How Automation is Revolutionizing the Aerospace Industry
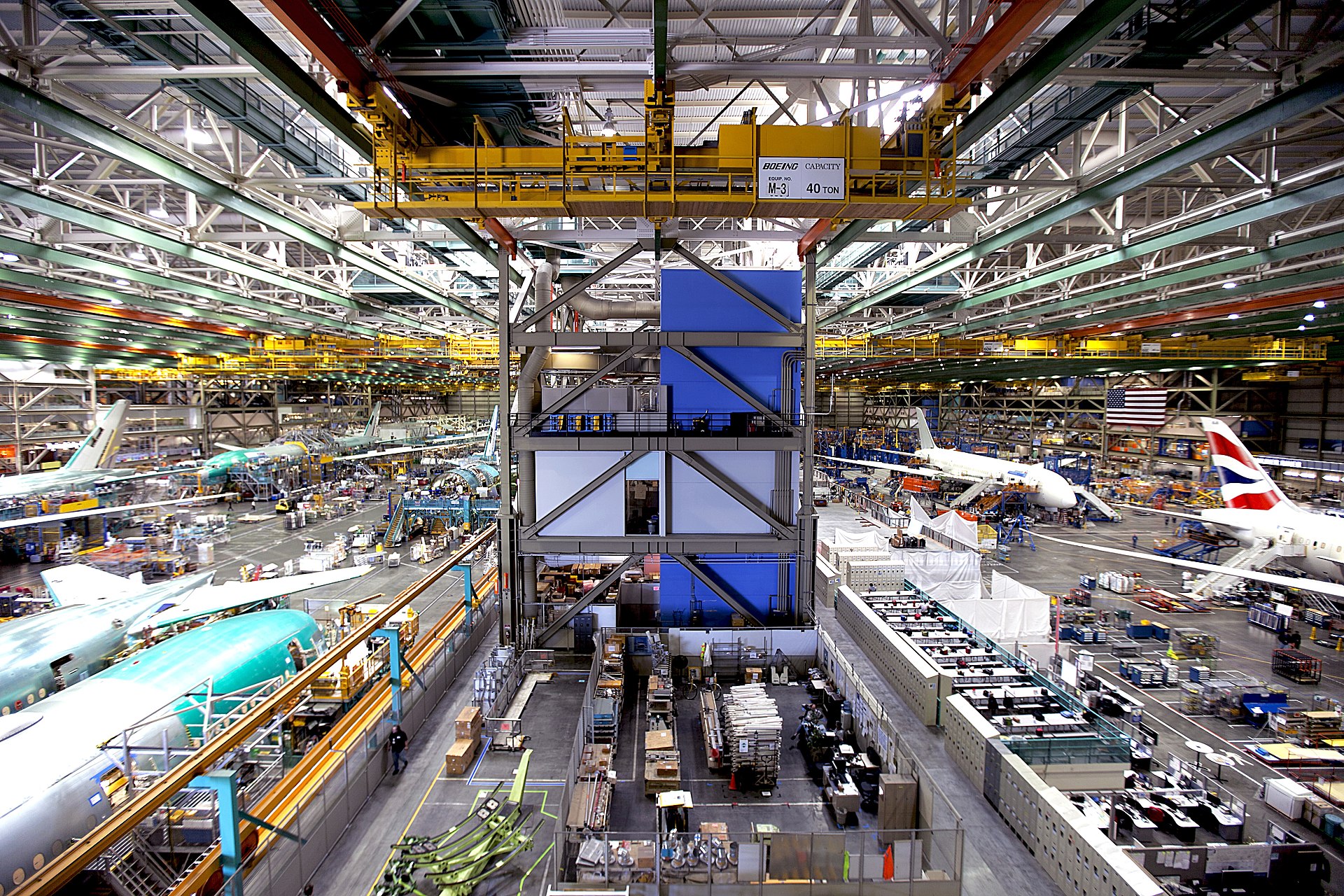
This article discusses how aircraft production techniques evolved and how this process will likely continue. Automation solutions drove the manufacturing revolutions, and nowadays, Artificial Intelligence is in the limelight.
Like in many other industries, automation has significantly reshaped the aerospace and defense industries. The aircraft, space, and defense industry, with unique demands for the highest levels of efficiency and precision, has found a reliable ally. The challenge of automation in aerospace industry, starting up front with product design and continuing through manufacturing and operations throughout the lifecycle, was to reduce the requirement for manual input with automation powered by digital solutions such as IoT and Artificial Intelligence. The outcomes of automation in the aerospace industry have been optimized product performance, lower costs, and improved product safety. Thanks to advanced automation technologies, the industry is continuing to ensure the necessary top-notch level of aerospace products and services.
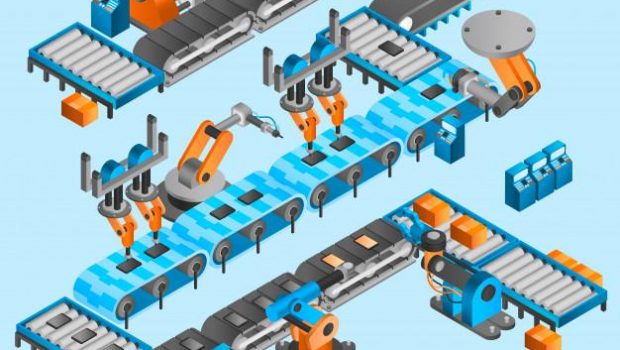
Understanding Automation in Industry - An Overview
The concept encompasses a massive portfolio aiming to increase productivity and consistency in various sectors. Traditionally, aerospace manufacturing relied on machinery, control systems, and traditional software processes to increase automation. At all stages of the product lifecycle, from aerospace product design to manufacturing and delivery, there was a common goal: to improve efficiency and reduce human operations in repetitive, expensive, and error-prone tasks.
Solutions have evolved through industrial revolutions, a journey we continue in the aircraft industry, always seeking a competitive edge. Those revolutions are known as Industry 1.0 - 2.0 - 3.0 and 4.0.
Industry 1.0 (The First Industrial Revolution): In the late 18th century, industry transitioned from hand labor to machines powered by steam and water. Mechanization increased efficiency but relied heavily on human labor.
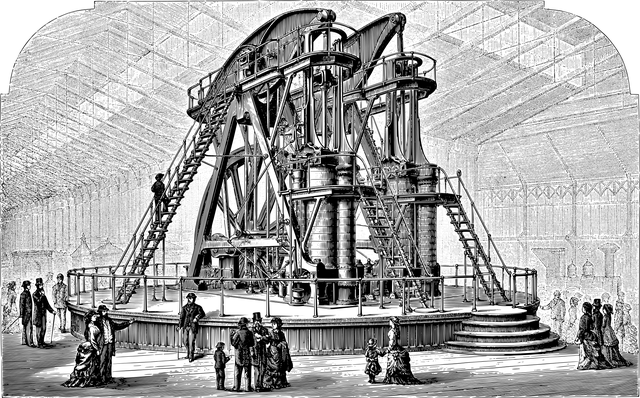
Industry 2.0 (The Second Industrial Revolution) introduced electricity and modern manufacturing techniques. Henry Ford’s assembly process revolutionized manufacturing, allowing faster throughputs and reduced costs.
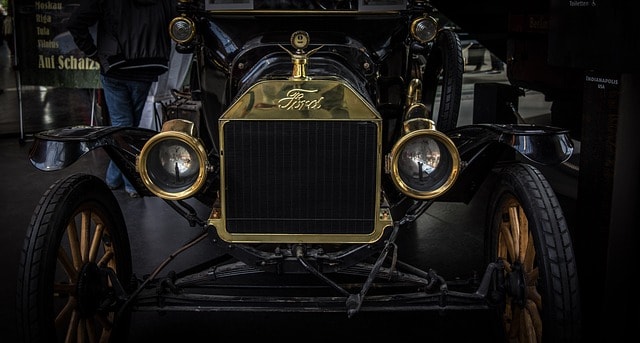
Industry 3.0 (The Third Industrial Revolution): The third industrial Revolution began in the mid-20th century. This revolution introduced electronics and I.T. into the manufacturing process.
Industry 4.0 (The Fourth Industrial Revolution): Industry 4.0 integrates high-end technologies, such as the Internet of Things, cyber-physical systems, and cloud computing, into digital solutions for "smart factories." The transformative power of Artificial Intelligence in the aerospace industry is reshaping aircraft manufacturing and design.
Recap on the History of Automation and Current Status in Aerospace
Automation dates back to the Industrial Revolution. Mechanization replaced manual labor. Henry Ford conceived the assembly line. Advancements in electronics and computing allowed manufacturers to implement programmable systems. Complex tasks became manageable with minimal human intervention. Industry 4.0 introduced machines that can communicate, adapt, and improve themselves.
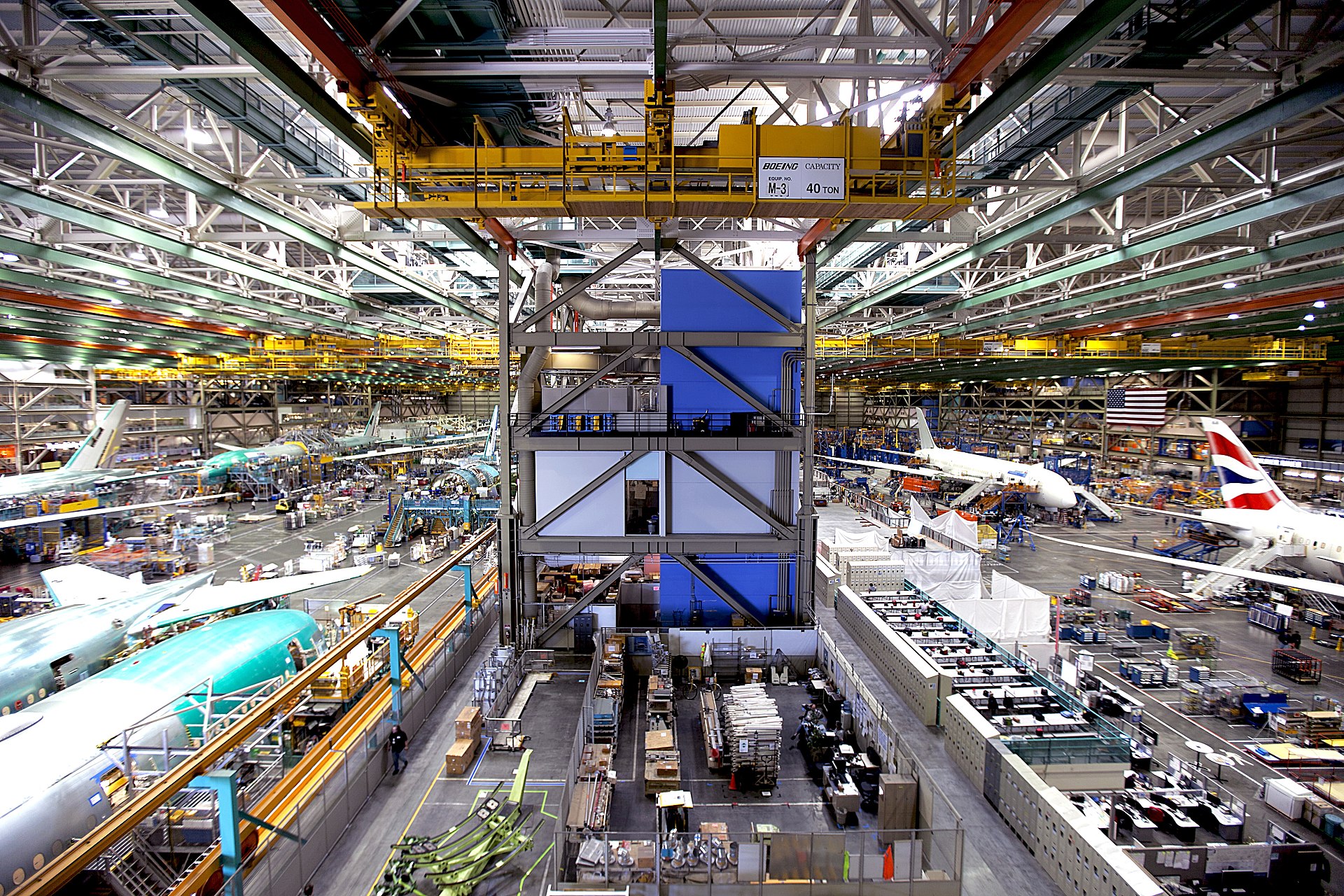
Current Status of Automation in Aerospace
The benefits of automation in the aerospace parts manufacturing can be seen with robotic systems, AI-powered simulation, and automated inspection systems that minimize manual labor and enhance precision. Robotic systems are employed in various production processes, from drilling holes in aircraft components to assembling intricate aircraft parts with high accuracy. The integration of collaborative robots, or cobots, has further transformed manufacturing. Cobots work alongside human operators to perform repetitive tasks and free skilled workers to let them focus on more complex problems.
Automation technologies offer advantages in military aircraft and civil aerospace manufacturing processes.
Automated inspection systems ensure that every component meets stringent standards, enhancing safety and reliability in aerospace components. Imaging technologies, machine learning algorithms, and real-time data analysis are used. These systems detect deviations from specifications with precision and reduce the likelihood of human error.
Manufacturers can continuously monitor their process when automated inspections are integrated into the assembly line. Individual aerospace components and overall assembly are improved, and there is greater trust in safety!
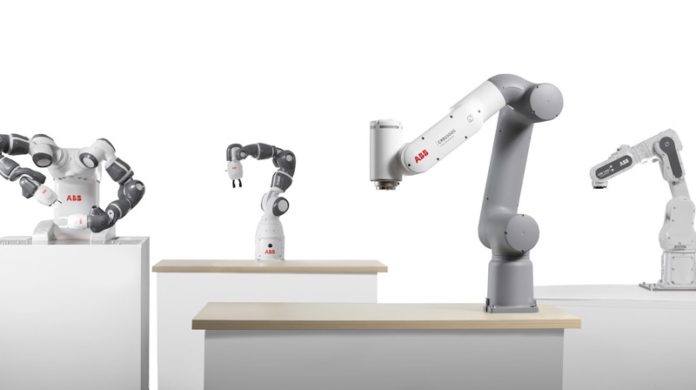
The Role of Robotics in Aerospace Automation
Robotic integration in the aerospace field is changing the game regarding automation. Robots are used for assembling parts, painting, and inspecting finished products. With robotic arms, manufacturers can work with high precision, accuracy, and consistency, whether fastening components or drilling holes. Thanks to advanced vision systems, these robots can spot and locate parts quickly, ensuring everything lines up perfectly during assembly.
This technological boost on the factory floor also helps with quality control, as they can perform real-time inspections to catch any potential defects early on. By adding end effectors—essentially tools that attach to robotic arms—these robots can take on even more jobs and be versatile. End effectors are specialized tools or attachments that enable robots to perform specific tasks, such as welding, painting, or gripping, enhancing the wide range of functions they can perform.
Benefits of Robotics in Aerospace
Improved Efficiency Via Robotics. Robotic systems can operate continuously with higher throughput. This is especially important in aerospace, where production schedules are tight.
Enhanced Precision with Robotic Integration. Automation reduces human error and ensures that components are manufactured and assembled according to specifications. This is critical in aerospace, where even minor errors can have serious, not to say fatal, consequences. For example, in the final assembly of aircraft wings, even a slight deviation in the dimensions can lead to imbalances during flight, resulting in catastrophic failure.
Improved Safety of Systems. Manufacturers can minimize workplace injuries and enhance safety protocols by automating hazardous tasks. For example, in the aerospace manufacturing environment, handling heavy components, working at heights, or performing repetitive motions can pose significant risks to human workers.
Applications of Automation in Aerospace Systems. Automation has different applications throughout the aerospace production cycle. Each stage gets substantial benefits in terms of:
- Design
- Manufacturing
- Assembly
- Quality assurance
Automated Manufacturing and Assembly
Robotic arms and CNC machines are used in manufacturing and assembling aircraft components. These robots perform tasks with greater accuracy than humans. For instance, robots can drill holes and fasten components accurately, ensuring each part fits perfectly during assembly.
Robotic integration greatly benefits the assembly of heavy components, such as fuselages and wings. Automated guided vehicles transport materials across the factory floor, reducing manual material handling and increasing safety. This speeds up production and enhances safety.
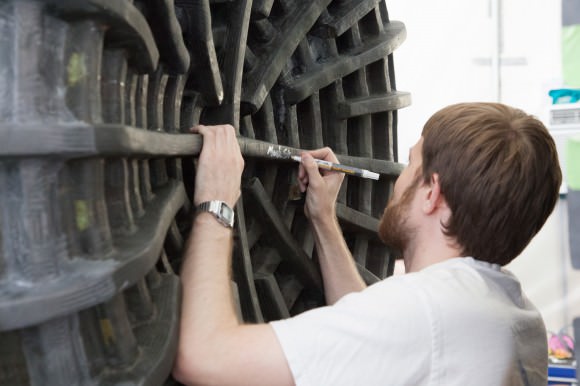
The risk of injury associated with manual labor is minimized.
Quality Assurance
Automated inspection systems utilize novel methods. Imaging and machine learning solutions can assess components during manufacturing. These automated systems can detect deviations from specifications, allowing for corrective action in the manufacturing line and helping manufacturers maintain high standards.
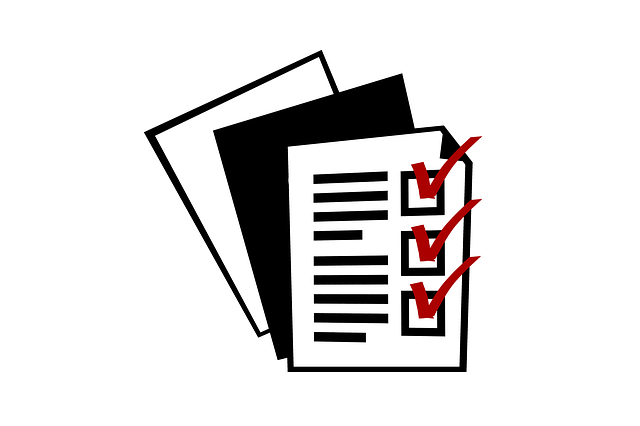
Unique Challenges of Aerospace Manufacturing
Despite the benefits, technological adoption presents challenges. Let us review them below.
High Initial Costs and Integration with Legacy Systems
Implementing those systems often requires substantial upfront investment by any aerospace manufacturer. Aerospace manufacturers must conduct thorough cost-benefit analyses to justify the expense. Long-term savings from greater efficiency and lower labor costs often offset the initial expenses.
Many aircraft manufacturers operate legacy systems that may not easily accommodate new automation technology. Integrating advanced automated solutions with existing infrastructure requires planning and execution to avoid disruptions.
Learning from Other Industries and Vice Versa
The aerospace industry can learn from other sectors that have automated. The automotive industry utilizes robotics for assembly and manufacturing, where collaborative robots (cobots) enhance production. Cobots mean that humans and robots work together.
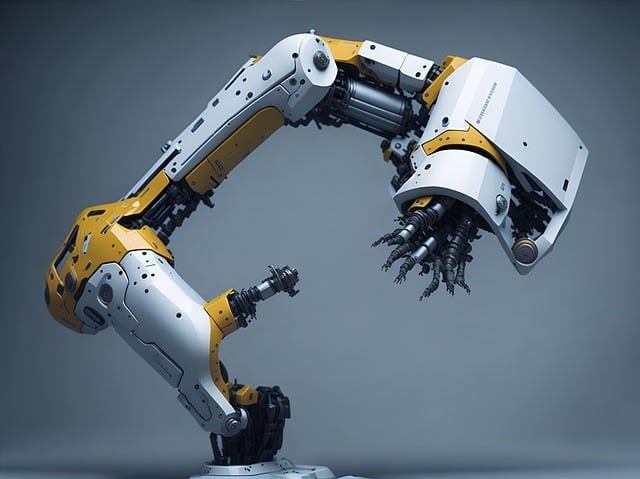
Aerospace manufacturers can adopt collaborative strategies, optimizing production times while leveraging human expertise. Conversely, aerospace’s rigorous measures can benefit industries like electronics. The aerospace sector employs comprehensive automated inspection systems to ensure compliance with strict regulations. Similar reliability assurance solutions can strengthen other sectors’ production processes and safety standards.
Future Trends in Aerospace Automation
Advancements in AI and robotics will drive the future, and several emerging trends will shape the industry’s trajectory.
AI and Digital Twins
AI is going to change how aerospace manufacturers approach design and production. AI algorithms for aerospace design and manufacturing analyze “datasets” and find “trends” by associating input and output data. Integrating AI into systems will lead to more innovative aerospace manufacturing processes.
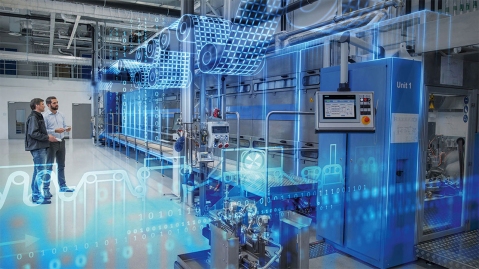
Digital twins are virtual replicas of physical systems. Their use in the industry is expected to grow significantly. This technology allows for real-time monitoring and simulation of production processes, enabling manufacturers to identify areas for improvement quickly.
Sustainability
Industries strive to reduce their environmental impact. Automated systems will play a key role in promoting sustainable practices to optimize resources, minimize waste, contributing to sustainability of the aerospace industry.
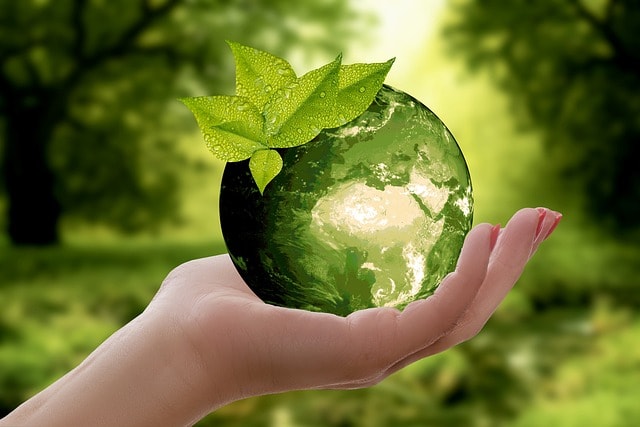
Conclusion & FAQs
Systematization is becoming essential for boosting performance and expense management in the aerospace industry. Manufacturers can streamline production, reduce human error, and improve operational performance. AI gives a perspective where aerospace manufacturing is efficient, sustainable, and adaptable to changing market demands.
Frequently Asked Questions
How Do Automation Solutions Enhance Manufacturing in Aerospace?
Automation improves the efficiency and accuracy of the aerospace manufacturing process. Robotic systems decrease manual work, ensuring consistent outcomes resulting in safer and more reliable aircraft.
How Can AI Improve Aerospace Automation?
AI enhances aerospace automation by enabling predictive maintenance, reducing downtime, reducing production time, and optimizing the design process. AI algorithms analyze data to identify inefficiencies and streamline operations, ensuring optimal production systems.
What Role Do Digital Twins Play in Aerospace Automation?
Digital twins are essential to aerospace production, providing real-time monitoring and simulation capabilities. They enable aerospace manufacturing teams to visualize and optimize the process and identify potential issues.
What Are the Main Challenges?
The main challenges in aerospace manufacturing are the high upfront cost, the integration of advanced technologies with legacy systems, and the skills gap among the workforce.