Conceptual Design in Engineering: Ancient to AI Innovation
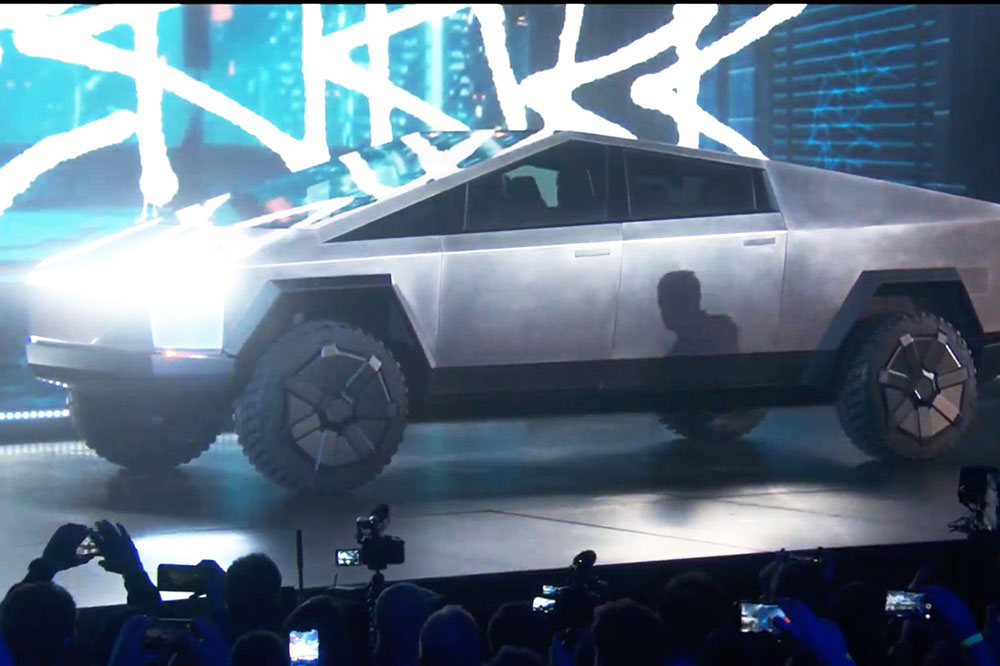
Engineering design processes are complex and require good problem-solving skills. But it is also essential to understand the difference between engineering phases.
Typical examples of an engineering design process are manufacturing, product reliability, and quality. Yet, an initial crucial phase is the idea or concept design stage, also known as conceptual engineering.
In the conceptual design phase, technical requirements are blended with enterprise-wide concepts that go beyond simple engineering performance such as product durability. Senior management, sales, and marketing strategies are discussed, sometimes starting from a brief description. The aim is to understand how to win over the competition and meet final user needs both in practical and emotional terms, consolidating and increasing the brand value.
Conceptual innovation in the product design process is the key winning factor. This is why in this article we'll explore its history from Ancient Egyptians to applications of AI in engineering.
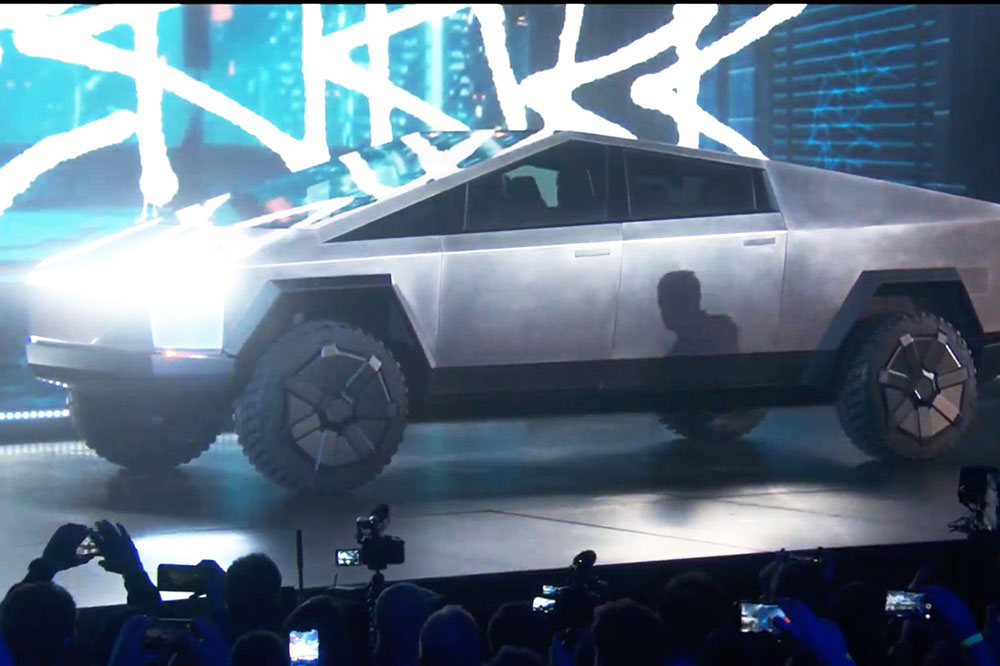
Innovation can happen at different levels with conceptual design:
- It can be disruptive, as in the case of the first iPhone model where a radically new way of using devices was created and users were driven by the concept.
- It can be a new "familiar" idea, as in the case of the "Tesla Cybertruck" model.
- Or it can be an incremental amelioration, such as in new "Volkswagen Golf" models.
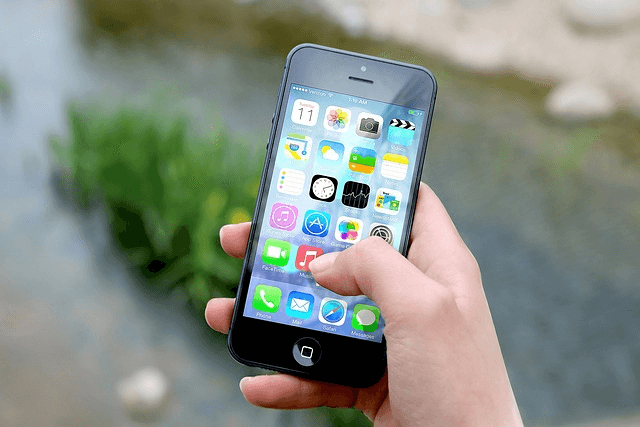
In any case, the conceptual design phase includes work on concept generation and concept evaluation before moving the engineering project planning to the next stage.
A Short History of Conceptual Design Engineering
Design has shaped our lives since ancient times. The surrounding natural environment and necessity influenced the Egyptians and the Romans. They approached design with a combination of practicality and awe for the divine.
Conceptual design consisted of early blueprints and sketches - the primary means of communicating design concepts, and they relied heavily on traditional methods and materials available at the time. The designs emphasized proportion, symmetry, and a harmonious relationship with nature.
During the Renaissance period, there was a significant shift in the way architects and designers approached their work. They began to blend science and art to create more imaginative and accurate conceptual design ideas. New tools and knowledge, such as the architect's compass and vanishing point perspectives, enabled them to craft more intricate and precise designs.
As the Industrial Revolution swept the world, new materials and construction techniques were developed, leading to a rise in standardized building methods. This era also marked the beginning of rapid urbanization, which required a more organized and systematic design approach.
In response, architects began relying on detailed hand-drawn sketches and scale models to communicate their ideas more effectively. Thus, the conceptual design phase was really born as an aide to the later detailed design phase. For instance, while the detailed design phase will contain all the "nuts and bolts", the conceptual design stage will be more concerned with issues like the bulk size of a component and how it fits with the rest.
In the latter half of the 20th century, the digital age arrived, and with it came Computer-Aided Design (CAD) tools. These revolutionary tools allowed architects and designers to create incredibly detailed 3D models, simulate various environmental conditions, make drawings, and make rapid modifications, bringing a new level of efficiency and precision to the engineering design process.
What's next in the 21st-century product design process?
Follow us in the rest of the article, to understand if AI design tools can facilitate seamless communication between concept design engineers and engineers in charge of subsequent design stages, to produce integrated ideas and design solutions instead of watertight-separated concepts.
What Is Modern Conceptual Design?
Let's define it.
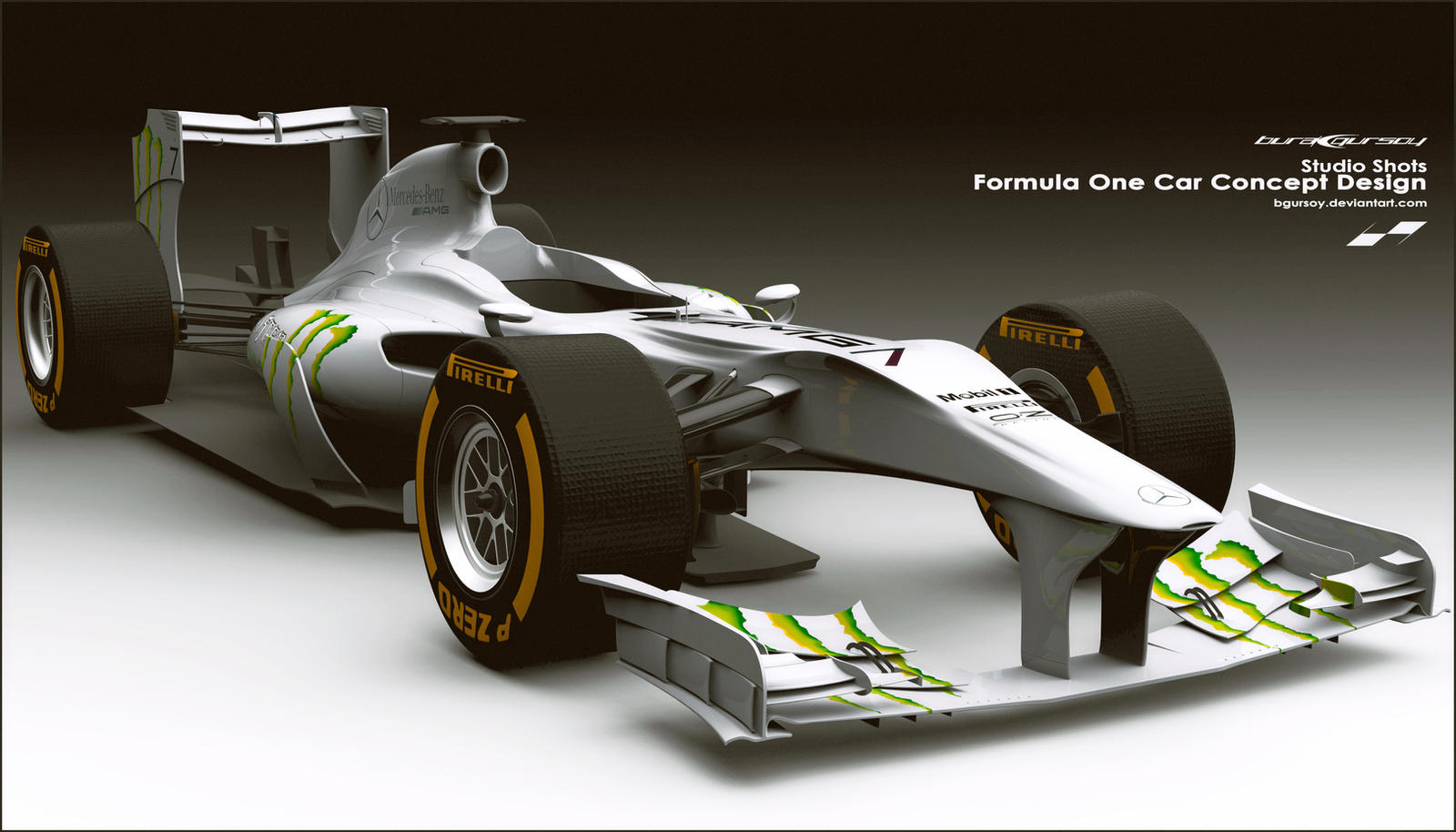
What Is Detailed Design Phase vs Conceptual Design Phase?
Engineering is an iterative design process, where revisions may be necessary at any project stage. This includes revising project requirements, specifications, and adopted solutions. Although the likelihood of needing revisions is higher in earlier product design phases, such as conceptual and embodiment designs, modifications are still possible during the detailed design phase based on reaching design specifications i.e. reaching or not functional requirements.
Iterations of detailed design should continue until the parameters and properties of custom-designed parts and off-the-shelf components converge.
In engineering detailed design, it's always possible to return to any previous design iteration and make necessary revisions based on modified requirements and conditions. This possibility is implemented in numerous 3D CAD modeling tools available to engineers and designers in the detail phases of the product design process.
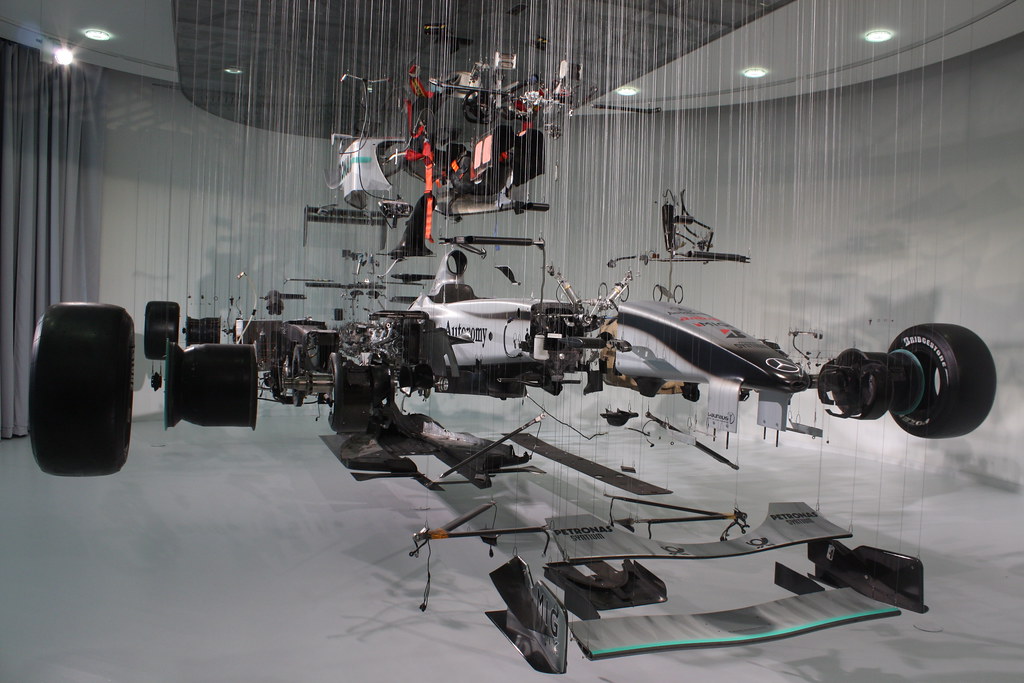
Conceptual Design vs Product Design: What Is the Engineering Problem to Solve?
Conceptual design focuses on defining the "what" and involves challenges related to idea generation, feasibility assessment, and concept selection.
Product design, on the other hand, is concerned with the "how" and entails solving more detailed engineering problems related to design, prototyping, manufacturing, and performance optimization.
Both design phases are critical in the engineering process, and successful product development requires a seamless transition from conceptual design to product design, with careful consideration of the specific challenges at each stage.
In the following, we'll outline the key differences and the engineering problems associated with each phase.
Conceptual Design in the Design Process
To successfully develop a product or system, engineers go through a series of stages. The first stage is problem identification. Here, the main challenge is defining the problem that the product or system should solve. This involves understanding user needs, market demands, and technological possibilities.
Once the problem is defined, the next stage is concept generation. This involves generating creative and innovative ideas that address the identified problem. At this stage, various concepts are explored, and the most promising ones are selected.
After selecting the promising concepts, the feasibility assessment stage begins. Engineers must assess the proposed concepts, considering technical, economic, and resource constraints.
Identifying potential risks and uncertainties associated with the chosen concepts is essential to make informed decisions. This is done in the risk analysis stage.
Finally, rough cost estimates are provided to help stakeholders understand the financial implications of each concept. This is done in the initial cost estimates stage.
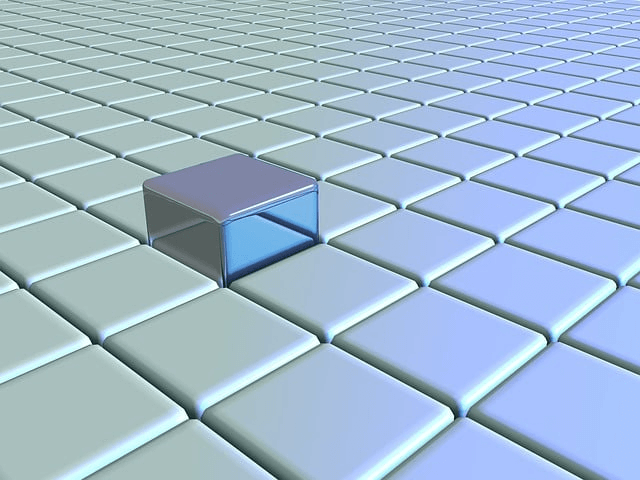
Product Design and the Detailed Design Process
Product design is the phase where detailed engineering specifications and plans (i.e. detailed design) are developed, to turn the chosen concept into a tangible product or system. However, this phase involves some significant engineering problems that need to be addressed for a successful outcome.
Detailed design is a crucial product design element, where engineers create detailed schematics, blueprints, and specifications for all components of the product. This involves making decisions about materials, dimensions, tolerances, and manufacturing processes, which can be quite challenging. In the engineering design process, some decisions are often irrelevant for the concept evaluation state and become relevant later on.
Prototype development is also an essential product design step. Functional prototypes are built to test and refine the design. Engineers must address issues related to manufacturability, assembly, and functionality to ensure the product meets the desired standards.
Material selection is another complex task in product design. The right materials must be chosen to meet performance, durability, and cost requirements.
Manufacturability is also an important product design consideration, since engineers must design the product in a way that is easy and cost-effective to manufacture at scale while maintaining quality standards.
Testing and validation are critical steps in product design: testing procedures are developed, and the product is tested to ensure it meets safety, reliability, and performance standards.
Cost optimization is an ongoing product design process. Engineers must work continuously to optimize production costs without compromising quality.
Lastly, the concept of "sustainability is becoming an increasingly important aspect of product design. Engineers must consider the environmental impact of the product, including materials, energy consumption, and end-of-life disposal.
Principles of Conceptual Design in Automotive Engineering
Conceptual design in automotive engineering is driven by several fundamental engineering principles to ensure the development of efficient, reliable, and cost-effective vehicles. These principles guide engineers through the process of designing automobiles that meet performance, safety, and regulatory requirements:
Creative Problem Solving: In automotive engineering, creative problem-solving is essential. Engineers must identify and address vehicle performance, fuel efficiency, emissions, safety, and consumer preferences. For instance, engineers may employ innovative aerodynamic solutions to reduce drag and improve fuel economy.
Holistic Approach: A holistic approach means considering the entire vehicle system rather than individual components in isolation. This approach ensures that all components work harmoniously to achieve the desired performance and efficiency.
For example, when designing a hybrid electric vehicle (HEV), engineers must optimize the integration of the internal combustion engine, electric motor, and battery system.
Iterative Process: Conceptual design is an iterative process in which engineers continually refine and improve designs based on feedback and analysis.
Engineers may iteratively adjust suspension geometry, tire selection, and chassis stiffness to achieve desired ride and handling characteristics.
Multidisciplinary Collaboration: Automotive design requires collaboration among various engineering disciplines, including mechanical, electrical, and software engineering.
For instance, when developing an advanced driver assistance system (ADAS), engineers from multiple domains collaborate to integrate sensors, control algorithms, and actuators seamlessly.
Steps of the Conceptual Design Stage in Automotive Engineering
Developing a new vehicle or system in automotive engineering involves several crucial steps during the design activities at the conceptual design stage.
Firstly, engineers must define the problem to be solved and the specific requirements that the vehicle or system must meet. These requirements may include performance metrics such as acceleration, top speed, fuel efficiency, safety standards, and environmental regulations.
Secondly, engineers generate various design concepts and solutions, brainstorming ideas and potential solutions. For example, considering the design of an autonomous vehicle, engineers may consider sensor configurations, mapping algorithms, and human-machine interfaces.
Thirdly, each potential solution is rigorously evaluated against the defined requirements and constraints. This assessment often involves computer simulations and modeling to predict how the vehicle will perform under different conditions.
Finally, based on the evaluation, engineers select the most promising solution. For instance, in the development of electric vehicles (EVs), engineers might choose a specific battery chemistry and size that optimally balances range, weight, and cost.
Tools and Techniques for Conceptual Design Process
The conceptual design process in automotive engineering employs a range of tools and techniques to facilitate the creation of innovative vehicle concepts and systems:
Computer-Aided Design (CAD)
CAD software allows engineers to create detailed 2D and 3D models of vehicle components, aiding in visualizing design concepts. For example, CAD tools are used to design complex engine components, such as cylinder heads and intake manifolds.
Finite Element Analysis (FEA)
FEA software helps engineers simulate how vehicle structures and components will perform under various loads and conditions. In automotive design, FEA is employed to analyze the structural integrity of chassis frames and body structures.
Computational Fluid Dynamics (CFD)
CFD software is used to simulate airflow over vehicle surfaces, aiding in aerodynamic design optimization. This is crucial for improving fuel efficiency and reducing drag on vehicles.
Parametric Design
Parametric modeling tools enable engineers to create design parameters and variables, making it easier to explore different design alternatives. For example, parametric design can be used to optimize the shape and form of a vehicle's exterior for reduced drag.
New Challenges in Conceptual and Detailed Design
AI and Machine Learning in Conceptual Design
AI and machine learning have the potential to transform automotive conceptual design. Optimization algorithms based on machine learning can efficiently optimize vehicle designs, finding configurations that maximize fuel efficiency, safety, or performance.
Predictive analytics models based on AI can predict and identify potential component failures. Machine learning models can predict component failures before they occur. AI algorithms can identify early signs of issues like engine component degradation by analyzing sensor data from various vehicle systems, such as engine temperature, vibration patterns, and wear indicators. This enables proactive maintenance, reducing unplanned downtime and maintenance costs.
AI-driven generative design tools can help engineers create lightweight yet structurally robust vehicle components. These tools can generate innovative structural designs by specifying design constraints like material properties and load conditions.
For instance, generative design algorithms can suggest intricate lattice structures that maintain structural integrity while minimizing weight when designing a lightweight chassis.
Virtual Reality and Simulation
Virtual reality (VR) and simulation technologies offer engineers an immersive experience in a virtual environment of the vehicle, where they can evaluate ergonomic and safety considerations.
Utilizing VR and simulation to replicate vehicle behavior enables designers to minimize the need for physical prototypes, significantly saving time and resources.