Electric Vehicle Simulation: Reducing Development Costs and Time
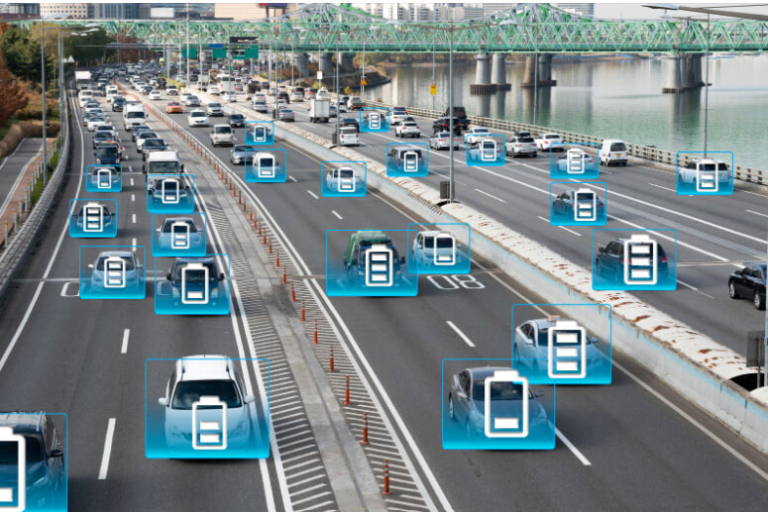
The electric vehicle market is driven by global pressure to reduce greenhouse gas emissions and the increasing demand for cleaner.
Governments worldwide are implementing stricter emissions regulations, providing subsidies, and setting ambitious targets for all-electric vehicles, further boosting the EV market. But on top of the government push, EV sales are fueled by advancements in battery technology, energy storage systems, and electric motors.
This expansion challenges automotive producers, particularly in the areas of cost, time-to-market, and vehicle performance.
Developing high-end electric vehicles requires overcoming complex technical obstacles, making efficient processes critical. Simulation has become an invaluable tool for meeting these challenges, enabling engineers to streamline the development process.
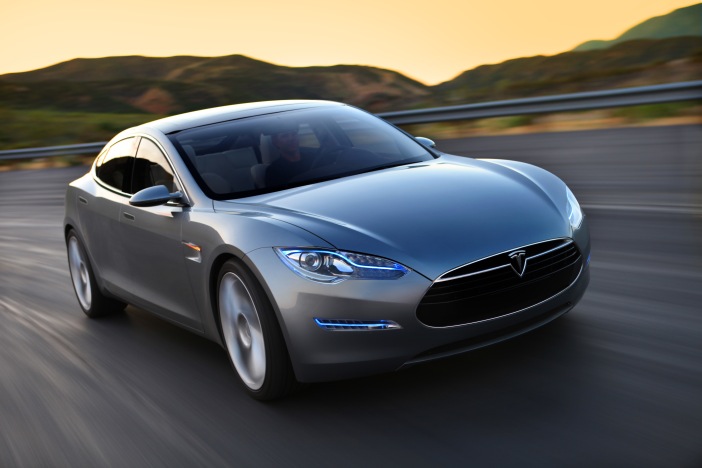
Challenges in EV Development and the Need for Efficient Processes
Developing electric vehicles involves intricate systems, including energy storage, power electronics, and EV battery thermal management.
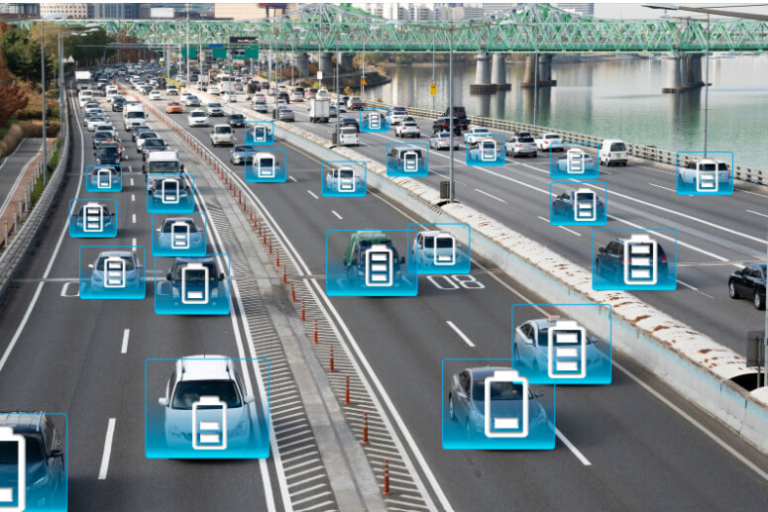
Unlike traditional internal combustion engines, EVs require integrated battery pack design solutions for battery capacity, power density, and control algorithms.
This complexity can slow down the development process, increase costs, and create uncertainty in predicting various configurations under real-world conditions.
Addressing "range anxiety"—the fear of running out of battery power—is a major concern for EV makers. Balancing performance, weight, and energy efficiency while ensuring the remaining useful life of batteries requires careful optimization of each component.
The growing demand for electrified vehicles also means that automakers need to quickly adapt to evolving market trends. Efficient processes, driven by advanced modeling and simulation tools, are essential to overcoming these challenges.
The Role of Modeling and Simulation in EV Development
EV simulation leverages digital modeling tools to test and optimize EV components and systems in a virtual environment. Multiphysics simulation allows engineers to evaluate everything from the aerodynamic simulations of a vehicle to the thermal management of battery systems.
With high-fidelity simulations, manufacturers can gain detailed analysis of the entire EV system without the need for extensive physical testing.
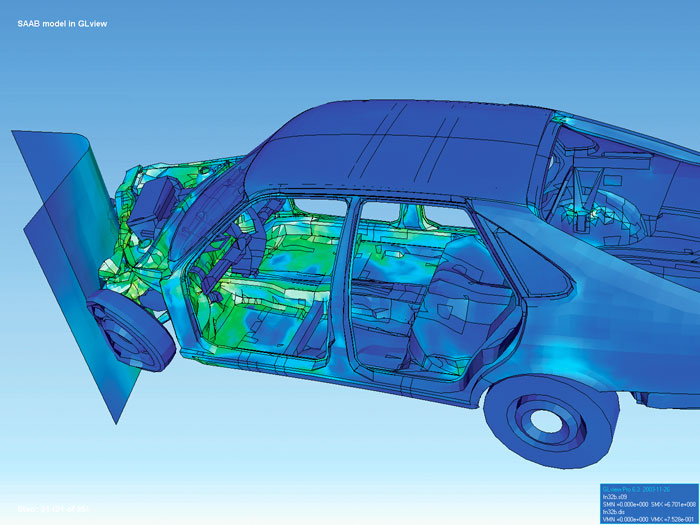
Cost and Time Benefits of Simulation
Simulation significantly reduces the time and cost of the development process. Instead of building multiple physical prototypes, engineering teams can use virtual models to test different drive cycles and evaluate performance under various environmental conditions.
Simulation-based development reduces costly design errors and shortens the time-to-market for electric vehicles.
Additionally, optimization algorithms can analyze countless configurations, ensuring that energy consumption, fuel economy, and power density are maximized throughout the development process.
The Importance of Simulation in EV Development
Simulation plays a crucial role in accelerating the design process, reducing development costs, and enhancing vehicle performance and safety.
Accelerate the Design Process
Using simulation, engineering teams can shorten design cycles with virtual models before moving to physical prototypes.
Unlike traditional design processes that rely heavily on iterative physical cycles, simulation-based design allows engineering teams to evaluate multiple parameters—such as power, energy efficiency, and capacity of batteries—simultaneously.
This results in faster scheduling, enabling car makers to respond more quickly to market demands.
For example, a traditional approach may involve building several prototypes, each undergoing physical testing under different conditions. By contrast, simulation-driven design can run hundreds of virtual tests in parallel, evaluating components such as fuel cells, motors, and energy storage systems with greater speed and accuracy.
Reduce Development Costs
The cost-saving benefits of early-stage simulation are undeniable. Identifying potential design flaws or inefficiencies early in the process prevents costly modifications later on.
Real-world examples demonstrate how companies have successfully used simulation to reduce development costs. For instance, a major EV manufacturer used virtual testing to optimize its battery management system, resulting in a 20% cost reduction and a 30% improvement in energy efficiency.
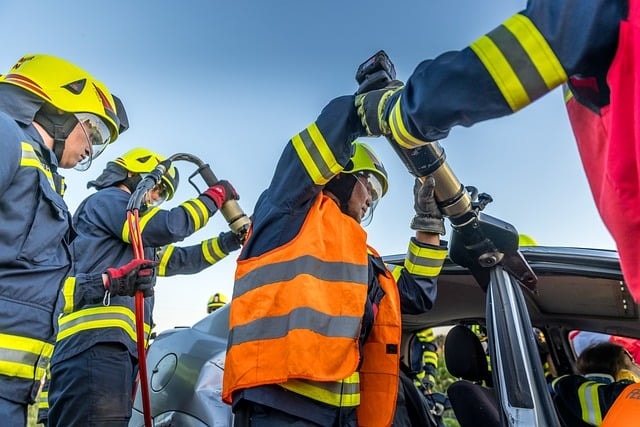
Enhance Vehicle Performance and Safety
Simulation enables manufacturers to optimize vehicle performance by allowing engineers to explore different combinations of materials, motor configurations, and powertrain setups. By simulating real-world driving conditions and various configurations, engineers can enhance energy consumption and ensure that the vehicle meets stringent performance and safety requirements.
Moreover, safety validation through simulation ensures that electric vehicles can withstand extreme conditions and potential accidents: under different simulated crash scenarios, engineering teams can enhance structural integrity and protect passengers in the event of a collision.
Key Use Cases for EV Simulation
To improve efficiency and performance, simulation helps optimize EV powertrains and battery systems. Engineers can model different powertrain configurations, evaluate battery capacity, and predict how components will interact.
AI-driven modeling takes this a step further. Machine learning algorithms predict power density and energy consumption. These predictive models can suggest design changes to extend the remaining useful life of the battery.
Thermal Management and Efficiency
Battery systems generate significant heat.
This topic is crucial for maintaining energy efficiency in EVs. Simulation allows engineering teams to model the thermal behavior of components under different conditions, ensuring that cooling systems are effective and energy-efficient. This improves the overall vehicle longevity.
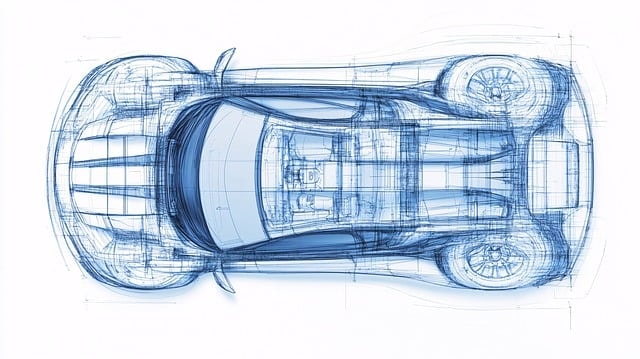
Aerodynamic and Structural Analyses
Simulation tools help optimize vehicle aerodynamics by evaluating how air flows over the body of the vehicle. Better aerodynamics reduce drag. Drag reduction means less energy is needed to move the car all the rest being equal. This is improving the economy of fuel and extending the driving range.
Another concern is the safety of our EVs and durability under fatigue.
Structural analysis through virtual simulations also ensures that the vehicle can withstand the stresses of real-world driving conditions.
Integration of Autonomous Driving Features
As electric vehicles increasingly incorporate autonomous driving features, simulation plays a critical role in developing these systems. With the simulation of real-world driving scenarios, automakers can assess the reliability of autonomous systems.
The Role of AI in Electric Vehicle Simulation
AI and ML enhance simulation-driven design by automating dataset analysis and accelerating optimization processes. AI uses algorithms to identify patterns in complex datasets. ML-trained models predict system behavior based on historical data.
In simulation workflows, ML algorithms handle high-dimensional data from electric motors. These models learn the interactions between parameters such as temperature, power density, or energy consumption. Models can run multiple simulations in parallel and generate detailed performance predictions.
What is the difference between CAE and AI?
Traditional simulations often involve solving differential equations for each physical domain, which is computationally expensive and time-consuming. In contrast, AI-driven simulations leverage reduced-order models and surrogate modeling techniques. These ML-based methods approximate the behavior of complex systems, producing results in a fraction of the time required for high-fidelity multiphysics simulations.
Furthermore, AI algorithms can optimize designs by iterating over thousands of parameters, something infeasible with traditional approaches. Running so quick, high-fidelity simulations allows engineers to test more configurations and refine designs early in the development process. The integration of AI ensures faster convergence, higher precision in predictions, and more efficient use of computational resources, making it indispensable for advanced engineering simulations like those in electric vehicle engineering.
Benefits of AI and ML
AI enhances the speed and accuracy of simulations, enabling faster iteration cycles and more efficient design processes. For instance, ML models can predict the behavior of electric motors, energy storage, and power electronics under various conditions, providing detailed analysis in a fraction of the time required for traditional simulations.
Case Studies: AI-Powered Simulations in EV Engineering
A notable example is the 3D Deep Learning platform Neural Concept Shape, which integrates AI-powered simulations into EV engineering workflows. By using AI to optimize vehicle aerodynamics and structural design, this tool has helped automakers reduce time-to-market and costs significantly.
Benefits of EV Simulation for Faster Development Process
Simulation drastically reduces the need for physical prototypes, allowing for faster iteration cycles. Engineers can test virtual models under different conditions, making design adjustments before building physical prototypes.
Time-to-Market Acceleration
By shortening the design and testing phases, simulation helps automakers bring products to market faster: meeting market demand more quickly also allows companies to survive in the fast-evolving EV industry.
Continuous Improvement Through Simulation
Simulation is not a one-time process—it enables continuous optimization. As new technologies and materials become available, automakers can use simulation tools to refine and improve their designs over time, resulting in long-term innovation.
Challenges in EV Simulation
EV systems are highly complex, with numerous interconnected components. Simulating these systems accurately requires advanced modeling tools that can account for various factors such as temperature, power, and efficiency.
Ensuring Simulation Accuracy
High-fidelity models are essential for accurate simulations. AI helps improve accuracy by learning from previous simulations and adjusting models accordingly. This allows engineering teams to make better predictions and optimize designs with greater confidence.
Integration with Existing Development Processes
Integrating simulation into traditional development workflows can be challenging, especially for teams that are resistant to change. However, modern simulation tools are designed to work alongside conventional development processes. This makes the collaboration on generating datasets and the transition smoother.
Conclusion: The Future of Electric Vehicle Development with Simulation
As the electric vehicle market continues to expand, simulation will play an increasingly critical role in meeting development challenges. AI-driven simulations offer speed and acceptable accuracy, helping engineering teams to accelerate the design process to enhance vehicle performance. With these advanced technologies, companies can stay competitive and continue to innovate.
FAQs
- How does AI-driven simulation differ from traditional simulation methods in EVs?
AI-driven simulation enhances speed and accuracy by using ML to predict system behaviors and optimize designs faster than traditional methods.
- What industries can benefit from the simulation techniques used in electric vehicle development?
Automotive, aerospace, renewable energy, and manufacturing industries can benefit from simulation techniques similar to those used in EVs.
- What are the future trends in electric vehicle simulation?
Future trends include increased use of AI and ML, integration of 5G for real-time simulations, and more advanced models for predicting performance under extreme conditions.