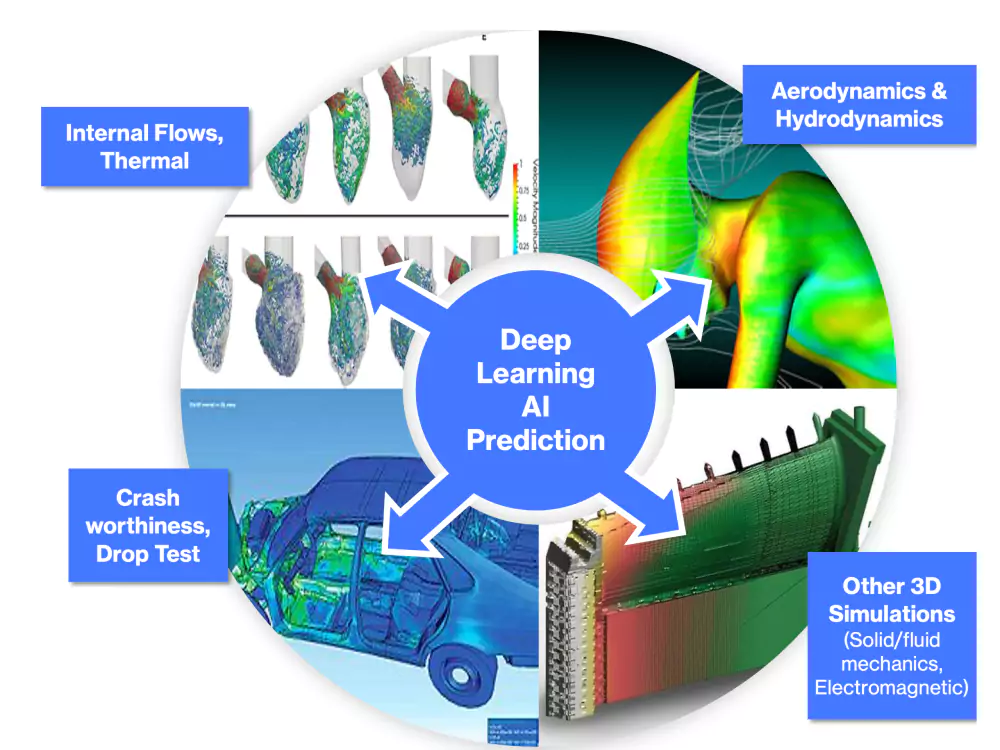
AI-driven predictive engineering analytics uses data from various sources, as in Fig. (14), including sensors, historical data collection, and data analysis, to create models that can forecast events. These models can be used to identify trends and optimize processes in design and manufacturing methods.
With AI-driven predictive engineering analytics, engineers use predictive models to create shapes and materials for optimal aerodynamics, heat transfer, or crashworthiness test performance.
Systems-Driven Product Development - Use Cases of Predictive Engineering Analytics
Product development can benefit with greater confidence from insights provided by predictive engineering analytics.
System simulation is highly developed in the automotive industry and covers mechanical functions to aerodynamics applications, as in Fig. (15). Hundreds of data points are stored and retrievable via PLM software.
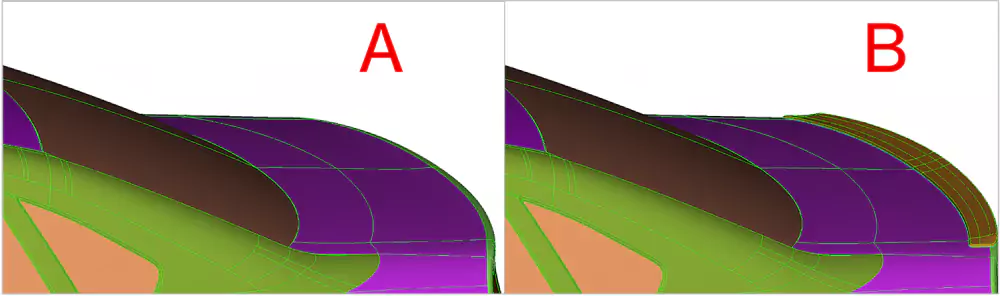
System simulation often needs to produce performance maps, such as Fig. (15) in aerospace. With AI, engineers can determine the effect of hundreds of variations of inputs within seconds.
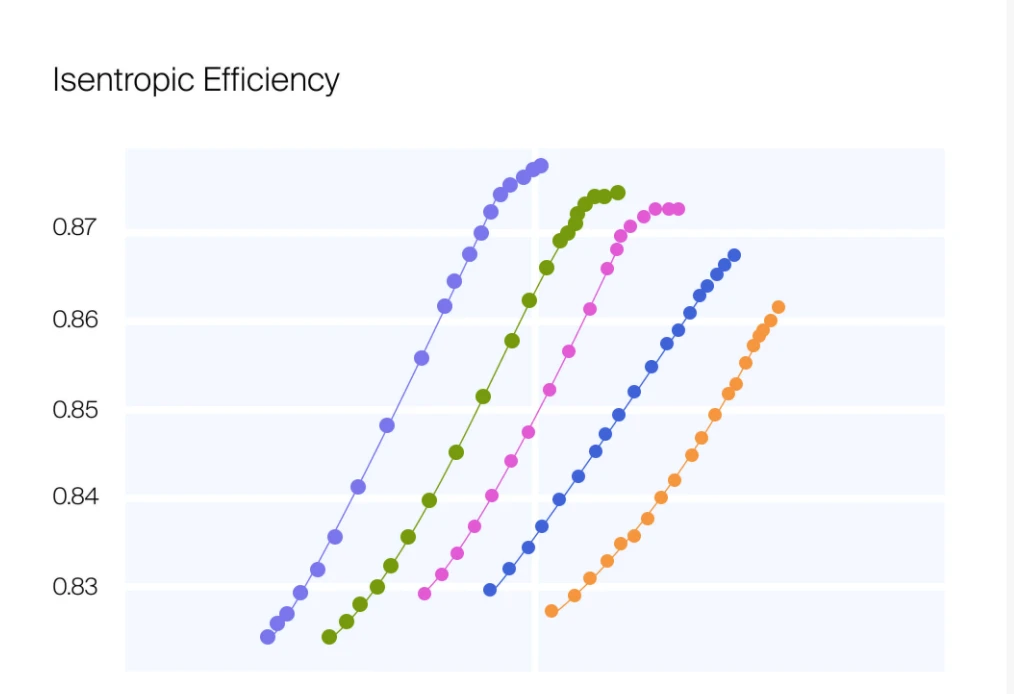
Deep Learning can support design engineers in "sweeps" over operating conditions for each design iteration, such as in a flight envelope, a turbine, or a water pump (Fig. (17)) performance map.
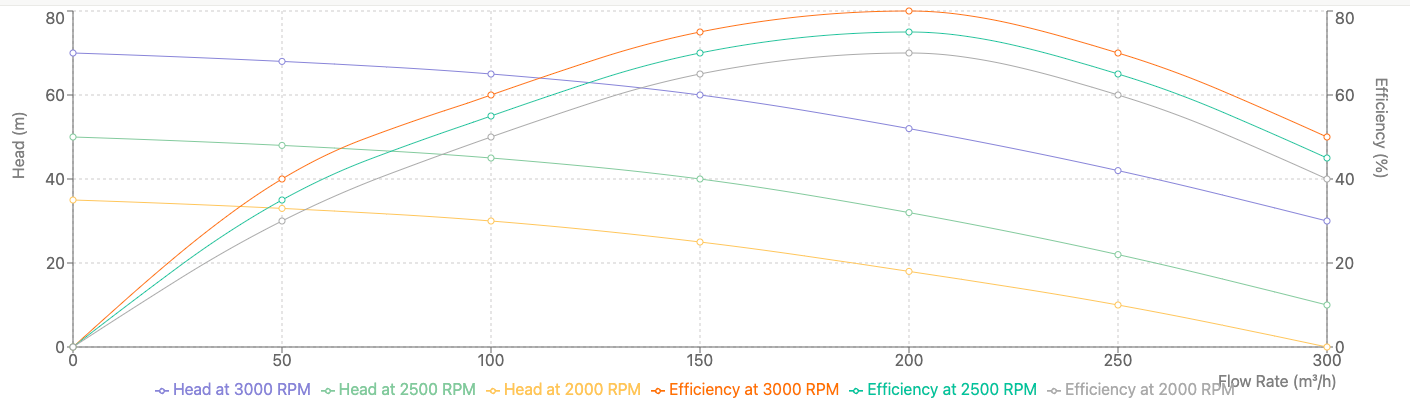
This is the democratization of simulation!
Beyond Predictive Engineering Analytics: System Optimization
How can predictive analytics models with machine learning help engineers identify new challenges and performance improvement opportunities? Fig. (18) shows the outcome of the predictive model of Neural Concept (NC) for the optimal design of a shock absorber.
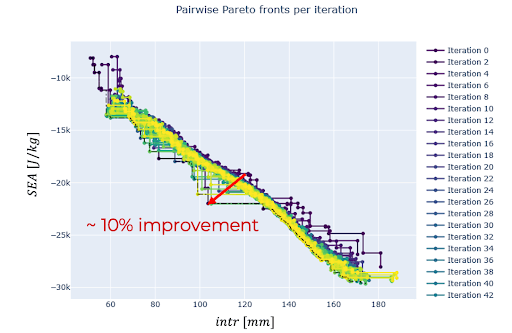
In the automotive industry, AI-powered analytics can optimize vehicle designs by identifying areas where vehicle performance can be improved and suggesting modifications as in Fig. (19).
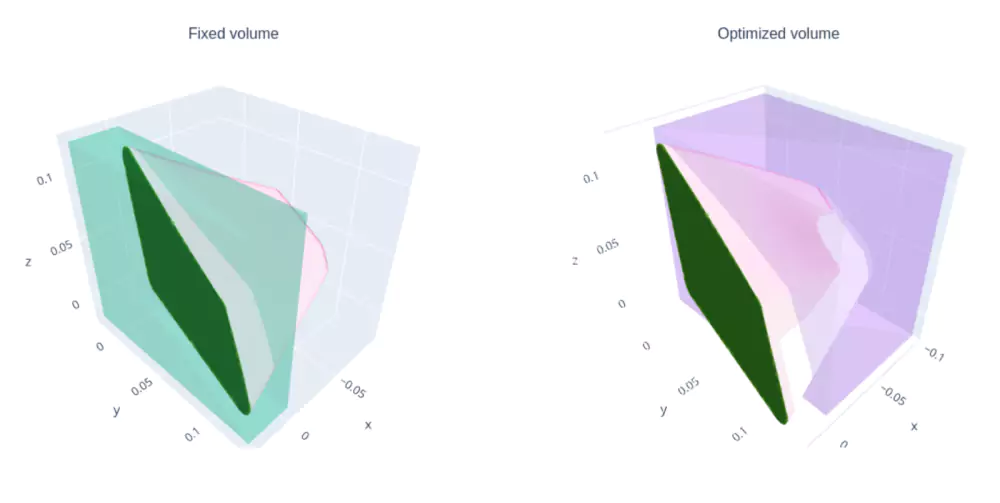
Another example is the energy industry - see Fig. (20).
Predictive analytics models can help engineers schedule maintenance and reduce downtime by identifying patterns showing when a turbine could fail. Engineering predictive analytics can optimize turbine performance, for example, by optimizing blade profiles and the thermal performance of turbomachinery systems.
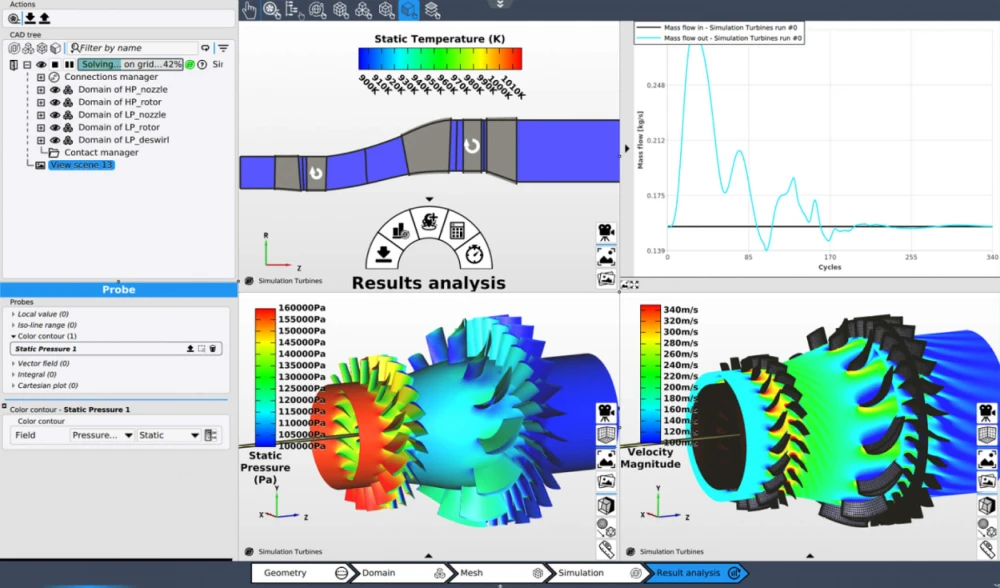
Conclusions
We have seen how predictive engineering analytics leverages data analytics to create models that predict engineering outcomes, enhancing design and manufacturing processes and integrating traditional physical simulations with AI methods.
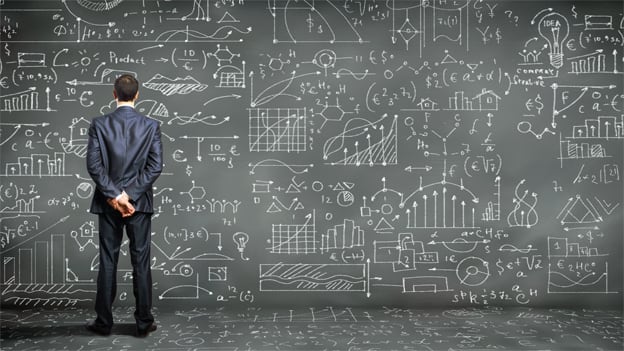
Predictive engineering analytics transforms data from simulations, testing, and manufacturing into actionable insights, enabling engineers to optimize performance and innovate.
These tools benefit industries with complex products, such as automotive and aerospace, where they enhance system simulation and streamline processes.