Enhancing Engineering Efficiency and Innovation: A Collaboration Between Neural Concept and Eaton
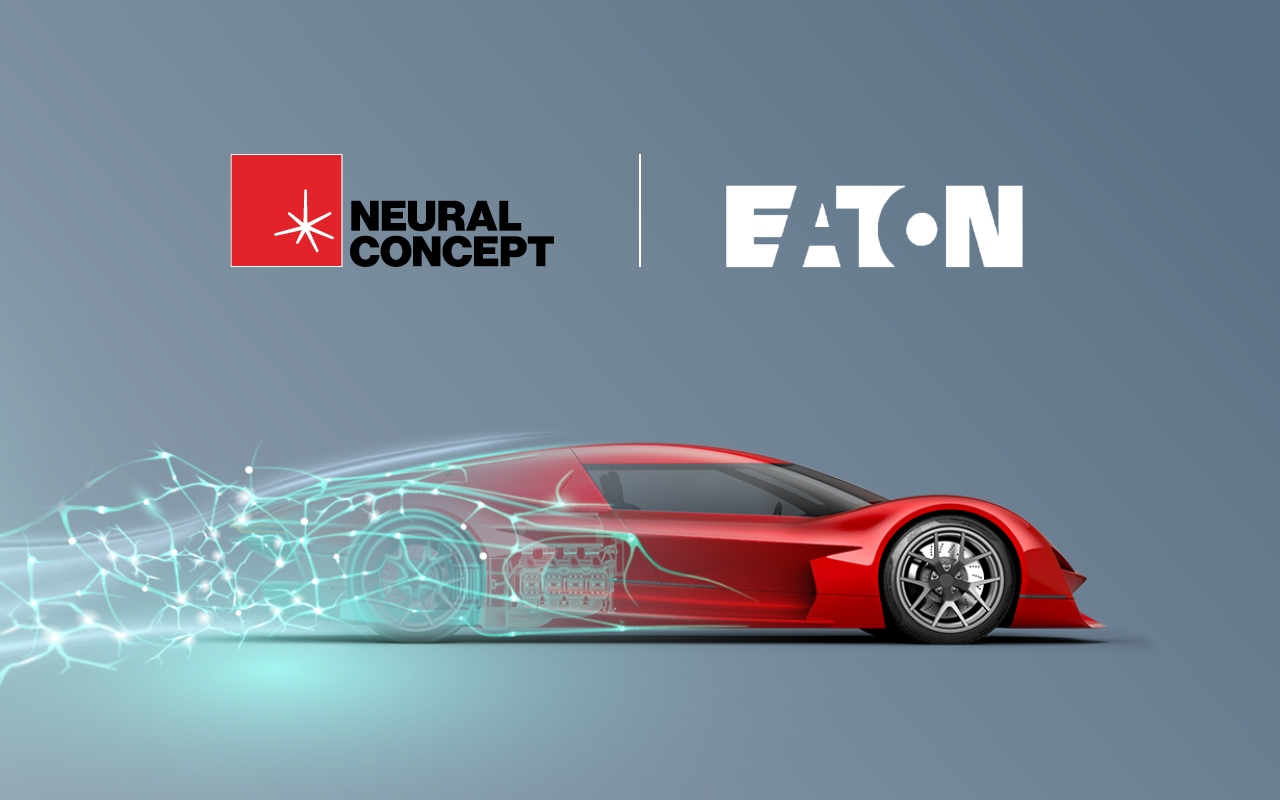
Neural Concept and Eaton, the power management company, have published a technical paper that explores the application of Geometric Deep Learning to construct a predictive model capable of accurately assessing the thermal performance of cooling plates for power modules within a matter of seconds.
The technical paper underscores the potential of Neural Concept's technology to accelerate AI for engineering by offering faster, more accurate, and AI-driven engineering results.
This workflow produced cooling modules which achieved more than a 30% improvement in pressure drop and reduced overall weight by over 10%.
Optimising Power Module Cooling Plates with Deep Learning
In the ever-evolving engineering landscape, innovative approaches to design optimisation are essential, especially in fast-paced production environments. Traditional CAD and simulation tools often fall short in handling the complexity and speed required for designing critical components.
As electrification advances, power electronics systems are becoming more energy-dense, necessitating compact and efficient thermal management solutions. Higher energy density, attributed to high-power electrical components packed in shrinking dimensions, demands more efficient and compact cooling solutions. Conventional design approaches hit their limits when pushing the boundaries of air or liquid-cooled solutions' efficiency and power density.
Advancing with Geometric Deep Learning
To overcome these limitations, Eaton leverages a valuable repository of legacy cold plate designs, developed through extensive engineering knowledge and experimentation. By integrating cutting-edge AI technology like Neural Concept, Eaton accelerates the design and development cycle for new applications, using past knowledge and experimental data.
Neural Concept can handle unstructured 3D data from CAD geometries directly and learn how they interact with the laws of physics. This approach predicts global quantities and field responses from a single geometry, accurately capturing highly non-linear phenomena or discontinuities in the physical response. The predictive models can learn from various topologies, handling a much wider design space.
Implementation and Results
In this study, Neural Concept was applied to a set of CFD simulations and cold plate CAD designs. The workflow includes three main pillars:
- Neural Concept Design Module: This module allows for automated and fast geometry generation.
- Simulation using Ansys Fluent: Thermal behaviour simulations generate the initial dataset to train the predictive model.
- Non-parametric Optimisation: Extensive optimisation explores innovative designs, overcoming the limitations of traditional parametric optimisations.
The optimisation workflow produced cooling modules that significantly outperformed standard products, achieving more than 30% improvement in pressure drop and reducing overall weight by over 10%. The designs generated through this workflow were innovative and beyond the reach of conventional CAD and CAE tools.
Conclusion
The novel approach to cold plate design, utilising Deep Learning-based predictive models, addresses the limitations of traditional workflows. By leveraging AI, this method explores a vast design space, offering engineering teams insights into product performance and paving the way for further enhancements. This end-to-end optimisation can be run in less than a week, enabling companies to deliver superior products faster, and adapting to new requirements even at the last stage of the design process.
The integration of the Neural Concept with existing CFD simulation infrastructure minimises downtime between steps and allows for continuous improvement, pushing the boundaries of what is achievable in thermal management design.
Download the technical paper here: https://saemobilus.sae.org/papers/optimization-power-module-cooling-plate-application-deep-learning-thermal-management-devices-2024-01-2583.